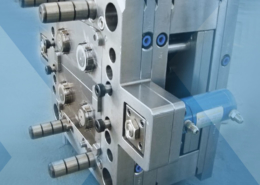
A Plastic Injection Machine You Can Use At Home - plastic injection molding at h
Author:gly Date: 2024-10-15
[fts_instagram instagram_id=2578666033 access_token=2578666033.da06fb6.85629cf5365f45a08a2a9ea6ebfbb8c6 pics_count=3 type=user profile_wrap=no popup=no super_gallery=yes columns=1 force_columns=no space_between_photos=1px icon_size=65px hide_date_likes_comments=no]
There is also a decision to be made between using cooling tower water or chilled water. While cooling tower water has a lower initial cost and operating cost, the water can become contaminated since it is an open loop (open to the environment). The chilled water from an air cooled chiller, on the other hand, is a closed system, so your molds are protected from possible debris and contaminants.
Unlike a hotrunner, a sprue must have a draft angle of greater than 6° during the injection process to prevent sticking of the sprue when the mold is opened. The sprue’s maximum height is reduced as a result. Otherwise, the sprue becomes too thick, causing it to cool or crystallize too quickly, extending the process time. Sprue walls should always be thinner than maximum product walls. PLA should crystallize in a mold when used with high heat materials. Amorphous materials can only be formed by polymers, leaving the rest in the semi-crystalline state.As a result, the product will be slightly flexible when ejected from the mold.When the product draft angle is increased ,enough ejector pins are installed and the ejector surface is sufficient, the product will not warp during ejection.
Conventional injection molding equipment can be used to process PLA. When processing PLA, use a barrel at least three to five times the shot weight, a screw with at least a 20:1 L/D ratio, and if applicable, low-shear hotrunners in the mold to prevent or reduce degradation.
Polylactic acid is available in several forms including Racemic PLLA, Regular PLLA, PDLA, and PDLLA. Their characteristics are somewhat different, but they share a similar characteristic, that they are derived from lactic acid, a renewable resource (versus conventional plastics, which come from petroleum).
As your partner, we look forward to working with you. At costs that are internationally competitive and that meet the highest quality standards, we are able to design, manufacture, and distribute injection molded PLA products.
The tool is precisely fabricated according to the validated design using Computer Numerical Control (CNC), and Electrical Discharge Machining (EDM) …
The process, however, is simple. Feed the plastic into the hopper. It melts in the barrel. Travels to the mold where it is cooled and then ejected. Then the process starts all over again. Lather, rinse, repeat. Check out the video below to see an injection molding chiller in action.
At the molding machines, a small unit called a thermolator, or temperature controller, helps to regulate the temperature of the cooling water going to the mold. While a single cooling tower or chiller can cool many molding machines, a thermolator is required at each machine. Since precise control to the molds is critical, these units are important to the overall process as well.
As a result, we offer an array of tooling, manufacturing, and shipment services to turn your biodegradable PLA injection molding concept into reality.
It is a tricky balance between the temperature of your cooling water, the quality of your plastic and profitability. If you chill the plastic too cold, it causes defects. But the faster it’s cooled and ejected from the mold, the more product that can be produced and more profit that can be made.
Molds are always optimized for certain polymers and fine-tuned to produce parts. Also, PLA molds need to be adjusted. To prevent degradation of the PLA material, you must use a hotrunner system that has a low shear without dead spots in the manifold or nozzle. A nozzle with an open channel that is externally heated should be used to prevent PLA from getting stuck in the nozzle and cause flow lines on the product, which can occur with an internally heated nozzle.
The first test shots will be sent via courier soon after the injection molds are made. Once sent, these usually arrive in 2-5 days.
At this point, Topworks makes any changes to the tool that is necessary to bring it into compliance with the approved specifications. Topworks makes any changes that are necessary (specifically excluding design changes, which are always charged for) free of charge.In this stage, the texturing process is done, which is usually the last step before mass production.Topworks side
“Steven is a very detail-oriented project manager and engineer who can solve problems creatively and also provides excellent service. It was a pleasure working with him.”
In the field of medical, China Injection Molding PLA is also widely used for devices such as disposable infusion equipment, detachable surgical sutures, and slow-release packaging agents for drugs.
For thicker walled products, cooling down time is longer than crystallization time. Consequently, crystallization time is no longer a determining factor in the rate of crystallization.
The injection of PLA in the mold will take place under high pressure. PLA is highly viscous. A defective venting system may result in (minor) flashes on the product. Initially, only minimal venting should be conducted and the machine should be opened (remove steel) as and when it becomes necessary. Molds that are not filled or areas of PLA material that are burned near venting points indicate insufficient venting and require increasing.
Topworks PLA Injection Molding Benefits– Long-lasting and safe for use– Variety of treatments available– Quick delivery– PLA plastic injection molding made to order– A one-stop service from quotation to delivery, including design, manufacturing, and sample.
There are a variety of plastics processing methods that require a plastics chiller. Whether it’s injection molding (the most common), extrusion, blow molding, lamination, or other types, these processes make a multitude of items we use in our everyday lives. For simplicity, we will only concentrate on one of these methods today. Because injection molding is the most common process, we will discuss this type of industrial HVAC product.
Topworks can optimize your design for cost savings or ensure compatibility by optimizing your design before tooling. Clients are welcome to supply 3D files
In injection molding, the plastic starts in pellet or granule form. It is dropped into a hopper where it is fed into a barrel. Inside the barrel, the plastic pellets melt and are fed towards the mold. Inside the mold, the molten plastic is cooled with either a cooling tower or chilled water. This process of cooling water is fed through many small channels within the mold.
Whether you are working with PLA injection molding copy parts already in progress or are still developing your PLA molded product, our process will streamline your product lifecycle at every stage.
Topworks is a reliable PLA injection molding company in China. With years of experience, we can provide high-quality products and services that meet your needs.
As the cooling water travels through the mold, it removes heat from the plastic, hardening it. When the cycle is complete, the mold opens and ejects the finished product. Inside these molds, plastic can be formed into a variety of shapes. You could make a garbage can, drinking cup, plastic fork, or even a computer case.
PLA is synthesized from starches, sugars, and other biomass materials when they are chemically converted and polymerized with lactic acid. Injection Molding PLA derived from bio-resources can be thermoplastically processed into highly transparent products to replace conventional disposable products and mitigate the shortage of petroleum.
Plastics made from PLA are the first commodity polymers made from renewable resources annually. By the United States Food and Drug Administration, it is generally recognized as a safe (GRAS) material that is safe for all food packaging applications. In addition to being non-toxic, nonirritating, high strength, and easy to process and mold, PLA is also biocompatible. PLA melts at 160-180 degrees and can withstand temperatures up to 150 degrees. Injection molding, foaming, and blow molding can all be done with PLA, but its toughness is not sufficient. PLA has the best mechanical properties and thermostability of any polymer.
For more information on plastics injection molding chiller systems, contact us online, call us at 281.540.2805 or visit our rental cooling equipment page.
In the quest for cost-effective, non-petroleum plastic, PLA production represents a popular approach. PLA’s versatile nature and natural decomposition make it an attractive bioplastic. If a PLA bottle is left in the ocean for 5 to 18 months, it will typically degrade.
The conveyer belt and collection box should be suitable for the purpose. In contrast to the cooling process from a melt below the glass transition temperature to a lower temperature, PLA crystallization is a slower process. In the case of thin walled products, cycle times can be longer for crystallized materials than for amorphous materials.
Topworks can utilize Computer Numerical Control (CNC) to produce a machined prototype or 3D printing that you can see and feel to validate the design of your part.Also we supply vaccum casting service
“I’m glad to inform you that all plastic parts are perfect!!! We are delighted, and therefore there are good chances to continue our relationship for any coming new project.”
This is truly remarkable in comparison to conventional plastics, which can degrade within a few hundred to a thousand years in the same environment. In summary, PLA has a high potential for being useful in applications with short lifespans where biodegradability is highly desired (e.g. a plastic water bottle or a fruit and vegetable container). Despite its ability to degrade over time when exposed to the elements, PLA is extremely robust in any typical application (e.g. as a plastic electronics part).
A stiff material like PLA can result in sharp flashes. Ventilation should be designed so that it is close to the place where it is needed, while at the same time ensuring that it does not take place where flashing is prohibited. Heat-resistant PLA products require more crystallization in the mold, so they shrink more than standard PLA products.For PLA products with tight dimensional specifications, designers should take this into consideration when developing molds. Create a mold so that steel can be removed at any place where it is needed after the first reproducible injection molding trial.
The injected material is cooled off as soon as possible in a cold mold, which produces amorphous PLA. When a PLA product has a higher temperature resistance, the mold temperature should be set at 90-100°C, which will allow the material to crystallize during cooling, resulting in a semicrystalline structure. It depends on the PLA formulation, mold temperature, and part design how long it takes to achieve maximum crystallinity within a mold during the crystallization phase, but it is usually longer than it takes to cool down PLA in a cold mold. Semi-crystalline products are therefore subject to longer cycle times. At 100°C, it becomes stiff enough to eject from the mold without deforming due to its semi-crystalline PLA structure. While the product is still somewhat flexible, it has not yet reached the glass transition temperature of PLA, which is around 55°C.
Injection molding of PLA offers several benefits– Degradable by microorganisms, minimal environmental impact after use– Excellent mechanical and Physico-chemical properties– Easily processed, useful, and suitable for blow molding, melt processing, and a variety of other processes– Compatible and degradable– Glamorous and transparent– Superior tensile and ductile strength– Permeance to air and oxygen
PLA(Polylactic Acid) is a naturally occurring plastic made of corn starch that is high in hygroscopicity and easy to absorb water from the air. PLA is an ideal material for use in thermoplastic injection molding, extrusion, films, 3D printing, and almost any process associated with the manufacture of thermoplastic components due to its ability to naturally break down and regenerate. Different industries can use PLA plastics to make PLA molded parts for many different applications.
Using the right mold temperature is essential for obtaining the shortest cycle time, especially for semi-crystalline products. The temperature of the mold should therefore be measured at different places with an internal or external thermocouple. If the mold heater temperature (return) is within the proper range, the mold temperature may still not be the correct one due to heat losses. It is important to ensure that the semi-crystalline or amorphous product is not deformed after ejection from the mold.
GETTING A QUOTE WITH LK-MOULD IS FREE AND SIMPLE.
FIND MORE OF OUR SERVICES:
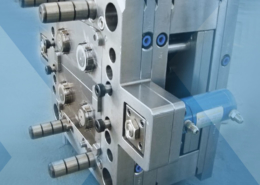
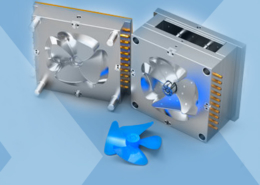
Plastic Molding

Rapid Prototyping
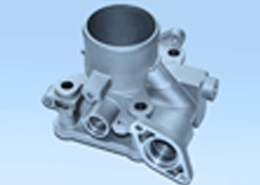
Pressure Die Casting
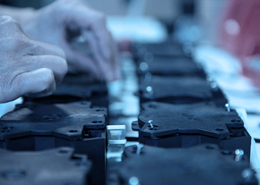
Parts Assembly
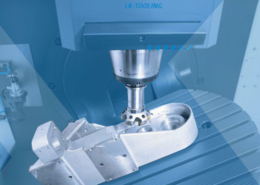