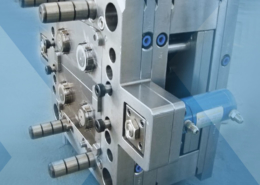
Unveiling the Potential of Low-Cost Injection Molding
Author:gly Date: 2024-06-08
In the realm of modern manufacturing, low-cost injection molding emerges as a disruptive force, challenging traditional perceptions and opening new avenues for cost-effective production. This article embarks on a journey to explore the intricacies of low-cost injection molding, shedding light on its significance, applications, and potential impact, captivating readers with its transformative potential.
Introduction to Low-Cost Injection Molding
Redefining Manufacturing Economics
Low-cost injection molding represents a paradigm shift in manufacturing economics, where the traditional barriers to entry are dismantled, and opportunities for small and medium-sized enterprises (SMEs) to compete on a global scale are unlocked. By leveraging innovative techniques, materials, and processes, low-cost injection molding offers a pathway to cost-efficient production without compromising on quality or performance.
Democratizing Access to Manufacturing
Historically, injection molding has been associated with high setup costs, making it prohibitive for many businesses, particularly startups and SMEs. However, advancements in technology and the emergence of low-cost manufacturing solutions have democratized access to injection molding, allowing entrepreneurs and innovators to bring their ideas to life without breaking the bank.
Driving Innovation and Entrepreneurship
Low-cost injection molding fosters a culture of innovation and entrepreneurship by empowering individuals and businesses to explore new ideas, iterate quickly, and bring products to market faster than ever before. By reducing the barriers to entry and lowering the cost of experimentation, it stimulates creativity and accelerates the pace of innovation across various industries.
Factors Influencing Cost Efficiency
Material Selection
The choice of materials plays a critical role in determining the cost-effectiveness of injection molding. By selecting affordable yet high-quality thermoplastic resins and compounds, manufacturers can achieve significant cost savings without compromising on product performance or durability.
Tooling Optimization
Optimizing tooling design and production processes is essential for minimizing upfront costs and reducing lead times in injection molding. Techniques such as rapid prototyping, computer-aided design (CAD), and additive manufacturing enable manufacturers to iterate quickly and refine designs before committing to expensive tooling.
Process Efficiency
Streamlining injection molding processes and maximizing equipment utilization are key strategies for improving cost efficiency. By optimizing cycle times, minimizing material waste, and implementing lean manufacturing principles, manufacturers can maximize productivity and reduce production costs without sacrificing quality or performance.
Applications and Industry Impact
Consumer Goods
Low-cost injection molding has a significant impact on the consumer goods industry, where affordability and scalability are paramount. From household appliances to consumer electronics and toys, low-cost injection molding enables manufacturers to produce high-quality products at competitive prices, catering to a diverse range of consumer needs and preferences.
Medical Devices
In the healthcare sector, cost-effective manufacturing solutions are essential for ensuring access to essential medical devices and equipment. Low-cost injection molding plays a crucial role in the production of disposable medical devices, such as syringes, IV catheters, and surgical instruments, enabling manufacturers to meet the growing demand for affordable healthcare solutions.
Automotive Components
The automotive industry is increasingly turning to low-cost injection molding for the production of lightweight yet durable plastic components. From interior trim panels to exterior body parts and under-the-hood components, low-cost injection molding offers automotive manufacturers a cost-effective solution for achieving design flexibility, performance, and efficiency.
Conclusion: Unlocking Manufacturing Potential
In conclusion, low-cost injection molding represents a transformative force in modern manufacturing, offering businesses of all sizes access to cost-effective production solutions and driving innovation across industries. By leveraging technology, optimizing processes, and embracing a culture of innovation, manufacturers can unlock new opportunities, reduce costs, and bring high-quality products to market faster and more affordably than ever before. As we look to the future, continued investment in research and development, along with collaboration across industry sectors, will be key to unlocking the full potential of low-cost injection molding and shaping the future of manufacturing.
GETTING A QUOTE WITH LK-MOULD IS FREE AND SIMPLE.
FIND MORE OF OUR SERVICES:
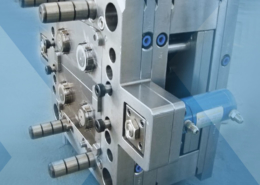
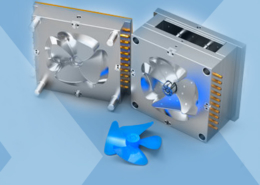
Plastic Molding

Rapid Prototyping
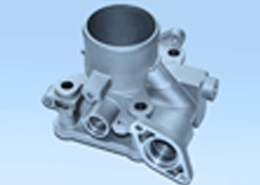
Pressure Die Casting
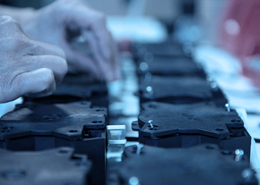
Parts Assembly
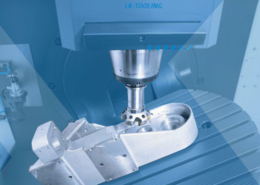