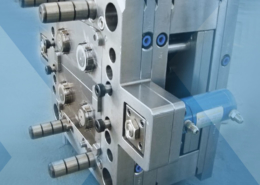
B.J. Plastic Molding Co. - plastics molding co
Author:gly Date: 2024-10-15
At their core, both injection molding vs plastic extrusion shape plastic into specific structures, catering to various product requirements. For instance, while plastic extrusion is preferred for creating long, continuous products like pipes or window frames, injection molding excels in producing items like bottle caps or automotive parts.
Plastic extrusion operates on a continuous manufacturing process. Resin pellets are heated and then extruded through a specific die to acquire their final shape. Unlike the cyclic nature of injection molding, this continuous process can generate products of various lengths, meeting different industry demands.
Acrylics are weather resistant which means they are durable and can withstand storms, winds, and heavy rains. There is no degradation in transparency which is why the clarity also remains the same, unlike glass.
These examples highlight the unique strengths and applications of plastic extrusion vs injection molding, emphasizing their significant roles in shaping advancements across different industries.
Plastic extrusion excels in creating large, uniform structures, evident in products like expansive piping systems and car bumper profiles. Conversely, injection molding specializes in crafting smaller, detailed components, including the internal parts of appliances like washing machines or microwaves, highlighting its precision and attention to detail in production.
PMMA has unique properties such as low density, biocompatibility, UV resistance, easy molding, and delivering aesthetics while being cost-effective. PMMA has thus become a popular biomaterial for dental applications. It is commonly used for prosthetic dental applications such as the fabrication of artificial teeth, denture bases, dentures, orthodontic retainers, and crowns, and the repair of dental prostheses.
Plastic manufacturing features two methodologies: plastic extrusion and injection molding. Both have been instrumental in sculpting the landscape of the products we see and use daily. These disparities highlight the need for a comprehensive understanding to ensure efficient usage.
Acrylics are inherently stable to UV light which is why PMMA is used for many outdoor applications such as solar panels.
Acrylic is one of those rare plastics that combine high-performing characteristics with beautiful aesthetics. The aesthetics can be customized according to the designers in the form of color, finishes, and effects. In addition to the furniture and design industry, acrylics are a popular plastic of choice for manufacturing photo frames, clear table tops, and storage plastic parts.
Plastics are our business. We manufacture plastic profiles in ABS, PVC, nylon, polycarbonate and more. No design is too simple or too complex for us to design or manufacture. We even offer custom materials and designs to meet your needs.
PMMA can be molded into developing complex designs. PMMA injection molding process can reproduce a significant number of complex products that are identical in terms of shape, size, and weight.
Further developments and advanced technology developed a far more accessible and cost-effective PMMA that could be used for consumer applications. This particular development made PMMA a versatile plastic whose application spreads today, across several industries!
PMMA is considered to be a better alternative to Glass. Glass is generally expensive, heavy, and can be unwieldy. E.g. iPhone screens are usually Gorilla glass and they are thus, heavy-weighted and expensive whereas various other brands use acrylic plastic for the screen displays thus, making the phones lightweight and relatively cheaper.
PMMA grades are known for their transparency! It allows 92% of the light to pass through, which is more than glass or any other plastic. This outstanding clarity makes it an ideal plastic of choice for various applications in the automotive, aviation, and marine industry such as rear lights, windshields, and plane windows.
With numerous products surrounding us, each shaped and formed through one of these techniques, understanding the contrast between them is essential. In this blog, we’ll unravel the complexities of these two techniques, shedding light on their evolution, methodologies, and significance.
Achieving optimal product quality mandates precise control over temperature and pressure. Whether it’s ensuring the clarity of a polycarbonate sheet through extrusion or the exact dimensional accuracy of a molded gear, the precision in these processes is paramount.
Both methods involve melting plastic resin, a critical step ensuring the material’s readiness for shaping. This melting ensures the material can be molded into intricate designs, whether it’s the detailed grooves in a plastic toy from injection molding or the consistent tubing for medical devices from plastic extrusion.
In addition to prosthodontic applications, PMMA can be applied to a wide range of medical applications such as diagnostics, and incubators.
VEM Tooling has the expertise for your PMMA injection molding project. At VEM Tooling, we ensure that receive a great experience and dependable service! To better understand how VEM tooling can serve you for your PMMA injection molding project, contact us or request a quote today.
Keller Products is a leading plastic extrusion manufacturer based in Manchester, NH. For over 40 years, we’ve been manufacturing plastic extrusions, plastic extruded products, coextrusions, hollow profiles, recycled profiles, custom profiles and more..
Keller Products is a leading plastic extrusion manufacturer based in Manchester, NH. For over 52 years, we’ve been manufacturing plastic extrusions, plastic extruded products, coextrusions, hollow profiles, recycled profiles, custom profiles and more.
Acrylics typically allow 92% light transmission which is greater than glass or any other plastic. This light transmission property enables the acrylics to exhibit outstanding clarity. PMMA can thus, be applied in various optical-related applications.
The essence of both plastic extrusion and injection molding lies in the transformative journey of plastic resins into tangible, functional products. Be it the intricate components of your vehicle or the sleek case of your mobile phone, these methods involve a meticulous process of heat application, pressure management, and design precision. Their foundational principle remains to convert raw materials into products, but the approach varies widely.
Acrylics are more flexible, lighter in weight, and exhibit more impact resistance than glass. They are easier to mold and fabricate according to the design specification. Additionally, Acrylics exhibit better insulation properties than glass which makes them perfect for skylights.
At Keller Plastics, our legacy is built upon the twin pillars of plastic extrusion and injection molding expertise. Whether your project demands the continuity of extrusion or the finesse of injection molding, we’ve got you covered. Reach out to us for precision-driven results.
Photovoltaic modules of solar panels are continually exposed to harsh environmental extremes such as sunrays and rain. Thus, the solar panels undergo constant stress which is why acrylics are a popular choice for photovoltaic solar modules. PMMA is durable, can withstand stress, and is weather-resistant which is why it is the perfect economical choice for solar applications.
PMMA was first discovered by a German chemist named Otto Rohm in 1901. The PMMA discovered in 1901 was in its most novice and preliminary form and it could not be used for commercial purposes as we use it today. It thus later underwent various developments and by 1943, a more processible form of the PMMA version was developed which created a version of PMMA that can be cured at room temperature.
The cooling rate of acrylics is fast thus, the plastic parts are easily stressed. The high and low control of injection mold temperature should be strictly maintained to avoid this. The general injection mold temperature should be controlled at 40-80℃ / 104 – 176°F.
PMMA, abbreviated for Polymethyl methacrylate, is a transparent and rigid thermoplastic. PMMA is a polymer that is produced through the polymerization of monomer methyl methacrylate.
PMMA beads or pellets which are usually the starting material should be free of solvents to avoid the formation of bubbles. This is achieved by drying. PMMA Injection molding is the same process as conventional injection molding:
The nuances of plastic extrusion vs injection molding, from the uniformity of extrusion to the meticulous detail in injection molding, remain central to creating products that shape our everyday lives. Each technique, with its distinct advantages, caters to varied industrial needs — whether it’s the expansive structures in automotive or the precision in consumer electronics.
Extrusion vs. injection molding plays a pivotal role in the automotive industry. Modern vehicles frequently utilize extrusion for parts like weatherstripping profiles and specific conduits, given its strength in forming extended structures. In contrast, injection molding, with its precision, is commonly chosen for the finer components of vehicles, such as dashboard elements, control buttons, and intricate details within the car’s interior.
Acrylics can be mixed with resins to create a wide variety of colored products. It can be further modified to improve a specific property. This is generally achieved by incorporating additives. These modifications are typically performed
Plastic extrusion is responsible for creating many everyday items, such as plastic tubes for your toothpaste or creams. On the other hand, the precision of injection molding lends itself to the production of finer details, resulting in components like the keys on your computer keyboard or the buttons on your remote control. Indeed, plastic extrusion vs. injection showcases a spectrum of products, with extrusion typically suited for continuous forms and injection molding excelling in detailed, specific designs.
Highlighting these shared features showcases the fundamental principles behind plastic extrusion vs injection molding. While each method offers unique advantages and processes, their common ground is instrumental in the successful evolution of plastics manufacturing.
In medical technology, the precision and adaptability of plastic extrusion vs injection molding are highly valued. While extrusion primarily creates tubes found in many medical devices, injection molding is the preferred method for producing intricate tools, detailed instrument components, and essential parts of diagnostic devices, showcasing its consistent precision.
The thermal stability of PMMA injection molding is medium and the thermal decomposition temperature is slightly higher than 270℃ / 518°F. For screw-type injection molding machines, the barrel temperature should be controlled at 180 – 230℃/ 356 – 446°F.
It’s crucial to note that while both processes transform plastic resins into finished products, the method and cycle of production differ substantially between plastic extrusion vs injection molding.
The selection of materials in plastic extrusion vs injection molding can be influenced by the demands of the specific process and the desired attributes of the end product:
Plastic extrusion and injection molding serve as the backbone of modern plastic manufacturing, producing a vast array of items, from the most basic household essentials to specialized, intricate components. The importance of products crafted through these techniques underscores their significance and versatility in shaping our everyday world.
In plastic manufacturing, industry professionals must recognize the distinctions between plastic extrusion and injection molding. Both methods play crucial roles in transforming plastics, but they follow different processes and are better suited for distinct applications.
Call us! (603) 446-6916 or email us at sales@kellerproducts.com Home About Us Why Keller? History of Keller Products Corporate Leadership Markets Served Sustainability Our Blog Capabilities 3-D Printing Custom and Recycled Plastic Manufacturers Free Design Engineering Manufacturing Capabilities Materials Polycarbonate PCV (Polyvinyl Chloride) Polystyrene Plastic Extrusions Advantages Of Extrusion Custom Plastic Extrusions Premium Thermoplastic Extrusions at Keller Plastics Specialty Plastic Profiles Antimicrobial Profiles Bio-based Biodegradable Plastics Flame Retardant Profiles Glow-in-the-dark KelBrite Medical Profiles Nanotechnology Profiles NSF/Latex Free Profiles Recycled Plastic Profiles Wood Composite Profiles Free Tooling Request a Quote Contact Us Employment
PMMA is also a cost-effective alternative to polycarbonate. If polycarbonate is too expensive to be applied to a project, PMMA is an excellent alternative. This is especially the case if the plastic requires a clear appearance bu not the properties of polycarbonate. There are various applications where one would prefer PMMA over polycarbonates such as jewelry, plaques, aquariums, windows, and display pieces. PMMA is comparatively lightweight and inexpensive in such cases.
In plastics manufacturing, understanding the distinct characteristics of plastic extrusion vs injection molding is crucial. However, it’s also essential to highlight their shared aspects, as these commonalities reinforce the foundational techniques of the industry.
An extrusion house is only as good as its capabilities. From standard plastic extrusion designs to coextrusions, hollow profiles and more, we do it all. We also offer 3D printing and free design engineering assistance to our customers.
Since the viscosity of PMMA melt is high and the flowability is poor, the injection pressure should be maintained high at 80-120 MPa / 11603-17404 Psi. The holding pressure is 40-60MPa / 5801-8702 Psi.
Extruded Acrylics are produced through the extrusion method. Extruded acrylics are produced by pushing acrylic mass through a form thus, depending upon the direction of the flow, they have varying properties. Due to the production process, they are heterogeneous. Some of its properties are listed below:
PMMA exhibits excellent optical clarity, high light transmittance property, surface hardness, and scratch resistance which are important properties for electronics that would be used on a regular basis. Due to these properties, acrylics are widely applied to manufacture LCD screens, TV, and mobile phones.
Consumer electronics have greatly benefited from both manufacturing processes. Extrusion often crafts components like protective sheaths and conduits in various gadgets. However, when precision is required, as in the compact internal components of smartphones and tablets, injection molding steps up, delivering detailed and uniform parts with consistency.
Since PMMA is lightweight and resistant to salt and cleaning products, it is extensively used for manufacturing windshields and windows. PMMA is also used for windscreens, windows, and canopies in airplanes as it can resist high inside cabin pressure and harsh UV radiations.
PMMA provides excellent optical clarity, light transmission, and color accuracy which is why it is extensively used in exterior, rear, and indicator light covers of the automotive.
Both plastic extrusion and injection molding offer diverse solutions in plastic manufacturing. The choice between them often rests on the requirements of the specific product, the desired material, and the production process itself.
As injection molding developed and became more integral to manufacturing, PMMA became even more versatile and the ‘plastic of choice’ for various manufacturers! Today PMMA gets injection molded into countless products.
In the dynamic sphere of plastic manufacturing, a frequent point of contention or confusion lies in discerning the fundamental differences and applications of plastic extrusion vs injection molding. Though seemingly similar, these two processes serve distinct purposes and have unique advantages.
Call us! (603) 446-6916 or email us at sales@kellerproducts.com Home About Us Why Keller? History of Keller Products Corporate Leadership Markets Served Sustainability Our Blog Capabilities 3-D Printing Custom and Recycled Plastic Manufacturers Free Design Engineering Manufacturing Capabilities Materials Polycarbonate PCV (Polyvinyl Chloride) Polystyrene Plastic Extrusions Advantages Of Extrusion Custom Plastic Extrusions Premium Thermoplastic Extrusions at Keller Plastics Specialty Plastic Profiles Antimicrobial Profiles Bio-based Biodegradable Plastics Flame Retardant Profiles Glow-in-the-dark KelBrite Medical Profiles Nanotechnology Profiles NSF/Latex Free Profiles Recycled Plastic Profiles Wood Composite Profiles Free Tooling Request a Quote Contact Us Employment
Cast Acrylics are produced by mixing acrylic liquid ingredients in molds. During the production process, the liquid ingredients are pumped into a mold which is then submerged in warm water, and here, the polymerization takes place. Some of its properties are listed below:
PMMA is commonly known as acrylics. Some of its common trade names are Crylux, Plexiglas, Acrylite, Lucite, Perclax, and Perspex. PMMA sheets that are of the glass type are called Plexiglass. It is also used in high-end applications such as hip replacement and lenses for eyewear.
Acrylics are not only cost-effective but also more durable than glass. It demonstrates more impact resistance than glass (Usually 10X more). Additionally, Acrylics offer a lustrous shine and a glossy finish!
PMMA demonstrates excellent physical properties such as extensive tensile strength, great flexural strength, and transparency, like glass. One of the most prominent properties of PMMA is that it resembles glass and it is thus often used as a replacement for glass. Additionally, it is a tough plastic material and is an excellent cost-effective alternative to the less resilient glass material.
Standardization and quality are part of our companies core values. We deliver the best possible experience and product to our customers, every single time consistent. Take a look at our certificates!
Acrylics have a water absorption rate of 0.3-0.4%. For injection molding, it should be below 0.1% of the temperature i.e. usually 0.04%. The presence of water leads to air bubbles and the formation of airlines thus, PMMA resins need to be dried well before introducing them into the barrel.
es of the polymer, usually targeted toward specific applications. Examples of the properties that can be adjusted in this way are impact resistance, chemical resistance, light diffusion, UV light filtering, or optical effects.
Acrylics are not toxic in their final forms but during production, their manufacturing process releases minute amounts of toxic fumes. Comparatively, the production of toxic fumes is not the same as other materials. Acrylic is classed as non-hazardous under OSHA regulations as it is one of the few materials that has very low toxic fumes released during its production and the final form is free of toxicity.
PMMA was processed extensively to be further developed such that it can be molded into complex shapes that are required for the biological environment. The earliest application of PMMA was in dentistry and it was later extended to orthopedics for thigh and hip replacements. Since PMMA was lightweight, easily processed, and demonstrates low toxicity, it found various applications in the medical industry. It was, however, not cost-effective and thus, restricted for a while to the medical industry.
Cast Acrylic is harder than extruded acrylic and is thus, more scratch-resistant. The manufacturing process of casting is labor intensive thus, cast acrylics are more expensive. Cast acrylics are homogenous and therefore have equivalent properties.
The manufacturing process of acrylic products can release highly toxic fumes thus, it needs to be handled with precaution. Anyone who is handling acrylic sheets should be provided with appropriate protective equipment and clothing. If not handled properly and the right precautions aren’t taken, acrylics could blow up during polymerization.
In contrast, injection molding is characterized by its batch production cycle. Heated plastic is introduced into a predefined mold cavity, and then cooled. The mold is released upon cooling, producing a product that stands out for its precision and design. Due to its batch nature, it’s particularly effective for items that demand consistent replication and high levels of detail.
Acrylics do not turn yellow in the sun. Acrylics are also not affected by UV rays. They are thus ideal for shed windows and colored skylights. They are also popularly used for panels in home projects.
In addition, PMMA has also been considered a safer option than polycarbonates as bisphenol A in polycarbonate has the potential to be hazardous.
PMMA abbreviated for Polymethyl methacrylate is commonly referred to as acrylics. PMMA injection molding is a process where molten acrylic is injected into a cavity which upon cooling and hardening forms various types of plastic products. PMMA is applied to manufacture various plastic parts such as car windows, aquariums, and mobile phone screens. In this article, we have focused on PMMA injection molding in-depth to help you understand if it’s the best-suited material for your project.
The versatility of plastic extrusion vs injection molding is prominently evident when looking at the myriad of applications across various sectors. These processes not only shape everyday items but are also instrumental in the advancement of specialized industries.
Acrylics demonstrate excellent scratch resistance. In addition, they can be processed toward featuring a glossy lustrous finish. These properties, combined with PMMA’s dimensional stability, enable its use in many different applications, such as automotive body parts, furniture, or kitchen. Additionally, acrylics are more scratch-resistant than any other glass product. In this manner, the molding process generates products that can maintain their lustrous appearances for a long time without degradation.
Acrylics can be modified according to the requirements. They are available in clear as well as various tints and colors. Acrylics can also be texturized to produce a variety of finishes. In addition, Acrylics are also incorporated with additives to exhibit a particular characteristic such as scratch- resistance or glare reduction.
Plastics are our business. We manufacture plastic profiles in ABS, PVC, nylon, polycarbonate and more. No design is too simple or too complex for us to design or manufacture. We even offer custom materials and designs to meet your needs.
PMMA has unique properties for the construction industry such as optical clarity and UV resistance. It is an ideal material for construction applications such as sound barriers, facades, aquaria, and greenhouses. PMMA also has high mechanical resistance and its reliability enables architects to build beautiful architectural monuments.
Both plastic extrusion and injection molding have a wide industrial footprint, crafting a range from daily essentials to specialized apparatus. For example, while plastic extrusions might produce plastic sheets used in greenhouses, injection molding is responsible for creating durable casings for electronic devices.
Acrylic has a density of 1.185 g/m3 – 0.00185kg/m3 whereas glass has a density of 2.4 g/m3 – 0.0024kg/m3 thus, PMMA plastic molding produces lightweight products and is an excellent alternative to glass.
GETTING A QUOTE WITH LK-MOULD IS FREE AND SIMPLE.
FIND MORE OF OUR SERVICES:
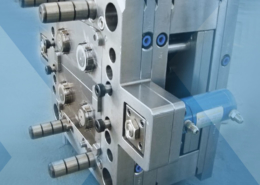
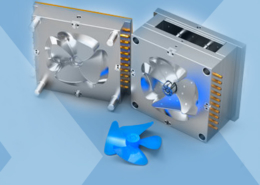
Plastic Molding

Rapid Prototyping
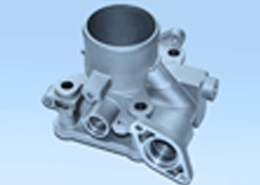
Pressure Die Casting
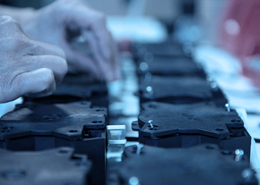
Parts Assembly
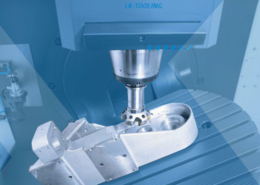