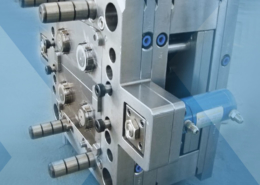
Bi-injection molding / 2k molding - FPM Injection - China - 2k molding
Author:gly Date: 2024-10-15
The process starts with the gas/polymer mixture being short-shot injected through nozzles directly into the mold. The blowing agent then expands and pushes the molten resin into the cavities, thus reducing sink holes over heavy cross-sections. This approach to manufacturing gives the product a cellular core surrounded by a rigid and dense outer skin, building structurally sound products while reducing their weight and density because of the development of the structural core. Keep reading
The foam made from it is closed-cell and waterproof, its cells are tightly connected, giving the CFAs are typically used when trying to achieve higher density foams and they can improve the quality of the final product immensely. They are often used for the production of strong, yet lightweight structural foam moldings. As well as the extra strength, — depending on the shape of the mold – CFAs will also save you money, since thicker walls make it easier for the foam to form. You can generally expect a reduction of 10 to 25% of the weight, or even more with a well-formed design.
One interesting fact about flexible foam is that it contours around molds, allowing you to take shapes and make flexible objects that can easily be used for production items. These are usually produced with silicone molds, but urethane or other molds Keep reading
Otima Veggie TraySeptember 30, 2022Washing Machine BalancerSeptember 30, 2022Plants POTSeptember 29, 2022Silicone LampJuly 25, 2022
When doing foam injection molding there are several ways of modifying a material’s properties. In most instances what you are looking for is weight reduction and sink removal on your parts, and one of the main ways of solving that is the usage of Chemical Foaming Agents (CFAs).
If you don’t feel foam is right for your product (ask us to clarify if you’re not sure) we also have much experience in silicone and plastic injection molding.
Ms. Lai Yuen CHIANG, Chairman and CEO of Chen Hsong Earns “GBA Outstanding Women Entrepreneur Award – Supreme Honorable Winner 2023” Title
Direct injection expanded foam molding is also known as injection molded foam, and it’s used to create soft foam products from a complex base resin made from an ethylene and polyolefin elastomer. They become very rigid, but are really easy to use and cure, and can be used as a lightweight casting or filling material.
Thickness variation EVA Foam injection molded parts can be made to any height or width, they aren’t limited by the process. There’s no need for lamination.
Aesthetically Pleasing EVA Foam develops a perfect mold finish upon completion, the process creates parts with great aesthetics, and the quality is always consistent. And even though EVA Foam products are more expensive than other types of foam production, the result is always an attractive product with long-lasting value which is less likely to deteriorate over time.
Chen Hsong Propels Plastic Industry Forward and Receives Minister’s Acknowledgment at Second Technology Conference in Mumbai, India
can work well as long as they are sealed and a silicone release agent is used on them prior to molding. Another plus with molding in flexible foam is the ability to add color pigments to achieve vibrant colors.
At J-CAD Inc. we are not specific about the form in which you provide us information about your project design. It could even be hand drawn, we don’t mind. We will convert it to a 3D file required for mold making and injection molding mass production. We will work with you to ensure that the design is optimized for the purpose for which it is intended. Our experienced team of highly skilled designers will help you bring out the best out of your product.
New Energy – New Generation! Chen Hsong Group signs strategic cooperation agreement with Chinese electric vehicle manufacturer BYD
One important feature of CFAs is their ability to be processed on all injection molding machines, if you know what you are doing. In order to obtain a uniform foam structure, the CFAs injection rate requires special attention.
Also known as polyethene, polyethylene is the most commonly found plastic around the globe, with annual production being around 80 million tonnes.
If you haven’t noticed, it is highly unlikely that a day comes by without you seeing some sort of polymer foam, they are being used everywhere with an incredible array of applications. You may ask yourself why are they everywhere?
Chen Hsong Propels Plastic Industry Forward and Receives Minister’s Acknowledgment at Second Technology Conference in Mumbai, India
J-CAD has a long-standing positive experience of close to a decade in foam injection molding. All of our products are of superior quality. Our experience coupled with recent technological improvements has enabled us to develop our own advanced structural foam injection molding system that produces products of ultra high quality.
At J-CAD Inc. we produce a very wide variety of products owing to our diverse customer backgrounds and industries served. Our products include:
When working with lower pressure, there’s the benefit of being able to use more economical molding equipment, for this reason, it is cheaper to do mass production of larger, thicker parts by structural molding, than conventional injection molding. And you can expect the finished part to be typically 10 to 30% under the weight of an equivalent conventional injection molded part.
You can add CFAs to the injection molding machine just as if they were colorants or additives. CFAs can also allow for an increase in shot speeds and can reduce clamp tonnage, achieving a reduction that can be as high as 30% in cycle and production times. Pretty amazing benefits from using just one simple additive!
If you have any question just get in touch with us! At J-CAD Inc. we’ll be glad to help you with your project. Call us 1-888-202-2052 or email jason@jcadusa.com
High-Quality Dimensioning With EVA Foam molding the process can be closely controlled, so you can expect to produce really consistent dimensional parts. The manufacturing of the foam and the final product are the same, they happen at the same time. Because of the simple controlling of the process, there is minimal part-to-part variation.
Polyurethane is a polymer that is available in thermosetting (does not melt when heated) and thermoplastic (melts when heated) versions.
Drain BasketJuly 25, 2022Air conditioning components: Panels,frames, wind bladesMarch 11, 2022Plastic Helmet VisorMarch 11, 2022Stationary Bicycle Belt Drive CoverJanuary 25, 2022
Polystyrene is a synthetic compound, that can be solid or foamed. It is made from monomer styrene and is considered and aromatic polymer. It is one of the best materials that could possibly be used for foam injection molding.
In Foam injection molding, thermoplastic materials are first melted. When the melted plastic is evenly soft, an inert gas (blowing agent) is introduced into the polymer melt to make the solution foam-able. The solution is then injected into a mold to make the foam product.
EVA foam is non-toxic and easy to work with. It has some of the properties of a low-density polyethylene with increased gloss, softness and flexibility. It’s also weather resilient; with resistance to UV radiation, low temperatures, good impermeability and high stress-crack resistance. There are both filled and unfilled EVA products. Keep reading
Our equipment have been customized to ensure utmost efficiency and cost effectiveness while maintaining superior quality. Our pumps can handle a highly controlled flow rate of a very wide range. They also handle a wide pressure range that is highly regulated.
Flexible polyurethane foams are easy to use and durable, and very efficient for absorbing energy at controlled rates, changing resonance or shock-pulse frequencies and relieving static stress on flexible materials. Some foams are also great at handling really high temperatures, with some avoiding long-term effects up to 180°F.
Low-pressure structural foam molding is very similar to the conventional injection molding process, with a much lower pressure. In most instances of low pressure molding, the molten polymer is injected with nitrogen gas, a chemical blowing agent or an inert gas (NI, CO2, CBA…). The mold won’t be completely filled with the resin as with high-pressure molding, the injected gases are mixed with the polymer, and then they are allowed to expand inside the mold.
Ms. Lai Yuen CHIANG, Chairman and CEO of Chen Hsong Earns “GBA Outstanding Women Entrepreneur Award – Supreme Honorable Winner 2023” Title
This type of resin can also be colored with a variety of additives and is very resistant to most chemicals. This allows products to be suitable for lots of uses. Keep reading
Ms. Lai Yuen CHIANG, Chairman and CEO of Chen Hsong Earns “GBA Outstanding Women Entrepreneur Award – Supreme Honorable Winner 2023” Title
The Chen Hsong Group has offices and distributors all around the globe. Select your region from below or search our global list of distributors.
Post Mold Stability Injection molding gives EVA Foam parts a very soft and malleable body after finishing their molding cycle. Because of this malleability a cooling fixture is sometimes required during the post-molding phase.
The visual above is just the basic principle of the foam injection molding process. The quality of the end product is highly dependent on how delicately the foam injection process is balanced which we have mastered at J-CAD Inc. We have done away with stop-and-flow molding because of the resulting inconsistency in gas dosing. We have come up with ways to ensure that there is continuous flow of both the blowing agent and polymer during the injection process. We have also introduced a lot more modifications to ensure that the end products are of superior quality and the cost of our products are affordable.
There are many kinds of CFAs, since they can be organic or inorganic compounds. CFAs generate exothermic or endothermic reactions, and they are used in this process to nucleate the foam structure that results from the expansion of the gas that is injected to the mold, as it decomposes while dispersing through the polymer melt. Keep reading
EVA, or ethylene-vinyl acetate foam is a soft and durable polymer processed as a thermoplastic material, commonly used in flooring and sports equipment due to it being highly cushioning and sponge-like.
Polyurethane foams are made by mixing two-part polyurethanes, that expand upon mixing and fill the molds, allowing for a lot of variety in material density and functionality. It’s important to stabilize both polyurethanes to a certain temperature; if when mixing the temperature is too hot the foam will be too light and weak, if the temperature is too cold the foam becomes too dense.
The foam made from it is closed-cell and waterproof, its cells are tightly connected, giving the foam a high tensile strength and making it strong and durable.The main benefit of injection molded foam is that its cycle is way faster; the foam and product are both manufactured simultaneously, as this process doesn’t require die-cutting or compression molding. Also, given its really high expansion rate, the products manufactured are self-skinning, meaning that they have a great reproduction of surface detail.
Ms. Lai Yuen CHIANG, Chairman and CEO of Chen Hsong Earns “GBA Outstanding Women Entrepreneur Award – Supreme Honorable Winner 2023” Title
Structural molding shares some similarities with injection molding, but these are the main differences between the two processes:
GETTING A QUOTE WITH LK-MOULD IS FREE AND SIMPLE.
FIND MORE OF OUR SERVICES:
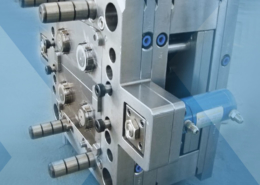
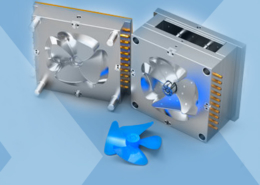
Plastic Molding

Rapid Prototyping
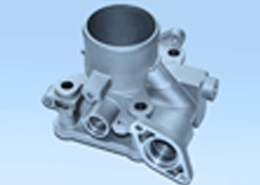
Pressure Die Casting
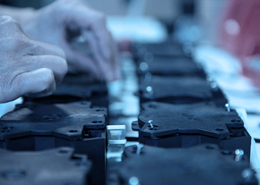
Parts Assembly
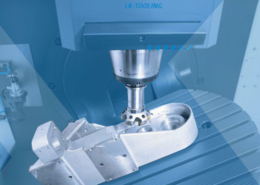