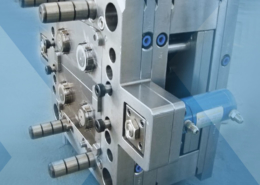
Advanced Injection Molding, LLC - advanced plastic molding inc
Author:gly Date: 2024-10-15
Before learning the components of injection molds, it’s essential to briefly familiarize ourselves with three types of molds, as parts of the injection mold we discuss today belong to different categories. I’ve previously mentioned these three types of molds, categorized based on their gating system’s basic structure: the two-plate mold; the three-plate mold; and the hot runner mold
Components used in mold design primarily to address issues with internal undercuts in the product. The working principle of a lifter is based on its draft angle, facilitating the opening and closing of the mold. Its main function is to assist in the smooth ejection of the mold.
Refer to components that are embedded within the mold, which can come in various irregular shapes such as square, round, or flat.
Warning Notice to Commercial Lure Manufacturers: On February 19, 2002, Gary Yamamoto Custom Baits, Inc obtained a U.S. Trademark registration for the name “SENKO”. Any use of this name in whole or in part or sufficiently similar name used for commercial on non-commercial purposes, without the written consent of Gary Yamamoto Custom Baits, Inc is a potential trademark infringement. Trademark infringements involve the potential for significant civil damages, including in particular cases, statutory damages, liability for up to three times actual damages and attorney’s fees.
These are larger diameter, cylindrical parts fixed to the mold. They serve as the guiding elements that direct the movement.
It heats the plastic in the channels through internal or external heating methods to ensure the melt remains fluid during flow. Internal heating is achieved by installing heating rods within the channels, while external heating involves drilling heating holes on the outside of the channels, into which heating rods are inserted or heating rings are installed for heating.
The two-plate mold features a typical structure as shown below. It is the simplest and most widely used type of injection mold, divided into the mold core and mold cavity by the parting line.
Tackle Warehouse wants you to be completely satisfied with your purchase. Items can be returned at any point in new condition within 365-days of the original invoice date.
The mold interior is usually divided into multiple channels through which the circulating cooling water is delivered. This can lower the mold temperature. During production, the flow rate and temperature of the circulating cooling water can be adjusted using a flow controller.
Specifically, during injection, when the injection material fills the cavity, a robot or other device presses the return pin downward. At this point, the A plate and B plate begin to separate, and the injection-molded product is ejected from the mold. Then, as the injection-molded product is being transported, the return pin resets the B plate back to its original position.
Comments: spray paint high temp motor gloss paint on the molds soft plastic's turn out way cleaner use rubbing alcohol and clean the molds first
Over the years, the mold base manufacturing industry has matured significantly. Mold manufacturers can either purchase custom-made mold bases tailored to specific mold requirements or opt for standardized mold base products. The variety of standard mold base designs, shorter delivery times, and even immediate availability offer mold manufacturers greater flexibility. As a result, the popularity of standard mold bases continues to rise.
Comments: Theses mold are made for the hobbyists, priced right and free shipping (when was the last time anyone bought under $50 from here, come on) being that these mold are sand cast and not milled the baits come out with a "dull" sheen but that doesn't effect the fish Catching at all. Do it molds hit a home run with theses for sure
Comments: I bought the 3.8" wave worm mold less than a month ago. First off I love the flat worm. It flat out catches fish! With me living on a budget, I thought this would be more cost effective. I love the concept of the mold and the bait. But in 3 weeks time I have yet to shoot all 9 cavities and have all of them come out without some sort of defect. (Mostly air bubbles and dents.) It's actually quicker to hand poor this mold. The quality is better than injection. Kinda disappointed in this mold.
The main components of an injection mold system include the mold base structure, the molding system, the feed system, the ejection system, the cooling system, the venting system, and the guiding structure.
In mold designs with layouts such as 2×4, 2×5, or other multiple configurations, several sub-runners are designed to further divide the flow of molten plastic.
Comments: Bought this over a month ago, although I do not use it often Its a great product! You do need an injector & to clamp the mold together so molten plastic does not spill but when done right you make great worms!
In previous articles, We explored “What is an Injection Mold” and got a basic understanding of its components. However, the structure of injection molds is indeed complex. Today, let’s delve deeper into the structure and components of injection molds.
A typical configuration of a mold base includes the clamp plate, A plate, B plate, C plate (spacer block), rear clamp plate, ejector retainer plate, and ejector plate, among other components.
Generally, structures capable of venting can also allow air intake. Methods of venting include parting line vents, vent grooves, insert venting, ejector pin venting, venting pins, sintered metal venting, and vent plugs, among others.
The molding system is the soul of a mold, responsible for giving shape and size to the molded plastic parts. Since the molding system controls the precision of the final parts, it is the part of the mold manufacturing process that requires the most time and effort.
Please note that while we want you to be happy with your purchases, an excessive number of returns within a twelve-month period may limit your eligibility for refund or store credit.
*Price comparisons are based on the Manufacturer's Suggested Retail Price ("MSRP") or Original Selling Price. Actual sales may not have occurred at this price.**Price matching restrictions vary by brands. Contact us for details.
Now, let’s formally examine the components of a mold. I will outline the names and functions of these mold parts. For some parts that require special attention, I will write separate articles to explain them in detail in the future.
Return Pins (Reset Rods) are primarily used to control the opening and closing movement of the mold, providing positioning and support when releasing the mold structure during injection.
These are suitable for ring-shaped, cylindrical, or products with a central hole. Ejection with sleeves involves full circumferential contact, leading to evenly distributed force that does not deform the product or leave noticeable ejection marks, thus improving the concentricity of the product. However, they should be avoided for products with thin peripheral walls to prevent processing difficulties and weakening of the product strength.
The primary functions of mold inserts include fixing the plates, filling the space between plates, reducing the height of the mold core to save material, facilitating mold modifications and maintenance, improving the mold’s venting effect, aiding in machining complex deep bone positions, and extending the mold’s lifespan. Inserts are usually made from copper, other metal materials, or plastic. In mold design, it’s essential to consider precise positioning methods for inserts, such as holes, pins, etc.
The water line is the core part of the cooling system. It refers to the system that injects circulating cooling water from the injection molding machine into the mold to control the mold temperature. This ensures the quality of the plastic parts and enhances production efficiency.
The Cold Slug Well, also known as the cold slug hole, is a feature in plastic injection molding molds. Its primary function is to store the initial cold material produced during the injection intervals. The purpose of this design is to prevent cold material from entering the cavity, which could affect the quality of the molded parts, and to ensure the molten material smoothly fills the cavity.
The hot runner mold combines the simplicity of two-plate mold actions with the advantage of the three-plate mold’s ability to inject molten material from any point within the cavity. Moreover, the hot runner mold eliminates the loss of pressure, temperature, and time of the molten material in the runner, thus enhancing the mold’s quality and reducing the molding cycle. It represents a significant innovation in injection mold gating system technology.
Its role is to secure the mold cavity. In some cases, high-quality materials are directly used to form the molding part.
Both the mold cavity and the mold core are indispensable parts of the mold, working together to achieve optimal processing results. During use, it’s crucial that the mold cavity and core closely cooperate to ensure the mold’s structure is robust, the pressure is balanced, and the molding precision is high, which also contributes to extending the mold’s lifespan.
Offering the very best in quality and design Do-it’s Soft Plastic Molds give anglers the ability to produce their very own customized soft plastics, over-and-over again. Molded from bar stock aluminum, each model of the Do-it Soft Plastic Mold has been rigorously researched and developed before it is available to the public, so you can rest assured that you have the very best the industry has to offer. Designed to work hand-in-hand with Do-it’s premium lineup of Soft Plastic Plastic Injectors, and Accessories, the Do-it Soft Plastic Molds are a must-have for the angler looking to pour their own.
The productivity of a single-cavity injection mold is often determined by the cooling time of the sprue. Besides providing adequate cooling for the sprue bushing, the minimum diameter of the inlet on the sprue bushing should be as small as possible while still being able to timely fill the cavity.
The guide injection mold components are critical in ensuring that the mold core opens and closes accurately along the designed path. The guiding system typically consists of guide pillars (guide pins) and guide bushings.
Free return shipping is available for all orders shipped within the 48 contiguous United States. These orders will include a complimentary pre-paid UPS Ground return label in the box when the order is delivered. If you use the pre-paid return label provided, please allow 7-10 business days for the return package to arrive back at Tackle Warehouse.
Products returned in new, store-bought condition are eligible for exchange, refund, or Tackle Warehouse store credit for the full value of your purchase.
Please use our Returns & Exchange form found on the back of your printed invoice. If you don't have your original invoice you can download our Tackle Warehouse Return Form.
Located in the rear half of the mold, is movable. It corresponds to the mold cavity and supports positions, and moves the mold, bearing certain pressures during the process. The mold core tends to have a more complex structure.
After passing through the sprue, the molten plastic enters the runner and is then dispersed into multiple channels, allowing the simultaneous molding of different parts.
The interaction between guide pillars and guide bushings creates a guiding channel. Through this channel, parts of the mold can maintain stable positioning during the injection molding process. The design of the guiding system must take into account the structure of the mold and the mechanical properties experienced during injection molding. The size, shape, and material selection of these components need to be carefully designed based on the specific requirements of the mold.
Ejector pins are the simplest and most common form of ejection mechanism within an ejection system. Due to their ease of manufacturing, fitting, and effective ejection results, they are widely used in production. However, the round ejection surface area is relatively small, which can lead to stress concentration, puncturing the product, and product deformation.
The gate is the endpoint for the molten plastic, from which it enters the mold cavity. The design of the gate is a significant area of expertise within mold design and is a focus in the field. We will discuss the various types of gates in detail later.
I am Young Lee. If you’re interested in the structure of injection molds or our mold manufacturing services, feel free to click on “injection mold making services” or “injection mold quote” for more information.
Products returned beyond 365-days from the original invoice date or that are unable to be returned to stock may be eligible for store credit at the sole discretion of Tackle Warehouse.
The design of the lifter is related to the stroke of the ejector plate, and its movement is primarily driven by the motion of the ejector plate. A mold lifter can be a line inclined from the vertical direction or an inclined plane. When the inner walls of the plastic product are thin, directly ejecting the product might damage it or cause difficulties in resetting. However, Lifters can prevent these issues.
The feeding system of an injection mold primarily transports the plastic melt from the nozzle of the injection molding machine to each cavity. Its components mainly include the Sprue, Runners, Sub-Runners, Gates, Cold Slug Well, and Manifold:
Injection mold components can slide perpendicular to or at a certain angle relative to the direction of mold opening and closing during the mold opening process of injection molding. When there are undercuts on the side of the product, slides must be designed in the mold. The principle is to first withdraw the slide and then eject the product. Otherwise, the product’s demolding motion would interfere with the mold, potentially causing damage to the product.
The hot runner manifold is a crucial component of the hot runner system. It’s situated between the main runner nozzle and the nozzles at each injection point. The main function of the manifold is to distribute the plastic melt from the main runner nozzle through its internal channels to each injection point, ensuring uniform filling of the mold cavity and a balanced flow of plastic. Additionally, the manifold is responsible for maintaining thermal balance within the system.
Comments: I purchased the Jerk Bait mold 28 days ago and out of the package the mold did not line up to the point where the injector tip will not fit correctly and one of the ribs for the bottom portion of the bait that makes the hook slot on the jerk bait, is missing/broken. This mold is dangerous and unusable since the tip could get stuck and when the injector is pulled out, hot plastic could spill everywhere. I contacted Do-it directly and they said they would replace it but we are going on a month now and I do not have a replacement mold in the mail yet. Not a good experience! Save your money and buy an aluminum mold.
The sprue can be regarded as the continuation of the nozzle’s channel within the mold. In single-cavity molds, the main channel that leads directly to the part’s gate is called a direct gate.
Cold slug wells are typically placed at the end of the sprue, and when the length of the sub-runners is long, cold slug wells should also be established at their ends to capture the cold material generated between two injections at the nozzle end. This helps prevent clogging in the sub-runners or gates.
There are multiple forms of ejection systems, and their design is a significant aspect of mold engineering. While it’s not possible to list all types of ejection injection mold components, here are a few commonly used parts in ejection systems:
The mold base serves as the semi-finished framework of a mold, comprising various steel plates and components, essentially forming the skeleton of the entire mold set. Due to the significant differences in processing requirements between mold bases and the molds themselves, mold manufacturers often choose to order mold bases from specialized manufacturers. This leverages the production strengths of both parties, aiming to enhance overall production quality and efficiency.
The venting system is crucial for expelling air from the cavity as the molten plastic fills it and for allowing air to enter the cavity when the mold opens, preventing a vacuum within the mold structure.
Orders shipped to international, APO/FPO, Alaskan or Hawaiian addresses or U.S. territories are not eligible for the free return shipping offer. Drop Ship and Oversized Items are not eligible for the free return shipping offer.
The ejection system is a crucial component of a mold, primarily designed to eject the molded plastic parts and the solidified runner material from the mold after the injection molding process is complete. The design and quality of the ejection system directly impact the quality of the final products. Therefore, it’s essential to design the system in a way that prevents defects like deformation, whitening, or cracking of the products during the ejection process.
The three-plate mold, separates into three parts when opened, adding a stripper plate compared to the two-plate mold. It is suitable for situations where the plastic parts must not show gate marks around their perimeter or require multiple points of injection for large projected areas. This mold type utilizes pin-point gates and has a more complex structure.
Comments: This is my second mold in essential series. Not real pleased with 2nd one. Its the 3.5 ripper. I'm going to need to file on mold because poor casting on tail area. Spend little more and order a CNC mold!
Situated in the front half of the mold and typically fixed to the injection molding machine, remains stationary. Located at the front, its primary function is to withstand the pressure during the molding process, allowing the raw material to form the desired product shape. The structure of the mold cavity is relatively simple.
Its purpose is to support the mold base. This plate is related to the ejection of the product, and its height correlates with the height of the product.
Comments: I have the 7" ribbon tail mold. I'm lucky if I can get one useable bait after several tries. Its tough to fill and webs despite clamping. I've tried a dozen different approaches and similar fails. Very frustrating.
The structures mentioned above constitute the fundamental components of an injection mold. Indeed, we’ve highlighted some of the more critical mold parts. There are many smaller injection mold components within a mold as well, such as knock-out holes, clamp slots, pry bar slots, locking blocks, support pillars, and more. We’ll take the opportunity to provide a more detailed introduction to these components in the future.
GETTING A QUOTE WITH LK-MOULD IS FREE AND SIMPLE.
FIND MORE OF OUR SERVICES:
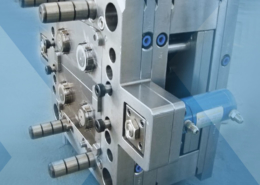
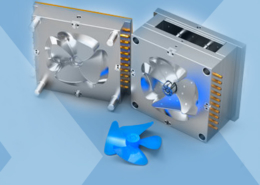
Plastic Molding

Rapid Prototyping
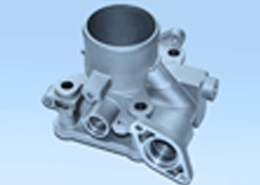
Pressure Die Casting
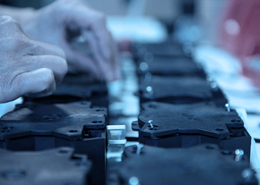
Parts Assembly
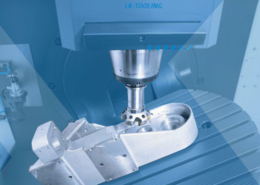