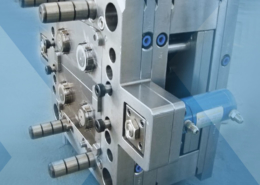
A comprehensive introduction to PVC injection molding - pvc injection
Author:gly Date: 2024-10-15
The PVC injection molding process requires careful consideration of various factors including the injection mold, temperature settings, and pressure.
PVC has a molding shrinkage rate of between 0.6% and 1.5%, hence the product must have a certain degree of draft angle, typically between 0.5° to 1°, to ensure adequate venting within the mold cavity.
Part volume and cavities: Part volume refers to the cavity size of a mold. The more cavities or cavity volume a mold requires the longer the press time. Increased press time slows down the production process which leads to increased cost.
In the manufacturing of automotive parts, PVC injection molding is utilized for components such as dashboards, interior panels, and weather strips because of its durability and smooth finish.
Setup/configuration cost: The setup labor focuses on the time taken to configure the utilized equipment to produce the mold and the finished product.
Use 3D printed injection molds with both benchtop and industrial machines to efficiently and affordably produce hundreds to thousands of functional prototypes, parts to accelerate product development, reduce costs and lead times, and bring better products to market.
One of the advantages of using PVC for injection molding is that this material has very low shrinkage. The shrinkage while molding amounts to 0.002 – 0.006 mm/mm, which is just 0.2 – 0.6%.
For an injection mold, the mold making process uses the liquified PVC through an injection. This custom mold has two sides. After the liquid has cooled, it is allowed to dry to set fully. The post-processing includes final touches that might need to be made.
The equipment associated with injection molding is generally self-regulating and relies on automation to get the job done. CNC machines, EDM machines, and 3D printers rely on the specifications of the CAD design to produce a mold. The injection molding machine also relies on automation to inject materials into the mold, and industrial IM machines often cool and eject the finished item autonomously.
Producing low volumes of parts with injection molding is the most cost-effective with smaller desktop injection molding machines and 3D printed molds. If you are new to injection molding and are looking into testing it with limited investment, using a benchtop manual injection molding machine such as the Holipress or the Galomb Model-B100 could be a good option. Automated small-scale injection molding equipment such as the desktop machine Micromolder or the hydraulic machine Babyplast 10/12 are good alternatives for medium-series production of small parts.
The table below highlights the cost associated with injection molding a hypothetical plastic item, such as a small enclosure of an electronic device, which makes the cost dynamics of injection molding easier to understand:
Embrace the use of self-mating parts to reduce the need to create multiple molds when one universal mold can be used to achieve similar results.
Due to the lower molding temperature, to prevent cold material from clogging the gate or flowing into the mold cavity, sufficient cold slug wells should be created at the end of the main runner and also for longer sub-runners.
Simple low-volume 3D printed molds can cost as little as $100, while the cost of designing and manufacturing complex molds for high-volume production may hit the $100,000 mark. Despite the considerable fixed start-up costs, the injection molding process has low variable costs due to the inexpensive thermoplastics materials, short cycle times, and the labor needs decrease progressively due to automation and economies of scale. This means that the variable costs of production are low and the process becomes more efficient and the cost per part decreases at higher volumes as the costs get distributed among hundreds or thousands of parts.
It is important to note that a majority of the injection molding process is dedicated to cooling. The quicker a mold cools down the faster the injected material solidifies and the faster the production cycle can be repeated. Thus, cooling channels play an important role, especially for high-volume production, and should be included in the design of the mold. For low-volume production with 3D printed molds, manual cooling using compressed air is an option.
Part size: The larger the item or part to be molded, the larger its mold will be to accommodate the part. Larger parts tend to require more injected materials to complete production cycles. Larger mold designs usually come at an increased cost compared to fabricating the same design but with smaller dimensions.
Simple low-volume 3D printed molds can be produced on an SLA 3D printer for as little as $100. An aluminum mold for a mid-volume production run of approximately 1,000-5,000 units falls within the range of $2,000 to $5,000. For molds with more complex geometries and primed for larger production runs of approximately 10,000+ units, the cost of mold can range from $5,000 to $100,000.
Understanding the different types of costs associated with injection molding requires an in-depth analysis of the process.
Download our white paper for guidelines for using 3D printed molds in the injection molding process to lower costs and lead time and see real-life case studies with Braskem, Holimaker, and Novus Applications.
To shorten the injection molding cycle for PVC, the mold’s injection gate should be as short as possible with a circular cross-section.
Many household items, ranging from containers to furniture parts, can be made using PVC injection molding. For instance, the strength and weather-resistance of PVC make it suitable for door and window frames, ensuring they remain intact in extreme weather conditions.
Large industrial injection molding machines can cost anywhere from $50,000 to $200,000+. These machines also come with more stringent facility requirements and require skilled labor for operation, maintenance, and monitoring. As a result, unless injection molding is a core competence, most enterprises outsource mass production to service providers and contract manufacturers, in which case the equipment costs are included in the service costs.
Both polyvinyl chloride and PVC are well-known names of this thermoplastic polymer. This polymer is strong but can prove brittle until elasticity is added by infusing it with plasticizers—the B.F. Goodrich Company was the first organization that made use of this compound commercially in the 1920s. Polyvinyl chloride is used in both its flexible and rigid forms. PVC infused with plasticizers can bend, whereas the rigid form is primarily used for industrial purposes where durability and stability take priority.
Normally, the main cost driver in injection molding is the cost of the mold, also known as the tooling cost. The cost of designing and building a mold depends on the required production volume, the complexity of the part design, mold material, and the process used to create the mold.
Injection molding with Polyvinyl Chloride (PVC) is a popular process for manufacturing a wide range of products. Here are the advantages and disadvantages associated with PVC injection molding:
This design prevents semi-solid materials that are poorly melted from entering the mold cavity, which could affect the surface finish and strength of the product.
Polyvinyl chloride or PVC is an industrial thermoplastic. This material is extensively used across industries for a variety of purposes. Because of its flexibility which ranges from soft and hard to rigid, PVC finds uses in many different ways. PVC is a strong compound and has commendable durability, which makes it ideal for pipes and injection molding.
When producing in-house, these costs are calculated into the labor costs. When a business outsources injection molding, the labor and the markup of the service provider are added to the service cost.
In this video, we've partnered with injection molding service provider Multiplus to walk you through the steps of the injection molding process using 3D printed molds.
ACIS®, Autodesk Inventor®, CATIA® V5,Creo™ Parametric, IGES, Parasolid®, Pro/ENGINEER®,Siemens PLM Software’s NX™, SolidEdge®, SolidWorks®, STEP
It is a fast, intensive process where high heat and pressure are involved to inject molten material inside a mold. The molten material depends on the scope of the manufacturing project. The most popular materials are various thermoplastics, such as ABS, PS, PE, PC, PP, or TPU, but metals and ceramics can be injection molded as well. The mold consists of a cavity that accommodates the injected molten material and is designed to closely mirror the final features of a part.
Part design: Complex part designs with intricate geometries require complex molds to execute the project. Mold designs usually have 2 sides: sides A and B. Side A, also known as the cosmetic side, is usually the side seen by the user. Side A is expected to be smooth and aesthetically pleasing. Side B contains the hidden structures that support the usage of the part. Side B structure may include ribs, bosses, etc., and its finish is usually much rougher than that of Side A. Molds with complex Side A and Side B designs are generally more expensive to fabricate compared to simpler molds. Complex designs that feature undercuts might also require sliding side-actions and cores, increasing the cost of the mold.
The compound is also very resistant to chemicals, flames, and abrasion. PVC is in great demand at any given point in time. The right manufacturer for injection molding who makes use of polyvinyl chloride is important. Any manufacturer will tell you that because of PVC’s dimensional stability, it is an excellent choice for injection molding.
PVC initially comes in the form of powder or granules, which need to be melted before they can be processed. The granules are placed into a barrel and heated. During the heating process, plasticizers might be added to the mixture to enhance fluidity, lubricants for better demolding, and stabilizers to increase thermal stability.
During the injection molding process, excessively high processing temperatures can accelerate the degradation of PVC, leading to the release of harmful gases that may pose a danger to the machinery. Corrosive compounds might corrode or damage certain parts of the injection molding machine, resulting in potential malfunctions and increased maintenance costs.
Monitoring costs: Despite the reliance on automation, equipment operators are expected to monitor the progress of the injection molding process. Operator wages accrued during the process are added to the total cost of injection molding.
Owing to its excellent insulating properties, PVC is employed in molding electrical components like wire insulation, conduits, and connectors.
Online injection molding cost estimators or quotes from injection molding service providers can provide benchmarks and help you estimate the cost of injection molding specific parts.
Apply a core cavity approach that simplifies the design of Side B of a mold. The core cavity approach involves sinking the wall cavities into the mold base, thereby reducing the need to mold steep draft angles while improving surface finish.
The cost of purchasing materials for molds differs according to the material chosen. Thermoplastic pellets cost approximately $1 to $5 per kg.
One of the most extensive applications of PVC injection molding is the production of pipes and related fittings. Due to their corrosion resistance and chemical resistance, these PVC pipes are widely used in plumbing, drainage, and sewage systems.
Polyvinyl chloride is a popularly used polymer because of its innumerable advantages that range from inexpensiveness to greater accessibility. Apart from these, there are many properties of polyvinyl chloride that can be taken advantage of by manufacturers for plastic injection molding service and otherwise alike. These are listed as follows:
Products made from injection molded PVC are known for their resilience. They exhibit strong resistance against corrosive elements, degradation from chemicals, and the effects of weathering. As a result, PVC products often promise long-term functionality and reliability.
Developing more complex molds requires technical expertise. As a result, enterprises often outsource specific aspects of the injection molding process such as the design and fabrication of the mold.
When burned, PVC can release dioxins and chlorine, harmful to both the environment and human health.Moreover, injection-molded products using polyvinyl chloride are not easily biodegradable, leading to the growing problem of plastic waste.
A molding cost comparison table also serves a similar purpose. Injection molding service providers use cost comparison tables to provide prospective customers with a rough estimate of the process.
Mid-volume production is the most efficient with machined aluminum molds that have a lower cost than traditional steel mold, but are durable enough to last a few thousand shots, depending on factors like the material and the design. In most cases, low-volume injection molding is only reasonable with 3D printed molds—in our example, if we were to use an aluminum mold to produce 100 parts, its cost would account for $30 for each part, while a traditional steel mold would mean $200 for each part.
In this guide, we provide an extensive breakdown of the different factors that make up the total injection molding cost.
Repair cost: Repair and maintenance tasks involve the replacement of defective parts and the use of tools to execute the maintenance process.
Evaluate the model’s design to eliminate unnecessary features. This reduces the mold’s size and the material used to develop the model.
Polyvinyl chloride has a high tensile strength which is why it is chosen for its strength and durability in a variety of applications. Whether it is mold making, overmolding, or manufacturing other products, PVC is versatile because it can be heated and molded into any shape possible.
Tooling costs for injection molding are very high and depend on a number of parameters and design complexity. Molds for injection molding are normally CNC machined out of aluminum or tool steel, EDM machined to shape a workpiece, or 3D printed. The machined or printed part is then finished to achieve the desired standard. The finished mold consists of features such as the surface geometries needed for a part, a runner system to guide the flow of injected materials, and cooling channels to ensure the mold cools down quickly.
The three scenarios in the table show the methods and the mold types that result in the lowest cost per part depending on the production volume.
3D printing: 3D printing is a powerful solution to fabricate injection molds rapidly and at a low cost. It requires very limited equipment, saving CNC time and skilled operators for other high-value tasks in the meantime. Manufacturers can benefit from the speed and flexibility of in-house 3D printing to create molds that can be used on both desktop and industrial molding machines. Furthermore, product development benefits from the ability to iterate on the design and test the end-use material before investing in hard tooling for mass production. Stereolithography (SLA) 3D printing technology is a great choice for injection molding. It is characterized by a smooth surface finish and high precision that the mold will transfer to the final part and that also facilitates demolding. 3D prints produced by stereolithography are chemically bonded such that they are fully dense and isotropic. Desktop SLA printers, like those offered by Formlabs, start below $5,000 and can seamlessly be integrated into any injection molding workflow as they are easy to implement, operate, and maintain.
Evaluate the CAD model to determine its feasibility before undertaking an injection molding project. Eliminate potential bottlenecks such as steep angles, undercuts, and other complex geometries.
Once the PVC is in a molten state, the machine’s screw pushes it forward, injecting the PVC into the mold cavity. For injection molding, the mold is made by injecting liquefied PVC. This custom mold has two parts.
Electrical discharge machining (EDM): The EDM method is generally used to create highly complex mold designs that cannot be easily reproduced using standard machining methods. EDM involves the use of a workpiece and a tool electrode to create the desired mold shape. The tool electrode and workpiece electrode are separated by a dielectric fluid and subjected to voltages that cause recurring current discharges. The discharges are responsible for shaping the workpiece electrode into the final mold. EDM is highly accurate and does not generally require any additional post-processing. Similar to CNC machining, EDM is also an industrial process that many companies outsource to machine shops.
For enterprises with the equipment and tools for injection molding, choosing to create molds in-house could be the least expensive option if the technical know-how is also available. If the tools needed for injection molding are not readily available, then outsourcing reduces the cost associated with developing a mold.
Production volume: The number of items to be produced using injection molding determines the production technology and the quality of material to use when creating the mold. Low volume projects might require 3D printed or lower-grade machined aluminum molds, while large production volumes will require high-grade steel molds or even multiple molds to manage the process without wear and tear affecting the quality of produced items. This affects the cost of the mold, but of course, the increased cost of high volume molds is distributed among more parts, which normally leads to a lower per part cost.
Stay updated with the latest 3D printing news, interviews with experts from around the world and tutorials on how to leverage 3D printing.
However, too fast an injection rate can cause poor venting, leading to more frictional heat, which can burn the plastic or cause color changes.
CNC machining: CNC machines are the most commonly used tools for manufacturing aluminum and stainless steel molds with high precision levels. CNC machining removes material by a spinning tool and fixed part. Machining can produce molds where the cavity design is highly complex, but they might require multiple tool changes that can slow down the process, which means that costs increase in line with complexity. CNC machines are industrial tools that require a skilled workforce and a dedicated space, which means that many companies outsource mold production to service providers.
The cost of the mold is largely defined by the complexity and the amount of time it takes to produce it. We advise adhering to design for manufacturing principles to drive down part costs with injection molding.
The material can also be reheated and remolded over time over and over without any degradation to its chemical properties, which is why it is one of the most easily available recyclable plastics. Injection molding is a great use of polyvinyl chloride because it can be liquified and hence can be used in injection molding. Industrial applications are common uses of PVC because of its lasting properties.
The short answer: plastic injection molds cost anywhere between $100 for a 3D printed low-volume injection mold to $100,000+ for a complex multi-cavity steel mold for high-volume production, which generally represents the most significant fixed start-up cost in injection molding. However, as these costs get distributed among hundreds or thousands of parts, injection molding is an ideal process to mass-produce plastic parts affordably.
Injection molding is one of the leading processes for manufacturing plastics. It is widely used for mass-producing identical parts with tight tolerances. It is a cost-effective and extremely repeatable technology that yields high-quality parts for large series production.
The temperature distribution along the barrel is usually arranged in a stepwise fashion; the nozzle temperature should be 10-20°C lower than the temperature at the end of the barrel.
PVC can be easily molded into a variety of items,This includes everything from soft toys that require flexibility to rigid and robust structures like pipes.Another dimension of its versatility is its ability to be dyed in any desired color, allowing for a wide range of aesthetic choices and applications.
The properties of PVC do not undergo any change or degradation when the material is heated and reheated for molding repeatedly in case of change in mould design.
While injection molding is traditionally considered a manufacturing process only for mass production due to its high tooling costs, leveraging 3D printing to fabricate injection molds empower you to use this process to produce high-quality and repeatable parts for prototyping and low-volume production.
Polyvinyl chloride is a durable and favorable material for manufacturing because of its high melting point. The melting point of PVC falls in the range of 212°F to 500°F as the type may vary depending on the infusion of other materials.
It’s important to monitor the speed of the screw; too high a speed can lead to excessive shear heat, causing the PVC to overheat and degrade, producing water and carbon dioxide. Therefore, the screw speed should be controlled between 50-70rpm in PVC injection moulding.
Special-purpose machines are used for injection molding that can range from smaller desktop injection molding machines that businesses can use in-house to large industrial injection molding machines that are mostly operated by service providers, contract manufacturers, and large manufacturers.
PVC often provides a more affordable alternative compared to other materials when it comes to injection molding. This cost-effectiveness becomes even more pronounced in high-volume production where economies of scale come into play.
A 3D printer nozzle specially catering to PVC has been developed, but manufacturers still prefer materials like ABS and PLA when it comes to 3D printing.
* Equipment costs are not calculated into the production costs in this example as the cost of these tools can be distributed among multiple projects. Purchasing a desktop injection molding machine and an SLA 3D printer allows businesses to get started with injection molding for less than $10,000.
The many additives that can be added to polyvinyl chloride include fillers, stabilizers, lubricants, plasticizers, pigments, processing aids, and impact modifiers. The polymers can be joined together either through rubber or through solvent cement.
Apart from these advantages, there are also some disadvantages that come with the manufacture and decomposition of polyvinyl chloride.
This white paper showcases the cost-dynamics for real-life use cases, and presents guidelines for using SLS 3D printing, injection molding, or both.
In general, injection molding is the most efficient at higher volumes, as the costs then get distributed among thousands of parts. But even though the cost per part for low-volume injection molding is slightly higher, it is still substantially more affordable for low-volume production than other manufacturing methods.
In this white paper, learn how to combine rapid tooling with traditional manufacturing processes like injection molding, thermoforming, or casting.
Some examples of the flexible type of polyvinyl chloride include insulation for electrical wires and cables, flooring for homes, and in some cases, a replacement for rubber. The rigid type of PVC is used on a larger scale as plumbing pipes, vinyl siding on buildings, and business machine housing.
In general, PVC contains additives such as phthalates, which can be dangerous to human health during the injection molding process, especially when used in contact with food or the body.
Too high back pressure can create excessive shear force, leading to the overheating and decomposition of PVC during the melting process.
A wide variety of plastics can be used for injection molding depending on the requirements of the final parts, including ABS, PS, PE, PC, PP, or TPU.
Material cost is defined by a model’s design, the material chosen, and the amount of material used to execute the injection molding process.
GETTING A QUOTE WITH LK-MOULD IS FREE AND SIMPLE.
FIND MORE OF OUR SERVICES:
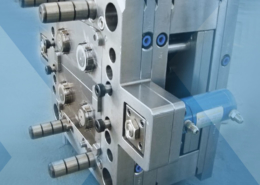
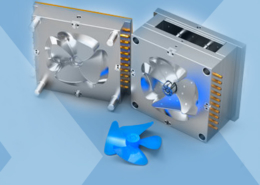
Plastic Molding

Rapid Prototyping
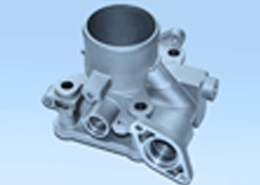
Pressure Die Casting
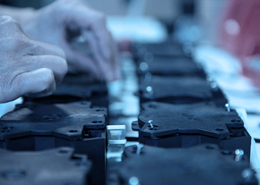
Parts Assembly
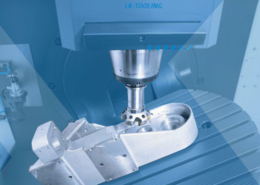