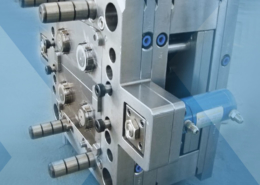
apa itu injection molding? - Industri pengetahuan - apa itu injection molding
Author:gly Date: 2024-10-15
Our structural foam injection molding equipment allows us to produce parts up to 7.5 feet in length with a typical wall thickness range of .200 to .500 inches. Our low-pressure structural foam machines have platen sizes of 98 inches x 89 inches and tie bar spacing of 58.5 inches x 67.5 inches. The shot size is up to 150 lbs. The structural foam process allows for running more than one mold at the same time in a single machine. We are happy to quote any new or existing structural foam projects.
We use the information you provide to us to contact you about our relevant updates. You may unsubscribe to receive these communication at any time. Read more about our Privacy Notice.
In one instance, a customer in the construction industry came to us to redesign their existing structural foam molding process. They were using a straight injection molding process to manufacture a line of linear trench drains for use in industrial, commercial, and residential applications. However, the single-cavity molds utilized in the existing process resulted in long cycle times and produced parts with warping and low dimensional tolerances.
Our team redesigned the manufacturing process to use the low-pressure structural foam molding method, which resulted in a 20% part weight reduction and a 40% cycle time reduction over the original process. The new process allowed for the creation of trenches in 17 different sizes. We built the aluminum molds and designed tools with interchangeable molds to allow the customer to run any two of the 17 sizes in a single machine at the same time.
Easily processed, KyronMAX® can be molded using the same equipment and tooling as standard for unfilled resins, while compounds can be customized to meet application requirements. Crucially, where traditional materials struggle, KyronMAX® injection moldable materials retain high strength in complex part geometries, making them stronger, lighter and longer lasting (tougher) than other thermoplastic composite and metal parts.
MCG Advanced Materials Engineered Solutions is vertically integrated across the globe and combines the experience, design engineering, material science and technology you need to help change the world. By integrating many technologies within one facility, we can simplify your supply chain, improve your process flow, and create more cost-effective solutions.
Using digital twins to test new ideas and a focus on small batch prototyping means our entire production process is further designed to minimize waste and maximize speed to market.
Founded in 1953 in Erie, PA, Port Erie Plastics began operations with a single injection molding machine in a small building. Since then, our company has grown significantly to accommodate increasing customer demand. Today, Port Erie Plastics is a leading provider of injection molding services, but, occasionally, another means of processing plastic is a better way to make a part. In recent years, our engineering talent has enabled us to add structural foam molding and extrusion to meet our customers’ needs.
Structural foam molding is an injection molding process that involves injecting liquid resin with an inert gas or a chemical blowing agent. The mixture is then injected into the mold cavity, where the gas or blowing agent expands and forces the resin to fill all areas of the cavity. As the material comes into contact with the walls of the mold, the surface cells collapse, resulting in a smooth and solid surface on the outside of the molded component.
"At AddiFab, we try to be pretty impartial when it comes to materials. The reason we keep coming back to KyronMAX® is that we never fail to achieve a good result. It's easy to forget that these materials are reinforced – they flow like un-filled materials.
Compared to other manufacturing methods, the structural foam injection molding process offers a number of advantages, such as:
Crosslink testing Oxidative induction time testing Hot and cold burst testing Hot and cold impact testing 100% in-line ultrasonic dimensional inspection CMM Laser mics
The world’s strongest injection moldable product line of structural thermoplastic materials using advanced carbon fiber technology adds new formulas reaching 60,000 psi tensile strength.
Our SPRINT (Soluble PRinted INjection Tooling) technology means we can develop functional prototypes in just a few days. SPRINT allows for rapid injection molding of functional parts in the right material. Alongside digital twinning, it means we can test real world designs quickly and accurately, shortening design timelines and meeting production deadlines faster.
If you need a partner for your structural foam molding and extrusion project, turn to the experts at Port Erie Plastics. To learn more about our capabilities, check out our case studies or contact us today. To discuss your project requirements with one of our team members, request a quote.
With Freeform Injection Molding, we've been able to provide our customers with unseen levels of speed, and design freedom. From automotive to prosthesis, KyronMAX® has consistently been our #1 pick where we've been asked to deliver high strength and low weight. And through our collaboration with Mitsubishi Chemical Group, we have been able to boost global availability and accessibility. As our users are global brands, they appreciate the flexibility that comes from having access to a world-class Freeform-as-a-service provider."
Find out more about our full range of capabilities and how we could be the right partner to help you design the right parts for the right job.
From make to remake, our KyronMAX® injection moldable materials can be returned to create zero waste using our end-of-life recycling program.
KyronMAX® is a range of new breakthrough high strength thermoplastic composite compounds, specifically designed for rapid, complex high-spec injection molding.
Equipped with over 60 years of injection molding experience, we have the knowledge and skills to create structural foam components for virtually any customer need. This expertise also allows us to help customers optimize existing structural foam molding processes to achieve better product and production quality.
GETTING A QUOTE WITH LK-MOULD IS FREE AND SIMPLE.
FIND MORE OF OUR SERVICES:
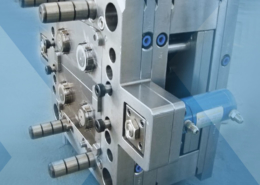
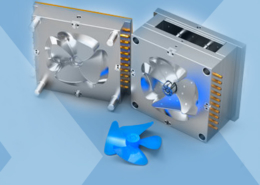
Plastic Molding

Rapid Prototyping
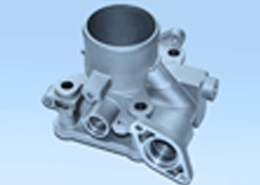
Pressure Die Casting
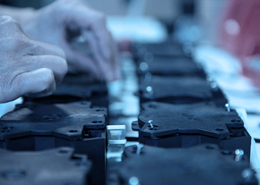
Parts Assembly
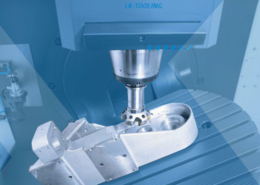