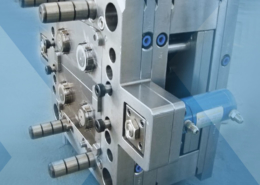
Applications of Engineering Plastic POM Injection Molded ... - pom injection mol
Author:gly Date: 2024-10-15
The manufacturing and processing techniques employed for Ultrahigh Molecular Weight Polyethylene (UHMWPE) play a crucial role in shaping its properties and determining its suitability for various applications. Let's delve into the different stages of UHMWPE production and the key processing methods utilized.
Injection molding is a highly versatile and efficient method for processing UHMWPE. In this process, the molten UHMWPE is injected into a mold cavity under high pressure. It allows for the production of complex shapes, intricate details, and large quantities of UHMWPE parts with excellent dimensional accuracy.Compression molding, as mentioned earlier, is also employed for UHMWPE processing. In compression molding, the molten UHMWPE is placed into a heated mold and compressed under pressure until it solidifies. This method is suitable for manufacturing larger components or parts that require specific configurations.These processing techniques allow UHMWPE to be molded into various forms, including sheets, rods, tubes, profiles, and intricate components. The choice of processing method depends on the desired shape, size, and mechanical properties required for the specific application.In the subsequent sections, we will explore the specific applications of UHMWPE in industries such as medical and healthcare, automotive and transportation, sports and recreation, industrial and chemical processing, as well as the food and beverage industry. Stay tuned to discover the diverse applications of this exceptional engineering plastic.
UHMWPE plays a vital role in the automotive and transportation sector. Its lightweight nature, high impact strength, and excellent chemical resistance make it an ideal material for various applications. It is used in components like gears, bearings, bushings, and liners, contributing to reduced weight, improved fuel efficiency, and enhanced performance. Additionally, UHMWPE's low friction coefficient and wear resistance make it suitable for applications like wear strips, slider pads, and truck bed liners.
The thermoplastic injection molding industry has evolved over the years: initially focused on the production of combs and buttons, it has evolved to the production of a wide range of products for many industries including automotive, medical, aerospace, consumer products, toys, plumbing, packaging, and construction.
Thermoplastic injection, or injection molding, use the thermoplastic properties of certain materials to inject a softened plastic into a mold to create an impression from it. This technique provides the best quality for your productions of large and very large series.
The first step in UHMWPE manufacturing is the polymerization process. UHMWPE is typically produced through a process called Ziegler-Natta polymerization. During this process, ethylene monomers are polymerized using a catalyst system, resulting in the formation of long polymer chains with an ultrahigh molecular weight.The control of molecular weight distribution is essential to ensure the desired properties of UHMWPE. Through precise control of reaction conditions and catalyst selection, manufacturers can achieve the desired molecular weight distribution, which contributes to UHMWPE's exceptional mechanical properties.
UHMWPE is widely employed in industrial and chemical processing applications. Its excellent chemical resistance and low friction properties make it ideal for lining pipes, tanks, and chutes in chemical plants and processing facilities. UHMWPE's ability to withstand corrosive substances, high temperatures, and abrasive materials ensures longevity and reliability in harsh industrial environments. It is also used as a material for conveyor components, seals, gaskets, and wear-resistant parts.
The advantage of this method is that it allows the duplication of many identical objects of high quality, thanks to the re-use of the mold, and in the right material. This is why this method is particularly suited to large or very large series production. A final advantage is that the parts thus designed require little or no subsequent machining.
The principle of plastic injection is the use of heat to soften a thermoplastic (TP) material in the form of pellets. The softened material is kneaded and injected into an endless screw. The rotation of the screw and the pressure added inserts the material into a mold. The material then takes on the impression of the mold. After cooling, the object takes on solid form and can be removed from the mold. The mold can then be reused for another injection.
In the medical and healthcare industry, UHMWPE has revolutionized orthopedic implants. It is commonly used in joint replacements, such as hip and knee implants. UHMWPE's biocompatibility, low wear rate, and ability to withstand the demanding forces and friction within the human body make it an ideal material for long-lasting and reliable orthopedic devices. It offers patients improved mobility, reduced pain, and enhanced durability.
However, this method has a cost because it requires the design of a steel mold, which allows the duplication of many series parts. This is why it is not recommended for designs for small series. For this, silicone molding is preferred, for example. (See our section on silicone molding.)
Pars Ethylene kish does not have any representative in iran ,The Company`s products are sold only through the central office :: Copyright © 2007- 2018 Pars Ethylene Kish Co. :: All rights reserved :: Design & Development by: Pars Ethylene Kish ::
Ultrahigh Molecular Weight Polyethylene (UHMWPE) finds extensive use in various industries due to its exceptional properties and versatile nature. Let's explore some of the key applications of UHMWPE across different sectors.
..:: Parsethylene kish co. does not have any representative in iran ,The Company`s products are sold only through the central office with an official Certificate ::..
In 1919, Arthur Eichengrün developed the first injection molding press, which can be considered the first modern injection molding machine. A few years later, in 1926, Eckert and Ziegler patented the first injection molding machine with commercial characteristics. The 1930s saw the emergence of the first injection molding machines in France. This marked the start of plastic household items and toys on the consumer market.
Pars Ethylene kish does not have any representative in iran ,The Company`s products are sold only through the central office :: Copyright © 2007- 2018 Pars Ethylene Kish Co. :: All rights reserved :: Design & Development by: Pars Ethylene Kish ::
..:: Parsethylene kish co. does not have any representative in iran ,The Company`s products are sold only through the central office with an official Certificate ::..
The industry developed rapidly in the 1940s, following huge demand for inexpensive, mass-produced products. In 1946, the American inventor James Watson Hendry built the first machine with injection screws, allowing much more precise control of the injection speed and the quality of the products produced. This machine made it possible to add colored or recycled plastic to the virgin material prior to injection. Today, machines with injection screws represent the vast majority of all injection machines.
In the food and beverage industry, UHMWPE plays a crucial role in ensuring safety, efficiency, and hygiene. It is widely used for food processing equipment, conveyor belts, cutting boards, and packaging machinery. UHMWPE's low moisture absorption, excellent chemical resistance, and ease of cleaning make it suitable for maintaining strict sanitary standards. Its non-toxic nature and resistance to bacterial growth further enhance its suitability for food contact applications.These are just a few examples of the extensive applications of UHMWPE. Its unique combination of properties makes it a versatile and sought-after material in numerous industries, ranging from medical and automotive to sports, industrial, and food processing. As technology advances, UHMWPE continues to explore new frontiers, expanding its reach and unlocking innovative applications.In the upcoming sections, we will discuss the comparison of UHMWPE with other engineering plastics, maintenance and care of UHMWPE products, and future trends and developments in the field. Stay tuned to stay updated on the latest advancements and insights related to UHMWPE.
The sports and recreation industry benefits greatly from the unique properties of UHMWPE. It is used in the manufacturing of ski and snowboard bases, providing excellent gliding properties, durability, and resistance to abrasion. UHMWPE is also utilized in protective gear, such as helmets and padding, due to its impact resistance and toughness. Additionally, its low friction coefficient makes it suitable for applications like playground equipment, ice rink boards, and synthetic ice surfaces.
Melt processing techniques are commonly used to shape and mold UHMWPE into desired forms. These techniques involve heating the UHMWPE resin to a molten state and then utilizing different methods to give it the desired shape.
The American inventor John Wesley Hyatt patented the first injection molding machine in 1872. This machine was relatively simple compared to the machines in use today: it worked like a large hypodermic needle, using a plunger to inject plastic into a mold through a heated cylinder. At the time, they produced principally necklaces, buttons, and combs.
Ram extrusion is a popular method for processing UHMWPE. In this technique, the molten UHMWPE is forced through a die using a ram or piston. Ram extrusion allows for the production of continuous profiles, such as rods, tubes, and sheets, with precise dimensions and excellent surface finish.Compression molding is another commonly used technique for UHMWPE. In this process, the molten UHMWPE is placed into a mold cavity, and pressure is applied to shape it into the desired form. Compression molding is suitable for producing intricate parts and components with varying thicknesses.
GETTING A QUOTE WITH LK-MOULD IS FREE AND SIMPLE.
FIND MORE OF OUR SERVICES:
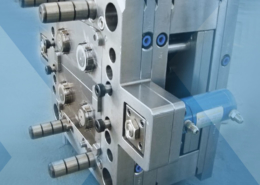
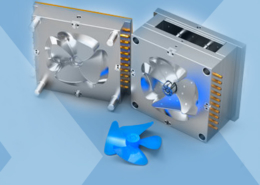
Plastic Molding

Rapid Prototyping
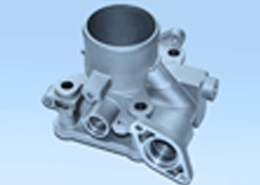
Pressure Die Casting
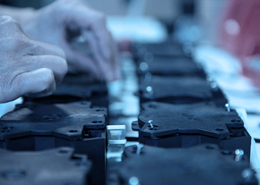
Parts Assembly
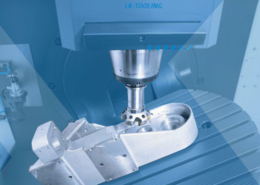