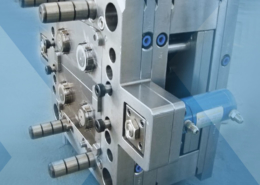
Aluminum Injection Mold: Home - injection moulding aluminium
Author:gly Date: 2024-10-15
“We received the charger base and I want you all to know it looks FANTASTIC! Thank you for getting us this one for the BOD meeting.”
Yes, multiple colors can be run even on the same order! When running multiple colors on the same order, a purge charge will be added.
AIM Processing specializes in small part plastic injection molding. We define "small plastic parts" as roughly the size of your fingernail to the size of your hand. Injection molding is a process in which plastic resin, in pellet form, is heated and sheared until it reaches a viscous state.
At Xometry, we first review your plastic injection molding online quote, then consult with you to ensure your specifications, lead time, and price fit your project needs. We then use your 3D part data to CNC machine a high-quality injection mold. Once the molded parts are created, Xometry sends ten part samples (T1) for approval. Once the mold is refined and approved, Xometry begins production. Xometry molds a variety of products and parts from the smallest medical insert up to large automotive, aerospace, and defense parts.
After receiving the order, the statement of work is reviewed by one of our manufacturing engineers. A case manager is assigned, and an appropriate manufacturing supplier is identified. A comprehensive DFM/PEG report is created and provided for approval. Upon approval, tooling and mold production is commenced. T1 samples are produced and shipped for approval. Upon approval, the remaining parts are made.
Several injection molding, liquid silicone molding, and compression molding options are available for an online quote. If you do not see the material stock you are looking for, please choose âOther" under the material drop-down on your quote page and submit for an expert engineering review once you have specified features, tolerances, inspection needs, and quantities required.
Get custom plastic molded prototypes and production parts in as few as five business days. We provide expert engineering reviews and $500 off your first mold. Dozens of materials and finishes are available.
The plastic injection molding process requires an injection molding machine, raw plastic material, and a machined mold. The raw plastic material is first melted in the injection unit and is then injected into the moldâmost often machined from steel or aluminumâwhere it cools and solidifies into the final plastic part.Â
Then there are factors like the manufacturability of gate locations, draft, and ejector pins. It's enough to make your head spin.
Standard injection mold tooling is defined by classes from Class 105 (prototype) to Class 101 (high volume production). These mold classes help manage expectations for both customers and suppliers on the overall tool requirements and scope.
VDI 3400 Surface Finish (commonly known as VDI surface finish) refers to the mold texture standard set by Verein Deutscher Ingenieure (VDI), the Society of German Engineers. This is mainly processed by EDM machining, producing fine to coarse matte finishes.
Injection molding is used across a wide range of industries including aerospace, medical devices, consumer goods, energy, electronics, automotive, robotics, toys, and more.
Steel and aluminum; Production grades range from Class 105, a prototype mold, to Class 101, an extremely high production mold. Xometry typically produces Class 104, 103, and 102 tools.
It is then injected under enormous pressure into a steel or aluminum mold, cooled until it hardens, and ejected. With small part injection molding, we are able to manufacture complex, small shapes in a cost-effective, repeatable process.
Under 500 cycles. Prototype only. This mold will be constructed in the least expensive manner possible to produce a minimal quantity of prototype parts. Class 105 molds are also known as Class V tools.Example: a one-and-done market test of 100 molded units.
Moldmaker's choice of finish. Typically SPI B-2, depending on geometry and drafts. Interior, non-cosmetic faces, are typically as-machined.
Discover AIM Processing's customer small part injection molding services, designed to deliver precise, high-quality components for industries requiring intricate and complex plastic parts.
At Xometry, our customers own their injection mold tools! After a run is complete, the tool will remain at our facilities. Tools can be shipped to you upon request; however, you will be responsible for any associated shipping and packaging costs. Our engineers will work with you regarding tool compatibility with your equipment if you're unsure.
Bosses should be designed at a depth of 30% the wall thickness and with a 30% edge groove. Attach them to side walls or ribs for structural integrity.
Medium to high production tooling, suitable for abrasive materials or parts requiring close tolerance. This is a high-quality, reasonably high-priced mold. Class 102 Molds are also known as Class II tools.Example: Steel tooling with an SPI A-2 finish, automated slides, scheduled production cycles.
Over 1,000,000 cycles. They are engineered for extremely high production. This is the highest-priced mold and is made with only the highest-quality materials. Class 101 molds are also known as Class I tools.Example: Multiple-cavity steel tooling with full automation and overnight production work centers for dedicated part manufacturing.
Tighter tolerances can be requested and may increase the cost of tooling because of additional sampling and grooming. Xometry will mill to a steel-safe condition on critical features.
Xometry's platform has built-in features that make managing tooled projects a breeze, giving customers greater transparency into production. Find all your tooling quotes and orders in one space with your Tool Library. From there, you can explore their Tool Details page, which covers the current status, milestones, tool specifics, and activity related to that tool. You can also easily find and contact the Xometry team member assigned to your project, no matter the project's current phase.
Range of Society of Plastics Industry (SPI) finishes from Grade 3 diamond / high polish to 320 stone low polish. Finishes include: SPI A-1, SPI A-2, SPI A-3, SPI B-1, SPI B-2, SPI B-3, SPI C-1, SPI C-2, SPI C-3, SPI D-1, SPI D-2, and SPI D-3
With molding, plastic or metal parts are created inside a mold. They are then removed from the mold as fully-formed parts. 3D printing, on the other hand, is an additive manufacturing process, meaning that the part is built layer-by-layer using processes like deposition or sintering.
Injection molding is the most cost-effective way to make a plastic part at scale. The injection molding process involves injecting molten plastic into a mold tool, then ejecting the solidified part. This process quickly repeats hundreds or thousands of times, amortizing the cost of the mold tool and driving down the cost of each unit to a few dollars or less. Since the injection molding process uses the same mold tool for each part, it offers consistent quality across every part. Injection molding also has the highest variety of materials, colors, cosmetics, polishes, and surface textures when compared to CNC machining or even 3D printing.
Reduce undercuts, which will increase the complexity and cost of the tool ejection mechanisms, by adding in pass-thru coring.
Xometry's custom plastic mold service is a service providing on-demand prototype and production molding. We take a customer-first approach which means we find the right injection molding supplier within our manufacturing supplier network to mold the parts the way you need themâwithout design compromisesâat the right price point. We offer expert consultation on each injection mold quote and project managers on every order to move your parts from design to production. Our team has experience in every industry, especially medical injection molding and liquid silicone rubber molding. First-time buyers receive $500 off their first mold with Xometry. We offer both domestic and China injection molding options, as well as ITAR injection molding.
This table depicts the general tolerances for Xometryâs injection molding services and accounts for adequate draft, radii, and coring for manufacturability. Learn more about our injection molding manufacturing standards.
Under 100,000 cycles. Low production mold. Use only for limited production, preferably with non-abrasive materials. Low to moderate price range. Class 104 molds are also known as Class IV tools.Example: Aluminum or MUD tooling, SPI B-3 finish, hand-loaded cores, and limited re-runs.
Choose from millions of possible combinations of materials, finishes, tolerances, markings, and certifications for your order.
Injection molding can be the ideal process for low-volume production molding of 250 units to mass production molding of over 1,000,000 units. Plastic injection parts will generally perform better than the same part CNC machined or 3D printed using the same material. Careful selection of the resins allow for a wide range of properties and solvent compatibility. Molds are CNC machined to high precision, high tolerances and are able to produce thousands of identical parts with very small and intricate details.
The design and manufacture of custom molded plastic parts can seem simple at first, but there are many details that must be taken into consideration depending on how the part will be used. For example, there are mechanical properties like:
Under 500,000 cycles. Medium production mold. This is a very popular mold for low to medium-production needs. Most common price range. Also known as a Class III tool.Example: Aluminum or steel tooling, automated lifts or slides, multiple re-runs with batches between 1,000-5,000 units.
As a leading small plastic parts manufacturer, we work with engineering grade plastics to create custom molded plastic parts that match the requirements for a part with properties like: chemical resistance, flexural strength, durometer, and yield strength to name a few. There are so many material options, and we can help you make the right choice for your program.
We are ISO 9001:2015, ISO 13485, and AS9100D certified. Only the top shops that apply to become Suppliers make it through our qualification process.
Manufacturing elastomeric parts can be accomplished through injection molding, transfer molding, or compression molding. When getting a quote through Xometry, our team can help you decide the best method depending on the part geometry, estimated annual volume, and the type of material required.
Range of finishes including matte, swirls, lines, and patterns. Our most common texture finishes include: MoldTech MT11010, MoldTech MT11020, and MoldTech MT11030. Other textured finishes can be added by request.
GETTING A QUOTE WITH LK-MOULD IS FREE AND SIMPLE.
FIND MORE OF OUR SERVICES:
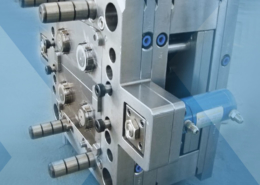
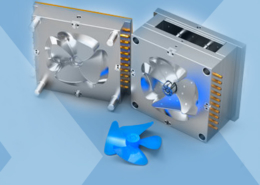
Plastic Molding

Rapid Prototyping
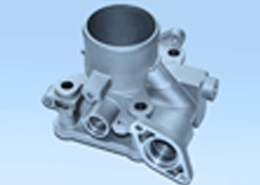
Pressure Die Casting
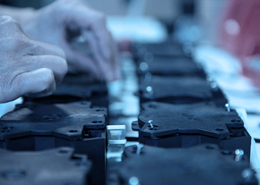
Parts Assembly
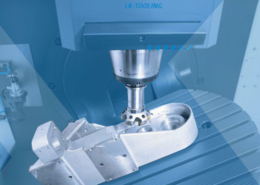