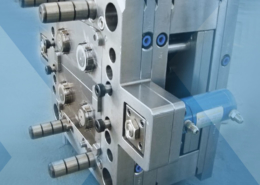
ACO Mold: Plastic Injection Molding Manufacturer - plastic mould maker
Author:gly Date: 2024-10-15
The Sussex, Wis., company, led by CEO Keith Everson, recently completed a new, 87,000-square-foot building near its 40-year-old facility. It has prepped the 20-acre lot and structure to be able to efficiently add another 70,000 square feet.
The new facility has a consistent ceiling height of 30 feet. This was important for several reasons, chief among those to accommodate an ISO Class 8 clean room for contract manufacturing and packaging products for Sussex's health-care industry clients. Sussex plans to complete construction of the clean room early next year.
"Clearly, a manufacturer like this, when we sit down with them, we'll always want to maximize square footage on the building," said Terry Koth, director of operations with Design 2 Construct, the design and construction firm that worked with Sussex. "This plant was no different. We had no less than a half a dozen iterations to figure out how to get the best square footage."
"We see some new products that we are working on that have some great growth possibilities," he said. "We have to be ahead with the facilities and the growth. It's not 'build it and they will come.' "
"We just became landlocked and couldn't expand anymore," Everson said. The original plant still is the "mother ship," he noted. It is sized at 125,000 square feet on 14 acres.
One of the key decsions with the new building was the ceiling height. Because it was expanded in phases, the original building has a variety of ceiling heights, from 20 to 25 feet, Everson said.
"We want to use resources in our area; we do not want to stick out like a sore thumb; we want to blend in. That's really the drive, just being a good neighbor," he said.
One of the current manufacturing cells that Sussex feels is suited for eventual transfer is a two-stage process to create an athletic hydration bottle assembly. In process one, Sussex uses a robotic transfer injection molding method to create a dispensing cap with molded-in soft touch grip and internal seal. An inline automation system completes assembly by installing a valve and retention ring component. Process two integrates an injection molding machine, via a six-axis robot, with an accumulator head blow molding machine. Injection molded soft touch side grips are inserted into the blow mold along with an in-mold decorating film.
The facility has 3,000 square feet of office space and was built to accommodate logistics operations. The company ships finished products directly to retailers, said John Berg, director of marketing for Sussex.
Tough Black (Loctite Henkel 3843) and Ceramic-Filled (BASF 3280) are two new advanced photopolymer materials now available for 3D printing.
As an injection molder, Sussex IM is used to handling complex parts and big projects. In some ways, building a new plant called on the same skills.
Sussex still is trying to determine the volume of material that will be processed through the new site. The company deals with 130 to 140 grades of resin. It does not have rail access so it uses tankers and silos. The original plant houses 65 injection molding presses ranging from 25 tons to 955 tons of clamping force, with 10 presses that are capable of two-shot molding. Sussex also has one blow molding machine for making water bottles.
"We just don't make little widgets," Everson said. "We literally are shipping finished, packaged products. We have to lay things out differently than it was 20 years ago."
"Our No. 1 priority is safety," Everson said. "I want everyone to come to work healthy and to leave healthy. We have bigger areas for guarding and more complex assemblies. We are molding the product, and it comes off the line so that it is ready to be hung on a retail shelf."
"We measure the current total real estate devoted to the complete manufacture of the product as 980 square feet," he said. "The additional elbow room of our new facility allows us to consider re-engineering the layout of the system based on the needs of the cell. It enables us, for example, to devote more space for in-and-out access for material handling. If we can optimize the process in any way with more layout flexibility and that means we need another 200 square feet, we can now commit the floor space."
"It is expensive to frequently rearrange molding presses to accommodate the additional space needs of a new project," Berg said. "More often than not, a custom molder will lay out a new cell to fit an existing press environment because they cannot easily — physically or financially — shut down and move a number of other presses to make more room. Our new facility gives us planning options for improvement. Once we get to the point where it is so filled with manufacturing activities that we start to see capacity restraints, we can easily expand."
Our digital factories create prototypes and low-volume parts fast, while our manufacturing network, offers advanced capabilities and volume pricing.
"When these trucks are coming into the facility, they divert and go to the right; any employee or visitor goes left," Koth said. "The design keeps them separated, which is important for safety."
Officials also wanted to find a way to economically use the bedrock that was blasted away during construction. Construction workers had to deal with bedrock that was jutting out of the ground. "The entire site is on bedrock," Koth said. "We had very little soil at all, and in some places the rock was projected. With massive bedrock, you have to blast it."
Our helpful design aid demonstrates part features that are too thin or too thick, bad bosses, right and wrong ribs, and other considerations to be mindful of while designing parts for injection molding.
Proto Labs, Inc. 5540 Pioneer Creek Dr. Maple Plain, MN 55359 United States P: 877-479-3680 F: 763-479-2679 E: [email protected]
The space for the complex cells was carefully planned with automation and safety in mind. Individual press sizes involved in the manufacturing cell are a key driver to the final floor space needs. The new site will house more involved and expansive cells that integrate distinct production and value- added processes with product validation and final packaging operations. The company envisions a range of different space requirements for the cells, starting from less than 1,000 square feet to double or triple that as project requirements and budgets dictate.
Koth said the company turned its experience with the bedrock from a negative into a positive. Contruction workers crushed the rock on site, which eliminated the need for trucking it out of the location. And, the company used it as the stone base under the building and parking lots.
Everson's goal was to become more efficient and also to allow for the square footage that will be needed for the fulfillment services it offers to its customers.
Officials also designed for safety on the outside of the facility. To help prevent accidents, the loading docks are located away from parking lots used by employees.
The village of Sussex has a tree policy that supports the community's efforts to retain its rural character, Berg said. The trees that were cleared for the building, driveway, loading dock areas and parking lot needed to be replaced within the village at a cost up to the value of the trees removed, which was $100,000. Sussex planted 127 trees on the new lot and on the corporate headquarters and manufacturing facility lot.
"We have always done cell manufacturing," Everson said. "We have always done our assembly and automation at our presses. The presses and automation seem to be getting more complex. You need more space, and that is what we were able to do with this greenfield startup that we have."
The site borders wetlands, which the company protected by constructing two detention ponds that prevent flooding while limiting soil erosion and storm-water runoff.
To accommodate expansion, the building has special features, Koth said. "We used high-efficiency insulated wall panels along the entire west wall," he said, noting that they are 30 feet tall and 3 inches thick with a 24-gauge metal skin. "That is the wall that would be part of the new expansion when that goes. That was done in order to make expansion much easier. It was cost-effective, too."
The ceiling height gives Sussex much more flexibility with the clean room and air systems. "When we were looking at putting a clean room in our existing facility, it just made more sense to put it into the new site versus trying to retrofit an older facility," Everson said.
Want to learn more about injection molding? Sign up to receive a Design Cube. This physical aid demonstrates how to properly design features commonly found on molded parts.
Get machined parts anodized and chromate plated with our quick-turn finishing option. Eligible materials include aluminum 6061/6082 and 7075.
In planning the facility, which has not yet begun molding operations, Sussex took special consideration of the environment and employee safety. For factories undertaking such a project, a greenfield expansion comes with plenty of challenges. They include site selection; dealing with local jurisdictions on items such as access; availability of skilled and unskilled labor; and local taxes and regulations. All of that should be considered before the first shovel of dirt is turned.
Polystyrene is an amorphous thermoplastic that offers transparency and heat resistance. It's commonly used in medical applications, packaging and containers, and appliances. The resin is also food contact compliant.
The environmental considerations for the project were critical, officials said, and carefully thought-out for both the exterior and interior. The precast panels that make up 75 percent of the exterior walls have a no-thermal-break design with continuous insulation. The HVAC system is a rotational air system that is more efficient than traditional rooftop units. The company uses LED high-efficiency lighting throughout the building and double-pane, Low-E glass for energy efficiency.
"It's all part of our culture," he said. "We try to treat people the way we want to be treated. We try to have a nice-looking campus. If we have a bunch of trees in between us and our neighbors, it's almost as if they do not know we are here.
Sussex plans to maximize the site's efficiency by running programs that are flexible in terms of how the production cells can be arranged.
"We have done that, we will do that, and that is another reason we did a higher ceiling," Everson said of using mezzanines. "That is definitely a trend. It is a much more efficient way of using your space."
GETTING A QUOTE WITH LK-MOULD IS FREE AND SIMPLE.
FIND MORE OF OUR SERVICES:
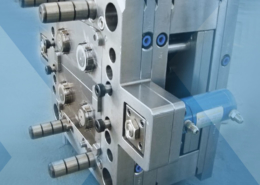
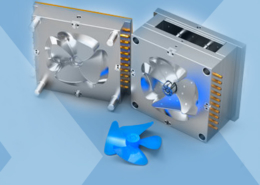
Plastic Molding

Rapid Prototyping
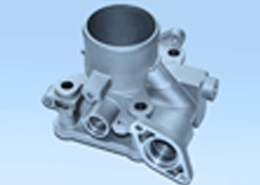
Pressure Die Casting
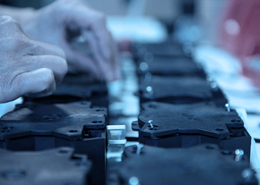
Parts Assembly
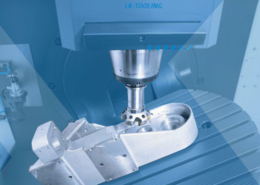