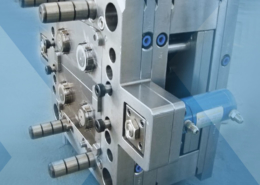
A Plus Plastics | Injection Moulding | Materials Handling ... - plastic injectio
Author:gly Date: 2024-10-15
Cause: Usually a poor seal between the first shot and the second shot mold. Or, the material is too thin in the shut-off area.
Automation and robotics can significantly improve the efficiency and quality of short run plastic injection molding. Automated systems can help reduce cycle times, minimize waste, and improve part quality. Examples of automated and robotic systems in short run plastic injection molding include robotic part removal, automated material handling, and automated inspection and testing.
Efficiency refers to the ability to produce a high volume of parts in a short amount of time while minimizing waste and costs. Quality, on the other hand, refers to the ability to produce parts that meet or exceed customer expectations in terms of functionality, durability, and aesthetics. In short run plastic injection molding, it is essential to balance both factors to achieve successful production. If the process is not efficient, it can lead to increased costs, longer lead times, and lower profitability. If the quality is not up to par, it can result in customer dissatisfaction, product recalls, and damage to the company’s reputation.
If the two materials are somewhat compatible and you simply need to increase the strength of the bond, try maximizing the surface area in the transition zone.
Material selection: The selection of the right material is crucial for achieving the desired properties and characteristics of the final product. Choosing the wrong material can result in poor quality parts, increased waste, and longer lead times.
Cause: Unfortunately, all tab gates produce this defect, known as vestige, on the surface of the part. They’re somewhat of a necessary evil.
Consistent process control: Consistent process control can help ensure that each part produced meets the desired quality standards. This includes monitoring key process parameters, such as temperature, pressure, and cycle time, and making adjustments as needed.
Continuous improvement and problem-solving: Continuous improvement and problem-solving can help identify areas for improvement and prevent quality issues from occurring in the future. This includes using tools such as root cause analysis and corrective action to address quality issues and improve the process.
Quality inspection and testing: Quality inspection and testing can help identify defects and ensure that each part meets the desired quality standards. This includes using visual inspection, dimensional inspection, and functional testing to verify the quality of each part.
Solution: Create a sharp transition between the first and second shot materials in the shut-off areas. To accomplish this, incorporate a step or accent grove into your design:
Maintenance and calibration: Regular maintenance and calibration of the machine and mold are essential for ensuring consistent quality and efficiency. Neglecting maintenance and calibration can lead to machine breakdowns, longer lead times, and lower quality parts.
Operator skill and training: The skill and training of the operator can also impact the efficiency and quality of the process. An inexperienced or poorly trained operator can lead to longer cycle times, increased waste, and lower quality parts.
Emerging technologies and trends in short run plastic injection molding can significantly improve efficiency and quality. Examples of future trends in the industry include 3D printing, advanced materials, and smart manufacturing. These trends have the potential to reduce cycle times, minimize waste, and improve part quality.
Efficient mold design and tooling: Efficient mold design and tooling can help reduce cycle times, minimize waste, and improve part quality. This includes optimizing the mold design for the specific part and using high-quality tooling materials.
Like most plastics manufacturing processes, injection molding has its share of problems and solutions. Same goes for two-shot injection molding — and there’s even more complexity. The key areas to consider when troubleshooting injection molding defects are captured in our Two-Shot Injection Molding Design Guide. Be sure to download your copy today. In the meantime, here are some common two-shot molding defects – and how to avoid them.
To maximize efficiency in short run plastic injection molding, several best practices can be implemented, including proper machine setup and operation, efficient mold design and tooling, material handling and preparation, and process monitoring and optimization.
As for any engineered plastic part, material selection is paramount. Typical considerations include mechanical and physical properties, , heat, electrical, flammability and chemical and UV resistance. For two-shot, if we’re to avoid defects, we must take it a step further and consider the compatibility between the first shot and second shot material.
Process monitoring and optimization: Process monitoring and optimization can help identify inefficiencies and areas for improvement. This includes using sensors and monitoring systems to track key process parameters and making adjustments to optimize the process.
Several factors can affect the efficiency and quality of short run plastic injection molding, including machine and mold design, material selection, operator skill and training, and maintenance and calibration.
Incorporate an accent groove, 1.5 mm – 2.0 mm deep and 0.8mm – 1.0mm wide, in the first shot profile along the edge of the second-shot.
Solution: The solution to the first-shot vestige is quite simple – position it so that the second shot material covers it! The second-shot vestige, however, will require additional processing after the mold cycle. The only way around the vestige all together is to use a hot tip gate, depending on the part design.
Quality control measures are essential for ensuring that each part produced meets the desired quality standards. Examples of quality control measures in short run plastic injection molding include visual inspection, dimensional inspection, functional testing, and statistical process control. Quality control measures help identify defects and ensure that each part meets the desired quality standards.
Proper machine setup and operation: Proper machine setup and operation can significantly impact the efficiency of the process. This includes setting the correct parameters, such as temperature, pressure, and cycle time, and ensuring that the machine is running at optimal conditions.
Two-shot injection molding defects often occur in the shut-off areas where the second shot mold seals against the first shot, or the substrate.
Machine and mold design: The design of the machine and mold can significantly impact the efficiency and quality of the process. A poorly designed machine or mold can lead to longer cycle times, increased waste, and lower quality parts.
To improve quality in short run plastic injection molding, several tips can be implemented, including consistent process control, proper material selection and handling, quality inspection and testing, and continuous improvement and problem-solving.
For more about maximizing efficiency and quality in short run plastic injection molding,you can pay a visit to Djmolding at https://www.djmolding.com/low-volume-manufacturing-service/ for more info.
As discussed in our Two-Shot Injection Molding Design Guide, the type of gate, its design, and location must be carefully considered to achieve the ideal cosmetic appearance and dimensions of your part. In single-shot injection molding, the gate is typically located so that the melt enters at the thickest part of the cavity and then flows to the narrower areas. Its placement in two-shot isn’t as straightforward.
Proper material selection and handling: Proper material selection and handling can help ensure that the final product meets the desired properties and characteristics. This includes selecting the right material for the specific application and ensuring that the material is properly handled and prepared before injection.
In conclusion, balancing efficiency and quality is crucial for successful short run plastic injection molding. Factors that affect efficiency and quality include machine and mold design, material selection, operator skill and training, and maintenance and calibration. Best practices for maximizing efficiency include proper machine setup and operation, efficient mold design and tooling, material handling and preparation, and process monitoring and optimization.
Article Original From: https://www.djmolding.com/maximizing-efficiency-and-quality-in-short-run-plastic-injection-molding/
Material handling and preparation: Proper material handling and preparation can help reduce waste and improve efficiency. This includes using the correct material handling equipment, such as drying ovens and material feeders, and ensuring that the material is properly prepared before injection.
Two-shot design can deliver a competitive advantage far above other molding processes, especially for complex parts. Learn the benefits of the process and explore the special design requirements needed to make it work in this free guide created by engineers, for engineers.
Are you tired of sacrificing quality for efficiency in your short run plastic injection molding processes? Well, it’s time to put an end to that. Maximizing efficiency and quality is not only attainable, but it’s imperative for the success and growth of your business. In this blog post, we’ll explore the strategies and techniques that can help you achieve both efficiency and quality in your short run plastic injection molding. So, get ready to take your plastic injection molding processes to the next level!
GETTING A QUOTE WITH LK-MOULD IS FREE AND SIMPLE.
FIND MORE OF OUR SERVICES:
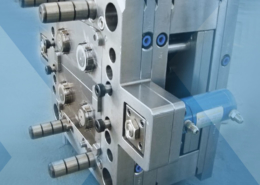
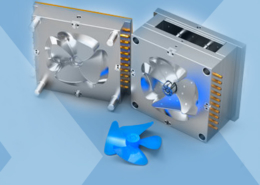
Plastic Molding

Rapid Prototyping
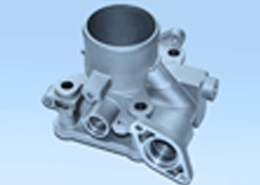
Pressure Die Casting
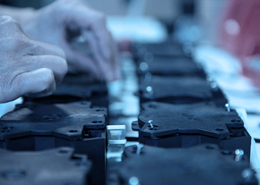
Parts Assembly
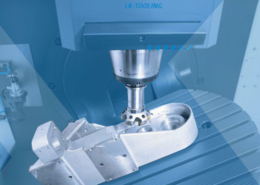