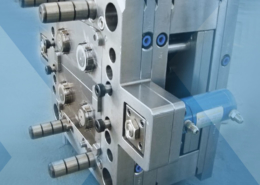
ABS Plastic | Material Series for Product Design - First Mold - casting abs plas
Author:gly Date: 2024-10-15
That’s pretty slick. I’ve been wanting to build one of these for a while now, and it’s good to see such a great DIY concept model.
The key here is automation (well at least for as much of the process as can be practically done). Sure you could absolutely do everything the motors do manually but I have a feeling the goal for this specific project was automation.
The build relies on a pair of beefy 3hp motors to drive the screw-based injection system. These are responsible for feeding plastic pellets from a hopper and then melting them and filling the injection reservoir, before then forcing the hot plastic into the mold. Further stepper motors handle clamping the mold and then releasing it and ejecting the finished part. A Raspberry Pi handles the operation of the machine, and is configured with a custom Python program that is capable of proper cycle operation. At its peak, the machine can produce up to 4 parts per minute.
Yep, that’s it, Kenner Moldmaster. I had a lot of “maker” kind of toys, Mattel Vac-U-Form and other stuff. Guess I was starting early.
Discover AIM Processing's customer small part injection molding services, designed to deliver precise, high-quality components for industries requiring intricate and complex plastic parts.
But you can also make your own from drill presses and readily available parts: https://www.youtube.com/watch?v=HoSVPHVESiE
Yeah a lowly arduino and small 16×2 lcd could definitely do the same job but I guess those were the parts they had lying around and wanted to use
I had one of these. It went the way of many of my toys, but I found a replacement on eBay a few years ago. Unfortunately, the molds were warped to the point where they won’t work any more, so I’ll have to make some new molds in order to play with it. The molds were made of what looks like nylon, and the plastic that was injected I think was a blend of polypropylene and paraffin that melts at a pretty low temperature (similar to what is sometimes called “carving wax”), but still, using thermoplastic molds to mold thermoplastics is kind of iffy.
for low temp plastic and for resin 3D printers using high temp resin you can even just skip straight to 3D printing the molds with some kind of basic “standardized” mold frame made from metal.
“We received the charger base and I want you all to know it looks FANTASTIC! Thank you for getting us this one for the BOD meeting.”
Good to see, straightforward to fabricated. Along with titanium 3D printed moulds could be a good mix for smart batches. Thanks for posting :-)
By using our website and services, you expressly agree to the placement of our performance, functionality and advertising cookies. Learn more
I work with injection moulding machines. This is real cute could I have one to put on a keyring or maybe my car’s rear view mirror. :0)
The really cool part is you can 3D print a pattern, make a plaster copy using a silicone mold and then cast zinc alloy dies after drying the plaster in the oven for 24 hours and achieve surface finish as good as the 3D print. Subject to details such as pulling a vacuum on the plaster to remove bubbles and other details.
AIM Processing specializes in small part plastic injection molding. We define "small plastic parts" as roughly the size of your fingernail to the size of your hand. Injection molding is a process in which plastic resin, in pellet form, is heated and sheared until it reaches a viscous state.
I had an injection molding machine as a kid… a toy of course, but it ticked all the boxes. It was a heated vertical cylinder with a plunger, below that was a slot for a 2-piece plastic mold.The feedstock was a granulated rather waxy material. The procedure was, fill the chamber with measured amount of the granules and put the mold in the slot below. After allowing time for the plastic to melt, you pushed down the plunger to inject it into the mold. It really worked pretty well for a toy. I had molds for tanks and soldiers and construction equipment like bulldozers, and the plastic material in several colors. I wish I could remember what it was called.
I’ve been planning to make something like this. All the motors and other stuff seem unnecessarily complex, when all it needs to do is: 1) Melt the plastic 2) Make good seal with the mold 3) Apply a lot of force (i.e. my weight) over a few seconds.
The design and manufacture of custom molded plastic parts can seem simple at first, but there are many details that must be taken into consideration depending on how the part will be used. For example, there are mechanical properties like:
I have a PIM shooter Model 150. I bought it used for $500 and I really like it: https://www.techkits.com/products/model-150a/
It’s an impressive piece of industrial-type hardware. If you want to produce a lot of plastic things in your own facility, a machine like this is very much the way to go. It’s not the first machine of its type we’ve seen, either! Video after the break.
3D printing is all well and good if you want one of something, but if you want lots of plastic parts that are all largely identical, you should consider injection molding. You can pay someone to do this for you, or, in true hacker fashion, you can build an entire injection molding setup in your own garage, as [Action BOX] did.
Then there are factors like the manufacturability of gate locations, draft, and ejector pins. It's enough to make your head spin.
It is then injected under enormous pressure into a steel or aluminum mold, cooled until it hardens, and ejected. With small part injection molding, we are able to manufacture complex, small shapes in a cost-effective, repeatable process.
Me Like! It’s also been running some hours, guessed from the wear on the timing belt @04:15. Also like the home-built mill in the backgound…
As a leading small plastic parts manufacturer, we work with engineering grade plastics to create custom molded plastic parts that match the requirements for a part with properties like: chemical resistance, flexural strength, durometer, and yield strength to name a few. There are so many material options, and we can help you make the right choice for your program.
GETTING A QUOTE WITH LK-MOULD IS FREE AND SIMPLE.
FIND MORE OF OUR SERVICES:
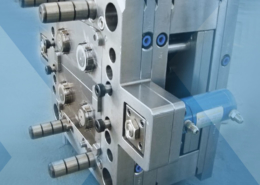
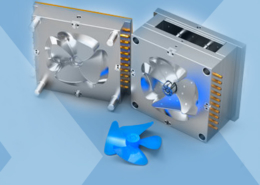
Plastic Molding

Rapid Prototyping
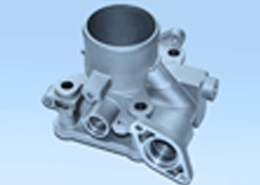
Pressure Die Casting
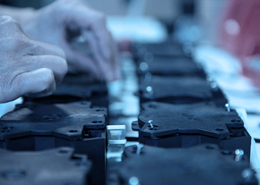
Parts Assembly
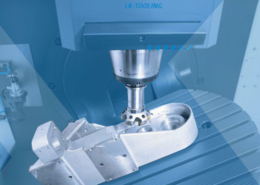