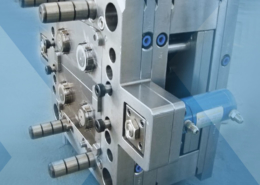
Basics of Plastic Injection Molding - mold plastic injection
Author:gly Date: 2024-10-15
When a manufacturing facility comes bigger, so does their profit, as they will have to pay off the factory rent, human expenses, and managing cost to maintain their running. However, these will make your injection molding expensive. So if you work with a small injection molding company, everything is based on lower pricing.
Lastly, it’s the space or area cost where the injection molding process is conducted. Again, depending on the production scale and the number of parts you need to be manufactured in the given amount of time, the space demands can differ from project to project.
The more complicated you parts are, the more money you would spend. Keep the part design simple is the most important factor for cheap injection molding. Undercuts on the parts add both tooling and molding production cost. Most of the undercuts could be avoidable if you redesign your part.
Nave ISK-8, Parque Industrial y Logístico Sky Plus, Avenida Mineral de Cinco Señores No.100, del Parque Industrial Santa Fe, Silao de la Victoria, Guanajuato, México
With labor advantages, offshore injection molding like China is mostly competitive on pricing. However, you may compare China pricing with onshore’s, especially for a small run of 25 or 50 pieces. In this case, China injection molding may not be cheap, as local companies could use Aluminum molds Also, consideration on international shipping cost and lead time are also necessary.
The process of injection molding may not cheaper than you thought. For some parts, use other processes like 3D printing, CNC machining, blow molding or plastic extrusion could be more cost-effective. To give you an example, the below part design is much cheaper than injection molding: extrusion mold cost of US$1000, comparing injection mold cost US$3500.
In addition, additional production factors and demands like product complexity, expected production quality, material, and the product’s size also contribute to extending or minimizing the costs.
When determining the overall cost involved in injection molding for any kind of project, it’s essential to consider each expense you will have to bear during the production process. From the raw material to the operation, and even the repair costs as well as tool costs, each factor collectively contributes to evaluating ‘how much does injection molding cost?’
As we all know, mold is the premise of the injection molding process. When the amount of products produced by injection molding is large, the mold cost may be negligible. But when the amount of injection molding products is small, mold cost will be a large part.
Once you understand every phase and the types of costs involved in every phase of the injection molding process, it is easier to determine the cost of plastic injection molding. As a result, with an estimated cost, you can ideally use, cater, and manage the injection molding cost to attain efficient part product outcomes.
Next up is the cooling phase involved in the injection molding process. This phase involves cooing the plastic inside the mold, which begins once the plastic comes in contact with the interior mold. Slowly, as the plastic cools and starts hardening, it takes the desired shape per the mold. However, the plastic part often does shrink slightly during this cooling phase.
While this is a process of wooden table production and the different costs involved, manufacturing plastic or rubber items through the injection molding process also comprises multiple processes and relevant finance demands. Since the injection molding process is focused on shaping products by injecting heated material inside a mold, multiple products and processes involved in this manufacturing method are involved in the overall injection molding cost.
Hence, understanding the injection molding cycle and the time each process takes can make it easier to plan the injection molding cost estimate to acquire this result. Does that sound like an intelligent plan to manage budget planning and financial investment? Then, let’s dive into the details of each stage and the time it takes!
Later, the pellets begin to melt due to the heat around the barrel and the pressure incorporated by the machine. As per the volume of the injected material, called ‘shots,’ the injection time and process are usually complete when the shots reach 95%-99% or the mold is filled.
So how do you evaluate the injection mold cost? Let’s go ahead and explore the detailed overview of these costs and how you can evaluate them per each process involved in injection molding.
In addition, the type of mold used in the machine is also involved in the material cost, as it affects the quality of the finished product.
Also, keep the less molding processes as less as possible. Co-molding or overmolding seems great for bonding 2 plastic part together, but it is expensive as well. There’s solution like to make 2 separate parts, not via co-molding to save the injection molding cost. For overmolding, you may consider tapping the plastic parts manually by end users. This is often seen like fan shrouds of a battery or electronics housings.
Once the cooling period has elapsed and the part has wholly taken its form, the mold can be reopened in the final stage.
To some customers, this could be difficult to decide. They would say: “well, I don’t know. It’s a new product, let the market decides” or “just give me the price, you don’t have to worry about the quantities”. Actually, an unsure mold life will surely make the injection molding not cost-effective. Why? The mold maker will have to use a longer mold life in case you need an increasing volume in future. So no mold life equals to longer mold life to injection molding manufacturers.
In other cases, the customers brief the molders the mold life clearly, like 1,000 pcs per order. 50,000 pcs for mold life. This will send them a message: the project is for the low volume of injection molding, and it should be as cheaper as possible. In China, mold makers might consider making the mold as below to lower the mold cost:
The second phase of the injection molding process is the injection phase. In this phase, the plastic pellets are fed to the mold using a hopper in the injection molding machine. The injection unit in the machine pushes these pellets toward the mold.
When it comes to the injection mold cost involved in the cooling phase, evaluating the time taken by this phase is crucial. It can evaluate this time through the wall thickness and the thermodynamic properties of the plastic part. The longer or less time this phase takes, the faster or later the machine can stop working, and the mold can be opened.
Cheap injection molding is essential especially when you have a limited budget for a new project, or just need a low volume of injection molding production. There is another reason why you need low-cost injection molding: your volume is high, but the end users need affordable plastic parts, like dispensable razors, plastic caps for toilet cleaners.
Once the ejection is completed, the mold can be shut down and used for another shot’s ejection process. In this final stage, the pressure and time taken to eject the mold is also a factor that should be considered to determine the cost of injection molding.
Once you have evaluated every factor that may cost you a certain amount when using the injection molding process for a project, is that all? Probably not! It’s just as crucial to consider, understand, and evaluate how each expense takes place. The whole injection molding process may last from 2 seconds to 2 minutes. However, the limitation or extension of time for each phase involved in this process can also extend or minimize the costs.
If you’re opting for the injection molding process for shaping and manufacturing plastic and rubber items for your business, you may be curious to know ‘what is the injection molding cost estimate’? Generally, when you’re opting for any manufacturing process, it’s evident that multiple stages/processes, materials, and additional requirements may need funding for the manufacturing process to proceed and complete. Whether it’s the simple manufacturing of wooden tables or plastic and rubber materials used in different industries like tech, hardware, etc., producing anything and everything is only possible if you can fund it.
Black is a popular color, which applies to a wide arrange of plastic housings. If white or clear colors required, the injection molding manufacturers will have to use many resins to clean their machines first to avoid leftover colors. Also, a cleaner injection condition is required to avoid black spots. So if you want cheap injection molding, sometimes you would have to give up using white or clear colors.
Lastly, the final phase of the injection molding process is the ejection process. As the machine’s last process, this process is handled by the ejection system. The machine pushes the part out with force when the mold is opened. Force is mainly used in this phase to smoothly push the shrunk part that may have stuck to the mold.
Now varying on the machine type and size, which depends on the project and how much clamping power the machine needs to incorporate on the mold halves, the time of closing and clamping the mold can be more or less. Simply put, larger machines may take more time, resulting in more plastic injection molding costs, whereas the smaller ones may cost less.
Of course, the above is just a list of the common basic costs of injection molding. There are also costs such as shipping, overhead, taxes, and other shared costs that affect the final injection molding cost. These costs are taken into account by the injection molding company during the injection molding quotation process.
Another crucial factor to consider when evaluating the cost of injection molding is the electricity expense. Since the entire injection molding process is carried out by machinery, electricity consumption is also exceeded.
The material cost is one of the high costs that affect the overall injection molding process budget. The material used for the part is of immense value in the molding process. The use of high-quality material for handling the injection process in the machine promises quality outcomes for the product/part, including better strength, durability, shape, and size.
It can be challenging to determine the estimated time to evaluate the injection molding cost involved in this phase. The main reason it had to determine the time and cost of the phase is the consistent changes in the flow of the plastic and its dynamic. However, it can evaluate the injection time if we consider other factors, including the injection pressure involved, the power applied by the machine varying on the project size and complexity, and the shot volume.
A) use a Multi-cavity molding solution if you have many parts. This will lower the setup tooling cost much. B) use a non-prehard mold steel like 738H. C) use existing mold base they have to save more mold cost. D) make a simple mold design like manual molding solution, not automatic.
Nevertheless, Let’s look at the average cost of injection molds first. On average, the injection mold cost for small and simple cavity injection molds is around $1,000 – $5,000. However, as per the size extension and complexity of the molds, the injection molding cost can increase up to $80,000 or more. So different factors, processes, and types of expenses involved in the production process handled through injection molding can be different for different users.
Whether your volume is 100,000 units or 100 units to start, in today’s post, I’ll share 6 practical tips you can use to get your own cheap injection molding.
Cheap injection molding is possible if you get it right. Make a simple part design, communicate with your injection molder, and compare advantages of offshore and onshore. You will save your money for your project.
Later, these halves are attached with an injection molding machine, where one-half is placed on the side. Once the machine starts running, the material is injected while the clamping unit consistently pushes the halves together. The machine holds these closed halves tightly together as the material is injected.
For instance, if we talk about making wooden tables, electricity costs, wood costs, base and structure cost of the table, machine and equipment cost for cutting and drilling the wood, and additional décor items cost to finish the final look of the table – all of these are essential to build and complete a table that is ready to be sold and used by a potential customer.
The artificial cost is also included in the overall injection molding cost estimate. This cost is mainly the expenses involved in the related departments. In simpler terms, the costs created by one department by utilizing other departments’ services within a company or manufacturing setup are known to be the artificial cost.
Depending on the type of machine, the pressure the machine invests on the part, and the time the machine runs, the electricity cost can differ for producing one or more parts of different kinds.
The very first stage that should be considered for evaluating the injection mold cost for your project is clamping. The primary purpose of the clamping stage is to close both halves of the mold before the mold is injected with the material. Hence, these halves are closed with the help of a clamping unit.
And varying on the production type, complexity, and expected final product, these costs can either be very minimum or a decent part involved in the overall injection molding cost.
Now the injection pressure usually ranges from 35-140 MPa. At the same time, you can evaluate the additional two factors by reading the hydraulic system in the machine once you complete the injection process for one product.
Another crucial factor to consider when evaluating the cost of injection molding is time. When you consider professional and reliable manufacturing companies that offer you various services and manufacturing process solutions like injection molding, they highly consider the time taken in the production process, varying on how long the machine is used. Simply put, manufacturing factories highly prioritize time when managing the injection molding process on a budget is an additional cost factor. Therefore, the time of an injection cycle is very important. That’s what we are about to talk about.
GETTING A QUOTE WITH LK-MOULD IS FREE AND SIMPLE.
FIND MORE OF OUR SERVICES:
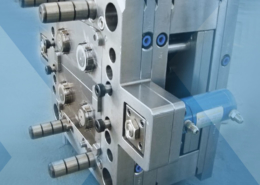
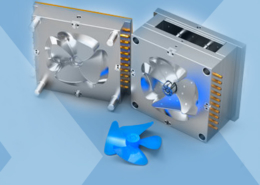
Plastic Molding

Rapid Prototyping
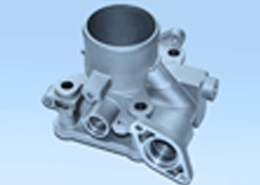
Pressure Die Casting
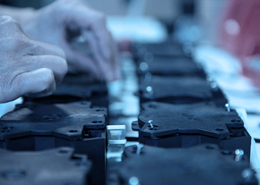
Parts Assembly
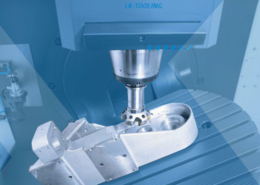