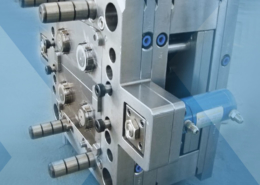
Advantages And Disadvantages of Two-shot Injection ... - multi shot injection mo
Author:gly Date: 2024-10-15
The design and manufacture of custom molded plastic parts can seem simple at first, but there are many details that must be taken into consideration depending on how the part will be used. For example, there are mechanical properties like:
Before deciding on injection molding for your manufacturing process, it’s essential to consider a few key factors, including:
Our knowledgeable team can help you determine the best plastic materials and process for your specific application and unique needs.
Manufacturers typically turn to the plastic injection molding process to produce a large volume of a particular part, for several main reasons:
For injection molding, it’s prudent to minimize cycle time as much as possible. The more time you can cut from the cycle, the more money you’ll save.
We address the most important design concerns for injection molding projects above, in the Important Factors to Consider for Injection Molding section. Below are more helpful guidelines:
Use cases for injection molding vary widely; it can be used to manufacture molds and parts from tiny components to large automotive parts.
If a part is to be produced by injection molding, this must be considered in its design — this includes simplifying its geometry and number of components as much as possible. The mold should be designed with a goal of minimizing the risk of defects during the production process.
Unsure if your part is suited for the injection molding process? Our experienced engineers are happy to answer any questions you have and will work with you to determine if plastic injection molding is right for your project.
As a leading small plastic parts manufacturer, we work with engineering grade plastics to create custom molded plastic parts that match the requirements for a part with properties like: chemical resistance, flexural strength, durometer, and yield strength to name a few. There are so many material options, and we can help you make the right choice for your program.
Simplifying production times often comes down to finding ways that can reduce the number of steps or tooling changes during the injection molding process. This could involve combining parts into a single section or reducing gate locations on the product.
Aero-Plastics specializes in injection molding projects such as insert molding and other value-added services. We offer injection molding PEEK, Ultem and other high-performance engineered resins, plus commodity resins such as polypropylene, polyethylene, polystyrene, ABS, and nylons.
Designs that are well-suited for plastic injection molding should ideally have a uniform wall thickness, as well as avoid sharp corners, undercuts, and other features that could increase manufacturing time or, in some cases, require additional molding processes for an individual injection molded part.
Aero-Plastics offers injection molding services for a variety of applications including medical, consumer goods, industrial equipment, automotive components and more. We have the capabilities to provide you with a custom solution that meets your needs.
The most common polymers and thermoplastics used for injection molding are acrylonitrile butadiene styrene, polyethylene, polycarbonate, polyamide (nylon), high impact polystyrene, and polypropylene.
Use cases for injection molding vary widely; it can be used to manufacture molds and parts from tiny components to large automotive parts.
While injection molding has a significant up-front cost, it quickly turns into one of the most cost-effective methods of manufacturing parts.
Injection molded products may be better suited for some projects over others, and understanding more about the plastic injection molding process can help you make an informed decision.
At Aero-Plastics, we strive to provide the highest quality plastic injection molding with the following tolerance objectives, which relate directly to the material to be molded.
Our team of experts will assess physical factors that can influence tolerances, namely the material being used as well as the size and shape of the part being manufactured.
We want you to achieve the best value possible — so our experts work with you on these tolerance objectives. Over-specified tolerances can increase project costs, and we understand how to minimize them without sacrificing product quality.
While cheaper methods make for a quicker time to market, custom injection molding takes more care with part design, material selection, mold design, and process control in order to achieve more consistent and accurate end products.
We use a Design for Manufacture process to align your project goal to our manufacturing methods. This process allows us to evaluate the design of a part and molding process before production begins – which ensures that we can successfully meet your requirements and attain part quality.
Injection molding is a manufacturing method in which molten material – commonly a thermoplastic or polymer – is injected into a mold in order to produce a part.
Our mantra — “Driven by Dependability” — is founded on our adherence to our quality system, and remains the leading reason our customers keep coming back.
MIM allows us to produce intricate parts in a wide range of metals, including steel, stainless steel, and high-temperature alloys.
After setup costs are paid off, the price per unit of products manufactured via injection modeling drops steeply and remains extremely low. The more parts produced, the lower the individual cost, making plastic injection molding especially suitable for high volume production.
As veterans in high-performance polymers and engineered resins, you can rely on us to provide expert guidance on materials. All of our tooling is built to Class 103, 102, and 101 industry standards.
The more complex a part’s geometry is, the higher the tolerance objective has to be in order to maintain quality and consistency. Complex features with tight tolerances may require substantial design revisions or additional tooling.
Injection molding is a perfect solution for scaling large volume or mass production due to the simplicity and consistency of the process. Standardized injection molds allow manufacturers to dial in the specific requirements of their product and reproduce them quickly and accurately.
The high injection pressure means that the molten material fills all of the mold’s cavities and forms a solid part. Through the cooling process, it hardens to the shape of the cavity, creating the desired product.
For tight tolerance parts, we can combine molding with post-mold machining operations. We’re on the Boeing QPL for all types and classes of molded parts, and an approved molder on the D1-4426 for BAC 5321 class II injection molded parts.
Toggle clamping uses the injection unit to melt the material, then inject it into a mold. In a process called metering, a screw then rotates to gather melted material from the hopper, until enough is accumulated to begin the injection process. The injection molding machine controls the injection speed via the rotation of the screw.
Larger parts require a larger tool set and will have greater variation in wall thickness, which can often create an increase in available tolerances.
The clamping unit of injection molding machines is used to open and close a die in the machine, and to eject the final product.
It also helps to keep assembly simple – the more parts required in the setup, the higher the cost, so it’s often beneficial to keep injection molded parts as self-contained as possible.
“We received the charger base and I want you all to know it looks FANTASTIC! Thank you for getting us this one for the BOD meeting.”
It is then injected under enormous pressure into a steel or aluminum mold, cooled until it hardens, and ejected. With small part injection molding, we are able to manufacture complex, small shapes in a cost-effective, repeatable process.
Injection mold production requires a significant up-front cost, in order to prepare the mold and manufacturing setup. However, this subsequently ensures a low production cost after that initial investment is paid off.
At Aero-Plastics, we specialize in producing high-quality parts with tight tolerances, thanks to our team of experienced engineers and detail-oriented processes.
A straight-hydraulic injection molding machine uses a hydraulic cylinder to open and close the mold, and then inject plastic through a nozzle in the machine. This type of injection molding machine produces parts with high repeatability and accuracy.
When the part is ejected, it can be post-processed if needed (e.g., painting, finishing) before being shipped out for use.
Injection molding tolerances, listed below, are directly related to the material to be molded; part size and part geometry. We review parts and tolerances on a case-by-case basis during quoting, and use a Design for Manufacture process to align your project goal to our manufacturing methods.
Yes. Injection molding can be used to manufacture metal parts, by a process called metal injection molding (MIM), in which metal powder is mixed with plastic and molded. The plastic is subsequently removed, and the remaining part sintered.
A heated barrel mixes the desired material and injects it into a mold cavity. Through the cooling process, it hardens to the shape of the cavity, creating the desired product. Molds are usually designed by an engineer or industrial designer, who then further refines the mold with precision machining.
The plastic injection molding process begins with the melting of raw material in a heated barrel, used to mix the desired material prior to injection.
Before selecting plastic injection molding as your production method, it’s important to first determine how many parts need to be produced in order to make the process (and initial investment) cost-effective. You may do this by figuring out how many parts it will take to break even on the project, and building in a conservative margin.
Discover AIM Processing's customer small part injection molding services, designed to deliver precise, high-quality components for industries requiring intricate and complex plastic parts.
Depending on your application, certain materials may be more suitable than others. For example, if you need a high-strength but flexible material to fill your mold tool, thermoplastic materials like ABS might be best. High-density polyethylene, on the other hand, features a high chemical resistance, making it suitable for products or components that will be exposed to moisture or chemicals.
The molds used for injection molding offer one of the strongest guarantees that parts will match the original. This lends to brand-consistent quality and part reliability and reduces the amount of plastic material waste.
Our team is sure to review parts and tolerances on a case-by-case basis for all plastic injection molding quotes to ensure that we can deliver on all objections and achieve optimal part quality.
Your project’s level of complexity is what determines the level of “customization” it requires — in other words, the level of engineering and design support required, analysis needed, and number of process technologies required.
Then there are factors like the manufacturability of gate locations, draft, and ejector pins. It's enough to make your head spin.
This molten plastic is then injected at high pressure into a mold cavity and cooled to form the desired shape. Molds are usually designed by an engineer or industrial designer, who then further refines the mold with precision machining.
AIM Processing specializes in small part plastic injection molding. We define "small plastic parts" as roughly the size of your fingernail to the size of your hand. Injection molding is a process in which plastic resin, in pellet form, is heated and sheared until it reaches a viscous state.
GETTING A QUOTE WITH LK-MOULD IS FREE AND SIMPLE.
FIND MORE OF OUR SERVICES:
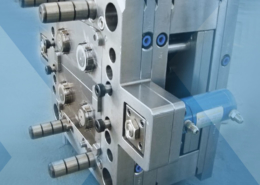
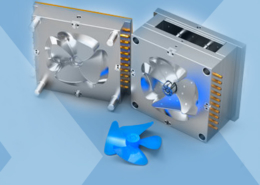
Plastic Molding

Rapid Prototyping
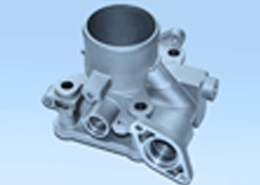
Pressure Die Casting
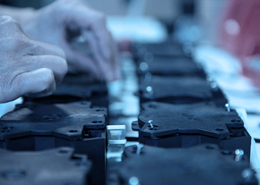
Parts Assembly
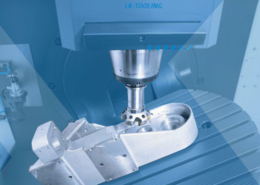