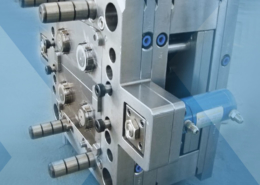
An Overview and Comparison of Multi-Material Injection ... - multi shot injectio
Author:gly Date: 2024-10-15
As the application scope of ASA and ABS continues to expand, concerns about safety hazards in plastic products have arisen: Is ASA toxic? Is ABS safe?
Manufacture is supported by Shamrock’s ISO based Quality Management System and upon final assembly all new Tooling is finish assembled under a “Buddy System” with one Toolmaker supporting & checking the other for the purpose of ensuring Specification Compliance & Quality Assurance.So if you require quality Plastic Injection Moulding Dies, accompanied by a professional service, call us at Shamrock Industries for a no obligation discussion.
Home | About Us | Products & Services | Technologies & Expertise | Working with us | Contact Us Precision Engineers, Tool and Die Makers, CNC Machining Specialists, CAD/CAM Manufacturers 51 Sandyford Street, Sydenham, Christchurch, New Zealand, Ph. 03 365 7906 Email sales@shamrock.co.nz Website by Zen Solutions Ltd. © Shamrock Industries Ltd 2010-2024
Overall, both ASA and ABS are versatile thermoplastic polymers that, despite their similarities, possess unique characteristics to meet different application needs.
The acetone smoothing method, known for achieving a high-gloss surface effect on ABS, is equally applicable to ASA materials. ASA injection molding products do not require painting, plating, or other surface protection and can be used outdoors directly.
ABS and ASA both exhibit good thermal stability during processing, but ASA’s enhanced resistance to UV light can translate to better long-term thermal stability in outdoor applications.
2D and 3D design files can be sent and received via email or disk, allowing us to develop and confirm the Tool design in consultation with you. Alternatively, your finished designs may be received electronically and entered directly into manufacture for exact and cost effective production.
ABS plastic is a terpolymer made from acrylonitrile (A), butadiene (B), and styrene (S), combining the properties of PB, PAN, and PS to create a material with a balanced set of mechanical characteristics that are tough, hard, and rigid.
Therefore, it is recommended to use ABS in well-ventilated areas and follow safety guidelines to minimize exposure to these emissions.
ASA is renowned for its outstanding weatherability and UV resistance, making it highly suitable for outdoor use where it can maintain its color and physical properties over extended exposure to natural elements.
In the numerous plastic applications where mechanical strength and stiffness are essential, ASA and ABS are often the materials of choice.
On the other hand, ASA boasts strong UV and impact resistance, making it suitable for various outdoor installations such as signage, sports equipment, and automotive exterior applications.
In additive manufacturing, its other common uses include prototyping, gears, and even tools, as it offers better resistance to physical stress than some other common 3D printing polymers.
Technically, ASA not only retains the main properties of ABS but also incorporates the weather resistance advantages of PMMA plastic, extending its application to outdoor uses.
The substitution of rubber double bonds plays a pivotal role in defining the subtle yet significant differences in performance between ASA and ABS.
ACIS®, Autodesk Inventor®, CATIA® V5,Creo™ Parametric, IGES, Parasolid®, Pro/ENGINEER®,Siemens PLM Software’s NX™, SolidEdge®, SolidWorks®, STEP
Compared to ABS, ASA significantly improves weather resistance by substituting butadiene rubber with acrylate rubber, which lacks double bonds.
Its electrical insulation properties also make it attractive for those looking to manufacture casings for electrical components, as well as automotive parts like dashboards or bumpers.
In terms of health and environmental safety, ABS does not contain any known carcinogens and is generally considered non-toxic when it is in its solid form.
However, the major drawback of ABS is the intense fumes produced during printing, accompanied by issues like warping, hence it’s recommended to print in well-ventilated areas.
In terms of heat resistance, ASA and ABS are relatively similar, with ABS having a heat distortion temperature of 93~118°C and still displaying some toughness at -40°C.
While both materials have the drawback of emitting fumes during processing, especially in 3D printing, this issue can be mitigated with appropriate safety measures.
Outstanding UV resistance and anti-aging capabilities mark a significant advantage of ASA and represent one of its largest differences from ABS plastic.
Additionally, for general purposes, it can be found in home appliances, hulls, decorative items, toys, and the renowned LEGO bricks.
ASA shares these strengths but stands out for its enhanced toughness and better integrity under UV exposure, especially in outdoor settings.
ASA can withstand degradation, aging, and fading caused by UV exposure, while also offering robust protection against decomposition or discoloration due to oxidation in the atmosphere and high temperatures during processing.
Despite its lower UV and weather resistance compared to ASA, ABS remains a popular choice for indoor applications where these factors are less critical, and its use continues to be supported by ongoing research and improvements in plastic formulation and processing techniques to enhance its safety profile.
Additionally, ABS’s composition allows it to be recycled, reducing its environmental impact compared to materials that cannot be easily processed for reuse.
This comparison highlights the key differences between ASA and ABS; for more insights into plastic materials, stay tuned to FOWMOULD!
ASA’s fire resistance is about ten times higher than that of ABS, with a fire rating of B1 level, meeting the basic fire protection requirements for residential housing, which ABS does not achieve.
ABS has been noted to emit styrene during printing, a VOC with potential health risks in poorly ventilated spaces, while ASA is often regarded as having a less intense odor but still requires proper safety measures.
ASA contains modifiers in its composition that enhance its resistance to UV-induced fading and yellowing, making it more suitable for applications where long-term aesthetic appeal is important.
Yet, printing with ASA typically demands higher extrusion temperatures, and it is pricier compared to ABS, necessitating a balance between cost and application needs when selecting plastic materials.
Our full CAD/CAM capability means that, from your Tooling concept, we can comprehensively design then accurately and cost effectively manufacture the finished Tool.
Accordingly, Moulding Dies may be custom designed by Shamrock or produced from client supplied drawings or CAD/CAM files.
Our experience includes knowledge of appropriate Tool Design and Manufacture for the following range of plastic mould materials:
As we’ve mentioned, one of the main attractions of ABS is its technical nature, which tends to steer its applications towards industrial uses.
ABS is celebrated for its robust mechanical strength and stiffness, making it suitable for durable products, alongside notable impact resistance, even in cold environments.
ABS, known for its high impact strength and mechanical robustness, is the material of choice for consumer goods, automotive parts, and electronic housings.
When you’re in the market for excellence in the manufacture of Plastic Injection Moulding Dies, take advantage of the Shamrock team’s decades of experience.We custom design and manufacture for a broad spectrum of clients that have a wide variety of needs. Some of these include:
In the following content, we will delve into the performance of these two materials and comprehensively evaluate their performance in specific application scenarios.
Due to its unique structure, ASA offers similar chemical resistance to ABS but with better weatherability and UV resistance, which can translate into better long-term performance and safety in outdoor applications.
GETTING A QUOTE WITH LK-MOULD IS FREE AND SIMPLE.
FIND MORE OF OUR SERVICES:
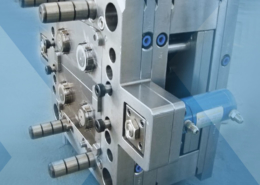
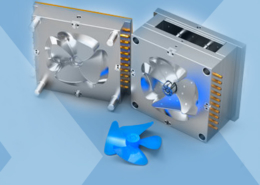
Plastic Molding

Rapid Prototyping
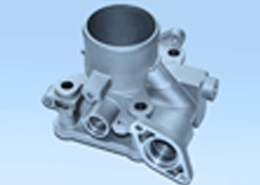
Pressure Die Casting
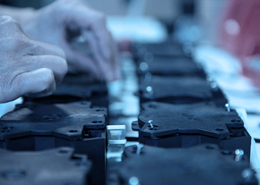
Parts Assembly
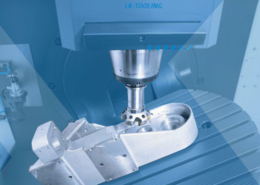