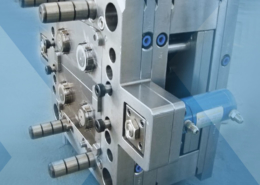
Apex Resource Technologies - apex injection molding
Author:gly Date: 2024-10-15
OGM first started supplying medical device companies in the UK over 20 years ago. Our first cleanroom was built in 2000 and today we are one of the leading plastic injection moulders for medical devices and components.
Consistent quality parts start with a quality, well-made and maintained mold. What expectations should you have for the care of your investment?
When determining press size for your plastic part, it’s important to calculate the total projected shut-off area. This area consists of only the space that is 90 degrees to the direction of the injection molding machine platens. Thickness does not have any implication on the clamp tonnage and the general rule is to have 2 to 5 ton of clamp tonnage per square inch of projected area.
Design is one of the most important factors in avoiding part defects. Avoid mistakes that can be costly both in regard to time and budget later on.
Are you a product designer or engineer that is looking for more information on how to make your plastic part design more efficient in regard to cost and production time? One important consideration during the part design process is to have a good understanding of plastic injection press basics including the size of machine needed for your part.
Our team is committed to delivering the best plastic injection moulding service with dedicated project management from concept to finished product.
Our tool designers can help you with everything you need to produce a successful injection mould design including the best choice of medical grade materials.
To learn more about our plastic injection moulding services please call us on +44 (0)1865 844300 or you can email us at info@ogmmedical.com
We guarantee complete quality control with full product inspection, testing and validation services accredited to medical standard ISO 13485, manufacturing standard ISO 9001 and environmental standard ISO 14001.
With ISO 13485 medical standard manufacturing and our new ISO 7 clean room (Class 10,000 clean room) for medical devices, we can help you design and develop high quality injection moulded products as cost effectively as possible. We can also reduce injection mould tool modification or repair times from weeks to just days and shorten the overall product development lead time.
Your plastic injection molder should help you determine the size of the machine needed to help you achieve the best result for your product. Knowing an approximate size of what will be needed can help you determine the best injection molding partner based on the press capacity they have available. For example, larger presses cannot accommodate smaller molds because they can’t close far enough and the injection process will not work.
Our experienced team will work closely with the design team to transform your mould tool design into the highest quality injection mould tooling.
Pressure plays a significant role in the overall quality of a plastic part. Pressure keeps the mold closed during the injection process. Too much or too little pressure can cause various issues such as flashing and viscosity. One important consideration in regard to pressure is that plastic compounds react differently from one another based on their Melt Flow Index (MFI). MFI measures the ease of flow of a thermoplastic polymer and the higher the MFI, the higher pressure needed to create a successful part.
Calculating shot volume to make sure your barrel has enough capacity can be accomplished by working with your injection molder to run a mold flow analysis. On some engineered materials, the increased residence of the material in the barrel can cause the material to degrade, resulting in poor part quality. Mold flow analysis will help you determine the volume of your part and runner while determining any factors that would cause safety issues.
The most successful parts are created when there is constant communication between a part designer, tool designer and manufacturer.
Designing a plastic part for manufacturability from the outset involves several considerations that can have a significant impact on key variables
As a UK based manufacturer, we can offer help with reshoring to reduce lead-times and production delays of medical devices and components.
OGM Medical is a UK based plastic injection moulding company supplying medical equipment manufacturers globally. We manufacture components and devices for a wide range of customers in the medical, pharmaceutical and life science sectors.
“Bigger the better” is not always the case when determining the press size needed. In the molding process, plastic is injected into the mold at an exceptionally high-pressure rate, which creates a natural pull to force the mold open. A press is designed to keep the mold shut with larger parts requiring more tonnage and force, and smaller parts requiring less. A general calculation for determining press size needed is as follows:
“Safety factor” is an additional percentage added to your calculation as a buffer to help reduce defects in your part. Most injection molders will recommend 2.5 times the surface square inches of the part and an additional 10% as a safety factor. If you have a part that is 120 square inches, you would need a press size with 300 tons of pressure. When you add the 10% safety factor, the required press size would have 330 tons of clamping force.
We will prepare a bespoke master validation plan and validation protocol for you including a full production part approval process (PPAP).
We specialise in high-volume production of plastic parts using precision-controlled robotics. We invest heavily in the latest technology from 3D metal additive manufacturing to high-definition vision systems for inspection and quality control.
Additionally, smaller presses have tie bar spacing too narrow to accommodate larger products. If the mold doesn’t fit between them horizontally or vertically, you must move up in press size. Many injection molders offer press sizes ranging from 68 tons up to 400 tons.
In order to streamline your process, consider these questions before requesting an accurate quote for your part design, development and production.
Regular injection mold maintenance can help your mold last longer, run with less interruptions & will ultimately save you time, money & frustration.
Having a general understanding of how to calculate press size is a good first step in determining what injection molding partners are available to you. Strong partners will make recommendations on how to appropriately tweak your part to ensure the final design fits your manufacturing needs and reduces upfront tooling costs. Nicolet Plastics has press sizes up to 610 tons.
We can support you through the entire process of bringing your product to market or upgrading and modifying existing products. All manufacturing, assembly, testing and validation is carried out at one of our UK sites in Oxford or South Wales.
GETTING A QUOTE WITH LK-MOULD IS FREE AND SIMPLE.
FIND MORE OF OUR SERVICES:
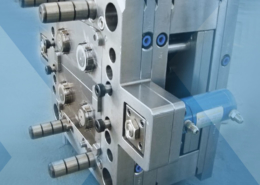
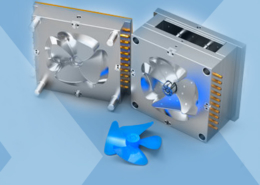
Plastic Molding

Rapid Prototyping
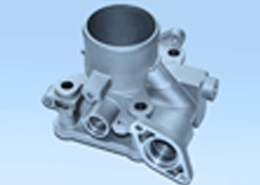
Pressure Die Casting
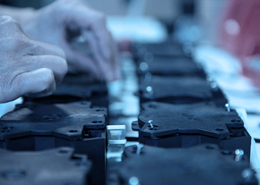
Parts Assembly
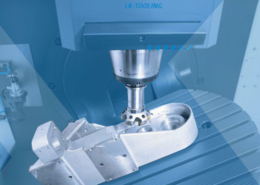