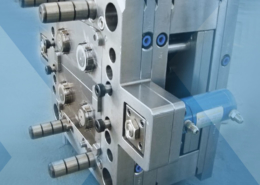
ALL SERVICE PLASTIC MOLDING, INC - all service plastic molding inc
Author:gly Date: 2024-10-15
An injection moulding machine is a complex piece of machinery that creates one solid part by injecting molten materials through a reciprocating screw system into a mould. This machine is made of many components; it is primarily consisted of a hopper, a barrel containing a reciprocating screw, temperature control devices, a clamping unit and the […]
Steel is a catch-all phrase use to describe a group of iron alloys. These alloys all have one thing in common: malleability. Steels can all be melted down and used in the injection moulding process to create everyday items. Steels can be cast directly into moulds, or can be made into other forms which allow […]
There are many factors to consider when designing for manufacture through injection moulding. You need to make sure your product can be accurately and consistently produced, yet it may need particular features or parts that will require extra efforts on the part of the Toolmakers. To ensure your design is smooth and the injection mould […]
A lot of people go through life with no real interest in the ‘behind the scenes’ stuff. They don’t want to know where their dinner came from, they just want to know it’s in front of them. They have a similar opinion on everything from how their car works to the physics that drive our […]
When you’re developing your product, the designer might come to you and say “I want to reduce the wall thickness in your part” even though you’ve said time and time again that you want a strong durable product. So why do designers push for thin walls? Let’s find out… There are three main reasons injection […]
Plastics are used for their versatility and flexibility in application. They can be used in everything from body parts to automotive components. The process of creating these parts involves a moulding process, and these are some of the most common types of moulding techniques in use. Blowmoulding This type of moulding is suitable for hollow […]
Living Hinges, it sounds weird, right? Especially when you are talking about plastic product. There’s nothing “living” about plastic. In this article, we are going to unpack the Living Hinges (also known as integral hinges) in Injection Moulding and why they should be in your product. A living hinge is basically a thin bridge of […]
Although Delrin® is so well known that the name is sometimes used interchangeably for acetal resin in general, there are key differences between acetyl copolymers and Delrin®. As an acetal homopolymer, Delrin® has a larger, uniform crystal block structure that provides better chemical bonding than acetyl copolymers. That imparts higher tensile strength, stiffness, creep and fatigue resistance, and much higher impact resistance. The combination of these mechanical properties give Delrin® significant advantages for part design and production, including:
Your labour costs will be barely noticeable when you consider that you won’t need to waste additional time joining or trimming your final products, as well as less rejects to deal with due to human error.
Plastic injection moulding is used to produce everything from vehicle parts and bodies to buttons on clothing. The impact of plastic injection moulding is visible in the daily lives of millions of people, with the average household containing a number of items created through this vital manufacturing process. However, few people understand just how plastic […]
Steel is a catch-all phrase use to describe a group of iron alloys. These alloys all have one thing in common: malleability. Steels can all be melted down and used in the injection moulding process to create everyday items. Steels can be cast directly into moulds, or can be made into other forms which allow […]
If you have an injection moulding project, contact Dienamics today for your high quality, low cost injection moulding solutions that can be customised to your businesses specific needs.
How does a Sprue Picker work? A sprue picker is a piece of specialized machinery that picks the sprue out of an injection mould, usually as the parts are being ejected. The sprue picker can then drop the sprue to either the operator side or the far side of the injection moulding machine. Now let […]
Let’s talk about bosses. And no, not the ones whipping you to do more work, but the rather helpful ones in plastic injection moulding. Bosses are design elements that strengthen parts. We’re going to unpack why you should have bosses, how to design them appropriately and some common part failures which can be avoided […]
Warpage: it’s the bane of the designer when it comes to injection moulding. Warpage occurs when cooling of the part is inconsistent. A section of the part will set whilst another remains molten. The set area will restrict the proper setting of the still molten area, resulting in warped parts that must be rejected or […]
The concept of injection moulding is simple enough. First, the moulder fills the machine with plastic pellets. Then colorants are added to create the desired colour (we can do just about any colour by the way, even metallic hues). After that the plastic is heated up to its melting point, liquefying it. The molten plastic […]
Most people are not aware of what plastic injection machinery is. In terms of product design, all of us are surrounded by plastic objects made with plastic injection machines – such as water bottles, telephone handsets, CD covers, dust bins, electric outlets and a lot more. Did you ever realize that these commonly used items […]
The basic concept behind rapid Tool Design for injection moulding has remained unchanged for the past 20 years. However, it is important to understand this basic concept to ensure success with injection moulding. This article will outline the four steps to success in rapid injection moulding product design.
In this article, we’re talking about gates. And no, not the kind that you shut behind you when you’re leaving the farm. In plastic injection moulding a Gate is where the molten plastic enters the cavity of the tool. That’s to say it’s different from the sprue or runner. Sprues and runners are simply there […]
Using recycled plastics can have big benefits, not just in reducing the overall cost of the manufacturing process but also the environmental impact it has by reducing the amount of plastic going into landfill. More often we are finding customers are wanting to use recycled plastics in the manufacture of their products. In this blog […]
If you’re a manufacturer of products that utilise plastic parts or you’re in the process of becoming a manufacturer, it’s likely you’ve considered getting a quote for injection moulding. As injection moulders, we are known for our ability to help product engineers get their item to market efficiently and cost-effectively. Obtaining an injection moulding quote […]
Until recently, most third party inspectors have used a fixed-base Coordinate Measuring Machine (CMM) to inspect the accuracy of plastic injection-moulded refrigerator parts. 3D Engineering Solutions, an ISO 17025 certified third-party inspector, has since announced the successful use of new scanning technology that captures millions of data points during inspection rather than just hundreds. Rob […]
Injection moulding is a plastics moulding methodology that is known for its reliability. It is widely used, with applications from large pieces to small computer components. These are some of the key industries in which injection moulding is widely used. Computing and electrical industries Computing and electrical parts use plastic components to hold moving parts […]
As your concept progresses through the design and development phases, it’s important to think about how you want your product to be manufactured. If you’re looking to produce it in a large volume, then injection moulding can be the way to go. What is injection moulding? Injection moulding is a manufacturing process for producing parts […]
Undercuts. No Plastic Injection Moulder wants them and every DIY part design has them. Undercuts, are part and parcel of what we do here at Dienamics. Most of our clients are looking to create or improve their own products, but are restrained to a strict budget. So, one of the first things we look for […]
Injection moulding is an affordable, versatile, and efficient manufacturing process that has earned an admirable place within the business of any production company.
As your concept progresses through the design and development phases, it’s important to think about how you want your product to be manufactured.
Living Hinges, it sounds weird, right? Especially when you are talking about plastic product. There’s nothing “living” about plastic. In this article, we are going to unpack the Living Hinges (also known as integral hinges) in Injection Moulding and why they should be in your product. A living hinge is basically a thin bridge of […]
In this article, we’re talking about gates. And no, not the kind that you shut behind you when you’re leaving the farm. In plastic injection moulding a Gate is where the molten plastic enters the cavity of the tool. That’s to say it’s different from the sprue or runner. Sprues and runners are simply there […]
Very recently, an old relic has resurfaced from the ‘90s electronics junk heap to become useful once again: the plastic injection moulds that were used to make the plastic components for the Atari Jaguar. These moulds, which cost Atari US$250,000 to design and build in the first place, were part of a “tooling package” that […]
Plastics are the common name for man made polymers. Chemically, these materials are made up of a single unit, the monomer, which will link up with millions of itself to form long chains. The length of these chains, if they have many branches, and how tightly they wrap together determine the physical properties of the […]
Injection moulding can do almost anything. This technology, created in the 1940s and constantly refined, allows for incredible flexibility in product design and has effectively revolutionised mass production. Injection moulding is the process of forcing molten materials into a mould or die. The material is then cooled, the finished result taking on the physical characteristics […]
A lot of people go through life with no real interest in the ‘behind the scenes’ stuff. They don’t want to know where their dinner came from, they just want to know it’s in front of them. They have a similar opinion on everything from how their car works to the physics that drive our […]
Threads are critical in Injection Moulding. Not only do they require more complexity in the tool design, the resulting plastic part must work perfectly, with next to no warpage and align perfectly when assembled. It’s important that you get it right the first time, so in this article we’ll explore what you need to know […]
Injection moulding is one of the most widely used polymer-moulding techniques in the world. It is used to produce everything from automotive parts and gear transmissions to furniture and household items. Cost factors One of the reasons why injection moulding has been so widely used is due to its cost benefits. The injection-moulding process is […]
For those of you who want to know a little more about plastic injection moulding, this article will attempt to explain, in layman’s terms, exactly what this means. Basically, injection moulding is a process that was first designed in the 1930s. Up until then die casting, or the process by which metals are cast from […]
Plastic injection moulding is used to produce everything from vehicle parts and bodies to buttons on clothing. The impact of plastic injection moulding is visible in the daily lives of millions of people, with the average household containing a number of items created through this vital manufacturing process. However, few people understand just how plastic […]
Most people would hear the term tool making and assume it is about making hammers, screwdrivers and spanners. In actual fact a toolmaker is a trade professional who builds Moulds, Dies and jigs. They are an essential part of product development and the manufacturing of plastic products. If you’re looking to get your product developed, […]
As your concept progresses through the design and development phases, it’s important to think about how you want your product to be manufactured.
In the world of manufacturing, the precision and quality of your products are paramount. At the heart of manufacturing, especially in industries relying on plastic components, lies the process of injection moulding. This method generally uses multiple moulds that come together and close to form a “cavity” that is the shape of the manufactured product. […]
Due to its properties, Delrin® is typically used for demanding applications in the automotive, industrial engineering, electronics, consumer goods, domestic appliance, and sports industries. Of course, to get the most out of the advantages Delrin® can provide, you need an experienced manufacturing partner who can help determine the ideal type of material to use for your project. Southwest’s engineering team can help you select the right variety if your part has unusual requirements.
Injection moulding is an affordable, versatile, and efficient manufacturing process that has earned an admirable place within the business of any production company. It’s used to make everything from Gameboys to gears, and with the process standing as one of the best options for businesses developing products. There’s a myriad of benefits to swapping over […]
A new paper by The Linde Group has revealed that carbon dioxide (CO2) can be used to cut cooling cycles and overall production cycles in injection moulding. The white paper is concerned with the manufacturing technique of gas assist injection moulding, which traditionally uses nitrogen as the gas of choice. However, the paper revealed that […]
The plastic injection moulding process is highly technical, and by no means an easy job. There’s a lot of room for expensive error, which can range from minor defects to major issues that could affect your product’s performance, desired design result, and safety.
How does an Autoloading Hopper work? An autoloading Hopper is just like a regular hopper, except that it can load material from storage bags around the machine. It does that by using a vacuum placed on top of the hopper. This vacuum is caused by a fan, connected to an electric motor. As the fan […]
Speaking of labour costs, another added advantage to the moulding process is how easily automatable it is. It requires very little supervision and oversight once the ball starts rolling. Our own machines are fully programmable with reproducible conditions that can be replicated with a touch of a button.
Drinktec 2013 was held during the month of September. This year, the Munich exhibition showcased injection moulding machines by Arburg and Engel. Engel Engel showed its e-cap 3440/380 injection-moulding machine that had a 72-cavity mould. The mould was created by z-moulds, a specialist Austrian toolmaker. The cell has the capacity to produce 1.8g still water […]
There are many factors to consider when designing for manufacture through injection moulding. You need to make sure your product can be accurately and consistently produced, yet it may need particular features or parts that will require extra efforts on the part of the Toolmakers. To ensure your design is smooth and the injection mould […]
Here at Dienamics, we have been pushing carbon neutral practices through the use of multiple new technologies. It is our goal to become carbon neutral and we have invested time and money into new technologies and strategies in an effort to become more eco friendly. This year, we have invested in more solar panels for […]
To ensure a successful finished product, you need to be aware of the process that goes into making your component. This should be at the forefront of your mind when considering the design of your part. Injection moulding will provide you with the component you want, and if you are able to consider its process […]
Warpage: it’s the bane of the designer when it comes to injection moulding. Warpage occurs when cooling of the part is inconsistent. A section of the part will set whilst another remains molten. The set area will restrict the proper setting of the still molten area, resulting in warped parts that must be rejected or […]
For some, the cosmetic appearance of a part is the last thing on your mind. It might be that the part is being used internally, hidden from view, or the appearance is not a key point of sale for your part or product. But for many, the cosmetic appearance is of great importance, and something […]
Discover how overmoulding in injection moulding, product design, and industrial design can enhance your product development and user experience.
While Delrin® is the stiffest unreinforced engineering polymer available, DuPont also offers dozens of specialized varieties of the resin that have been treated or reinforced to enhance selected characteristics. These include glass-reinforced polymers for extra strength; UV-stabilized polymers; polymers modified with PTFE fibers, lubricants, or Kevlar® for low wear and low friction; and polymers designed for food contact applications.
Drinktec 2013 was held during the month of September. This year, the Munich exhibition showcased injection moulding machines by Arburg and Engel. Engel Engel showed its e-cap 3440/380 injection-moulding machine that had a 72-cavity mould. The mould was created by z-moulds, a specialist Austrian toolmaker. The cell has the capacity to produce 1.8g still water […]
Injection moulding is a versatile process and can be applied to almost any product. Although injection moulding is the industry standard for fabricating parts for products, it is not without its holdups. There are a few basic limitations to be taken into account. Here’s eight rules to follow when designing your product to ensure quality […]
Most plastic products are created using a common manufacturing technique called ‘plastic injection moulding‘. During this process the raw material, some form of plastic, is completely melted and then inserted into a special mould. Then the material is cooled and expelled immediately. Most of the plastic items and products we use in our everyday lives […]
When it comes to injection moulding, there are many factors you need to consider to make sure you are putting the tool in a suitable machine and tonnage is an important one!
Let’s talk about bosses. And no, not the ones whipping you to do more work, but the rather helpful ones in plastic injection moulding. Bosses are design elements that strengthen parts. We’re going to unpack why you should have bosses, how to design them appropriately and some common part failures which can be avoided […]
The concept of injection moulding is simple enough. First, the moulder fills the machine with plastic pellets. Then colorants are added to create the desired colour (we can do just about any colour by the way, even metallic hues). After that the plastic is heated up to its melting point, liquefying it. The molten plastic […]
Injection moulding is an affordable, versatile, and efficient manufacturing process that has earned an admirable place within the business of any production company. It’s used to make everything from Gameboys to gears, and with the process standing as one of the best options for businesses developing products. There’s a myriad of benefits to swapping over […]
Peter Reid, a Senior Research Engineer from the CSIRO, had a problem. As part of a research project at Pullenvale, Peter was developing a machine that helped to map and survey mine sites using advanced technologies. Requirements He was using LiDAR and other light-based sensors to survey the mine. What he needed was an optically […]
When designing for manufacture with injection moulding, there are still more guidelines to be taken into consideration. The easier it is for the Toolmakers to create your mould, the faster your turnaround time will be, increasing the speed that your product will be out there for consumers. Here’s 10 more design guidelines to follow when […]
Injection moulding can do almost anything. This technology, created in the 1940s and constantly refined, allows for incredible flexibility in product design and has effectively revolutionised mass production. Injection moulding is the process of forcing molten materials into a mould or die. The material is then cooled, the finished result taking on the physical characteristics […]
Crack open almost any plastic shape and you will the internal volume is mostly air, and anything that actually does any work inside the part is reinforced by a strange pattern of thin little walls. Those little joining walls are called ribs, and they are one of the most important and powerful parts of any […]
When you’re developing your product, the designer might come to you and say “I want to reduce the wall thickness in your part” even though you’ve said time and time again that you want a strong durable product. So why do designers push for thin walls? Let’s find out…
When designing for manufacture with injection moulding, there are still more guidelines to be taken into consideration. The easier it is for the Toolmakers to create your mould, the faster your turnaround time will be, increasing the speed that your product will be out there for consumers. Here’s 10 more design guidelines to follow when […]
An injection mould is the key to creating a successful one-piece finished plastic or metal component. Melted material is forced from the injection moulding machine into the mould (which is usually cool) where it sets. The result is a solid piece of the material which may be a component to, or the whole of, a […]
The modern human owes many of his or her daily conveniences to the technique known as plastic injection moulding. This manufacturing technique has been in use since the 19th century. Key steps Key steps in the plastic injection moulding process include clamping, injection and cooling: Clamping keeps the mould in place under heating and other […]
Gas Assisted Injection Moulding is a highly technical form of injection Moulding, that uses both plastic and gas (usually nitrogen) to fill an injection mould under pressure. The main benefit of this manufacturing process is that it’s ability to form hollow parts in the cycle time of injection moulding machines. The basic process of Gas […]
The speed of production also means that the time saved on production speeds up your business processes. It means that you’ll be spending less cost on associated labour and profiting from the output.
Once your product has been designed, prototyped and you’ve ironed out any issues, it’s time to think about manufacturing. There are a few different techniques that could be used to manufacture your product. To decide which process is best for your product, think about: Market demand for your product Availability of resources The amount of […]
A lot of different casting products require finishing after the moulding process. One fantastic advantage of injection moulding is that they come finished right out of the mould looking great and ready to use.
Bosses are small cylindrical elements in a design. They are used for accepting screws or other fastening components (threaded inserts usually). Essentially they are locating, mounting and assembly devices built in to the design of the part and if not for accepting screws, will attach to the mating part of another component of the design. […]
Injection moulding is an efficient and effective way of producing quality goods. The process is simple in concept, but intricate details can have big impacts on costs, particularly on large production runs.
If you’re a manufacturer of products that utilise plastic parts or you’re in the process of becoming a manufacturer, it’s likely you’ve considered getting a quote for injection moulding. As injection moulders, we are known for our ability to help product engineers get their item to market efficiently and cost-effectively. Obtaining an injection moulding quote […]
Most plastic products are created using a common manufacturing technique called ‘plastic injection moulding‘. During this process the raw material, some form of plastic, is completely melted and then inserted into a special mould. Then the material is cooled and expelled immediately. Most of the plastic items and products we use in our everyday lives […]
The basic concept behind rapid Tool Design for injection moulding has remained unchanged for the past 20 years. However, it is important to understand this basic concept to ensure success with injection moulding. This article will outline the four steps to success in rapid injection moulding product design.
Flashing is one of the most common flaws found in injection moulded parts. Flash is fine, feathery sections that stick out from a finished part, usually at right angles to the wall section they connect to. What causes it? Sneaky plastic, that’s what. Technically, flash is plastic that has escaped from the mould cavity along […]
Delrin® is an acetal homopolymer (Polyoxymethylene POM) that combines low friction and high wear resistance with high strength and stiffness, making it ideal for injection-molded parts intended to replace metal. High-load mechanical applications where it can be successfully used include gears, door systems, safety restraints, conveyor system components, medical delivery devices, and more. Delrin® has a wide operating temperature range (from -40 degrees C to 120 degrees C), good colorability, good electrical insulating characteristics, and excellent dimensional stability in high-precision molding. It also mates well with metals and other polymers.
An injection mould is the key to creating a successful one-piece finished plastic or metal component. Melted material is forced from the injection moulding machine into the mould (which is usually cool) where it sets. The result is a solid piece of the material which may be a component to, or the whole of, a […]
How does an Injection Moulding Press work? An Injection Moulding Press or Injection Moulding machine is a rather complicated, fully automated piece of machinery. An injection moulding machine makes moulded plastic parts quickly and with a high degree of repeatability. The plastic parts can be made from a range of different plastics for different purposes. […]
Very recently, an old relic has resurfaced from the ‘90s electronics junk heap to become useful once again: the plastic injection moulds that were used to make the plastic components for the Atari Jaguar. These moulds, which cost Atari US$250,000 to design and build in the first place, were part of a “tooling package” that […]
The world’s first fully synthetic plastic was bakelite, invented in 1909 in New York by Leo Baekeland, who also coined the term ‘plastics’. Before that, semi-synthetic plastic products like celluloid and PVC rocked the late 19th century. The invention of parkesine in 1862 led the course and started a wave of plastic production that shaped […]
Injection moulding produces very little waste. Not only is it one of the most efficient users of raw material, but any excess isn’t wasted; you can simply recycle it back into the machine for future components.
Injection moulding is a manufacturing method where plastics are shaped (or ‘moulded’) to form all kinds of objects that we use in our everyday lives. If you’ve ever sat on some plastic lawn furniture, unscrewed a plastic bottle cap or combed your hair with a plastic comb, then you’ve probably used an item that was […]
Discover how overmoulding in injection moulding, product design, and industrial design can enhance your product development and user experience.
Have you ever gotten an injection? A flu shot? A vaccine? Anaesthetic? If the answer is yes then it’s almost guaranteed that a plastic injection moulded syringe was used. With plastic manufacturing becoming more reliable after WW2, the use of plastics in consumables began to become common practice, and with this even more progress […]
Are you looking for an efficient and cost-effective way to manufacture your product? Look no further than injection moulding. Injection moulding is a manufacturing process that involves injecting molten plastic into a mould to create a solid product. This process offers several advantages over other manufacturing methods. In this article, we will explore four advantages of […]
When it comes to injection moulding, there are many factors you need to consider to make sure you are putting the tool in a suitable machine and tonnage is an important one!
A sad fact of injection moulding and plastics manufacturing in general, is that plastic shrinks. And sometimes it shrinks a lot. So as plastic Injection moulders we’ve learnt to deal with shrinkage and today we are going to share a few of our tips and tricks to avoid excessive shrinkage and explain a bit about […]
For starters, there’s a wide spectrum of materials and colours that you can use in the process, but assuming you fit the basic design criteria you’ll also have a lot of flexibility in how you approach your design.
Injection moulding is an ideal manufacturing solution as it can be used to produce a wide range of products efficiently and cost effectively. Here, we look at 6 ways injection moulding can benefit your business:
Injection moulding is an efficient and effective way of producing quality goods. The process is simple in concept, but intricate details can have big impacts on costs, particularly on large production runs.
Last week’s blog was all about Cold Runner Systems, this week, it’s time you learnt all about the alternate option – Hot Manifold Systems! To reiterate last week’s blog, the runner system is what controls the distribution of the plastic from the moulding machine’s nozzle to the tool cavities. If you haven’t already read it […]
If you’re searching for the right manufacturer for your custom plastic molding projects with Delrin®, Southwest Plastics has the expertise and experience you’re looking for. As a proven U.S.-based engineering and manufacturing firm, we have worked continually over the years to keep our knowledge and capabilities at the forefront of our industry to provide top quality service at competitive prices to our clients in the automotive, aerospace, healthcare, electronics, telecom, and defense sectors. Our engineering department has the knowhow to solve challenging design problems and optimize your part design to take advantage of the features of materials like Delrin® for smoother manufacturing and better performance.
How does a Regrinder work? A regrinder or plastic granulator is an electrically powered series of grinding blades, which takes plastic and chops them up into little pieces, commonly referred to as regrind. This regrind is a major step in any plastics recycling scheme. It takes what was reject or waste plastic and breaks it […]
Plastic injection moulding is by far the most popular method for producing mass manufactured plastic products – though if you’re new to the design and manufacturing game, here’s a quick recap. An injection moulding machine has a few main elements; a material feeder, called a ‘hopper,’ where plastic granules are poured; a heated barrel […]
Injection moulding is a plastics moulding methodology that is known for its reliability. It is widely used, with applications from large pieces to small computer components. These are some of the key industries in which injection moulding is widely used. Computing and electrical industries Computing and electrical parts use plastic components to hold moving parts […]
Injection moulding is one of the most popular methods for manufacturing and mass producing plastic products. It can be used for a wide range of plastic products, from a button for your shirt, to parts for a car. If you’re thinking of using injection moulding to produce your product, the first step is to choose […]
Injection moulding is one of the most popular methods for manufacturing and mass producing plastic products. It can be used for a wide range of plastic products, from a button for your shirt, to parts for a car. If you’re thinking of using injection moulding to produce your product, the first step is to choose […]
Are you in the final stages of designing your product? If so, it’s time to think about manufacturing. If you’re looking to produce your product in a large volume, then injection moulding can be the way to go. In this blog, we’re giving you a comprehensive guide to injection moulding, so that you can know […]
If you take a quick look around your house, you can probably find numerous objects that were made using plastic injection moulding – even the computer or smartphone you’re viewing this on. Countless products are completely reliant on this process for their manufacture; many which are common items we use on a daily basis.
How does an Autoloading Hopper work? An autoloading Hopper is just like a regular hopper, except that it can load material from storage bags around the machine. It does that by using a vacuum placed on top of the hopper. This vacuum is caused by a fan, connected to an electric motor. As the fan […]
Plastics are used for their versatility and flexibility in application. They can be used in everything from body parts to automotive components. The process of creating these parts involves a moulding process, and these are some of the most common types of moulding techniques in use. Blowmoulding This type of moulding is suitable for hollow […]
Peter Reid, a Senior Research Engineer from the CSIRO, had a problem. As part of a research project at Pullenvale, Peter was developing a machine that helped to map and survey mine sites using advanced technologies. Requirements He was using LiDAR and other light-based sensors to survey the mine. What he needed was an optically […]
Using recycled plastics can have big benefits, not just in reducing the overall cost of the manufacturing process but also the environmental impact it has by reducing the amount of plastic going into landfill. More often we are finding customers are wanting to use recycled plastics in the manufacture of their products. In this blog […]
When you’re developing your product, the designer might come to you and say “I want to reduce the wall thickness in your part” even though you’ve said time and time again that you want a strong durable product. So why do designers push for thin walls? Let’s find out… There are three main reasons injection […]
Are you in the final stages of designing your product? If so, it’s time to think about manufacturing. If you’re looking to produce your product in a large volume, then injection moulding can be the way to go. In this blog, we’re giving you a comprehensive guide to injection moulding, so that you can know […]
An injection moulding machine is a complex piece of machinery that creates one solid part by injecting molten materials through a reciprocating screw system into a mould. This machine is made of many components; it is primarily consisted of a hopper, a barrel containing a reciprocating screw, temperature control devices, a clamping unit and the […]
Two highly effective and time-tested manufacturing techniques are Injection Moulding and Rotomoulding. Both techniques have their own distinct advantages and disadvantages and may or may not be suitable for your moulding requirements.
Injection moulding is one of the most widely used polymer-moulding techniques in the world. It is used to produce everything from automotive parts and gear transmissions to furniture and household items. Cost factors One of the reasons why injection moulding has been so widely used is due to its cost benefits. The injection-moulding process is […]
We’ve previously mentioned the importance of wall sections in our article about Ribs in Injection Moulding so in this article we’re going to go greater depths with that subject. We’ll talk about the basic process of injection moulding and how it relates to wall thickness, then outline some of the problems that may occur due to […]
The world’s first fully synthetic plastic was bakelite, invented in 1909 in New York by Leo Baekeland, who also coined the term ‘plastics’. Before that, semi-synthetic plastic products like celluloid and PVC rocked the late 19th century. The invention of parkesine in 1862 led the course and started a wave of plastic production that shaped […]
To ensure a successful finished product, you need to be aware of the process that goes into making your component. This should be at the forefront of your mind when considering the design of your part. Injection moulding will provide you with the component you want, and if you are able to consider its process […]
As your concept progresses through the design and development phases, it’s important to think about how you want your product to be manufactured. If you’re looking to produce it in a large volume, then injection moulding can be the way to go. What is injection moulding? Injection moulding is a manufacturing process for producing parts […]
While the mould themselves can be expensive to produce, you’ll be able to recoup that quickly once you begin production, often in magnitudes of 10-20 times the savings in large batch scale operations.
Discover how overmoulding in injection moulding, product design, and industrial design can enhance your product development and user experience.
Flashing is one of the most common flaws found in injection moulded parts. Flash is fine, feathery sections that stick out from a finished part, usually at right angles to the wall section they connect to. What causes it? Sneaky plastic, that’s what. Technically, flash is plastic that has escaped from the mould cavity along […]
Are you looking for an efficient and cost-effective way to manufacture your product? Look no further than injection moulding. Injection moulding is a manufacturing process that involves injecting molten plastic into a mould to create a solid product. This process offers several advantages over other manufacturing methods. In this article, we will explore four advantages of […]
The biggest advantage of injection moulding is a three-pronged feedback loop that keeps on benefitting you and your company the longer you use it.
Threads are critical in Injection Moulding. Not only do they require more complexity in the tool design, the resulting plastic part must work perfectly, with next to no warpage and align perfectly when assembled. It’s important that you get it right the first time, so in this article we’ll explore what you need to know […]
Here at Dienamics, we have been pushing carbon neutral practices through the use of multiple new technologies. It is our goal to become carbon neutral and we have invested time and money into new technologies and strategies in an effort to become more eco friendly. This year, we have invested in more solar panels for […]
Injection moulding is a versatile process and can be applied to almost any product. Although injection moulding is the industry standard for fabricating parts for products, it is not without its holdups. There are a few basic limitations to be taken into account. Here’s eight rules to follow when designing your product to ensure quality […]
How does a Regrinder work? A regrinder or plastic granulator is an electrically powered series of grinding blades, which takes plastic and chops them up into little pieces, commonly referred to as regrind. This regrind is a major step in any plastics recycling scheme. It takes what was reject or waste plastic and breaks it […]
Today, plastic injection moulding is responsible for the creation of products as varied as buttons and toys to state of the art computer touch screens and parts for aerospace products. A versatile and incredibly useful process, plastic injection moulding has paved the way for modern invention and design, and is something the world today could […]
Much of the success in designing a custom plastic injection-molded component comes from using the right material for the job. Both the intended use of the part and its design help determine the properties that its material should have for effective manufacture and use. As a result, at Southwest Plastics we frequently use specialized materials to achieve superior results for our clients. One such material is Delrin®, a high-performance acetal resin produced by DuPont.
Have you ever gotten an injection? A flu shot? A vaccine? Anaesthetic? If the answer is yes then it’s almost guaranteed that a plastic injection moulded syringe was used. With plastic manufacturing becoming more reliable after WW2, the use of plastics in consumables began to become common practice, and with this even more progress […]
Discover how overmoulding in injection moulding, product design, and industrial design can enhance your product development and user experience.
The Dienamics team has recently welcomed two new machines to the workshop! Both new machines offer excellent energy-saving capabilities and are a huge step in the right direction for Dienamics becoming a more environmentally friendly manufacturer. The machines are 90 tonne and 160 tonne. Tonnage, also known as clamping force, is the measurement which represents […]
Once your product has been designed, prototyped and you’ve ironed out any issues, it’s time to think about manufacturing. There are a few different techniques that could be used to manufacture your product. To decide which process is best for your product, think about: Market demand for your product Availability of resources The amount of […]
Today, plastic injection moulding is responsible for the creation of products as varied as buttons and toys to state of the art computer touch screens and parts for aerospace products. A versatile and incredibly useful process, plastic injection moulding has paved the way for modern invention and design, and is something the world today could […]
Injection moulding is a manufacturing method where plastics are shaped (or ‘moulded’) to form all kinds of objects that we use in our everyday lives. If you’ve ever sat on some plastic lawn furniture, unscrewed a plastic bottle cap or combed your hair with a plastic comb, then you’ve probably used an item that was […]
A sad fact of injection moulding and plastics manufacturing in general, is that plastic shrinks. And sometimes it shrinks a lot. So as plastic Injection moulders we’ve learnt to deal with shrinkage and today we are going to share a few of our tips and tricks to avoid excessive shrinkage and explain a bit about […]
Crack open almost any plastic shape and you will the internal volume is mostly air, and anything that actually does any work inside the part is reinforced by a strange pattern of thin little walls. Those little joining walls are called ribs, and they are one of the most important and powerful parts of any […]
How does a Sprue Picker work? A sprue picker is a piece of specialized machinery that picks the sprue out of an injection mould, usually as the parts are being ejected. The sprue picker can then drop the sprue to either the operator side or the far side of the injection moulding machine. Now let […]
Sink marks are a common manufacturing flaw found in injection moulded parts. Here is how to identify them, and avoid them.
The plastic injection moulding process is highly technical, and by no means an easy job. There’s a lot of room for expensive error, which can range from minor defects to major issues that could affect your product’s performance, desired design result, and safety.
It’s used to make everything from Gameboys to gears, and with the process standing as one of the best options for businesses developing products. There’s a myriad of benefits to swapping over to it today.
Southwest prides itself on white-glove customer service on every order, whether it’s a design prototype or a large production run. When it comes to quality, schedule, and price, we don’t believe in compromise—we’re dedicated to providing value, reliability, and service to all our customers. We also put the utmost emphasis on protecting your valuable intellectual property, ensuring that you retain control over your design and intellectual property rights. Based in Southern California, we can provide fast turnaround times, flexibility, dependability, quality, and reduced shipping costs that overseas manufacturers just can’t match.
Bosses are small cylindrical elements in a design. They are used for accepting screws or other fastening components (threaded inserts usually). Essentially they are locating, mounting and assembly devices built in to the design of the part and if not for accepting screws, will attach to the mating part of another component of the design. […]
The Dienamics team has recently welcomed two new machines to the workshop! Both new machines offer excellent energy-saving capabilities and are a huge step in the right direction for Dienamics becoming a more environmentally friendly manufacturer. The machines are 90 tonne and 160 tonne. Tonnage, also known as clamping force, is the measurement which represents […]
Flow Lines are a family of cosmetic flaws which can occur in injection moulded plastic parts. We would like to share our experience with you to aid you in spotting these flaws, and understanding how to avoid them The Flow Line family of visible marks can be defined as marks which make the route the […]
We’ve previously mentioned the importance of wall sections in our article about Ribs in Injection Moulding so in this article we’re going to go greater depths with that subject. We’ll talk about the basic process of injection moulding and how it relates to wall thickness, then outline some of the problems that may occur due to […]
Plastics are the common name for man made polymers. Chemically, these materials are made up of a single unit, the monomer, which will link up with millions of itself to form long chains. The length of these chains, if they have many branches, and how tightly they wrap together determine the physical properties of the […]
Whether you’re looking to re-shore your injection molding projects or simply need a highly skilled manufacturing partner to produce specialized parts to exacting standards, Southwest Plastics is your source for quality parts custom-made in America. For more information about Delrin® or to find out how Southwest Plastics can support your manufacturing needs, contact us here.
On top of that, you can use different types of plastic throughout your cycle. Plastic can be co-injected so that a machine can process two different plastic types in the same process!
Plastic injection moulding is by far the most popular method for producing mass manufactured plastic products – though if you’re new to the design and manufacturing game, here’s a quick recap. An injection moulding machine has a few main elements; a material feeder, called a ‘hopper,’ where plastic granules are poured; a heated barrel […]
Two highly effective and time-tested manufacturing techniques are Injection Moulding and Rotomoulding. Both techniques have their own distinct advantages and disadvantages and may or may not be suitable for your moulding requirements.
Most people would hear the term tool making and assume it is about making hammers, screwdrivers and spanners. In actual fact a toolmaker is a trade professional who builds Moulds, Dies and jigs. They are an essential part of product development and the manufacturing of plastic products. If you’re looking to get your product developed, […]
When you’re developing your product, the designer might come to you and say “I want to reduce the wall thickness in your part” even though you’ve said time and time again that you want a strong durable product. So why do designers push for thin walls? Let’s find out…
The modern human owes many of his or her daily conveniences to the technique known as plastic injection moulding. This manufacturing technique has been in use since the 19th century. Key steps Key steps in the plastic injection moulding process include clamping, injection and cooling: Clamping keeps the mould in place under heating and other […]
Flow Lines are a family of cosmetic flaws which can occur in injection moulded plastic parts. We would like to share our experience with you to aid you in spotting these flaws, and understanding how to avoid them The Flow Line family of visible marks can be defined as marks which make the route the […]
We use injection moulding when it comes to creating products in bulk. The reason for this is the sheer speed of production and the cost efficiency of the process, parts can usually be produced in seconds.
So, your design is done! Looking back over your masterpiece, do you notice any overhangs or what is more affectionately known in the injection moulding industry as “undercuts”? You may not realise that these little cliffhangers can have your design on edge, but why is this? In today’s blog, we discuss why you should try […]
For some, the cosmetic appearance of a part is the last thing on your mind. It might be that the part is being used internally, hidden from view, or the appearance is not a key point of sale for your part or product. But for many, the cosmetic appearance is of great importance, and something […]
Sink marks are a common manufacturing flaw found in injection moulded parts. Here is how to identify them, and avoid them.
Last week’s blog was all about Cold Runner Systems, this week, it’s time you learnt all about the alternate option – Hot Manifold Systems! To reiterate last week’s blog, the runner system is what controls the distribution of the plastic from the moulding machine’s nozzle to the tool cavities. If you haven’t already read it […]
Undercuts. No Plastic Injection Moulder wants them and every DIY part design has them. Undercuts, are part and parcel of what we do here at Dienamics. Most of our clients are looking to create or improve their own products, but are restrained to a strict budget. So, one of the first things we look for […]
Gas Assisted Injection Moulding is a highly technical form of injection Moulding, that uses both plastic and gas (usually nitrogen) to fill an injection mould under pressure. The main benefit of this manufacturing process is that it’s ability to form hollow parts in the cycle time of injection moulding machines. The basic process of Gas […]
Until recently, most third party inspectors have used a fixed-base Coordinate Measuring Machine (CMM) to inspect the accuracy of plastic injection-moulded refrigerator parts. 3D Engineering Solutions, an ISO 17025 certified third-party inspector, has since announced the successful use of new scanning technology that captures millions of data points during inspection rather than just hundreds. Rob […]
So, your design is done! Looking back over your masterpiece, do you notice any overhangs or what is more affectionately known in the injection moulding industry as “undercuts”? You may not realise that these little cliffhangers can have your design on edge, but why is this? In today’s blog, we discuss why you should try […]
Most people are not aware of what plastic injection machinery is. In terms of product design, all of us are surrounded by plastic objects made with plastic injection machines – such as water bottles, telephone handsets, CD covers, dust bins, electric outlets and a lot more. Did you ever realize that these commonly used items […]
A new paper by The Linde Group has revealed that carbon dioxide (CO2) can be used to cut cooling cycles and overall production cycles in injection moulding. The white paper is concerned with the manufacturing technique of gas assist injection moulding, which traditionally uses nitrogen as the gas of choice. However, the paper revealed that […]
For those of you who want to know a little more about plastic injection moulding, this article will attempt to explain, in layman’s terms, exactly what this means. Basically, injection moulding is a process that was first designed in the 1930s. Up until then die casting, or the process by which metals are cast from […]
How does an Injection Moulding Press work? An Injection Moulding Press or Injection Moulding machine is a rather complicated, fully automated piece of machinery. An injection moulding machine makes moulded plastic parts quickly and with a high degree of repeatability. The plastic parts can be made from a range of different plastics for different purposes. […]
As a combination of the availability of customisation options and the ease of customisation in the process itself, there’s a lot you can do with injection moulding to mix up your project.
In the world of manufacturing, the precision and quality of your products are paramount. At the heart of manufacturing, especially in industries relying on plastic components, lies the process of injection moulding. This method generally uses multiple moulds that come together and close to form a “cavity” that is the shape of the manufactured product. […]
As part of the moulding process, you can add fillers or additives to the moulded part via plastic injection process in order to create reinforced and stronger products, an option that most other processes lack.
GETTING A QUOTE WITH LK-MOULD IS FREE AND SIMPLE.
FIND MORE OF OUR SERVICES:
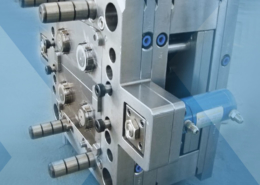
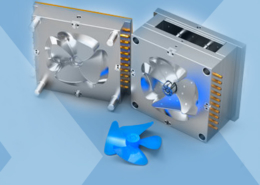
Plastic Molding

Rapid Prototyping
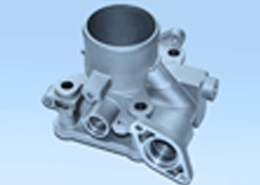
Pressure Die Casting
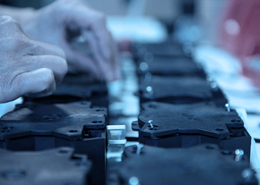
Parts Assembly
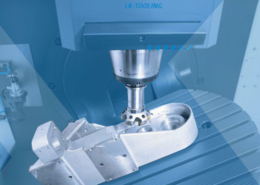