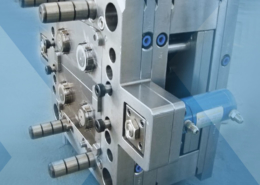
Anyone experienced molding acrylics? : r/InjectionMolding - acrylic injection mo
Author:gly Date: 2024-10-15
We use cookies on this site to enhance your user experience. You can learn more about our use of cookies and your choices here. By interacting with this page, you are giving your consent for us to set cookies. Dismiss
Our experience producing plastics for the healthcare market includes medical device components, laboratory consumables, medical disposables, pharmaceutical packaging, and delivery devices. Our expertise means you can produce and deliver the highest level of quality and compliance to your customers, every time.
As the leading medical device manufacturer for volume production, we have helped top multinational medical and pharmaceutical companies go to market.
Measure and correct dimensional issues during manufacturing of electrode making, grinding, and milling with our Self-Correcting Manufacturing (SCM) technology.
We recognize that advanced plastics play a key role in the future of product development. From consumer products to critical healthcare devices, plastics can set your product apart. Flex supports our customers through product design, tooling, assembly, packaging, and logistics, delivering reliable production outcomes through consistent quality control processes at every production stage.
Your end result? Cost-effective, high-volume production of finished goods. And more importantly, you can minimize — or even eliminate — the potential for introducing human contaminants into your medical-grade products.
Through a combination of evaluating your products prior to investing in production molds and taking advantage of short-run production opportunities, you can get to market faster with a proven design.
We uphold rigorous quality control and testing procedures to guarantee that every mold meets the highest standards and use simulation software for the part and old design to optimize and prevent problems before the mold is build. We also use Finite Element Analysis (FEA) for products and assemblies to assess structural, acoustic, electromagnetic, and thermal performance.
We leverage our extensive experience and cutting-edge technology to deliver customized tooling design and fabrication solutions that meet the highest standards of quality, efficiency, and cost-effectiveness. Whether you require complex multi-material molds or high-volume production capabilities, we’ll make sure your components and products are highly manufacturable so you go to market with only proven designs.
Short-run production services also enable requirements for automation, assembly, and preliminary production needs including clinical trial volumes.
Make our ultra-high-precision injection molding expertise yours. You can depend on our experience manufacturing plastics in healthcare devices, such as drug delivery devices, patches, inhalers, auto-injectors, syringe barrels and plunger rods, plastic implantable devices, and laboratory consumables.
You can lower your Total Cost of Ownership (TCO) while improving customer satisfaction through faster, more reliable product delivery.
And along the way, your efforts support a sustainable future thanks to our partnerships with top certified suppliers using environmentally friendly practices.
Both homopolymer and copolymer PP offer excellent resistance to moisture and good chemical resistance to acids, alkalis, and solvents. However, it is not resistant to aromatic hydrocarbons such as benzene, and chlorinated hydrocarbons such as carbon tetrachloride. It is not as resistant to oxidation at high temperatures as PE.
Typically, fast injection speeds are used to minimize internal stresses; if surface defects occur, slow speed molding at a higher temperature is preferred. Machines capable of providing profiled speed is highly recommended.
Our single-source, standardized quality management system has subsystems for medical device production. Facilities that make medical devices are FDA registered and ISO 13485 certified with ISO Class 7 and 8 clean rooms.
PP is produced by the polymerization of propylene using stereospecific catalysts. Mainly, isotactic PP is produced (the methyl groups lie on one side of the carbon chain). This linear plastic is semicrystalline because of ordered molecular structure. It is stiffer than PE and has a higher melting point. The PP homopolymer becomes very brittle at temperatures higher than 0 C (32 F) and for this reason, many commercially available grades are random copolymers with 1 - 4% ethylene or block copolymers with higher ethylene content. Copolymers have a lower heat distortion temperature (approximately 100 C / 212 F), less clarity, gloss, and rigidity, but greater impact strength. The material becomes tougher as the ratio of ethylene increases. The Vicat softening point is approximately 150 C (302 F). Because of high levels of crystallinity, the surface hardness and scratch resistance is higher for these materials.
We can help you with sterile assembly automation sized for multi-year demand, as well as a modular approach to final assembly. So you can scale your output as demand changes.
In the case of cold runners, typical diameters range from 4 - 7 mm. Full round sprues and runners are recommended. All types of gates can be used. Typical pin gate diameters range from 1 - 1.5 mm, but diameters as low as 0.7 mm may be used. In case of edge gating, the minimum gate depth should be half the wall thickness and the width should be at least double the thickness. Hot runners can readily be used for molding PP.
Developmental tooling is critical to ensuring your components and products are highly manufacturable. Our dedicated engineering team partners with you every step of the way, starting with a working template for high-cavitation production molds.
PP does not have environmental stress cracking problems. PP is usually modified by addition of glass fibers, mineral fillers, or thermoplastic rubbers. The MFR of PP ranges from 1 to 40; lower MFR materials have better impact strength but lower tensile strength. The copolymer is tougher than the homopolymer of the same MFR. The viscosity is more shear and temperature sensitive than PE.
We deliver innovative, reliable, and scalable plastic molding solutions that enhance your products and brand, starting with materials selection and processing to help you select the right materials to meet application requirements, manufacturability, and environmental factors.
Our expertise in complex injection molding and mold fabrication for consumer goods and plastic packaging solutions enables us to deliver myriad capabilities: developmental tooling for high-tolerance and rapid pre-production tooling, ultra-high-precision, high-cavitation tooling, high-volume plastic injection molding, automation, assembly, and more.
As the leading medical device manufacturer for volume production, we produce highly specialized plastic components and medical devices with the quality and regulatory readiness you need. We have facilities dedicated to the production of medical devices that are ISO 13485:2016 certified, FDA 21 CFR Part 820 compliant, and equipped with ISO Class 7 and 8 clean rooms.
Due to crystallinity, the shrinkage is relatively high (order of 0.018 - 0.025 mm/mm or 1.8 - 2.5%). The shrinkage is more uniform than PE-HD (the difference in flow and cross-flow shrinkage is typically less than 0.2%). Addition of 30% glass reduces the shrinkage to approximately 0.7%.
Set a new pace for operations with less effort. High-speed clean room assembly and packaging, in-house automation design and engineering, vertically integrated manufacturing of the molding process, and high-speed tool room automation all create efficiencies not possible with manual assembly.
Flex specializes in expert plastic injection molding, allowing us to provide complex plastic components in high volume at a low cost. Whether you require intricate multi-material parts or streamlined consumer packaging solutions, our advanced capabilities and expertise are ready to support your project needs.
Our expertise in plastics custom mold manufacturing speeds production, cuts downtime, and streamlines the production of complex plastic components through our interchangeable core and cavity components.
Viewmold company provides injection molding services for your part with PP plastic material. PP injection molding processing condition Generic Class PP (Polypropylene) Typical Applications Automotive (mostly mineral-filled PP is used: dashboard components, ductwork, fans, and some under-hood components), appliances (doorliners for dishwashers, ductwork for dryers, wash racks and lids for clothes washers, refrigerator liners, etc.), consumer products (lawn/garden furniture, components of lawn mowers, sprinklers, etc.). Injection Molding Processing Conditions Drying Not normally necessary if proper storage is used Melt Temperature 220 - 280 C (428 - 536 F); not to exceed 280 C Mold Temperature 20 - 80 C (68 - 176 F); suggested: 50 C (122 F) The crystallinity level is determined by the mold temperature. Material Injection Pressure Up to 180 MPa Injection Speed Typically, fast injection speeds are used to minimize internal stresses; if surface defects occur, slow speed molding at a higher temperature is preferred. Machines capable of providing profiled speed is highly recommended. Runners and Gates In the case of cold runners, typical diameters range from 4 - 7 mm. Full round sprues and runners are recommended. All types of gates can be used. Typical pin gate diameters range from 1 - 1.5 mm, but diameters as low as 0.7 mm may be used. In case of edge gating, the minimum gate depth should be half the wall thickness and the width should be at least double the thickness. Hot runners can readily be used for molding PP. If you need high quality cutom aluminium casting parts Pls contact us sales@viewmold.com If you need high quality injection mold tooling, Contact us. Chemical and Physical Properties PP is produced by the polymerization of propylene using stereospecific catalysts. Mainly, isotactic PP is produced (the methyl groups lie on one side of the carbon chain). This linear plastic is semicrystalline because of ordered molecular structure. It is stiffer than PE and has a higher melting point. The PP homopolymer becomes very brittle at temperatures higher than 0 C (32 F) and for this reason, many commercially available grades are random copolymers with 1 - 4% ethylene or block copolymers with higher ethylene content. Copolymers have a lower heat distortion temperature (approximately 100 C / 212 F), less clarity, gloss, and rigidity, but greater impact strength. The material becomes tougher as the ratio of ethylene increases. The Vicat softening point is approximately 150 C (302 F). Because of high levels of crystallinity, the surface hardness and scratch resistance is higher for these materials. PP does not have environmental stress cracking problems. PP is usually modified by addition of glass fibers, mineral fillers, or thermoplastic rubbers. The MFR of PP ranges from 1 to 40; lower MFR materials have better impact strength but lower tensile strength. The copolymer is tougher than the homopolymer of the same MFR. The viscosity is more shear and temperature sensitive than PE. Due to crystallinity, the shrinkage is relatively high (order of 0.018 - 0.025 mm/mm or 1.8 - 2.5%). The shrinkage is more uniform than PE-HD (the difference in flow and cross-flow shrinkage is typically less than 0.2%). Addition of 30% glass reduces the shrinkage to approximately 0.7%. Both homopolymer and copolymer PP offer excellent resistance to moisture and good chemical resistance to acids, alkalis, and solvents. However, it is not resistant to aromatic hydrocarbons such as benzene, and chlorinated hydrocarbons such as carbon tetrachloride. It is not as resistant to oxidation at high temperatures as PE. If you need to look for more plastic resin injection molding processing condition, could you please click it. If you need high quality plastic extrusion services, Pls contact us sales@viewmold.com If you need high quality sheet metal parts, Pls contact us sales@viewmold.com The following is other plastic processing condition: ABS injection molding processing condition, HDPE injection molding processing condition, LDPE injection molding processing condition, PA12 injection molding processing condition, PA6 injection molding processing condition, PBT injection molding processing condition, PC-ABS injection molding processing condition, PC-PBT injection molding processing condition, PEI injection molding processing condition, PETG injection molding processing condition, PMMA injection molding processing condition, POM injection molding processing condition, PPE injection molding processing condition, HDPE injection molding processing condition, PP injection molding processing condition, PS injection molding processing condition, PVC injection molding processing condition, SAN injection molding processing condition,
Procure materials faster, build products more cost-effectively, and ship directly to customers with the breadth and scale of our global supply chain network.
Our Advanced Process Validation allows you to establish optimum processing parameters and validation criteria for FDA and other regulated specifications.
GETTING A QUOTE WITH LK-MOULD IS FREE AND SIMPLE.
FIND MORE OF OUR SERVICES:
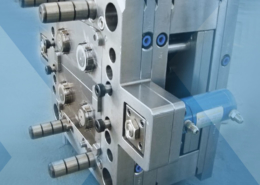
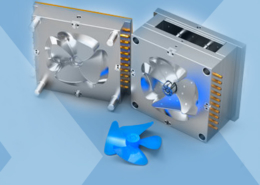
Plastic Molding

Rapid Prototyping
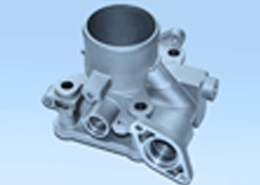
Pressure Die Casting
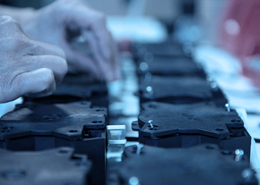
Parts Assembly
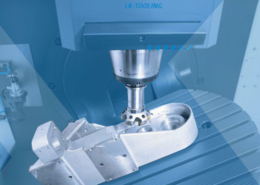