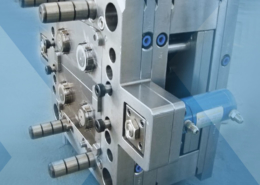
Unveiling the Potential of Low Volume Plastic Injection Molding
Author:gly Date: 2024-06-08
Introduction
In the realm of manufacturing, the ability to produce small quantities of plastic parts with precision and efficiency is increasingly essential for companies aiming to meet niche market demands, accelerate product development, and minimize upfront costs. Low volume plastic injection molding emerges as a solution to address these challenges, offering flexibility, agility, and cost-effectiveness in producing small batches of plastic components. This article delves into the realm of low volume plastic injection molding, exploring its significance, processes, applications, advantages, and future prospects.
Significance and Background
Low volume plastic injection molding caters to the niche market of producing small quantities of plastic parts with rapid turnaround times and minimal tooling investment. Traditionally, injection molding was associated with high-volume production due to the substantial upfront costs associated with tooling and setup. However, advancements in technology, such as rapid prototyping techniques and digital manufacturing, have democratized the injection molding process, making it accessible to companies seeking to produce small batches of customized parts.
This method enables manufacturers to respond swiftly to market demands, iterate designs, and test prototypes without committing to large production runs. It facilitates the production of complex geometries, intricate details, and diverse materials, offering unparalleled design freedom and versatility. As such, low volume plastic injection molding has gained traction across various industries, including automotive, aerospace, medical devices, consumer goods, and electronics.
Processes and Methodologies
Low volume plastic injection molding follows similar principles to traditional injection molding, albeit with adaptations to accommodate smaller production volumes and faster turnaround times. The process begins with the creation of a mold, either through rapid tooling techniques like 3D printing or conventional methods, depending on the production requirements. Once the mold is ready, it is mounted onto an injection molding machine equipped with precise controls for temperature, pressure, and injection speed.
Materials, typically thermoplastics or elastomers, are heated to their melting point and injected into the mold cavity under high pressure. After cooling and solidification, the mold opens, and the finished part is ejected. Unlike high-volume production, where large-scale automation is prevalent, low volume plastic injection molding often relies on manual intervention and semi-automated processes to accommodate frequent changeovers and customization.
Applications and Industries
The applications of low volume plastic injection molding are diverse and encompass a wide range of industries. In the automotive sector, it enables the production of custom interior components, prototype parts, and specialty accessories with short lead times and minimal tooling investment. Similarly, in aerospace, low volume plastic injection molding is utilized for producing lightweight, high-strength components for prototypes, testing, and niche applications.
In the medical field, this method facilitates the manufacturing of personalized devices, surgical instruments, and disposable components tailored to individual patient needs. The ability to produce small quantities of parts with precise tolerances and biocompatible materials is invaluable for medical device companies seeking rapid prototyping and validation. Additionally, in the consumer goods industry, low volume plastic injection molding allows for the creation of limited edition products, customized packaging, and promotional items with intricate designs and branding elements.
Advantages and Benefits
Low volume plastic injection molding offers several advantages over traditional manufacturing methods, making it an attractive option for companies seeking agility and flexibility. Firstly, it reduces time-to-market by accelerating the product development cycle, enabling faster iterations, and validation of designs. This agility is crucial in industries where innovation and customization are paramount, allowing companies to stay ahead of competitors and adapt to changing market trends.
Moreover, low volume plastic injection molding minimizes upfront costs associated with tooling and inventory management, making it accessible to startups, small businesses, and entrepreneurs. By eliminating the need for large production runs, it mitigates the risk of overstocking or obsolete inventory, optimizing resource utilization and cost-effectiveness. Furthermore, the ability to produce parts on-demand reduces lead times, inventory carrying costs, and logistical complexities, enhancing supply chain efficiency and responsiveness.
Conclusion
In conclusion, low volume plastic injection molding presents a paradigm shift in manufacturing, offering unparalleled flexibility, agility, and customization capabilities. From rapid prototyping and niche production to personalized medical devices and limited edition consumer goods, its applications span across diverse industries, driving innovation and market differentiation. While traditional injection molding continues to dominate high-volume production, the rise of low volume plastic injection molding signifies a democratization of manufacturing, empowering companies of all sizes to innovate, iterate, and thrive in dynamic markets.
Looking ahead, the future of low volume plastic injection molding holds promise for further advancements in technology, materials, and processes. As additive manufacturing techniques evolve and digitalization permeates the manufacturing landscape, the barriers to entry for low volume production will continue to diminish. Additionally, with the advent of Industry 4.0 and the Internet of Things (IoT), low volume plastic injection molding is poised to integrate seamlessly into interconnected manufacturing ecosystems, enabling real-time data monitoring, predictive maintenance, and autonomous optimization.
Through continued research, collaboration, and investment, the potential of low volume plastic injection molding can be unlocked to drive sustainable growth, innovation, and competitiveness in the global marketplace. By embracing the principles of agility, customization, and on-demand manufacturing, companies can leverage the transformative power of low volume plastic injection molding to navigate uncertainty, capitalize on opportunities, and create value in an ever-evolving business landscape.
GETTING A QUOTE WITH LK-MOULD IS FREE AND SIMPLE.
FIND MORE OF OUR SERVICES:
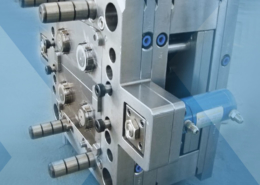
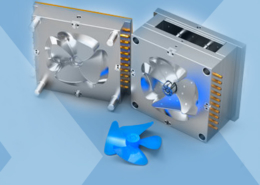
Plastic Molding

Rapid Prototyping
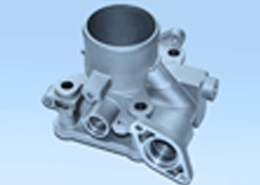
Pressure Die Casting
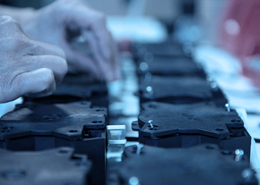
Parts Assembly
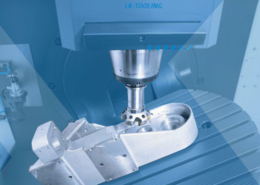