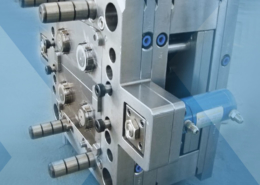
Unraveling the Dynamics of High Volume Injection Molding
Author:gly Date: 2024-06-08
High volume injection molding stands as a cornerstone in modern manufacturing, enabling the efficient production of large quantities of plastic components with precision and reliability. This article aims to capture readers' interest by introducing the concept of high volume injection molding and providing background information on its significance in various industries.
Introduction to High Volume Injection Molding
High volume injection molding is a manufacturing process that involves the mass production of plastic parts using injection molding machines. It is characterized by its ability to produce large quantities of parts quickly and cost-effectively, making it a preferred choice for industries such as automotive, electronics, consumer goods, and medical devices.
Advantages of High Volume Injection Molding
High volume injection molding offers several advantages over other manufacturing processes.
Efficiency and Cost-Effectiveness
One of the primary benefits of high volume injection molding is its efficiency and cost-effectiveness. By producing large quantities of parts in a single production run, manufacturers can achieve economies of scale, reduce per-unit costs, and remain competitive in the marketplace.
Consistency and Precision
High volume injection molding ensures consistent part quality and precision, thanks to advanced molding techniques, automated processes, and rigorous quality control measures. This consistency is essential for applications requiring tight tolerances and dimensional accuracy.
Flexibility and Versatility
Despite its high volume capabilities, injection molding offers flexibility and versatility in part design, materials, and finishes. Manufacturers can easily adjust production parameters to accommodate changes in customer requirements, market demands, or design iterations.
Process Overview
The process of high volume injection molding involves several key steps, from mold design to part production.
Mold Design
The first step in high volume injection molding is designing the mold, which determines the shape, size, and features of the final part. Mold design considerations include part geometry, gating system, cooling channels, and ejection mechanisms.
Material Selection
Once the mold design is finalized, the next step is selecting the appropriate material for the intended application. Factors such as mechanical properties, chemical resistance, and cost are taken into account when choosing the optimal material for high volume production.
Injection Molding
The injection molding process begins with the melting of plastic resin pellets in the barrel of an injection molding machine. The molten material is then injected into the mold cavity under high pressure, where it cools and solidifies to form the desired part. After cooling, the mold opens, and the molded part is ejected, trimmed, and finished as needed.
Applications
High volume injection molding finds applications across various industries, where its efficiency and scalability make it an attractive option for mass production.
Automotive
In the automotive industry, high volume injection molding is used to produce a wide range of components, including interior trim, exterior body panels, under-the-hood parts, and functional prototypes. Its ability to meet strict quality standards and tight production schedules makes it indispensable for automotive manufacturers.
Electronics
In the electronics industry, high volume injection molding is utilized for the production of enclosures, connectors, housings, and other components for electronic devices. Its precision, repeatability, and cost-effectiveness make it ideal for meeting the demanding requirements of the electronics market.
Consumer Goods
High volume injection molding is also prevalent in the production of consumer goods such as toys, appliances, packaging, and household products. Its ability to produce complex shapes, vibrant colors, and durable finishes allows manufacturers to create innovative and appealing products for consumers worldwide.
Future Directions
Looking ahead, the future of high volume injection molding is poised for continued growth and innovation.
Advancements in Materials and Technology
Ongoing research and development efforts are expected to lead to advancements in materials, additives, and processing technologies, further enhancing the capabilities and performance of high volume injection molding.
Integration of Automation and Industry 4.0
The integration of automation, robotics, and digitalization is likely to transform the landscape of high volume injection molding, leading to increased productivity, efficiency, and connectivity across the manufacturing process.
Conclusion
In conclusion, high volume injection molding plays a vital role in modern manufacturing, enabling the efficient production of large quantities of plastic parts with precision and reliability. By understanding the intricacies of the injection molding process and embracing its potential, manufacturers can unlock new opportunities for productivity, innovation, and market competitiveness. As technology continues to evolve and market demands evolve, high volume injection molding will remain a cornerstone in the manufacturing landscape, driving continuous improvement and shaping the future of industry.
GETTING A QUOTE WITH LK-MOULD IS FREE AND SIMPLE.
FIND MORE OF OUR SERVICES:
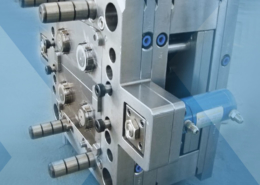
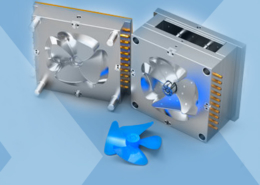
Plastic Molding

Rapid Prototyping
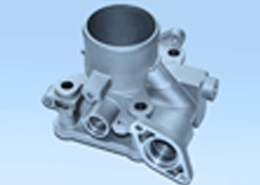
Pressure Die Casting
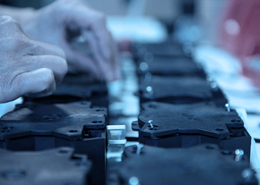
Parts Assembly
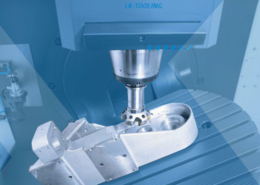