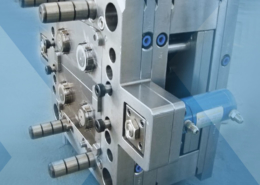
Aerospace Plastic Injection Molding Solutions - aerospace plastic injection mold
Author:gly Date: 2024-10-15
Have you ever wondered how intricate and complex features are seamlessly molded into plastic parts? The answer lies in the fascinating world of injection mold slides. These specialized components are the unsung heroes behind creating undercuts, threads, and other intricate details in molded parts.
Conversely, too fast, and the plastic might create stress within the mold, leading to warping or other surface imperfections. Furthermore, the speed must be adjusted based on the material used, as different plastics have varying flow properties and cooling rates.
The cooling time must be accurately calculated and controlled, as too short a time might lead to parts being ejected prematurely, causing deformation or warping.
Based on the part design, decide on the type of slide needed. The choice of slide type depends on the specific feature to be created, such as undercuts or threads. Additionally, determine the number of slides required, which will depend on the complexity of the part and the number of features to be produced.
Conversely, excessively long cooling times can reduce the overall efficiency of the production process and increase cycle times. The cooling process’s effectiveness also hinges on the mold temperature and the thermal properties of the plastic material used, necessitating precise control systems to regulate and monitor these parameters.
Understanding these mechanisms is vital for achieving efficient and reliable injection molding processes. Each component plays a unique role in ensuring the successful production of high-quality molded parts.
The world of injection molding is rapidly evolving, with advancements in parameter control techniques playing a pivotal role. These developments not only enhance the capabilities and efficiency of the injection molding process but also pave the way for innovative product designs and sustainable practices.
In the meticulously timed process of injection molding, cooling time is a critical factor that significantly influences the dimensional stability and quality of the final product. This phase allows the molten plastic within the mold to cool and solidify into its intended shape.
Optimize your slide design for ease of manufacturing, assembly, and maintenance. This optimization reduces costs and minimizes downtime. Remember the specific manufacturing process and equipment available during the design phase.
Specialize in CNC machining, 3D printing, urethane casting, rapid tooling, injection molding, metal casting, sheet metal and extrusion
The field of injection molding is continually evolving, with advanced techniques emerging for enhanced parameter control. These advancements significantly improve product quality, process efficiency, and the ability to handle complex designs.
While designing slides for injection molds, it’s essential to be mindful of common pitfalls that can hinder the production of high-quality parts. By avoiding these mistakes, you’ll enhance the efficiency and effectiveness of your slide mold design. Let’s delve into these common errors in more detail:
Cycle time in injection molding encapsulates the total time required to complete a full cycle of the process, encompassing injection, cooling, and mold opening stages. For a small and simple part, the cycle time might be as low as 30 seconds.
Injection molding, a cornerstone in the world of modern manufacturing, involves nuanced parameters that dictate its efficiency and quality. This guide dives deep into understanding and mastering these critical parameters.
Speaking of which, understanding the different slide actions and components of injection mold slides is essential for achieving precision and consistency in the injection molding process. In this article, we will delve into the inner workings of an injection mold slide, unfolding its importance and explaining how to design it effectively.
Factors such as the complexity of the part design, the material used, and the specific process parameters like injection speed, pressure, and temperature settings all interact to determine the feasible cycle time.
The recovery rate in injection molding refers to the speed at which the screw draws new material into the barrel after each injection cycle. This rate impacts the cycle time and the efficiency of the production process. A faster recovery rate can increase production speed but may require careful balancing to avoid material degradation.
Material Selection: Consider the material you plan to mold. Injection molding slides are not typically employed for softer materials, as they may lead to issues like sticking and uneven cooling.
Optimizing injection molding parameters is pivotal for ensuring the highest quality in production. The process’s complexity requires a nuanced approach, balancing various factors to achieve optimal results. Here, we discuss strategies for parameter optimization, providing actionable insights and real-life examples.
Incorporate draft angles into the slide mold design. Draft angles are essential to prevent damage to the part during ejection. Be sure to consider both the draft angle of the part and the slide in your design.
Wear plates are designed to minimize friction and wear between moving parts of the slider system. They help extend the lifespan of the components and ensure smooth operation.
In the sophisticated process of injection molding, the parameter of speed is not to be underestimated. Injection speed refers to the rate at which the molten plastic is introduced into the mold. This aspect of the process plays a critical role in determining the quality and efficiency of the final product.
The injection speed is a dynamic parameter that can greatly influence the characteristics of the final part. In the intricate dance of the injection molding process, the speed at which plastic enters the mold impacts everything from the material’s flow performance to the product’s surface quality. For a medium-sized part, a typical injection speed might range from 50-100 mm/s.
The typical injection molding pressure ranges from 500 to 1500 bar, varying based on material and part complexity. For example, more viscous materials require higher pressures for effective molding, while intricate designs demand precise pressure control to fill molds properly and prevent defects.
Begin by reviewing the part design to identify features that necessitate the use of slide molds. These features could include undercuts, threads, or other complex shapes. The part design will determine the type and number of slides required.
For many applications, the injection pressure might be around 500 to 1500 bar. The correct setting of injection pressure is key to achieving optimal surface quality and dimensional accuracy of the injection molded parts. It also plays a significant role in the distribution of materials within the mold cavity, impacting the final strength and properties of the product.
Looking ahead, the injection molding industry is poised to witness several transformative trends, significantly influencing how parameter control is approached.
Part Size: Evaluate the size of the part you intend to produce. Sliders are typically best suited for smaller parts as they require the mold to open and close for the slider to function effectively.
Screw speed in injection molding is the rate at which the screw rotates to mix and inject the molten plastic. This speed affects the quality of the mix and the consistency of the injection. Proper adjustment of screw speed is vital for optimal material homogenization and to avoid issues like material degradation or air entrapment.
In cases where inserts are used, the guide pin prevents their displacement. To ensure proper functionality, the guide pin should be positioned between 15 and 25 mm above the product. Furthermore, the slider guide pin, located 10 to 15 mm below the mold guide pin, guides the movement of the slide.
The guide block, sometimes called a slider, complements the guide pin’s function. Working together, they facilitate both vertical and horizontal motion within the system.
This parameter is a critical measure of the efficiency of the injection molding production process. Shorter cycle times translate to higher production speeds and increased output, which are vital in high-volume manufacturing scenarios.
If you’re unsure if injection mold slides are the optimal choice for your specific application, you can consider several key factors, including:
Proper management of holding pressure is essential for minimizing defects like sink marks and ensuring consistent part weight and dimensions. This pressure helps maintain the integrity of the product during the crucial stage of cooling and solidification, ensuring that the final product meets the desired quality standards.
Thus, back pressure is not just a step in the process; it is a significant contributor to the molding process’s overall efficiency and the quality of the injection molded products.
Temperature regulation in injection molding is a balancing act of precision and control, vital for achieving optimal product characteristics. It encompasses several elements, each playing a pivotal role in the molding cycle.
This uniformity is essential for achieving the desired surface quality and mechanical properties in the final product. Moreover, appropriate back pressure helps in reducing the presence of air and other volatiles in the melt, which can otherwise lead to defects in the molded parts.
Selecting the wrong materials for your slides can be a costly mistake. The chosen material should be compatible with the mold material and the specific molding process.
Include interlocking features in your slide design to prevent any undesired movement during the molding process. These interlocking features help maintain the integrity of the slides and ensure accurate part production.
Injection molding stands as a pivotal manufacturing process used extensively in producing complex and varied plastic parts. This technique involves melting metal or plastic pellets and injecting the molten plastic into a mold cavity, where it cools and solidifies into the desired shape. Its versatility in handling a range of materials and complexities makes it a preferred choice in industries from automotive to consumer goods.
The selection of materials in injection molding significantly impacts the setting of process parameters. Each material has unique properties that necessitate specific parameter adjustments for optimal production quality.
Choose the appropriate material for the slides. It’s essential to select a material that is compatible with both the mold material and the specific molding process. Common materials for slides include tool steel, aluminum, and beryllium copper.
Nozzle pressure in injection molding is the force exerted by the machine to push molten plastic through the nozzle into the mold. This parameter is critical for ensuring the material fills the mold cavity effectively, influencing the quality of the final product. Optimal nozzle pressure varies depending on the material’s viscosity and the design of the part being molded.
This parameter impacts factors such as cooling time, dimensional stability, and surface finish. A well-regulated mold temperature ensures reduced stress and shrinkage, contributing to the overall product quality and durability.
Designing an effective injection molding slider is a crucial part of the mold creation process. These slides play a pivotal role in enabling the production of complex parts with undercuts, threads, and intricate features. To help you navigate this process, here’s a step-by-step guide for designing an injection slide mold:
The slide body is an integral part of the slide system, housing the components necessary for the sliding mechanism. It provides structural support and ensures the coordinated movement of other components.
Accurately calculate the dimensions of the slides. These dimensions ensure proper movement and clearance within the mold cavity. The calculations will be influenced by the part design and the type and number of slides used.
The choice of guide pin type depends on the product and mold’s specific requirements. Two key differences in guide pin types are their height above the slide and the lock mechanisms. Let’s explore these types:
In injection molding, slides play a pivotal role in achieving what might seem impossible – producing complex parts without needing multiple molding steps. They move in and out of the mold cavity precisely, coordinating the formation of the desired shape.
Different plastics respond distinctively to parameter changes, making it essential to understand their characteristics for optimal parameter settings.
In the realm of injection molding, certain challenges frequently arise when setting parameters. These challenges can impact product quality and process efficiency.
In the intricate world of injection molding, pressure stands as a cornerstone parameter, deeply influencing every aspect of the molding cycle. From the way molten plastic flows into the mold to the final structural integrity and surface quality of the product, understanding the different types of pressures and their roles is crucial.
The minimum precision in injection molding typically lies between ±0.005 inches (±0.127 mm) to ±0.010 inches (±0.254 mm), depending on machine capabilities and material characteristics. High-grade machines and stable materials can achieve tighter tolerances, essential for precision components.
This temperature needs to be precisely controlled to ensure smooth flow and complete filling of the mold cavity, directly influencing the injection molding techniques and the quality of injection molded products. Improper melt temperature can lead to issues like poor surface quality, inadequate strength, or warping in the final product.
The guide pin is a critical element of the slide mold. It is used to locate the core and side of the mold cavity, facilitating smooth and easy movement within the mold system. Additionally, the guide pin plays a crucial role in supporting the weight of the mold.
Melt temperature, the heat at which the polymer becomes fluid enough for injection, is crucial for the process’s success. For instance, ABS plastic typically requires a melt temperature ranging from 210°C to 270°C.
These factors collectively influence the melting, flow performance, and solidification of the plastic. Advanced control systems are employed to monitor and adjust these temperatures, ensuring a stable and efficient molding process.
Shrinkage rate is the percentage of reduction in size a plastic part undergoes as it cools and solidifies in the mold. This parameter is crucial for achieving dimensional accuracy in the final product. Factors like material type, mold temperature, and cooling time significantly influence the shrinkage rate.
As the industry continues to embrace these advancements, we can expect to see a significant impact on production quality, environmental sustainability, and the overall landscape of manufacturing.
For instance, in the case of a simple, thin-walled plastic part, the cooling time might typically range from 10-30 seconds. This duration is vital to ensure that the part has solidified enough to maintain its shape upon ejection from the mold.
The guide block exerts a force on the guide pin, ensuring it remains in place even under high mold pressure. Additionally, the guide block guides the motion of the guide pin, allowing for precise and controlled movement.
Simplicity is often the key to successful slide design. Creating overly complex slides can result in difficulties during manufacturing, assembly, and maintenance. Complex designs may also increase costs and lead to unnecessary downtime. To avoid this mistake, prioritize straightforward and effective slide designs that align with the specific features required for your parts.
Injection pressure, the force exerted to push the molten plastic into the mold cavity, is a vital factor in the injection molding process. This pressure needs to be high enough to ensure a good flow of the material, filling the mold completely and accurately.
Clamping force is the pressure used to hold the mold closed during the injection and cooling stages. Adequate clamping force is essential to prevent mold opening due to internal pressure, ensuring the production of defect-free parts. The required clamping force depends on the projected area of the part and the injection pressure.
However, optimizing the cycle time requires a delicate balance. While reducing cycle time can lead to higher productivity, it should not come at the cost of product quality.
Understanding and optimizing these parameters is not just a technical necessity but also a strategic advantage in the competitive manufacturing landscape.
Too slow, and the material may start solidifying before the mold is completely filled, leading to defects and poor structural integrity.
Are you confused about how an injection mold slide differs from a lifter? Let’s delve further into the specific differences between mold lifters and sliders to gain a comprehensive understanding of their unique applications and mechanical mechanisms.
Troubleshooting parameter issues in injection molding is essential for maintaining efficiency and product quality. Here is a step-by-step guide to identifying and solving common parameter-related problems.
Failure to include interlocking features in your slide design can lead to unwanted movement during the molding process. These features are very important for keeping the slides stable and in place, especially when they are under pressure. Incorporating interlocking mechanisms ensures that the slides function as intended, preventing errors and defects in the final parts.
One of the most fundamental errors is failing to account for the draft angle of both the part and the slide. The draft angle is crucial in preventing damage to the part during ejection. Without adequate draft angles, parts may get stuck or damaged during the release process. Always consider and incorporate appropriate draft angles into your slide design.
Temperature control in injection molding is not just about reaching the right temperature but maintaining it consistently throughout the production process. It encompasses the management of barrel temperature, nozzle temperature, and the temperature of the mold.
Production Volume: Think about the production volume of your part. Sliders can experience wear and tear, especially during long production runs, and incur significant costs. For larger products, it may be prudent to maintain spare sliders to mitigate the impact of wear and tear on your production schedule.
The slide mold system comprises several key components, each serving a specific purpose in the injection molding process:
The mold temperature, another key parameter, significantly affects the cooling process and final properties of the molded part. For materials like polycarbonate, the mold temperature usually ranges between 80°C and 120°C.
Nave ISK-8, Parque Industrial y Logístico Sky Plus, Avenida Mineral de Cinco Señores No.100, del Parque Industrial Santa Fe, Silao de la Victoria, Guanajuato, México
The heart of injection molding’s success lies in its parameters. Each aspect, from injection pressure to mold temperature, plays a vital role in determining the quality and efficiency of the end product. Precision in these parameters ensures reduced defects, enhanced strength, and consistency in production.
Once the mold is filled, holding pressure comes into play. This is a lower pressure applied to the molten plastic to pack the material into the mold and compensate for any material shrinkage during cooling. Typically, holding pressure can be approximately 50-65% of the injection pressure.
Using incompatible materials may lead to premature wear and tear of the slides, reducing their lifespan and impacting part quality. Common materials for slides include durable options like tool steel, aluminum, and beryllium copper. Make an informed choice based on your project’s requirements.
Injection molding parameters are the critical factors that influence the quality and efficiency of the molding process. They include:
Mold locking pressure is the force applied to keep the mold closed during the injection process. This pressure must be sufficient to counteract the force of the injected material, preventing mold flash and ensuring the integrity of the molded part. It is adjusted based on the size and complexity of the mold, as well as the injection pressure used.
Therefore, achieving an optimal cycle time is a result of meticulously balancing these various factors to ensure both efficiency and quality in the injection molding process.
Back pressure in injection molding refers to the pressure applied during the retraction of the screw in the injection molding machine. This pressure is crucial for homogenizing the plastic melt, ensuring consistent quality across production cycles.
The press block plays a role in exerting the necessary pressure and force for the proper functioning of the slider. It works in tandem with other components to facilitate the slide’s motion.
Typically, a common back pressure setting might be in the range of 5-20 bar. The application of back pressure aids in the proper mixing and melting of the polymer materials, leading to an even distribution of pigments, fillers, and other additives.
GETTING A QUOTE WITH LK-MOULD IS FREE AND SIMPLE.
FIND MORE OF OUR SERVICES:
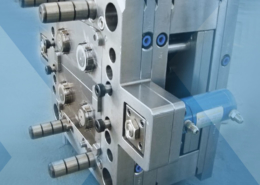
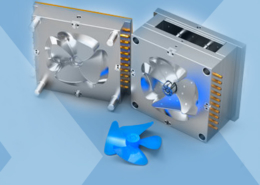
Plastic Molding

Rapid Prototyping
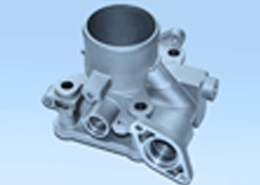
Pressure Die Casting
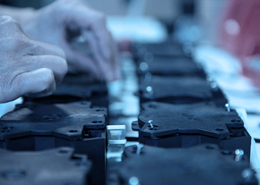
Parts Assembly
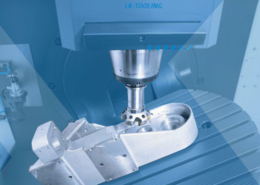