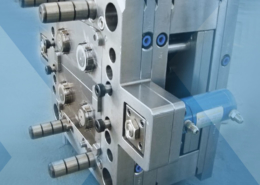
ABS Injection Molding 101 - abs plastic injection molding
Author:gly Date: 2024-10-15
Structural foam injection molding is a unique manufacturing process that combines traditional injection molding with a foaming agent to create parts with a foamed core and solid outer skin. The process begins by heating thermoplastic material until it becomes molten. At this point, a foaming agent is introduced into the material, which will later cause the plastic to expand and form the characteristic foam structure. The molten, gas-infused material is then injected into a mold under lower pressure than in conventional injection molding. This lower pressure allows the foaming agent to expand within the mold cavity. When the material contacts the mold walls, the surface cells collapse. This results in a core of interconnected cells surrounded by outer layers that make up a smooth, dense, solid skin.
2. Material of steel cavity and core with imported 1.2316 stainless steel with fine polishing, high hardness and anticorrosion to get mold’s high precision and good quality.
4.About hot runner hot runner system is designed and made by ourselves, it can achieve ideal and prompt heating effect for preform production ,cavity with lower injection pressure to reduce wear and tear of mould parts.
Want to discuss a question or comment related to plastics manufacturing and our services? Contact us via the contact form below. A team member will review your submission and follow up as soon as possible.
Consider the company’s capabilities to manufacture both structural foam and structural web products. That’s something you won’t find with every plastic manufacturer. Think about the company’s quality control and testing protocols as well. A company that takes quality control seriously is a company worth considering.
The material used in the structural foam process is critical to achieving the desired product properties and aesthetics. Selection is often based on application requirements such as chemical resistance, dimensional stability, or the ability to withstand environmental stress. One of the benefits of working with Cooper Plastics is that we have an experienced team that can provide recommendations to ensure the final product is cost-efficient and meets industry and application specifications.
Structural foam injection molding is a method of creating lightweight, durable plastic products. The process is cost-effective due to reduced material usage and the ability to create large, complex parts in a single molding cycle. The structural foam molding process includes the following steps:
Another quality indicator is the company’s investment in advanced technology and equipment. The best structural foam molding companies like Cooper Plastics have state-of-the-art machines that offer precise control over the manufacturing process, resulting in product consistency and strict adherence to project specifications.
8.special satisfied serve each mould undergoes strict mould test before delivery.we can provide an experienced team for installation and test as per client’s request Standard inter-changeable mould components
As the material cools, it solidifies into a lightweight yet rigid and strong structure. Companies can mold medium wall thickness or very thick wall sections based on need. This makes structural foam injection molding particularly advantageous for producing large, complex parts that need to be durable without being heavy. Additionally, the reduced pressure involved in the process allows for the use of larger molds and can lead to lower material costs, making it an efficient and cost-effective option for many industries.
At Cooper Plastics, we are capable of producing both structural foam core and web core plastic products. This versatility is relatively rare in the industry and makes it possible to produce a wide range of plastic structural elements that are durable and cost-effective.
3.About gate pin-valve gate ,pneumatic drive the nozzle pin simultaneous high speed open and close action. which can effectively control the injection hole open and close actions on each cavity. reliable seal function, smooth moving, low thermal expansion rate ,long using life and also saves electric energy.
The machine we utilize at Cooper Plastics is relatively unique in that it allows us to manufacture both structural foam and structural web products. This versatility enables our customers to get ultra-large plastic parts that wouldn’t be possible with other molding technologies.
In addition to the above features, Sinco has great after sale customer service. The English edition of machine manual book and spare parts will be delivered together with Sinco Bottle cap molds to our customers. More importantly, Sinco will send experienced and skilled engineers to the place where you would like to install the machine, and they will finish the rest work for you to make the machine be ready to use.Also,Please don not feel uncomfortable to call our 24/7 customer service number for any technical questions or problems. Sinco will achieve world-class status by successfully meeting our goals and completing our objectives. Now, please contact us now for your next Bottle cap mold.
Parts that are made with the structural web process are solid with hollow channels and hollow thick sections packed out by internal injection of low-pressure nitrogen. Benefits of using the structural web process include:
Want to partner with Cooper Plastics for your structural foam injection molding needs? Request a free quote or contact us for more information.
At Cooper Plastics, we offer numerous other value-added services in addition to our structural foam molding service. These services include product development, finishing, assembly, and more. By offering these services, we elevate the experience for our customers and help them get the most out of our partnership.
one stop solution for your cap production, 1-16 cavity, 24 cavity, 26 cavity, 32 cavity, 48 cavity, 72 cavity with neck finish ROPP, ALASKA,PCO1881, 30/25, 29/25, 26/22, 38mm, 48mm, 50mm.
5.heat system with double heating system,it has separate temperature control mode ,the heat bar are used to heat the mould mainfold plate,small heaters supply the heating temperature for cavity nozzle continuously.
At Sinco, we always start by learning and understanding all the specifics of the cap products you manufacture, then decide the best processes and machinery to produce them. Based on our rich experience in this industry, we offer different kinds of plastic cap mould solutions, automatic unscrewing ejection cap solution, bi-injection system cap solution, complex flip top cap solution, irregular shape design cap solution and cap moulding machines at reasonable prices. Each year, weoffer more than 100 sets of Bottle cap mold that has already been globally recognized and according to our clientsthose machine working smoothly, stability and perfectly. it helps them get the business not only because of quality cap production, but also due to wonderful appearance that gives charm to production site.
We can provide customized solutions to meet strength, weight, and materials specifications. Below is an overview of Cooper Plastics structural foam and web capabilities.
Structural foam molding is a desirable plastics manufacturing process if you need to produce large, complex parts with excellent strength-to-weight ratios. It is popular for the production of:
Seek transparency from the company you’re considering by requesting a detailed quote. Getting a breakdown of anticipated production costs will allow you to decide whether you want to proceed with the project, make adjustments and get a new quote, or drop the company from your consideration list and vet a different company.
Finally, you never want to overlook customer service. Seek a plastics manufacturing partner that will work closely with you throughout the entire process, from initial design to final production. The company should offer guidance, support, and communication that will ensure a project that you are completely satisfied with.
Key features often include multi-nozzle systems to ensure even distribution of material and foaming agents, as well as precise control over injection speeds, pressures, and temperatures. Advanced structural foam molding machines are also equipped with state-of-the-art monitoring systems that allow operators to fine-tune the process in real time.
Specifications 1.hot runner with valve gate system; 2.self-lock structure; 3. Spare parts for free; 4. Interchangeable for core, cavity,neck
7.heat treatment mechanical treatment cavity and core to prolong service life ,nitrogen treatment with neck screw.with?fitly operation ,guarantee?Long using life over 2.0 million times of injection cycle
The cost of structural foam injection molding varies based on many factors, including the type and complexity of the product, material used, project requirements, and production run size. There are additional services that can be added that increase costs. These services include finishing processes like drilling and assembly or various post-production testing services.
Other structural foam materials that can be utilized include polypropylene (PP) and acrylonitrile butadiene styrene (ABS). These materials are known for their strength and impact resistance, making them ideal for components that require a balance of rigidity and reduced weight.
We engaged in manufacture the high quality Bottle cap moldfor your business in complete price. Our blowing machine designed with high output with working stable, and power saving.
You must evaluate several factors to identify quality structural foam molding companies. A good place to start is with the level of expertise. Does the company have extensive experience with foam injection molding services? A dependable company will have a proven track record of producing structural foam parts with consistent quality and durability. This means knowing which materials and processes will yield the best results.
1.About design Advanced structure is designed to improve rate of finished products Two-step dual taper locating technology; each cavity self locked independently; off-center adjustment system make the thickness error of perform less then0.05mm. Bottleneck is adopted International Screw thread standard, No cutting of gate is employed to reduce the labor intensity
Structural foam molding machines are typically high-tonnage injection molding presses equipped with advanced controls and capabilities to manage the lower pressure required for the foaming process. The machines are designed to accommodate larger molds and produce consistent, high-quality components.
Sinco ensures that every machine is designed & developed as per specifications laid by our esteemed client. Our company endeavors to also provide customized solutions for every machine. The only thing that customers need to do is sending us cap pictures which they like, then let us to finish designing and producing of Bottle cap mold work for you. With our in-depth knowledge of hydraulic operations, and by using the most advanced technology and the newest design we have streamlined our activities, resulting in faster delivery of machines at competitive price.Our vast infrastructure is well equipped with latest facilities and machines which are supervised by experienced professionals.And with the PLC controller and the Human-Machine interview, workers are able to control the Machine and finish the work on one screen, which means any trained worker can use the machine easily and individually.
GETTING A QUOTE WITH LK-MOULD IS FREE AND SIMPLE.
FIND MORE OF OUR SERVICES:
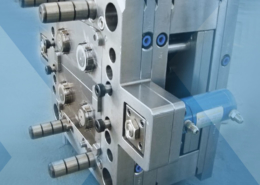
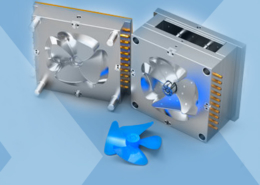
Plastic Molding

Rapid Prototyping
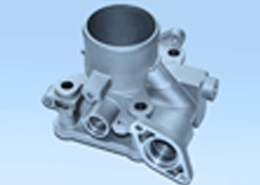
Pressure Die Casting
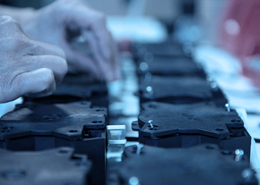
Parts Assembly
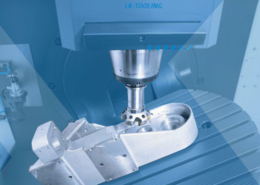