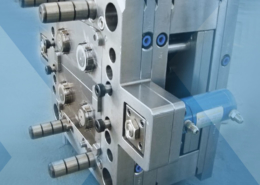
Brain Shaped Large Plastic Mould - large plastic molds
Author:gly Date: 2024-10-15
High-Performance Polymer: HDPE 8000F stands out as a high-performance grade, primarily due to its excellent stress crack resistance. This property makes it an optimal choice for manufacturing chemical containers, outdoor equipment, and products exposed to challenging environments.
Low Shrinkage and Dimensional Accuracy: HDPE 8000F's low shrinkage rate of 0.8% enhances its ability to maintain precise dimensions during cooling.
Elevated Heat Deflection: HDPE 6000F's heat deflection temperature of 90°C makes it suitable for applications that face moderate thermal challenges. It is employed in crafting items like automotive interior parts, kitchen utensils, and electrical components that withstand elevated temperatures without deformation.
The choice of materials plays a crucial role in ABC Plastic Moulding, influencing the mechanical properties, aesthetics, and performance of the final product. Engineers meticulously select resins based on factors such as strength, flexibility, and environmental considerations, ensuring compatibility with the intended application.
Diverse Industrial Applications: HDPE 7000F's combination of properties makes it versatile for various industrial applications. It is used to craft large storage containers, material handling equipment, and industrial machinery components that withstand heavy loads and harsh environments.
Moderate Tensile Elongation: HDPE 7000F's tensile elongation of 500% balances flexibility and strength, making it suitable for products requiring a blend of both attributes. This property is advantageous for producing hoses, tubing, and flexible containers.
Mechanical Strength: With a tensile strength of 27 MPa and a flexural strength of 45 MPa, HDPE 6000F offers solid mechanical performance. It's an excellent fit for creating industrial components, agricultural equipment, and structural parts that demand a blend of strength and reliability.
Balanced Strength and Flexibility: HDPE 5000S combines a commendable tensile strength of 30 MPa with a high elongation of 600%, rendering it suitable for manufacturing durable yet flexible products.
In conclusion, ABC Plastic Moulding represents a cornerstone of modern manufacturing, offering unparalleled versatility, efficiency, and reliability across a diverse range of industries. From automotive to healthcare, its impact reverberates throughout society, driving innovation, enhancing quality of life, and shaping the future of manufacturing. As we look ahead, the continued advancement of technology and sustainability initiatives promises to further elevate the capabilities and impact of ABC Plastic Moulding, ushering in a new era of ingenuity and progress.
Dimensional Stability: HDPE 5000S exhibits low shrinkage (1.5%) and maintains its shape during cooling, contributing to the accurate and consistent production of precision parts.
The versatility of ABC Plastic Moulding extends to the realm of electronics and consumer goods, where it facilitates the production of enclosures, housings, and connectors for electronic devices. Its ability to accommodate complex geometries and tight tolerances makes it an ideal choice for manufacturers seeking to optimize product performance and aesthetics.
In the medical and healthcare sector, ABC Plastic Moulding plays a vital role in the production of disposable medical devices, surgical instruments, and equipment components. Its ability to meet stringent regulatory requirements, coupled with its cost-effectiveness and scalability, makes it indispensable in the quest for innovation and patient care.
As technology continues to evolve, so too does the landscape of ABC Plastic Moulding. Innovations in materials science, process optimization, and automation are poised to enhance efficiency, reduce waste, and expand the capabilities of this versatile manufacturing technique.
Excellent Impact Resistance: This grade's Izod impact strength of 30 J/m ensures resilience against impacts and shocks. It finds relevance in creating toys, household items, and industrial components that require impact resistance to withstand rough handling or accidental drops.
In the automotive industry, ABC Plastic Moulding is instrumental in the production of interior and exterior components, including dashboards, bumpers, and trim panels. Its ability to deliver lightweight, durable, and aesthetically pleasing parts aligns with the industry's emphasis on fuel efficiency, safety, and design innovation.
Enhanced Flow: HDPE 6000F's improved melt flow characteristics make it a prime choice for manufacturing intricate components with complex geometries. Its versatility applies to applications like thin-walled parts, including intricate automotive components and electronic enclosures.
Central to the success of ABC Plastic Moulding is the meticulous design and fabrication of moulds. Engineers employ advanced CAD/CAM software and CNC machining to create precise moulds tailored to the specifications of each component. This emphasis on tooling ensures optimal part quality and efficiency throughout the production cycle.
At the heart of ABC Plastic Moulding lies the injection moulding process, a sophisticated technique wherein molten plastic is injected into a mould cavity under high pressure. This process allows for the rapid and cost-effective production of intricate parts with high precision and repeatability.
Balanced Impact Resistance: An Izod impact strength of 35 J/m ensures robust resistance to impacts and shocks. This property is ideal for crafting items like safety equipment, consumer goods, and housings for power tools.
Enhanced Stiffness: Boasting a flexural modulus of 1300 MPa, HDPE 7000F excels in applications that demand stiffness and structural integrity. It is ideal for creating items like furniture, automotive components, and machinery parts where robustness is essential.
Optimized Heat Deflection: With a heat deflection temperature of 85°C, HDPE 5000S is apt for applications with elevated temperatures. It produces kitchenware, automotive components, and products exposed to moderate heat sources.
High-Density Polyethylene (HDPE) is a thermoplastic polymer known for its high strength-to-density ratio. It's produced from petroleum and exhibits excellent resistance to chemicals, impact, and moisture, making it suitable for various applications, including packaging, pipes, and injection-molded products.
In response to growing environmental concerns, the ABC Plastic Moulding industry is embracing sustainability initiatives aimed at reducing carbon footprint and minimizing waste. From the adoption of biodegradable resins to the implementation of closed-loop recycling systems, manufacturers are actively seeking ways to mitigate their environmental impact while maintaining operational excellence.
In the realm of manufacturing, ABC Plastic Moulding stands as a beacon of innovation and efficiency, offering versatile solutions for the production of plastic components across various industries. From automotive parts to consumer electronics, ABC Plastic Moulding plays a pivotal role in shaping the modern world. In this article, we delve into the intricacies of ABC Plastic Moulding, exploring its processes, applications, and impact on the manufacturing landscape.
High Molecular Weight: With an elevated molecular weight, HDPE 7000F offers improved mechanical properties and durability. It finds application in crafting industrial components, tanks, and agricultural equipment that require enduring performance under demanding conditions.
Elevated Heat Deflection: Featuring a heat deflection temperature of 100°C, HDPE 8000F is ideal for applications subjected to higher temperatures. It produces parts for automotive engine compartments, outdoor fixtures, and products with moderate heat exposure.
Superior Impact Strength: With an Izod impact strength of 50 J/m, HDPE 8000F ensures exceptional resilience against impacts and shocks. It finds relevance in creating challenging and durable items like tool cases, industrial bins, and protective equipment.
GETTING A QUOTE WITH LK-MOULD IS FREE AND SIMPLE.
FIND MORE OF OUR SERVICES:
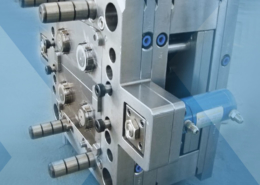
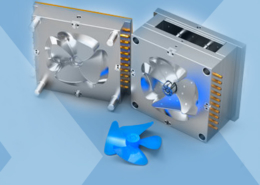
Plastic Molding

Rapid Prototyping
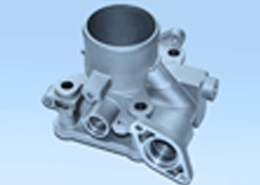
Pressure Die Casting
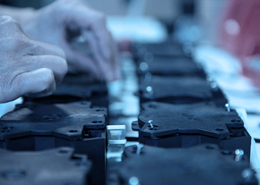
Parts Assembly
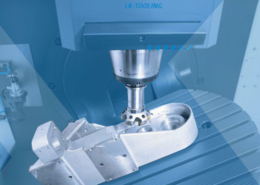