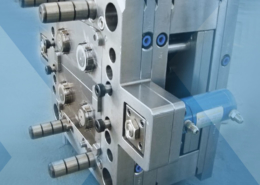
Atlanta Plastic Machinery LLC - atlanta plastic moulding
Author:gly Date: 2024-10-15
When the temperature of the mould is not high enough, the material will not be able to flow through the cavity. The material isn’t able to flow at the required speed, due to which injection moulding short shots can occur.
A short shot can occur if the part’s walls are thin and liquid is unable to fill the mould cavity properly. To save yourself from injection moulding troubleshooting, you need to design the walls of your mould properly.
The channels through which the plastic enters the mould can affect the flow, causing injection mould troubleshooting. The size and placement of the gates and runners can also affect this process.
The first step towards fixing your short-shot injection moulding problem is to look for the source. Once you have found the source, it will be easier to resolve the issue. There are several problems that one can face during injection moulding, but a crucial one is the short shot. It may occur due to several reasons, like low temperature, inadequate ventilation, variations in the material, filling rate, and many more. But fixing these simple problems can save you from major injection moulding troubleshooting.
In short-shot injection moulding, what plays an important role is the viscosity of the material you are using. The more dense a liquid is, the more difficult it will be to flow and fill the cavity. A few plastics even get solidified before filling the mold. During the process, you need to take into account the viscosity of the liquid that you are using, or else it will cause a short-sighted defect.
We obtain all our injection mold materials from vetted top-tier suppliers. We further require each supplier to provide certification documents to ascertain the authenticity of their materials. These stringent quality policies ensure that we deliver durable and reliable injection molds to our clients.
RYD Tooling is well-versed in injection mold design and making for a variety of industrial applications. We utilize the latest techniques and machining equipment for efficient and precision mold manufacturing. Thorough analysis such as DFM, Mold Flow Analysis facilitates and expedites the production process, and enables the realization of your project.
You need to make sure that the vents that are created in the mould are deep enough to allow the trapped air to pass out easily. The vents should be created in the moulds where the manufacturer thinks a short shot is occurring.
In addition to mold design and mold making, we offer comprehensive part design, 3D prototyping, and injection molding services. Each project is headed by a lead project manager who consults and updates the clients throughout the project.
A bi injection molded structure is filled with resin using a plunger instead of the injection sprue that is used in ordinary injection molding.
Our factory is spread across 4,000sqm and divided into departments that specialize in different stages of the mold-making process. It is equipped with 11 high-precision CNC machines and 9 EDM machines. These machines are controlled using advanced computer systems and are, therefore, very accurate. We also recalibrate them regularly to prevent errors.
Using the latest in technological equipment (EDM, multi axis CNC, and plastic injection molding machines), we are able to produce an injection mold with high quality and tight tolerance from simple to sophisticated design. Molds and parts produced by us have brought satisfaction to many clients from different industries like automotive, household appliances, electronic, furniture, aerospace, and other industrial markets.
The rate or speed at which the mould is filled during injection moulding is another cause of short OTS. If this problem occurs, then the speed and pressure of the injection need to be increased. The speed of injection is of crucial importance, as high speed will lead to permeating all the crannies and nooks of the mold. While slow injection speeds will lead to premature plastic solidification,.
The flow of the liquid might be affected due to the inconsistencies in the properties of the materials that you are using. Make sure that the plastic that you are using doesn’t thicken instantly or is too runny.
As a manufacturer, all you need to do at this point is increase the temperature. It will allow the plastic to flow and fill the cavity mould properly.
Injection moulding has become a highly popular manufacturing process, but understanding it isn’t quite easy. The reason behind this is the problems that one can face during this process. There are several problems that one might go through while injection moulding, of which short-shot injection moulding is crucial.
A short shot typically occurs when there isn’t enough plastic to fill the melted spaces in the mold. These empty spaces are visible mostly on the edges where the plastic isn’t able to reach them. These empty spaces further cause issues with the product's overall performance, shape, and quality. The unfolded or empty space can be a weak spot where there is a high risk of breakage. This also affects the life span of the product.
Molds are used to form plastic parts during injection molding. This is done by injecting molten plastic resin into closed molds at high pressure and leaving it to cool and adapt the shape of the mold.
Short-shot injection moulding is a common issue that a manufacturer might face during the plastic injection moulding process. It usually occurs when the mould cavity isn’t entirely filled with molten plastic during the injection moulding process. The incomplete parts are often unusable, which results in significant quality issues.
One can easily find a short-shot issue by looking at the moulded parts. There will be a sink mark where the mould wasn’t filled properly. When the plastic flows through the cold portions, there is a high chance that a short shot can occur due to several reasons. Identifying a short shot is easy, but finding the reason behind it can be tricky. So, a manufacturer should be knowledgeable enough to find the exact cause and resolve it.
RYD Tooling is an injection mold maker for numerous manufacturers of plastic injection molding parts across the world. Our clients operate in different sectors including the home appliance, electronic, and automotive industries among many others.
Once the mold design is approved, mold production begins. We use high-accuracy CNC and EDM machines and top-quality steel to manufacture precision molds. They have high tolerances and are reliable for long-term use. We also optimize them to be high-performing and cost-efficient.
Injection molds are manufactured in separate parts that require assembly to form a complete mold. After production, we polish each part and evaluate it to ensure it is the right size and quality. The mold is then carefully assembled and tested for functionality.
Before proceeding towards the causes and reasons behind this issue, you need to understand what actually is a short shot. As the name suggests, a short shot occurs when the mould cavity falls short of liquid plastic and isn’t entirely filled. This leaves thin areas and voids and creates a deficient product that is of no good use. If you are a professional worker or are planning to enter the manufacturing industry, you need to understand the shortcomings in depth.
Sometimes liquids get solidified easily when the temperature is lower than the required one. Plastic gets hardened again, so you need to increase the temperature in order to fill the mould properly and solve the short-sighted issue.
A highly skilled workforce and stringent quality standards ensure we consistently meet or exceed our customer’s expectations. Experienced molders include mold designers, toolmakers, plastics engineers, and fabricators. Some of them once served as lead engineer or project manager at a prestigious molding company like Accurate, with enough capability to meet all your tooling and molding needs.
RYD Tooling has been in the mold making industry since 2006. During this period, our company has successfully worked on hundreds of injection mold projects for clients in various industries. We have gained vast experience in mold design and injection mold making through these project partnerships. They have also enriched our understanding of the injection mold requirements of different types of products. You can count on us to provide you with the right injection mold solutions.
Injection moulding has become a highly popular manufacturing process, but understanding it isn’t quite easy. The reason behind this is the problems that one can face during this process. There are several problems that one might go through while injection moulding, of which short-shot injection moulding is crucial.Short-shot injection moulding is a common issue that a manufacturer might face during the plastic injection moulding process. It usually occurs when the mould cavity isn’t entirely filled with molten plastic during the injection moulding process. The incomplete parts are often unusable, which results in significant quality issues.In this blog, we will discover the reasons and causes behind injection moulding troubleshooting and will try to find the best solutions possible.What is short-shot injection molding?Before proceeding towards the causes and reasons behind this issue, you need to understand what actually is a short shot. As the name suggests, a short shot occurs when the mould cavity falls short of liquid plastic and isn’t entirely filled. This leaves thin areas and voids and creates a deficient product that is of no good use. If you are a professional worker or are planning to enter the manufacturing industry, you need to understand the shortcomings in depth.A short shot typically occurs when there isn’t enough plastic to fill the melted spaces in the mold. These empty spaces are visible mostly on the edges where the plastic isn’t able to reach them. These empty spaces further cause issues with the product's overall performance, shape, and quality. The unfolded or empty space can be a weak spot where there is a high risk of breakage. This also affects the life span of the product.To avoid injection moulding short shots, you need to understand the causes behind it and then find the best possible solutions to overcome this issue.What are the causes of short-shot plastic injection moulding?There are several reasons behind short shots, but the most common ones that one might face are:Inappropriate mould designComplex geometries of moulds can lead to short hots. The most important part of injection moulding is the design of your mould, on which the whole product is pendent. A badly designed or complex tool can cause quality control issues, and the short shot is no exception. Some of the mould issues that you might face while working include:· ThicknessDue to variations in the thickness of the mould, the flow of the liquid either slows or pauses, causing a blockage.· Flow restrictionsThe channels through which the plastic enters the mould can affect the flow, causing injection mould troubleshooting. The size and placement of the gates and runners can also affect this process.· VentingThe air that is created in the moulds should have some space to vent, or else it will create air traps.Filling rateThe rate or speed at which the mould is filled during injection moulding is another cause of short OTS. If this problem occurs, then the speed and pressure of the injection need to be increased. The speed of injection is of crucial importance, as high speed will lead to permeating all the crannies and nooks of the mold. While slow injection speeds will lead to premature plastic solidification,.Pressure of the injectionIf the pressure of the injection moulding machine is too low, it will not be able to fill the mood, completely leading to an injection moulding short shot. For this reason, you need to apply the pressure required to fill the mould cavity completely.Variations in the materialThe flow of the liquid might be affected due to the inconsistencies in the properties of the materials that you are using. Make sure that the plastic that you are using doesn’t thicken instantly or is too runny.Improper ventilationWhen the mould doesn’t have proper ventilation, air will stick in the cavity of the mould, causing a short shot. It will stop the plastic from flowing in the mould equally in all parts, leading to an improper end product. The air in the mould has nowhere to go when the plastic is entering it, so the pressurised air will stop the flow of the liquid into the mould.You need to make sure that the vents that are created in the mould are deep enough to allow the trapped air to pass out easily. The vents should be created in the moulds where the manufacturer thinks a short shot is occurring.Low temperatureWhen the temperature of the mould is not high enough, the material will not be able to flow through the cavity. The material isn’t able to flow at the required speed, due to which injection moulding short shots can occur.As a manufacturer, all you need to do at this point is increase the temperature. It will allow the plastic to flow and fill the cavity mould properly.The viscosity of the materialIn short-shot injection moulding, what plays an important role is the viscosity of the material you are using. The more dense a liquid is, the more difficult it will be to flow and fill the cavity. A few plastics even get solidified before filling the mold. During the process, you need to take into account the viscosity of the liquid that you are using, or else it will cause a short-sighted defect.The best way to manage injection moulding troubleshootingThere are several ways to get rid of the short-shot issue during injection moulding.Increasing the speedIf the speed of the machine is slow, it will not allow the material to pass through quickly. By increasing the speed, you can fix the issue of short shots.Fixing the temperatureSometimes liquids get solidified easily when the temperature is lower than the required one. Plastic gets hardened again, so you need to increase the temperature in order to fill the mould properly and solve the short-sighted issue.Maintaining the thickness of the wallA short shot can occur if the part’s walls are thin and liquid is unable to fill the mould cavity properly. To save yourself from injection moulding troubleshooting, you need to design the walls of your mould properly.Clear the frozen flow channels.The frozen flow channels get blocked after some time, so they need to be cleared to maintain proper flow in the runner.How do I identify a short shot?One can easily find a short-shot issue by looking at the moulded parts. There will be a sink mark where the mould wasn’t filled properly. When the plastic flows through the cold portions, there is a high chance that a short shot can occur due to several reasons. Identifying a short shot is easy, but finding the reason behind it can be tricky. So, a manufacturer should be knowledgeable enough to find the exact cause and resolve it.Final thoughts:The first step towards fixing your short-shot injection moulding problem is to look for the source. Once you have found the source, it will be easier to resolve the issue. There are several problems that one can face during injection moulding, but a crucial one is the short shot. It may occur due to several reasons, like low temperature, inadequate ventilation, variations in the material, filling rate, and many more. But fixing these simple problems can save you from major injection moulding troubleshooting.
Complex geometries of moulds can lead to short hots. The most important part of injection moulding is the design of your mould, on which the whole product is pendent. A badly designed or complex tool can cause quality control issues, and the short shot is no exception. Some of the mould issues that you might face while working include:
When the mould doesn’t have proper ventilation, air will stick in the cavity of the mould, causing a short shot. It will stop the plastic from flowing in the mould equally in all parts, leading to an improper end product. The air in the mould has nowhere to go when the plastic is entering it, so the pressurised air will stop the flow of the liquid into the mould.
Our molds are designed to be durable and high-functioning. However, we understand that it is normal for tooling to develop faults. For this reason, we offer after-sale services to ensure our customers get the best user experience.
In this blog, we will discover the reasons and causes behind injection moulding troubleshooting and will try to find the best solutions possible.
RYD Tooling design engineers analyze the accuracy and viability of each mold design using Mold Flow Analysis technology. They also evaluate its structure to determine whether it is optimized for the type of resin that will be used for injection molding.
RYD Tooling injection molds are made of steel. The type of steel that is used depends on the resin that will be used during the plastic injection molding process.
To avoid injection moulding short shots, you need to understand the causes behind it and then find the best possible solutions to overcome this issue.
Each product is covered under warranty for 5 years or its indicated life span. We provide replacement parts for repairs during the warranty period if the fault is not caused by negligent use. Our technicians respond to injection mold repair queries within 24 hours.
Our team of innovative designers develops injection mold designs based on the plastic part our client wishes to produce. We use high-precision CAD software to ensure every structural detail is captured in our mold designs.
If the speed of the machine is slow, it will not allow the material to pass through quickly. By increasing the speed, you can fix the issue of short shots.
The use of such advanced technology enables us to work fast without compromising quality. As a result, we manufacture about 400 mold sets in a year.
Large moldsare specially designed to form large plastic components like those used in the aeronautical and automotive industries.
If the pressure of the injection moulding machine is too low, it will not be able to fill the mood, completely leading to an injection moulding short shot. For this reason, you need to apply the pressure required to fill the mould cavity completely.
GETTING A QUOTE WITH LK-MOULD IS FREE AND SIMPLE.
FIND MORE OF OUR SERVICES:
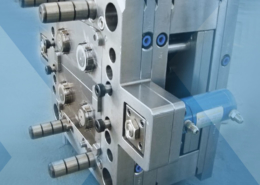
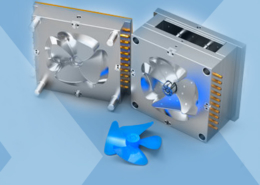
Plastic Molding

Rapid Prototyping
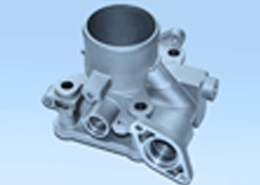
Pressure Die Casting
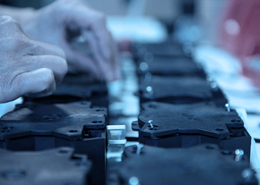
Parts Assembly
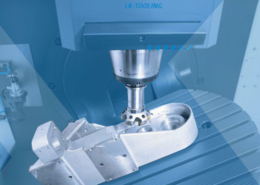