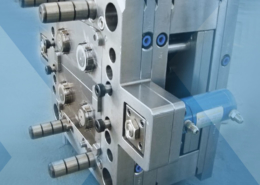
A Rookie's Guide to Plastic Injection Molding - mold plastic injection
Author:gly Date: 2024-10-15
Increase added value, optimize the injection molding process, automate further, integrate innovatively? Then we are your partner as a primary contractor. As it has been for many leading companies worldwide.
Steel Tooling is the most expensive but also the strongest. Steel tooling is used any of the following instances: when high temp and pressure is required (SMC), when producing very large volumes (50,000+) or when a Class A high gloss surface finish is needed.
Because ergonomics are paramount when you’re overmolding inserts: use our vertical ALLROUNDER injection molding machines from the sector’s most extensive range.
The arburgXworld customer portal gives you access to a wide range of digital apps and features that make your daily work easier.
We utilize cross functional reviews from product engineering to manufacturing engineering to operations…we discuss moldability, manufacturability, shipping and handling.
The lead times for all tool materials will vary. Heavier, denser steel is much more difficult to machine than, say, aluminum which, of course, effects the lead time. Below is a list of tooling types with an approximated lead time.
Choose our hydraulic injection molding machines if you want to use a wide range of injection molding processes, reliably and with precise reproducibility.
Electronics, medicine, mobility, packaging, complex components for a wide range of sectors. This is where you excel. So do our machines and solutions.
Is injection molding part of your business? When productivity and efficiency are your goal: Choose ALLROUNDER. Because the modular ARBURG injection molding machines meet your requirements to the letter.
If you are familiar with injection molding, you may have heard about a mold flow analysis. This is a computer model that simulates the flow of the material into the mold. With this type of analysis, you can accurately predict the flow to achieve a quality part within the first few shots, if not the first.
Performance-oriented and at the same time cost-efficient: companies appreciate working faster and more precisely with the electric ALLROUNDER injection molding machines.
To give you some more insight into what goes in to making a tool, here are the lead times broken down by each step of the mold making process.
We know your sector. We know your materials. We have the accessories. And we can think ahead together when you are pursuing new possibilities in injection molding.
Fast cycles with reduced energy requirements - that’s what our ALLROUNDER CUBEs deliver. Because you produce in large series or multi-component parts.
And while the process is important, tooling will hit you in the pocketbook right from the start. In fact, in some cases, the cost of tooling is a factor in choosing a molding process. Therefore, it will be important to know everything that goes into creating a tool so that you can better understand where your money is going.
At Romeo RIM, we utilize Aluminum tooling almost exclusively. This is because Reaction Injection Molding (RIM) doesn’t require high temperature and pressure. Our engineers learn to understand your project and can match you with the right grade aluminum to help maximize your ROI.
From practical experience – for practical use, that’s how we share knowledge. You benefit from our know-how. Targeted, fast, and cooperative. With our machines, for your purposes.
We mentioned above that the two main components to molding a good part are the tooling and the process. When your tool gets shipped to your RIM molder, it is up to them to have the right manufacturing process in place to ship a quality part.
Composite or epoxy tools are limited to short, prototype runs only as these tools generally don’t last much longer than 100 shots. The options for a desired surface finish is also very limited.
Unfortunately, the reaction injection molding process does not have any such predictive tools. And because of that, it will be very important to choose a RIM Manufacture with good standards and procedures to get the best parts possible.
Because Nickel Shell tooling is even lighter than Aluminum, we at Romeo RIM utilize nickel shell tools when the size of the parts begin to push the upper limits of our size capacity. We also use them to achieve a very high gloss surface finish (70-80 on a 60 degree scale).
For reliable performance, a slimline design, and an unbeatable price, there is only one choice: the new ALLROUNDER 720 E GOLDEN ELECTRIC!
Typically, tools used for reaction injection molding are much the same as those used in injection molding and are made from (in order of cost) Steel, Nickel Shell, Aluminum, Epoxy, or in some cases, Silicone. The decision to choose any one of these over another will depend on a number of factors including the temperature and pressure requirements of the process, the surface finish of the part and the number of parts needed.
At Romeo RIM, we rarely use steel tooling as large RIM parts tend to be ordered in lower volumes. And since reaction injection molding works at much lower temperatures and pressures, the cost of steel doesn’t justify its use.
Combining molded parts, colors and materials, rethinking additive manufacturing, realizing visions and bringing them into series production – that is your goal. We provide the opportunities.
Nickel Shell tooling is also very expensive, but much lighter than steel making it easier to work with, machine and ship. This type of tooling can also achieve an extremely high gloss finish.
With over 35 years of experience manufacturing reaction injection molded parts, we are EXPERTS in understanding how our material will react within the mold so that you get a good, quality part every time.
Our manufacturing philosophy starts with Lean practices which helps to eliminate waste, either from wasted movements or actual material waste.
Aluminum tooling is a popular option because it still performs relatively well at higher temperatures and pressures. And with the advancement in aluminum technologies over the years, there is a decreasing need to use steel tooling in even higher volumes.
GETTING A QUOTE WITH LK-MOULD IS FREE AND SIMPLE.
FIND MORE OF OUR SERVICES:
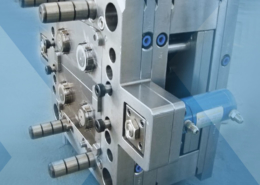
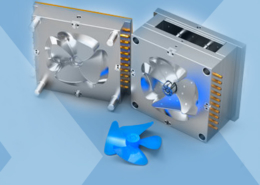
Plastic Molding

Rapid Prototyping
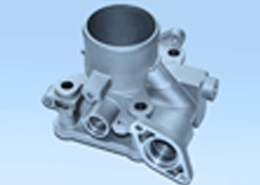
Pressure Die Casting
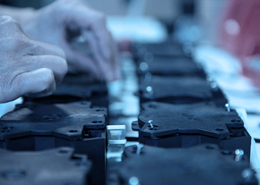
Parts Assembly
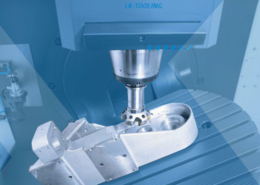