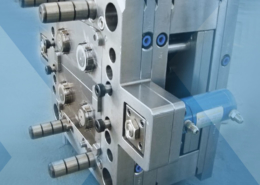
Biodegradable Injection Molding | Meridian Products Corp. - biodegradable plasti
Author:gly Date: 2024-10-15
Acetal polymers are semi-crystalline. They offer exceptional inherent lubricity, fatigue resistance, and chemical resistance. Acetals suffer from outgassing problems at elevated temperatures, and are delicate at low temperatures. Glass-filled Acetal from PTI, Inc. is available with added lubrication grades. Flame retardant grades are not.
That’s before we even consider the resins suitable for heavy-duty use, capable of withstanding everyday wear and tear. Add in chemical and heat resistance, and finding plastic materials with the perfect profile for EV use cases is simple.
From design to delivery, PTI, Inc. can coordinate your entire tool building program from start to finish. Aided by its quality assurance program, PTI's mission is to provide molded products that fully meet or exceed the requirements and expectations of its customers. Company management is committed to continuous quality advancements. For superior quality materials and services, contact PTI, Inc. today.
The convenience, versatility, speed, and scale of injection molding processes make this manufacturing method an obvious choice for supporting today’s EV needs. However, another fundamental reason to choose plastics is that their material properties perfectly suit electric vehicles. Much lighter than comparable parts made in metal, plastic lowers overall vehicle weight substantially and thus contributes to an extended range on a single charge.
With so many potential areas to apply molding of components for the electrical sector, the right partner makes a difference.
From design to delivery, PTI, Inc. can coordinate your entire tool building program from start to finish. For superior quality and efficient services, Request A Quote by sending your information to njeffers@pti-incorporated.com or contact PTI, Inc. today by calling 304-675-2392.
With this growing movement to adopt EV worldwide, the sector — already a vigorous, multibillion-dollar industry — seems poised to explode even more in size and value over the next decade. With this pace of change, massive growth in consumer demand, and increase in the number of players, there are genuine concerns about achieving reliable production. Sourcing suitable materials to continue growing and satisfying customers requires a serious heavy-lift effort. The EV industry must embrace several technologies, chief among them plastic injection molding for the automotive industry.
PTI, Inc. is a diversified molder of both thermoset and thermoplastic compounds to meet all of your molded component requirements. A modern manufacturing facility with injection and compression presses ranging from 85-500 Ton, PTI offers many secondary operations including assembly, painting and pad printing.
Rapid prototyping allows for ideas from the drawing board to be put into tangible materials; test proofs of concepts to be run on shorter timelines, opening the door to rapid iteration. With this technology, you can create a part design ready for full-scale production and inclusion into an EV sooner rather than later.
At PTI, Inc., we understand that quality material is everything. Understanding how different materials act and react with each other is essential for creating great products. Our professional team has the know-how to provide the best materials that are right for you products.
Contact Reliant Plastics for a quote or to get more information on what you can achieve in plastic with Reliant for vehicle manufacturing.
After a slow start and a general reluctance among established automakers to embrace electric vehicles, the industry has kicked into high gear. No longer is Tesla the sole independent producer of electric vehicles; today, there are many prominent brand names, including Ford and Chevrolet, navigating the EV space. Even luxury brands, such as BMW, now offer all-electric vehicles.
Using injection molding for electric vehicles, automakers can tap into a flexible, scalable, and highly mature technology with international and domestic production capacity. Modern plastic molding processes remain cutting-edge, incorporating new techniques and technologies. Simultaneously, they provide a highly versatile solution for meeting many material needs within every electric vehicle.
Ready to start learning more about automotive plastic molding processes and how they can contribute to better EV production? At Reliant Plastics, our depth of knowledge and hands-on experience are valuable assets to our partners – assets we’re ready to put to work for your next product. From prototyping to large-scale production, we offer key insights, guidance, and access to the manufacturing solutions that will support the electric vehicle industry today and tomorrow.
Even components that must withstand extreme conditions, from a corrosive chemical environment to high heat levels, can be produced through injection molding. Molding of components for the electrical sector could yield critical improvements, too. Future battery compartment redesigns could rely on molding for more robust housing or efficient storage designs. Adding this capability to your technology lineup today ensures broad access to critical parts.
The automotive industry moves rapidly to meet consumer demand and improve vehicle models from year to year. The world of electric vehicles moves even faster, especially with intense competition driving manufacturers to seek innovations wherever possible. Rapid prototyping, which is possible through injection molding, can swiftly propel projects toward achieving such critical milestones.
The versatility of plastic injection molding is by far one of its biggest strengths for EV manufacturers. This process does not produce just one or two critical components. Instead, you can apply injection molding to many car parts. Molding suits everything from interior trim components on the dashboard to everyday touchpoints like the charging connector. Even with all the metal pins necessary inside a charging gun, advanced injection molding techniques ensure it is possible to create these assemblies quickly and efficiently.
The most suitable injection molding partners can help you build a highly resilient supply chain to meet the most extensive needs. The repeatable nature of injection molding means you can see hundreds of thousands of product outputs from one extended production run. That level of volume keeps all the parts you need close at hand for the assembly line. Investing in the capacity for large-scale production and the necessary inventory warehousing now means EV makers can also guard against future supply chain disruptions.
GETTING A QUOTE WITH LK-MOULD IS FREE AND SIMPLE.
FIND MORE OF OUR SERVICES:
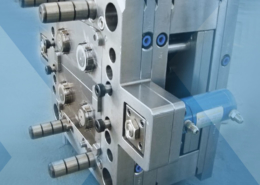
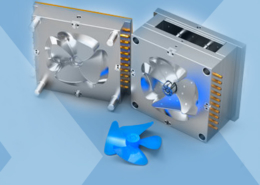
Plastic Molding

Rapid Prototyping
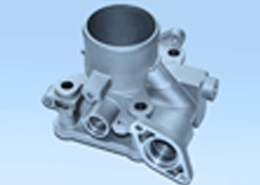
Pressure Die Casting
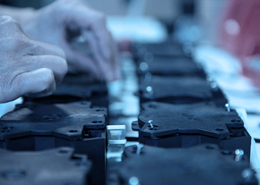
Parts Assembly
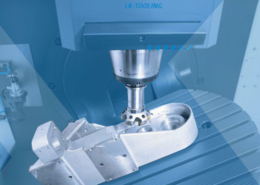