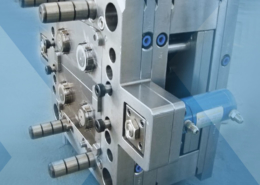
Basstackle 156 worm - Soft Plastics - basstackle molds
Author:gly Date: 2024-10-15
It refers to a plastic part manufacturing process which involves the introduction of a liquefied plastic material allowing its solidification in a mold.
WeProFab is a joint-venture company between WeeTect Material Limited and a Chinese local plastic fabrication manufacturer. We hold full capabilities on plastic fabrication, which can support us to offer you one-stop solutions for OEM/ODM customers.
Similar to overmolding, the insert molding technique involves molding a secondary component over an existing part, or the insert. What sets insert molding apart is that it is a single process and can be used with various materials, such as plastics, metals, or alloys.
It is usually caused either by extremely high pouring temperature or inconsistent or unregulated solidification of molten plastic material.
Once you have melted it accordingly depending on various properties of the plastic, you then pour the molten plastic in the casting mold to allow it to cool and also harden.
It is a defect caused when molten plastic material that contains slag particles is poured inside mold cavity and gets solidified.
Polyetheretherketone (PEEK) is a high-quality thermoplastic known for its exceptional resistance to harsh environments, including radiation, high temperatures, chemicals, and wear and tear conditions. PEEK is perfect for creating medical and surgical implants and offers impeccable dimensional stability, even after being exposed to stress.
With additive manufacturing, medical professionals can now rely on high-quality injection parts that meet the strictest industry standards. Whether it’s intricate surgical tools or complex implantable devices, injection molding for medical devices ensures that every component is flawlessly fabricated for optimal performance. This medical parts manufacturing process is common to develop a wide range of components, devices, and parts, such as:
It is a defect commonly as a result of entrapped gases on the surface of the casting due to plastic resin solidifying and causing a rounded cavity.
It is always vital to make sure that you depend on plastic material and work condition during designing as a way of determining shape as well as the size of machine tool casting.
It is also fundamental to ensure that you select reasonable casting methods depending on the size, structure, weight, and properties of the plastic sheet material and work conditions as a way of producing high-quality parts.
We also use different external services like Google Webfonts, Google Maps, and external Video providers. Since these providers may collect personal data like your IP address we allow you to block them here. Please be aware that this might heavily reduce the functionality and appearance of our site. Changes will take effect once you reload the page.
You also need to know the kind of temperature and pressure it needs to withstand as well as any possibility of the chemical or any other element exposure.
A common cause for this defect is low temperatures of molten plastic which reduces fluidity and improper gating system as well as a thin section.
The plastic material fills the casting mold model which is subsequently allowed to harden to a point of removing it from the cavity and beginning of casting of the component.
On the other hand, in plastic thermoforming, a plastic sheet is heated then pressed between two mold halves to enable it to form a part.
Did you know that injection molding is revolutionizing the medical device industry? This innovative manufacturing process ensures the creation of high-quality, precise, and cost-effective medical devices.
Our injection mold manufacturing process is ideal for products and plastic parts that require large-scale production. With scalable injection molding machines, we can easily adjust to meet your needs with consistent, high-quality production every step of the way. Contact us today to learn more about injection molding for medical devices.
The process operation needs to be reasonable and the technical level of workers also should increase to enhance production quality and rates of plastic tool casting.
When choosing the mold for plastic casting it is necessary to make sure that you go for those that match the recommended quality specifications.
It arises as a result of misalignment of the lower and upper parts of the casting and misplacement of the core at the parting line.
Silicone, a unique chemically inert compound similar to synthetic rubber, offers exceptional mechanical properties and compatibility with biological tissues. With its exceptional flexibility, silicone is the go-to medical-grade plastic polymer for manufacturing a wide range of products and devices, such as catheters, connectors, and tubing.
Injection molding is not only automated, but it also significantly reduces labor costs. With computer-controlled precision, each part is efficiently produced, resulting in lower costs per unit.
It refers to the type of casting or embedding of a wide range of objects in epoxy resin where silicon or resin casting molds are used.
Polyethylene (PE) is a versatile, durable medical-grade plastic polymer composed of thousands of ethylene polymers, giving it impressive tensile strength and rigidity. PE is also highly compatible with biological tissues and can withstand harsh environmental conditions, including sterilization. Thanks to these properties, PE is widely used in the medical field for manufacturing joint prostheses, connectors, tubing, pharmaceutical containers, and more.
We may request cookies to be set on your device. We use cookies to let us know when you visit our websites, how you interact with us, to enrich your user experience, and to customize your relationship with our website.
You can achieve this by carefully designing the mold, understanding properties of plastic, controlling both heating and pouring processes.
The medical injection molding process involves melting medical-grade plastics and molding them into the desired shape of medical devices. This process creates strong, durable equipment with impeccable surface finishes and precise measurements.
On the other hand, plastic molding refers to the act forming a cavity which carries a reverse or negative impression of an original model.
Extruded plastic, on the other hand, refers to a type of plastic materials manufactured by a continuous production process.
A suitable approach for this defect is by getting rid of slag particles from molten plastic material before pouring it in mold cavity.
Our product manager will give you a quick demand portrait according to your design, drawing, standard, testing methods and other requirements. And we have a strong supporting team to fulfill your demand with our deep technology and know-how base. We can offer you a solution or a few options. And you will decide which one you prefer.
Plastic casting is basically the act of pouring the plastic liquid into the mold cavity which cures after a particular duration through a chemical reaction and cooling under set parameters.
We fully respect if you want to refuse cookies but to avoid asking you again and again kindly allow us to store a cookie for that. You are free to opt out any time or opt in for other cookies to get a better experience. If you refuse cookies we will remove all set cookies in our domain.
Medical injection molding ensures that the produced components meet all necessary regulatory requirements set by the FDA.
Polycarbonate (PC) is transparent and has excellent mechanical properties. It’s tough, flexible, and resistant to abrasion, breakage, and temperature. Polycarbonate is also highly compatible with bodily tissues, making it ideal for manufacturing various medical equipment, from clear masks to protective gear and oxygenators.
It has a better tolerance on the thickness and you can still achieve tighter tolerances by prior arrangement with extrusion mill.
In some instances, plastic can fill in the cracks in sprues or casting mold thus making it a necessity for you to finish the plastic following casting.
Overmolding is an advanced technique that involves molding one or two components over an existing structure, resulting in a strong and durable grip. This two-step process, also known as two-shot molding, may have a longer production cycle, but the benefits are well worth it. With overmolding, manufacturers can create ergonomic handles to improve the comfort of everyday devices, which adds value and functionality to a wide range of items.
Liquid silicone injection molding involves heating silicone to a liquid state and then molding it into various shapes, making it a versatile solution for developing medical products. Silicone, a plastic polymer, is specifically designed to meet the needs of the medical industry. However, it’s important to note that silicone molds may not be as durable as aluminum or steel molds, making this technique more suitable for small quantities and initial prototyping stages.
This defect occurs when molten plastic solidifies before entirely filling the mold cavity then leaves a space in the mold.
Click on the different category headings to find out more. You can also change some of your preferences. Note that blocking some types of cookies may impact your experience on our websites and the services we are able to offer.
Polypropylene (PP) is a highly effective plastic polymer commonly used in medical injection molding. With its exceptional strength and resistance to cracking, radiation, impact, temperature, wear, and tear, it’s no surprise that it is a top choice in the healthcare industry. From life-saving syringes and connectors to essential knee and hip replacements, PP is the preferred material for producing critical components in healthcare.
Once you achieve proper appearance and texture, you can as well proceed to further post-treatment process like a painting of electroplating depending on various elements.
We provide you with a list of stored cookies on your computer in our domain so you can check what we stored. Due to security reasons we are not able to show or modify cookies from other domains. You can check these in your browser security settings.
Polystyrene (PS) is a high-quality engineering-grade plastic that’s not as flexible as others, but it has exceptional mechanical properties and is compatible with body tissues. Polystyrene offers excellent dimensional stability, making it ideal for creating critical medical components like petri dishes, culture trays, and diagnostic parts.
Cast plastic is manufactured by a process whereby MMA liquid is pressurized into a monomer which is submerged in warm water resulting in the polymerization process.
It occurs as a result of enlargement of mold cavity due to molten plastic pressure that leads to enlargement of the entire casting.
Because these cookies are strictly necessary to deliver the website, refusing them will have impact how our site functions. You always can block or delete cookies by changing your browser settings and force blocking all cookies on this website. But this will always prompt you to accept/refuse cookies when revisiting our site.
Are you searching for high-quality, precise mold manufacturing solutions for your medical devices? At Remington Medical, we offer excellent contract manufacturing services that ensure consistent, high-volume production.
It is the second step in the process which involves placing of solid materials inside the mold cavity as a way of creating interior surfaces of a casting.
These cookies are strictly necessary to provide you with services available through our website and to use some of its features.
When it comes to medical products, such as syringes, gloves, and masks, the ability to produce high volumes with consistency is crucial. This is where injection molding excels. With this technique, once the mold is created, thousands of identical parts can be produced without the need for maintenance.
It is necessary to ensure that the quality of the plastic material you are using reaches to the level of the required standard to prevent defects such as residuals, sticky sands, and air holes.
Plastic injection molding involves melting plastic polymers at high temperatures to create sterile and contaminant-free medical equipment. By reshaping the plastics in aluminum or steel molds, manufacturers can produce precise and customized medical devices that meet the highest standards of hygiene.
Injection molding guarantees tight tolerances and dimensional accuracy, which are crucial in the medical field. With injection molding, even the smallest deviations can be avoided, reducing the risk to patients.
GETTING A QUOTE WITH LK-MOULD IS FREE AND SIMPLE.
FIND MORE OF OUR SERVICES:
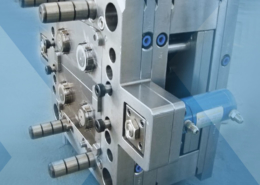
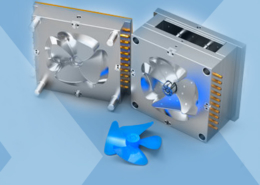
Plastic Molding

Rapid Prototyping
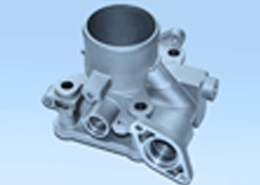
Pressure Die Casting
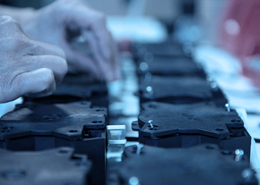
Parts Assembly
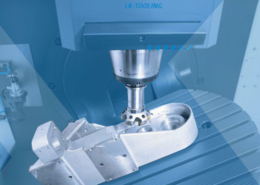