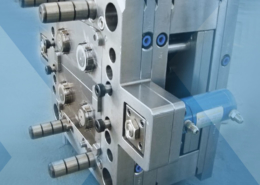
Angling A.i.: Fishing Lure Molds | Aluminum Bait Molds - basstackle molds
Author:gly Date: 2024-10-15
Experience the Thogus Difference Connect with us today to discuss your project and to learn more about our capabilities.
Short run production, also sometimes called small batch injection molding, produces a limited number of parts, either for highly specialized projects or for preliminary manufacturing of eventually larger runs. For this reason, short run production is often used in initial product development to create a set of pieces to determine whether they work together as intended. Short run production can also be used to create replacement parts after a product is on the market. During the initial product release, a long run may be necessary, but after that point a smaller number of parts may need to be continually produced for service and replacement.
The pneumatic vice can generate a force of up to 4000 Newton at 8 bar, which ensures that the molds are closed with adequate pressure even for very complicated molds. Furthermore, an automatic feeding system can be used with the pneumatic version of the injection molding machine. This automatic injection system allows you to manage both the timing of the closing vice and the timing of the descent of the piston for the injection, thus helping obtain the constancy of processing times and improve the quality of the work.
Founded in 1950, Thogus is an established, family-owned custom plastic injection molder and contract manufacturer headquartered in Avon Lake, Ohio.
The use of Pneumatic Injection Molding with Pneumatic Clamp in combination with the Automatic Material Feeding system allows the material to be fed automatically before each injection cycle, giving the possibility of speeding up, facilitating and improving the quality of the work. The Automatic Material Feeding system manages the loading of the material using a microprocessor, feeding the injection chamber with the necessary amount of pellet.
Even if you’ve already done a short run, you’ll need to invest in a more complex set of molds for a long run manufacturing process. In a long run, each mold typically contains multiple cavities, meaning they are more expensive to produce than the molds used in limited short runs.You can also expect high material costs at the start of long run production, as large quantities of material are needed to produce the high part counts characteristic of this production process. ROI in a long run comes from volume. Long runs work quickly to churn out large numbers of parts; the more parts that are produced, the lower the cost per part as the price of the mold and material is distributed among them. The faster parts are produced, the more quickly you get your investment back and the run begins to pay dividends. Whether you need a short or a long run for your project, Thogus is here to help. Learn more about our injection molding capabilities.
Short run production follows essentially the same manufacturing process as any other injection molding run. That means that appropriate materials need to be selected and tooling needs to be created specifically for each short run project. Plastic injection molders will have some things that you need for your project, like the injection mechanism, on hand. However, the mold itself must be custom created for each project. Because the mold has to be manufactured regardless of the size of the run, you can expect higher cost per part in short run production. However, short runs have the advantage of extremely fast time to market. Prototypes can be produced and evaluated quickly and working models can be in customers’ hands within a very short timeframe.Short run production can also help prepare for long run production, if that’s where your project is headed. Short run tools can be easily and inexpensively modified to become long run tools, and the revenue from an initial short run can help finance production costs in a long run.
The fact that 3D printed resin molds can be used with the Benchtop Injection Molding machine means that it is no longer necessary to make custom CNC machined aluminum molds for small scale production. This is a huge step towards making plastic injection molding accessible to all kinds of audiences. It should be kept in mind that molds produced with 3D printers have to be placed inside metal counter molds (provided by the manufacturer on request).
Plastic injection molding is famous for long run production, where large quantities of parts (often in the millions) are produced quickly. To accommodate this capacity, long run production uses bigger molds than short run production, and tends to have higher startup costs, though the cost per part is low when compared to other manufacturing methods.
The CE certified pneumatic Benchtop Injection Molding machine for thermoplastic molding was developed and manufactured in Italy by Robot Factory. The Benchtop Injection Molding machine is available in two options: a manual vice for mould clamping with a lever mechanism or a pneumatic vice for mould clamping with an automatic Ø 80mm piston mechanism.
The materials tested and recommended for use with the Benchtop Injection Molding machine by Robot Factory are PE, PS, PMMA, TPV, EVA, PP, ABS and TPU/TPE. Those polymers can be used in the form of pellets or plastic shreds recycled from 3D printing waste, for example with the help of the Felfil plastic shredder or the ProtoCycler+. The Virtual Foundry 316 stainless steel Filamet pellets (80 % metal, 20 % PLA base) were also tested with the Benchtop Injection Molding machine with satisfying results. Materials that are not recommended are PC, PET, PVC and Nylon.
In addition to the injection system (timing control) you can also automate the entry of material. The new Automatic Material Feeding system is one more piece that adds to the universe of Pneumatic Injection Molding, making the system increasingly powerful and competitive in the market.
More detailed technical information on the Benchtop Injection Molding machine can be found in the Manual in the Downloads section.
The Benchtop Injection Molding system by Robot Factory is based on the simple principle of injection molding where compressed air moves a Ø 63 mm piston to inject molten plastic into a mold placed in the injection chamber. Once the plastic is at its melting point, it is injected into a two shell mold and it assumes the shape of the mold, maintaining the new shape as it cools and solidifies.
Plastic injection molding is a highly versatile manufacturing process; it can produce large quantities of parts relatively inexpensively in a short period of time, or it can allow for meticulous product development, smaller batches of parts, and more extensive prototyping. The kind of run you need will depend on your end goals for your part, as well as its complexity and your project timeline. The following considerations and expectations will help you decide between short run production and long run production for your project.
Furthermore, to adapt to the constantly changing production practices, the Benchtop Injection Molding machine enables the user to produce parts with recycled material or from raw materials readily available on the market, for example pellets. This makes the Benchtop Injection Molding machine a user friendly and ecological manufacturing solution.
While normally the mold is made of aluminum or steel, the pneumatic clamp in the Benchtop Injection Molding machine is also compatible with FFF or SLA 3D printed resin molds provided that they are designed to have a sufficient thickness and that the filament or resin used for making the molds is suitable for temperatures of up to 350 ºC. In the case of FFF molds, suitable mold materials would be PPS, PBT, Ultem or Peek, and in the case of resin molds, the High Temp Resin by FormLabs would be ideal.
Plastic injection molding is a decades old manufacturing method used to inject thermoplastic material into molds for the purpose of prototyping, production or research and development. Despite its popularity, traditional plastic injection molding is still relatively costly and only rentable for mass production. The Robot Factory Benchtop Injection Molding machine bridges that gap as it can be used at any scale by anyone, especially for the manufacturing of small and medium size electronics, jewelry pieces and medical devices.
The capacity of its injection chamber is 32 cm3 (about 32 g by weight at 1.0 g/cm3 density) and the injection nozzle has a 6 mm diameter. The Benchtop Injection Molding machine weighs only about 14 kg and measures 260 (width) x 400 (length) x 700 (height) mm, which makes it ideal for any workshop or even a standard desk.
GETTING A QUOTE WITH LK-MOULD IS FREE AND SIMPLE.
FIND MORE OF OUR SERVICES:
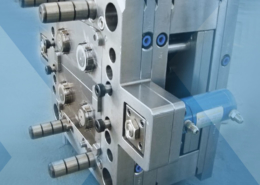
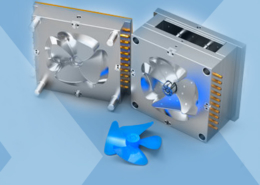
Plastic Molding

Rapid Prototyping
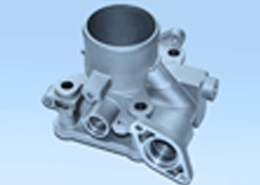
Pressure Die Casting
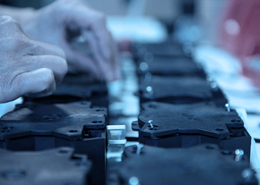
Parts Assembly
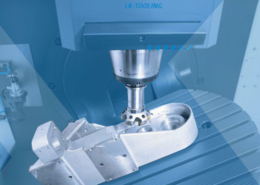