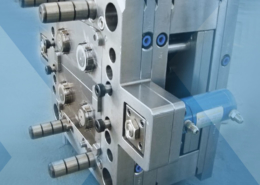
biodegradable PLA injection molding From CHUNAY - pla molding
Author:gly Date: 2024-10-15
Though most often an indicator that the plastic needs more time inside the mold to properly cool and cure, sink marks may sometimes be remedied by reducing the thickness of the thickest wall sections, which helps to ensure more even and thorough cooling. Inadequate pressure in the mold cavity or higher-than-desirable temperatures at the gate can also contribute to the development of the defects.
Raising the temperature of the molten resin can help to prevent the solidification process from beginning too soon, as can increasing injection speed and pressure. Resins with lower viscosity and lower melting points are less prone to developing weld lines in injection molding, which can also be eliminated by removing partitions from mold design.
Additive manufacturing is slowly establishing itself as a viable production tool, and we’re increasingly seeing our clients utilize these benefits. However, this does not mean that additive manufacturing should be treated as a complete replacement for traditional manufacturing. For large-scale production, traditional methods still offer unmatched economies of scale.
3D printing allows you to update and change your design throughout the entire production process. Not only does it provide flexibility, but it is also a faster choice and more cost-effective option for small quantities. This makes additive manufacturing the perfect choice for prototyping and iterations.
Sink marks appear as depressions, dents, or craters in thick sections of a part. Thicker sections take longer to cool, which can have the often unanticipated side effect of the inner portions of the part shrinking and contracting at a much different rate than the outer sections.
When it comes to production methods, two processes, injection moulding and 3D printing are often compared. These two methods represent a classic debate of ‘old’ vs. ‘new’ in today’s manufacturing industry. While 3D printing has allowed for innovative design implementation within hours, plastic injection molding remains an industry standard for high-quality, reliable, large batch production.
The cost of 3D printing versus injection moulding a part. For this example, we’ve taken an SLS printed and injection moulding PA+GF part that is 84.5mm x 80.0mm x 24.0mm in size with a standard deburr finish.
On the design side, the risk of sink marks can be minimized by ensuring proper injection molding rib thickness and wall thickness. These actions can also help to increase the overall strength of the part.
With prototype injection mold tooling, also known as rapind tooling, you can test the part in the production intent material, understand how the part will work when manufactured in the production process, and it allows for low volume production runs to test the market.
When it comes to production methods, two processes, injection moulding and 3D printing are often compared. These two methods represent a classic debate of ‘old’ vs. ‘new’ in today’s manufacturing industry. While 3D printing has allowed for innovative design implementation within hours, plastic injection molding remains an industry standard for high-quality, reliable, large batch production.When comparing the two methods, cost is often the first topic that comes to mind: Which is cheaper, injection molding or 3D printing? It is crucial to determine when it is more economical to use injection molding over 3D printing, and vice versa. In this article, we will analyze the differences in per unit cost, total cost and advantages of using each process. 3D printing vs injection molding: cost comparisonThe cost of 3D printing versus injection moulding a part. For this example, we’ve taken an SLS printed and injection moulding PA+GF part that is 84.5mm x 80.0mm x 24.0mm in size with a standard deburr finish. *Please note that the chart is crafted based on the specific case mentioned. The cost per unit of your specific part may vary significantly based on factors such as size, geometry, complexity, material, post processing, and other considerations. For an accurate cost assessment of your part, we encourage you to get a rapid quote from our team at hlhrapid.com. Piece-part priceIn the case above, it is estimated that a mould would immediately cost the client $3,000 to have manufactured. Of course, this can vary depending on the size, complexity, and where the tool is manufactured.Based on the chart above, 3D printing is a much cheaper option for lower quantities due to the absence of high upfront mold tooling costs. As we reach 500 pieces and above, injection moulding starts becoming more cost-effective. At 10,000 pieces, the total cost of injection moulding is approximately $12,900 (around 99 cents per piece), while 3D printing costs $70,000 (around $7 per piece), making additive manufacturing five times more expensive. Setup and tooling considerationsIn injection moulding, every design modification or iteration usually demands the reworking of the mould, which can be costly and time consuming. Due to the nature of the process, significant changes may even require a completely new tool. This puts 3D printing at a notable advantage in this comparison. 3D printing allows you to update and change your design throughout the entire production process. Not only does it provide flexibility, but it is also a faster choice and more cost-effective option for small quantities. This makes additive manufacturing the perfect choice for prototyping and iterations. Scaling with 3D printingThe argument typically goes that the cost to deliver a 3D-printed part will always remain the same, regardless of whether you are producing 1 or 1000 units. However, this is not the case, as evident in the chart above. 3D printing technologies has advanced over the years. Nowadays, manufacturers like HLH Rapid with automation systems, streamline processes and larger industrial printers, now enable the production of larger quantities at lower unit costs.Additive manufacturing is slowly establishing itself as a viable production tool, and we’re increasingly seeing our clients utilize these benefits. However, this does not mean that additive manufacturing should be treated as a complete replacement for traditional manufacturing. For large-scale production, traditional methods still offer unmatched economies of scale. Prototyping with injection mouldingCan you prototype with injection moulding? At HLH Rapid, we use a single-cavity aluminum mold, known as a prototype injection mold tool, that can produce hundreds of parts. Nevertheless, project budgets are generally tight and deadlines are even tighter, so why would you invest the time and money needed to manufacture a prototype via injection molding? Why not go straight from your 3D printed prototype to production tooling? With prototype injection mold tooling, also known as rapind tooling, you can test the part in the production intent material, understand how the part will work when manufactured in the production process, and it allows for low volume production runs to test the market. 3D printing vs injection molding: which to chooseHLH Rapid has over 15 years of experience in 3D printing, injection molding, rapid tooling, and scaling from prototype quantities to product quantities. Request for an accurate quote from our team for multiple quantities to better understand which option is more cost-effective, when to justify high tooling costs, and which technology to use for your next rapid project.
When comparing the two methods, cost is often the first topic that comes to mind: Which is cheaper, injection molding or 3D printing? It is crucial to determine when it is more economical to use injection molding over 3D printing, and vice versa. In this article, we will analyze the differences in per unit cost, total cost and advantages of using each process.
Also called knit lines, these defects mark where two flows of molten resin came together as they moved through the mold geometry. This happens around any part of the geometry that has a hole. As the plastic flows and wraps around each side of a hole, the two flows of plastic meet. If the temperature of the flow isn’t just right, the two flows won’t properly bond together and will instead cause a visible weld line. This reduces the overall strength and durability of the component.
Jetting defects in injection molding are another potential result of an uneven solidification process. Jetting occurs when an initial jet of resin enters the mold and has enough time to begin setting before the cavity fills. This creates visible, squiggly flow patterns on the piece’s surface and decreases the strength of the part.
Reducing injection pressure is often the best way to ensure more gradual fills, but increasing the mold and resin temperature can also help to prevent any jets from preemptively setting. Placing the injection gate so that the flow of material runs through the shortest axis of the mold is another effective means of minimizing jetting.
Flow lines can also appear when the thermoplastic resin moves through parts of the mold with different wall thicknesses — which is why maintaining consistent wall thickness or ensuring that chamfers and fillets are an appropriate length is critical. Placing the gate in a thin-walled section of the tool cavity can further help to reduce flow lines.
“Short shots” refer to instances in which the resin doesn’t entirely fill the mold cavity, resulting in incomplete and unusable parts.
Injection molding can be a highly efficient manufacturing method for producing highly repeatable plastic parts, but, as with many processes, producing high quality end-parts requires a high level of attention to detail and a proactive approach to risk management. Everyone involved in the product development process — from the initial design and proof-of-concept stages all the way to fulfillment — needs to do their due diligence to ensure products meet the highest quality standards and avoid these common plastic injection molding issues.
Choosing a manufacturing partner like SyBridge, who is well-versed in common defects in injection molding and their troubleshooting, can mean the difference between high-quality parts — produced on-time and within budget — and those marked with weld lines, jet, flash, sink marks, and other defects. In addition to being an experienced on-demand manufacturing shop, we also provide design consulting and optimization services that ensure we’re able to help every team create functional, elegant, high-performance parts as efficiently as possible. Contact us today to learn more about our injection molding services.
Injection molding warping refers to unintended twists or bends caused by uneven internal shrinkage during the cooling process. Warping defects in injection molding are generally the result of non-uniform or inconsistent mold cooling, which creates stresses within the material.
HLH Rapid has over 15 years of experience in 3D printing, injection molding, rapid tooling, and scaling from prototype quantities to product quantities. Request for an accurate quote from our team for multiple quantities to better understand which option is more cost-effective, when to justify high tooling costs, and which technology to use for your next rapid project.
Based on the chart above, 3D printing is a much cheaper option for lower quantities due to the absence of high upfront mold tooling costs. As we reach 500 pieces and above, injection moulding starts becoming more cost-effective. At 10,000 pieces, the total cost of injection moulding is approximately $12,900 (around 99 cents per piece), while 3D printing costs $70,000 (around $7 per piece), making additive manufacturing five times more expensive.
Flow lines are off-color lines, streaks, and other patterns that appear on the surface of a part. These are caused by the shot of molten plastic moving at different speeds throughout the injection mold, which ultimately causes the resin to solidify at different rates. This is often a sign that injection speed and/or pressure are too low.
Preventing warpage defects in injection molding is a matter of guaranteeing that parts are given enough time to cool — and at a sufficiently gradual rate — to prevent internal stresses from forming and damaging the piece. Uniform wall thickness in mold design is crucial for many reasons, critical among them being that it helps ensure that the plastic flows through the mold cavity in a single direction.
*Please note that the chart is crafted based on the specific case mentioned. The cost per unit of your specific part may vary significantly based on factors such as size, geometry, complexity, material, post processing, and other considerations. For an accurate cost assessment of your part, we encourage you to get a rapid quote from our team at hlhrapid.com.
The argument typically goes that the cost to deliver a 3D-printed part will always remain the same, regardless of whether you are producing 1 or 1000 units. However, this is not the case, as evident in the chart above. 3D printing technologies has advanced over the years. Nowadays, manufacturers like HLH Rapid with automation systems, streamline processes and larger industrial printers, now enable the production of larger quantities at lower unit costs.
Can you prototype with injection moulding? At HLH Rapid, we use a single-cavity aluminum mold, known as a prototype injection mold tool, that can produce hundreds of parts. Nevertheless, project budgets are generally tight and deadlines are even tighter, so why would you invest the time and money needed to manufacture a prototype via injection molding? Why not go straight from your 3D printed prototype to production tooling?
Here are a few of the most common defects that may occur in plastic injection molding — and how product teams can avoid them.
What causes short shots in injection molding? Typically, they are the result of restricted flow within the mold, which can be caused by gates that are too narrow or have become blocked, trapped air pockets, or insufficient injection pressure. Material viscosity and mold temperature are also contributors. Increasing mold temperature and incorporating additional venting into mold design to allow air to properly escape can help prevent the occurrence of short shots.
In the case above, it is estimated that a mould would immediately cost the client $3,000 to have manufactured. Of course, this can vary depending on the size, complexity, and where the tool is manufactured.
Defects can reduce the speed and cost-efficiency of the entire product development process, and can potentially shorten product life spans if left unchecked. Injection molding issues and defects can be caused by a host of reasons, including poor design, production process mistakes, quality control failures, and more. As such, it’s important to take a proactive approach to risk mitigation throughout the product development process so as to reduce the chances of potential injection molding defects.
What is delamination? Delamination is a condition that causes a part’s surface to separate into thin layers. These layers, which appear like coatings that can be peeled off, are caused by the presence of contaminants in the material that do not bond with the plastic, creating localized faults. An over-dependence on mold release agents can also cause delamination.
To encourage delamination repair and prevention, teams should increase mold temperatures and tailor the mold ejection mechanism to be less dependent on mold-release agents, since these agents can increase the risk of delamination. Properly pre-drying the plastic before molding can also help.
In injection moulding, every design modification or iteration usually demands the reworking of the mould, which can be costly and time consuming. Due to the nature of the process, significant changes may even require a completely new tool. This puts 3D printing at a notable advantage in this comparison.
Injection molding is an efficient production method when high volumes of identical parts are needed. However, it also requires a high degree of technical expertise to master. With so many different variables in play, small, seemingly minor mistakes in early phases of product development can lead to major problems — and even compromise product integrity — down the line.
GETTING A QUOTE WITH LK-MOULD IS FREE AND SIMPLE.
FIND MORE OF OUR SERVICES:
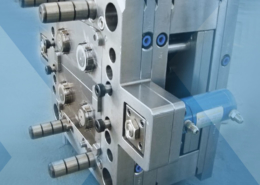
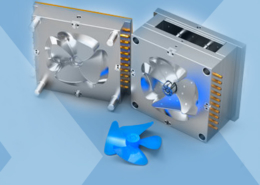
Plastic Molding

Rapid Prototyping
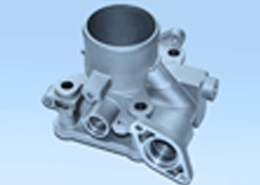
Pressure Die Casting
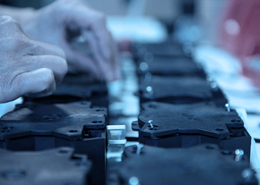
Parts Assembly
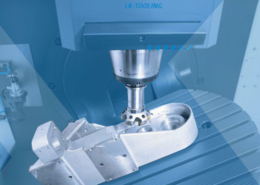