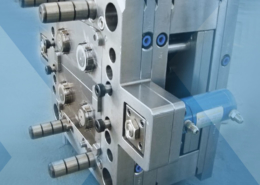
APSX - Innovative Manufacturing Solutions - apsx injection molding
Author:gly Date: 2024-10-15
Do you need design-for-manufacturing (DFM) assistance? Or, are you ready for production? We have a full suite of services to offer and a lifetime mold guarantee.
Two-shot injection molding is also called “2k molding” or co-injection molding. To successfully perform liquid silicone rubber two-shot molding, a specially designed co-injection molding machine is needed, and a mold builder and molder that are skilled and experienced in LSR processing to ensure accurate alignment and precision placement.
If you spend $20,000 on a steel mold and then use that mold to create 400,000 parts, the cost per part would end up at 5 cents. There’s more to it than that, however, as the labor and material used will also have an impact on the total investment.
An injection mold generally costs between $1,000 and $80,000. A number of factors, including size and complexity, impact the final price. At Rex Plastic, the average price for an injection mold is $12,000. To read more about the cost of injection molding, check out our blog.
Materials with the lowest cost, generally polypropylene and polyethylene, are incredibly versatile and are used to make everything from milk jugs to car batteries. These are the materials most people use every day and low material costs help make mass production possible.
I am looking to mold a cat sculpture for our local Humane Society. I have the model, formerly done in a 6 piece mold using fiberglass. I need about 50 cats, they stand 22″ floor to top of head, 30″ to top of tail, 6″ wide sideways and 16″ chest to rear. I also could use many more if the ideas goes to other HS.locations. The fiberglass ones were pure white, solid, but now I am thinking of technocats, clear plastic or solid white, hollow so that artists can utilize some tech including audio.
When thinking about what material to use for your plastic injection project, it’s important to remember that the function of the product should determine the material used. Having an understanding of the options available and the prices associated with those materials will help you to make an informed decision.
In the case of connectors, covers, valves, and others components that use a seal, when produced as a multi-material component the product’s performance is enhanced. A superior chemical bond is achieved, the seal fits perfectly, remains in-place and eliminates seal rollover or displacement that can occur with loose seals added during a secondary assembly process.
These three materials are used so often because they are affordable and durable. The material used to create a product should be determined by the product itself, and what it will be used for. To read more about different injection molding materials and their features, check out our materials blog here.
Our advanced molds and molding capabilities enable us to fulfill even the most complex design requirements — without sacrificing quality, durability or aesthetic appeal. What’s more, we support our multi-shot injection process with a full complement of value-added services for our customers, such as design support and prototyping on the front end, and value-added inline secondary processes at the end for a full portfolio of services.
Hey I was looking for useful information on Plastic Surgery and just came across your blog and found it quite interesting, can’t wait to see your post. You’ve been sharing really insightful posts and I’m an avid reader of your posts. Keep sharing the knowledge and adding value to our lives.
SIMTEC has perfected their multi-shot LSR injection molding technology and is one of few with the expertise and quality results needed for complicated, critical component requirements. We are proud to be able to provide our customers with solutions that meet the product performance they need for their long-term, high volume programs, and deliver quality precision multi-material components, consistently.
Regardless of the industry, our liquid injection molding cells allow for the production of liquid silicone rubber parts or components that must withstand extreme conditions and make your products more effective. Industries and applications include:
In 2k LSR injection molding, there are two types of molds used: transfer molds and rotary molds. Using a transfer molding process, after the thermoplastic parts are molded, the molded parts are robotically removed from the mold and transferred up to the LSR mold for completion.
Contact us today to learn more about the many ways in which multi-injection molding can add value to your company’s manufacturing processes and applications.
These materials are generally stronger or have special properties that make them suitable for specialized functions. Additives and other components can make these plastics even more durable but do add to the price.
In two shot molding, the LSR and thermoplastic parts are both molded and combined during the same molding cycle. The molds for the LSR and thermoplastic parts share the same platen in the molding machine. Typically the mold for the LSR parts is on the top and the thermoplastics mold is on the bottom.
For product designers, the use of multiple materials in a single component allows for greater design flexibility to achieve complex part designs, desirable product features, and enhanced product performance.
When utilizing more than one material, the desirable characteristics from each of the materials can be realized – the rigidity of a thermoplastic or weight of a metal mass combined with the flexibility, sealing, or delicate features of an LSR.
Two-shot LSR injection molding involves molding an LSR material and a second polymer in the same molding process. The second material can be either a compatible thermoplastic material or a different grade of LSR (different durometer or pigment). The two materials are molded during the same process and combined to form one integrated two-material component. This process is a two-shot injection molding process.
There are several benefits that can be achieved by choosing a multi-shot process versus a single-material part followed by assembly, heat staking, ultrasonic welding or other secondary process used to mechanically combine two or more substrates.
The overmolding injection molding process is sometimes confused with or referred to as two-shot molding. Although similar because the finished component of both consist of a combination of two different materials or substrates, the manufacturing process and bonding is different. In the 2k molding process, the two materials are both chemically and physically integrated providing a superior bond compared to overmolding.
With design flexibility, advanced technology and exceptional quality, there’s no better partner to manufacture your high volume Liquid Silicone components than SIMTEC. Contact us today to discuss your requirements.
In the overmolding process, a finished molded component or a metal or other substrate is placed within the LSR mold during the LSR molding process. Once introduced, the mold closes and the LSR is molded around or over the presented substrate or component, integrating the two.
SIMTEC is proud to be a leader in the development of multi-injection molding technology. We’ve created and implemented technological approach to the integration of functions and materials, resulting in a proprietary multi-shot molding process that is unmatched in our industry.
Multi-shot or multi-component injection molding is a collective term that refers to an injection molding process where two or more materials are molded in the same molding machine and within the same molding process. The result, an integrated molded component consisting of multiple materials and substrates.
GETTING A QUOTE WITH LK-MOULD IS FREE AND SIMPLE.
FIND MORE OF OUR SERVICES:
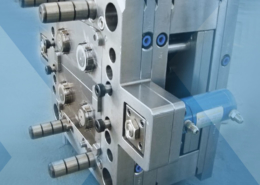
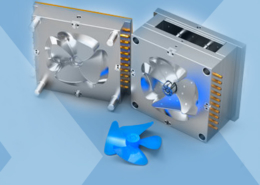
Plastic Molding

Rapid Prototyping
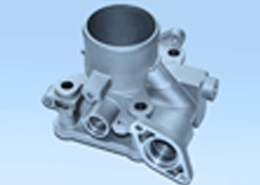
Pressure Die Casting
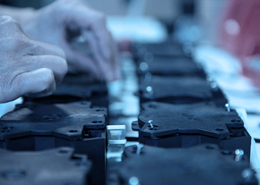
Parts Assembly
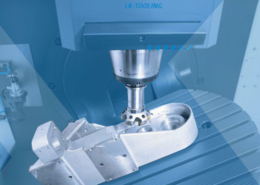