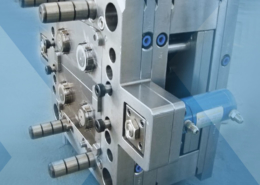
ABS Injection Molding: Pros and Cons for Your Project - abs molding
Author:gly Date: 2024-10-15
Target 20 to 80 percent shot capacity for applications using general-purpose resins but a 30 to 50 percent shot capacity for engineered resins.
The electrode is then lowered to the workpiece. Then, using a controlled electrical source, the electrode is used to destroy and disperse the metal in the area opposite of the electrode. The electrode never contacts the workpiece. A spark gap of a few thousandths of an inch is always maintained between the electrode and workpiece. This process is a slower method of removing metal from a mold; however, the EDM process can produce shapes that are not possible with conventional CNC machining.
Electrical discharge machining (EDM) has become widely used in mold making. EDM is a process in which a desired shape is obtained through the use of an electrode, which is fabricated out of graphite or copper. It is then mounted in an EDM machine and positioned over the workpiece, which is submerged in a dielectric fluid.
A mold is usually designed so that the molded part reliably remains on the B half of the mold when it opens. The runner and the sprue are drawn out of the A half. The molded part then falls freely when ejected from the B half.
In modern CNC systems, the mold design and manufacturing processes are both highly automated. The mold’s mechanical dimensions are defined using computer-aided design (CAD) software, and then translated into manufacturing instructions by computer-aided manufacturing (CAM) software. “Post processor” software then transforms these instructions into the specific commands necessary for each machine used in creating the mold. The resulting commands are then loaded into the CNC machine.
Beyond just clamp tonnage, review other important factors such as tie-bar spacing, minimum mold height, maximum mold height, stroke and daylight.
The injection unit is often an afterthought when it comes to quoting machines. Factors to consider include material type, fillers in the material, the molded shot size, the cycle time, the residence time, the injection plastic pressure, screw recovery time and screw geometry.
Let's look at the types of clamp design. The toggle clamp is a time-tested design that has been around for decades, as has the clamp design based on a hydraulic ram. Over the last 20 years, the industry developed the two-platen machine, which for practical purposes has replaced the hydraulic ram. Last is the C-frame clamp design typically employed by vertical machines; it has more recently been seen in horizontal machines but only those offered by one supplier. The most common clamp designs are toggle and the two-platen.
How about when you purchase an injection unit that is too large for the minimum shot size required? You underutilize the injection unit. This may result in shot inconsistencies since the ratio of material from the seating of the check ring to shot size will result in inconsistent shot weights. A certain amount of material is required to set the check ring. As shot utilization goes down, the effect of the check valve on the material flow goes up. Additionally, you might end up with residence time that is too long, causing the material to degrade.
Another advantage of the EDM process is that it allows pre-hardened molds to be shaped and eliminates the need for additional heat-treating. At times, such as with speaker grille molds, the resulting fine EDM finish serves to be the final part finish without any polishing of the mold cavity.
Considering the maximum shot size of any given injection unit, general-purpose resins like PP, PE and PS will run best if the shot size is 20 to 80 percent of the injection unit’s shot capacity — the 20/80 rule. Engineered resins like ABS, PC, EOM and nylons will run best if the shot size is somewhere between 30 and 50 percent of shot capacity.
The plastic injection mold consists of two primary components, the cavity half of the mold (A half) and the ejector half of the mold (B half). These mold halves are designed to work in conjunction as follows:
Volumetric metric capacity is the right way to specify the injection unit and compare suppliers. Tackle this analysis carefully to account for the type of material used by your application. Most molding machine manufacturers present injection unit specifications based on PS. But the performance data will be different for other materials.
Many steel molds are designed to process well over a million parts during their lifetime. For lower volumes, pre-hardened steel molds provide a less wear-resistant and less expensive option.
One of the mistakes many molders make is to misunderstand stroke vs. daylight. Stroke is the dimension from either the minimum mold height or the maximum mold height, to the most open position of the moving platen. Daylight is the dimension of the face of your fixed platen to the face of the moving platen in its most open position. Stroke and how it is referred to changes depending on whether you are talking about a toggle machine or a hydraulic cylinder machine.
Always remember to adjust your calculations for the right output factor of the material that you'll be running and then adjust your specifications properly for the calculated shot size.
An important factor to consider is tie-bar spacing. Today’s molders are trying to put big molds into clamps. Don’t forget about minimum mold height, maximum mold height, stroke and daylight to ensure the largest mold you plan to run will fit comfortably in the machine.
Analyze the clamp specifications and the injection unit specifications of the molding machine under consideration separately.
What happens if you purchase a machine and the screw and barrel are too small for the application? You overutilize the injection unit. When processing, the residence time may be too short, restricting the homogenized melt; recovery time may exceed the cooling time and you’re wasting precious cycle time.
Say you are molding PP, though, with that same screw. PP has a melt factor of 0.73 gram per cubic centimeter. To reflect the true performance specifications using PP, take the volumetric capacity of 9,698 cubic centimeters, multiply it by a melt factor of 0.73 gram per cubic centimeter of PP, and you have 7,079 grams of processable weight, not 8,825 grams. There is a loss of almost 20 percent in injection capacity between the PS-based specification sheet data versus the performance you will experience using PP. This is significant, especially when you consider materials that apply to the 20/80 rule. You might need to move up an entire injection unit size to maintain the proper injection pressures, proper screw recovery time and proper residence time.
Unless otherwise specified, most machine manufacturers quote their molding machines with a general purpose (GP) screw. But many applications should be using a mixing screw, and sometimes, a barrier mixing screw.
Copper alloy inserts are sometimes used in areas of the mold that require fast heat removal. This can reduce cycle time and improve the aesthetic quality of the part.
A single plastic injection mold can have one cavity, producing one part at a time, to multiple cavities for extremely high-production molds (like those for bottle caps) that can have 100 plus cavities.
In its conventional form, standard machining requires the manual use of lathes, milling machines and drill presses. With advanced technology, CNC machining has become the predominant means of creating more complex and accurate molds, while still using standard machining methods. With CNC, computers are used to control the movement and operation of the mills, lathes, and other cutting machines.
Aluminum molds, on the other hand, can cost substantially less, but they typically are ill-suited for high-volume production or parts with narrow dimensional tolerances. Nevertheless, aluminum molds can economically produce tens of thousands to hundreds of thousands of parts, when designed and built using computer numerical control (CNC) machines or Electrical Discharge Machining (EDM) processes.
Tonnage is presented by manufacturers in three ways: kilonewtons, metric tons and U.S. tons. Asian suppliers typically refer to kilonewtons, whereas European suppliers will discuss metric tons and U.S. suppliers and customers talk about U.S. tons. A metric ton is basically a 10th of a kilonewton. A U.S. ton is going to be 10 percent more than a metric ton.
For example, a screw with 9,698 cubic centimeters of volumetric capacity will process 8,825 grams of PS at 26,397 PSI. This is based on the material’s melt factor of 0.91 gram per cubic centimeter.
CS Tool Engineering ♦ P.O. Box 210-K ♦ 251 West Cherry Street ♦ Cedar Springs, MI 49319Phone (616)-696-0940 ♦ Email cste@cste.comWebsite design and hosting by Creative Technology Corp
The clamp has tons to consider. Yes, that pun was intended. Beyond just clamp tonnage, other important factors are tie-bar spacing, minimum mold height, maximum mold height, stroke and daylight.
We are often asked, “My total shot weight is 100 ounces. Does this mean I need a 100-ounce shot?” No! Here are some of the common rules of thumb that you should use in specifying the injection unit.
Plastic injection molds are typically constructed from hardened or pre-hardened steel, aluminum, and/or beryllium-copper alloy. Steel molds cost more, but are often preferred because of their high durability. Hardened steel molds are heat treated after machining, and they are by far superior in terms of wear resistance and lifespan.
Injection molding machinery suppliers often receive requests for quotes asking for pricing based on the tonnage of the machine only. When asked for more details, the buyer might respond, “I just need a 1,000-ton quote.” Better to consider the molding machine as two separate pieces — the clamp unit and the injection unit — and dig into the details to help ensure you purchase the best configuration for your needs.
GETTING A QUOTE WITH LK-MOULD IS FREE AND SIMPLE.
FIND MORE OF OUR SERVICES:
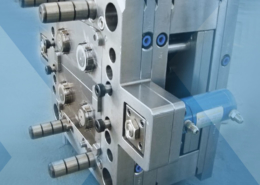
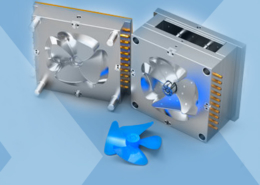
Plastic Molding

Rapid Prototyping
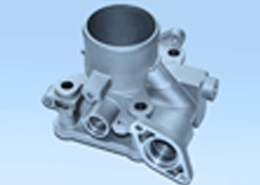
Pressure Die Casting
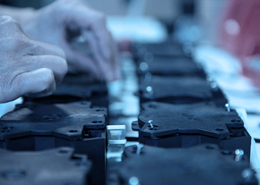
Parts Assembly
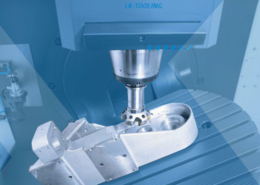