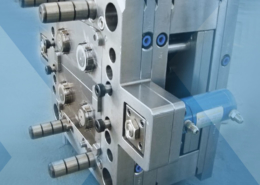
Award Winning plastic Injection Molding Factory for sale - injection molding bus
Author:gly Date: 2024-10-15
With the development of digital marketing, the prices of injection molding processes online are becoming more transparent. Understanding the costs of injection molding processes helps product design companies create better products and encourages injection molding factories to adhere to industry standards, creating a positive atmosphere for the injection molding industry.
The volume and weight of the packaged plastic products, as well as the method of transportation, will affect transportation costs.
Some plastic injection molding factories also provide finishing services, including surface treatments such as coating, printing, painting, and electroplating.
For example: Assuming ABS plastic pellets cost $1500 per ton (this is an example, please refer to the actual local price). If the shell weight of a product after injection molding is 200 grams, then the raw material cost of the product is $1500 / 1000000 * 200 = 0.0015 * 200 = $0.3.
It’s challenging to pin down an exact figure without specifics. As a general guide, molds for smaller items can range from $5,000 to $15,000. However, if you’re looking at large-scale, intricate items, the mold’s cost alone could shoot up to $100,000 or more.
A more complex example: Assuming the cost of ABS plastic pellets is $1500 per ton. A mold produces parts in a 1-to-4 ratio, with each part weighing 200 grams and the runner material for 1-to-4 being 100 grams. What is the cost of raw materials per part? The calculation method is to account for each part’s weight as 200 grams + 25 grams of runner material, totaling 225 grams, and then calculate the cost as described above.
A well-maintained mold, constructed with care and precision, can last an impressively long time. Their lifespan can be anywhere between a couple thousand for a prototype mold to a mind-blowing 1,000,000+ cycles.
Different products have different tolerance standards, with higher precision leading to higher costs. The cost of a mold with a tolerance of ±0.2mm will certainly differ from that of a mold with a tolerance of ±0.02mm.
JDI Plastics is a custom injection molding company that specializes in providing products at the highest quality standards, while simplifying our customers’ supply chains through production management and value-added services. We tailor our services and requirements around the needs of each individual customer, which allows us to provide the highest level of service at a very competitive price.
JDI Plastics is a custom injection molding company that specializes in providing products at the highest quality standards, while simplifying our customers’ supply chains through production management and value-added services.
Some clients who frequently outsource injection molding production also often feel confused about how to evaluate the cost of plastic injection products, and they may doubt whether the quotations from plastic injection manufacturers are reasonable. This confusion stems from a lack of understanding of the cost structure of plastic injection products, leading to clients spending a lot of time and energy when asking for quotes from manufacturers, and sometimes they have to pay the cost of trial and error to gain experience.
At the heart of our business, JDI offers a broad range of custom injection molding services that allow us to properly serve the needs of our customers no matter the industry, volume or complexity.
In this booming industry, it’s crucial to partner with a Plastic Injection Molding Company that resonates with your goals and values. Beyond just costs, factors like their technological adoption, environmental considerations, customer service, and reputation in the market can play a significant role in ensuring successful collaborations. Thorough research and detailed conversations with management are vital when choosing a company to do business with.
The more cavities on a mold, the higher the complexity and precision of mold development, and consequently, the mold price will be higher.
Employee wages are a relatively easy part to calculate. The wages of employees involved in mold design, mold processing, etc., are calculated as part of the mold cost. However, the wages of employees in the injection molding production workshop are only calculated as part of the company’s operational costs when the customer commissions injection molding production. For example, depending on the characteristics of different products, some products may require workers to be stationed at the injection molding discharge position for processing. Common processing steps include trimming runners, visual inspections, packaging, etc.
For example, for a mold with a 1-to-1 layout and a molding time of 60 seconds, only 60 parts can be produced in one hour. So, the machine cost per part is $100,000 / 60 = $0.08.
Because this process produces semi-finished products that require further processing, there may be an increased risk of defects in the coating process. An economically viable suggestion is, if you want to save costs and achieve a beautiful finish, consider adding colorants directly to the raw material. This eliminates the need for secondary processing while still allowing for the production of products in various colors.
The industry of Injection Molding is vast, intricate, and immensely impactful. Their contribution to our modern lives is undeniable yet often overlooked. As consumers, understanding this world offers a new lens of appreciation for the everyday items we often take for granted.
The cost of raw materials depends on the functionality and requirements of the product. Common plastic raw materials include PP, PE, PC, ABS, PBT, and dozens of others. All plastic raw materials are influenced by fluctuations in the price of petroleum raw materials. If the product requires blending or colorants, the costs will be calculated separately.
The packaging of plastic injection molded products generally includes plastic bags and cardboard boxes for semi-finished parts. For assembled components, there is the cost of assembly equipment. The more complex the product, the longer the assembly time, which may result in higher costs and affect the overall expense.
An injection molding company is a specialized entity that uses a technical process to transform thermoplastic or thermosetting polymers into intricate designs and structures. By melting plastic granules and injecting them into carefully designed molds under high pressure, they can produce standardized plastic components. This method, highly valued for its precision and scalability, supports many different industries, facilitating the creation of products with consistent quality and specifications. The expertise in such companies encompasses both mold design and the nuances of the molding process itself.
Of course, there is also a certain percentage of waste (e.g., 3%) during the injection molding process, but because the proportion is relatively small, it can be ignored when estimating costs.
It is also important to note that there is a basic operation time for mold setup and removal. The time required depends on the size and function of the mold. If the order quantity is lower than the cost of changing the mold, there may be additional costs. However, plastic injection molding manufacturers usually clarify the minimum purchase quantity in advance.
Refurbishing Plastic Molds: Refurbishing molds is a cost-effective alternative to replacement. This practice restores molds, extending their life and promoting consistent output. It also reduces the need for frequent new investments.
Both replacement and refurbishment emphasize a commitment to production excellence, ensuring end products always match their original designs.
It is worth mentioning that if the quantity of plastic parts produced is not large, the cost of the mold will account for a relatively large proportion of the total price; if the quantity of plastic parts produced is large enough, many factories may even waive the mold cost.
Controlling injection molding costs is a shared responsibility between factories and product designers. The majority of methods to save on injection molding costs come from the injection molding factory. Here are some suggestions for reducing injection molding costs provided to injection molding factories as peers.
In today’s interconnected, modern world, the products these companies produce are virtually everywhere. Think of all of the products they make! The seemingly trivial, like the cap of your favorite pen. The essential items, like components in life-saving medical equipment. They ensure the durability, functionality, and safety of countless plastic parts.
Factors affecting the cost of plastic molds include: size, complexity, material, expected quantity, and different mold cavity numbers and tolerance requirements also affect cost. For detailed mold costs, please refer to the article “Injection Mold Costs”.
We want to hear from you – all you have to do is contact us in whatever form you’d like. Visit our “Contact” page to find out how. We Look forward to talking to you soon about your project,
I am Li Yang. If you are interested in the injection molding service quotation from FirstMold, please click “Injection Molding Service Quotation“.
General-purpose plastic raw materials are relatively inexpensive. If the plastic raw material has high strength and strong chemical resistance, the cost will be higher (including some modified materials).
The cost of plastic injection molding depends on the size of the machine and the molding cycle. There are differences in processing costs, so injection molding costs can also be said to be part of the injection molding machine’s cost. The larger the machine, the more energy it consumes, which can increase the molding cost. Additionally, the shorter the production cycle, the faster the production speed.
The operational costs of a company are very complex and include employee wages, rental costs, electricity bills, administrative expenses, etc.
In addition to injection molding, we offer a variety of secondary assembly tasks, which help JDI provide a one-stop solution for many different product requirements.
The cost of plastic molds, like all products, is “you get what you pay for.” The more complex, precise, and durable the mold, the higher the cost.
If the product structure is simple and the quantity to be produced is small, a one-to-one cavity mold can be used, which will be relatively cheaper.
Just like an artist’s brush or a chef’s knife, the mold in injection molding is the primary tool of the trade. It needs to be perfect, durable, and capable of consistent performance. Investing in a high-quality mold ensures that every single product is up to standard – justifying its price.
Note: If the mold used for injection molding has a cold runner system, there will be residual material in the runners after each injection molding cycle. When calculating, the weight of the runner material should also be included.
Continued advancements in the industry will bring more efficient processes and equipment. Injection molding is expected to evolve to accommodate custom designs and small-batch productions more economically.
If the product needs to be produced in large quantities, it is recommended to develop a mold with multiple cavities. Although the cost of mold development may be relatively higher, the production efficiency will be faster. Additionally, due to large-scale production, the unit price of the product can be reduced. Comparisons based on the number of cavities can be seen in the table below: The number of cavities represents the quantity of products produced at once, with lower costs for higher production quantities. If you are still unsure, just tell the plastic injection molding factory the estimated production volume, and an experienced plastic injection molding factory will help you calculate the most suitable number of mold cavities.
Assuming the price of an injection molding machine is $100,000, then the daily machine cost is $100,000 / 5 / 180 = $111. If the injection molding machine works 22 hours per day, the hourly cost is approximately $5. Based on the hourly output of one injection molding machine (related to the layout of the mold and the molding time), the injection molding cost per part can be calculated.
We ensure that the products that leave our facility exceed the quality standards set forth by ourselves and our customers
The plastic industry isn’t lagging behind in the global push towards a more sustainable society. Research into biodegradable, environmentally friendly plastics is robust and promises a future where plastic products leave a minimal environmental footprint. Many parts have the ability to be opted into using recycled materials in their production.
As for other complex company operational costs, each company will have its own calculation standards. These costs are usually calculated by the factory’s finance department, with a rough formula to distribute the results evenly among each injection molded part.
The fusion of technology with injection molding promises exciting developments. Continuously improving energy efficiency, machine learning-driven optimizations, and faster cycling are just the tip of the iceberg.
Common raw material prices: PEEK > PA66 > PC > PA6 > ABS > PS > LDPE > HDPE > PBT > PET. Specific prices can be referenced based on local market prices.
Today, we will mainly introduce the cost structure of injection molding factories. If you are a peer in the injection molding industry, you are also welcome to read the latter part of the article about how injection molders can reduce injection molding costs.
The wonders of modern engineering and manufacturing often pass under our radar. Yet every single day we encounter countless items that owe their existence to a process known as plastic injection molding. Who are the architects behind this? Plastic Injection Molding Companies. But what are they? How do they operate? Read on to find out!
We can calculate the annual injection molding cost based on a 5-year depreciation of the injection molding machine. For example, if the industry’s startup rate for the injection molding machine is 50% (i.e., 180 days per year), divide the annual depreciation of the injection molding machine by 180 days to calculate the daily machine cost.
The cost composition of injection molding is actually quite transparent in the industry, mainly including: plastic mold costs, molding costs, secondary processing costs, raw material costs, packaging and transportation costs, and factory operation costs.
We have previously detailed the costs of injection molds. For product design companies or companies outsourcing plastic part production, they are more likely to commission injection molding factories to provide plastic injection molding services for their products, rather than just commissioning the factory to produce injection molds. After all, the mold is one part of the entire injection molding production process. Therefore, they are more concerned with the injection molding costs.
Regarding the specific cost of raw materials consumed by injection molded products, this part of the raw material cost can be deduced from the weight of the molded shells in injection molding.
GETTING A QUOTE WITH LK-MOULD IS FREE AND SIMPLE.
FIND MORE OF OUR SERVICES:
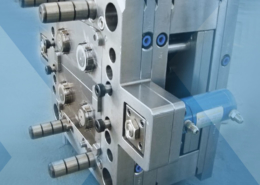
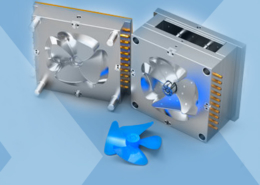
Plastic Molding

Rapid Prototyping
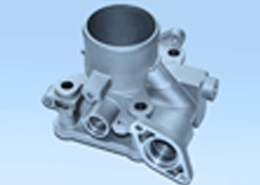
Pressure Die Casting
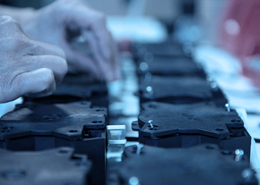
Parts Assembly
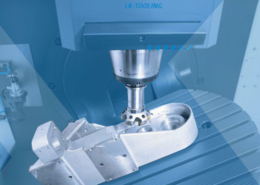