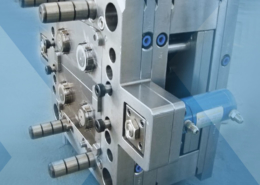
A comprehensive introduction to PVC injection molding - pvc injection molding
Author:gly Date: 2024-10-15
You have some questions? Upload your drawings or documents, and we have professional technicians to answer them for you.
Nylon, also known as polyamide, is a popular thermoplastic renowned for its high strength, toughness, and excellent wear resistance. The molding temperature typically ranges from 446°F to 572°F, depending on the specific type of nylon being processed.
Situation when the angle between slide core pulling direction and parting surface is slider pulling direction fixed-die.
When the angle situation between the slider core pulling and the parting surface is called the slider pulling direction moving-die.
Polyethylene is a thermoplastic polymer known for its excellent chemical resistance, low cost, and ease of processing. Melt temperatures start around 375 F, but generally have a wide range from there. PE is categorized into different types based on its density. Low-density polyethylene (LDPE), high-density polyethylene (HDPE), and ultra-high-molecular-weight polyethylene (UHMWPE).
g. It is best to have fixed block on the front of pole, easy to adjust and processing, consist three point bearing, increase the strength of pulling block.
a. Assemble requirements: assemble the slider insert and inclined insert hole, it should notice the relationship between the size A and A1, should be A>A1.
CNC machining optionsStainless steels MenuStainless steelsRelated LinksFinishing OptionsCNC Materials MenuFinishing OptionsCNC Materials
PET is a strong, lightweight thermoplastic with a relatively high melt temperature, typically around 500°F to 554°F. Although these melt temperatures are achievable on most molding machines, the molds themselves often require running at temperatures above 212 degrees F. Hot oil temperature controllers may be required when using injection molding materials like this.
Polystyrene is a widely used thermoplastic with a melt temperature typically around 356°F to 464°F. This ensures efficient processing inside the injection molding equipment. It is known for its transparency, ease of molding, and affordability. PS can be categorized into two main types: general-purpose polystyrene (GPPS) and high-impact polystyrene (HIPS). PS is prone to cracking instead of deforming.
How slider head insert connected is controlled by end product. Different end products have different connecting methods.
3D Printing options3D printing materials Menu3D printing materials3D Printing LinksThe application of 3D printing in the laryngoscope mold3D printing raise the manufacturing capacityHow much should you pay for your 3D printing components? MenuThe application of 3D printing in the laryngoscope mold3D printing raise the manufacturing capacityHow much should you pay for your 3D printing components?
Polyvinyl chloride is a thermoplastic polymer known for its excellent chemical resistance and flame retardancy. It’s typical molding temperature ranges from 320°F to 410°F, allowing for the production of a wide range of products.
If you’re unsure what material is best, contact us to consult with one of our material experts. We’ll ensure you choose the most suitable material that aligns with your project goals and other requirements. With the right material and proper molding technique, you can create high-quality, durable products that meet or exceed your expectations.
Due to the undercut surface of the end product is tilt, so the move direction of slider should follow the direction of end products’ undercut surface, otherwise it will cause damages when pulling the end product.
Die casting optionsAluminium die castingZinc Die castingGravity CastingLow-pressure die casting MenuAluminium die castingZinc Die castingGravity CastingLow-pressure die castingRelated LinksDie casting Tolerance5G productsAutomobile gearboxMaterials for die castings MenuDie casting Tolerance5G productsAutomobile gearboxMaterials for die castings
There is a huge pressure during the molding machine injection process. To avoid affecting the side and appearance(eg. burrs) of end products, we should keep the slider and core unmoved when molding machine injection. So the slider should use locking fixed method to keep it stay. normally, this part is motion-stoping block or heel.
c. There should has taper on SPRUE BUSHING head to fit for clamping and should be on the top clamping plate to avoid brush nozzle on the molding machine separating from SPRUE BUSHING and then result in brush, which is inconvenient to take out and affects next injection.
After cooling, the plastic will be narrowing and shortening, including the die core and the other parts (like oblique tip, slider, insert etc)Therefore, we must consider the enclosed strength that end product impact on slider, stress state, see pic on the right
The diameter of diagonal bracing tip is affected by many factors, like obliquity, length, and required de-molding distance. Thus, in designing, some parameters should be adjusted and matched to obtain the best result to make sure the slider to move smoothly. Calculation formula:
a.bottom wearable plate needs bevel, reduce loss between slide block and core plate, normally takes 1.5˚~3˚, assemble location be at the 3 / 4 of the center of gravity of the slide block.
Injection molding optionsClear Plastic MoldingInsert MoldingOver MoldingThreaded plastic productsCases for soft rubber mold MenuClear Plastic MoldingInsert MoldingOver MoldingThreaded plastic productsCases for soft rubber moldRelated LinksInjection materialsInjection Molding ToleranceInject Design TipsFinishing OptionsColor card MenuInjection materialsInjection Molding ToleranceInject Design TipsFinishing OptionsColor card
S=(L1xsina-δ)/cosα(δ – the space between taper pin and slider, normally is 0.5MM,L1is the taper pin vertical distance inside the slider)
n. Explosive slide block must have shoulder (wings for fixing) to provide convenience for grouping mold and also a base level is necessary, cannot reduce the material)
Generally, forming on the cavity side and large slider forming area, especially using slider when the cavity side is very deep.
PBT is another commonly used thermoplastic for injection molding. Its molding temperature range is 428°F to 500°F, allowing for efficient processing in various injection molding machines.
Undercuts treatment uses the mold opening movement and ejection force to causes the tendency of relatively motion between angle pin and slider. There are two movements to make it separate from the undercut : mold opening direction & horizontal direction. As the below pic shows:
This website uses cookies to improve your experience while you navigate through the website. Out of these cookies, the cookies that are categorized as necessary are stored on your browser as they are essential for the working of basic functionalities of the website.
a. Thickness of top clamping plate H2≧1.5D (D – diameter of large tie rod; hyperlink of large tie rod diameter calculation, three play mold large tie rod calculation; H2- thickness of top clamping plate).
Office:1602, Unit 8, Building 2, Shangxing Commercial Street, Shangde Road, Xinqiao Street, Baoan District, Shenzhen City 518125
e.The wearable plate should be 0.5mm higher than master mold plate to protect the taste mold plate and support the support pulling block to prevent it from distorting due to the external force.
Generally, for thick and deep products’ wall, the side of the wall has many core pulling holes. The core pulling force is strong, so when moving the slide block, the product might be distorted or scratched. To avoid these happening, we need to place the ejector pin inside the slide block to stop the distortion or scratches.
PPS is a high-performance thermoplastic known for its exceptional chemical resistance, flame retardancy, and high-temperature stability. It has a molding temperature around 536°F to 626°F. Although these melt temperatures are achievable on most molding machines, the molds themselves often require running at temperatures above 212 degrees F. Hot oil temperature controllers may be required.
Polycarbonate is a transparent thermoplastic known for its exceptional impact resistance, optical clarity, and high-temperature resistance. PC should reach a molding temperature around 518°F to 608°F, ensuring the material flows smoothly into the mold cavities.
One of the most important decisions you’ll make is selecting the appropriate injection molding materials for your part. Material selection significantly influences your product’s performance, durability, and cost. In this guide, we explore the most common materials, their strengths, molding temperatures, common applications, and other important properties. By the end of this guide, you’ll be able to make an informed decision for your project.
Polypropylene is a versatile thermoplastic known for its excellent chemical resistance. It has a melt temperature from 320°F to 464°F, making it suitable for both low and high-volume production processes.
m. The slide block head must have datum plane to provide convenience for grouping mold. The processing base level is normally over 8mm.
I. When assembling slide base and pulling block, need to notice about the relationship between size B and B1, it shoulbe B>B1, while in order to assemble smoothly, can also dig through the rear mold located after the slide base.
Factory1:NO. 101,Building 21, Zone B, Yuanshan Industrial Zone, Shangcun Community, Gongming Street, Guangming District, Shenzhen City, Guangdong Province, China
POM, also known as acetal, is a high-performance engineering thermoplastic with excellent dimensional stability and low friction. Its molding temperature ranges from 347°F to 410°F. This is critical to achieve desired flow consistency during injection molding.
PMMA, commonly known as acrylic, is a transparent thermoplastic known for its optical clarity, UV resistance, and weatherability. Its molding temperature is on the lower end when compared to other injection molding materials. Typically molded around 464°F to 518°F, this allows it to be processed in a variety of molding machines.
Sheet metal optionsBending sheet metal processingConsiderations of the sheet metal parts design MenuBending sheet metal processingConsiderations of the sheet metal parts designRelated LinksSheet metal materials MenuSheet metal materials
The slider will move a certain distance in mold opening. One way to make the slider return back smoothly is to use equipment to fix it and it should be flexible and stable so that the slider will stay at where it should be. Some exceptional situations do not need fixed equipments, like left to right slider, so it is suggested to apply a fixed equipment.
Undercut forming on the side of master mold. No marks allowed on appearance. Need to switch to master mold runner slider.
The size of pulling block section checking is as same as the calculation of diagonal bracing tip. It only needs to alter the last step. Formula:
Selecting the right injection molding materials can make or break your injection molding project. As you can see, each material has its unique properties, advantages, and limitations. Remember, the material you choose not only impacts the performance of the final product but also manufacturing costs and the environment.
Finishing Services optionsAnodic OxidationSandblastingPlastic ElectroplatingMetal Electroplating MenuAnodic OxidationSandblastingPlastic ElectroplatingMetal ElectroplatingRelated LinksSecondary processing MenuSecondary processing
ABS is a thermoplastic polymer known for its exceptional impact resistance, toughness, and dimensional stability. It has a molding temperature around 410°F to 527°F, which ensures proper flow and mold filling during injection molding.
In the slide guiding, the slider must be smooth and stable so that no stutters or beats, which will affect the aspects, like quality and service life of mold. (Link for the specifications of platen)
1. Application range of oblique slider Normally applied in the products with slider structure, at the same time, along the slider’s direction, the end product also has undercut, which indicates that we can apply oblique slider.
GETTING A QUOTE WITH LK-MOULD IS FREE AND SIMPLE.
FIND MORE OF OUR SERVICES:
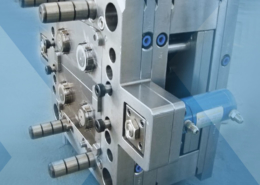
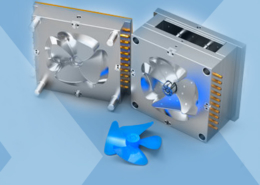
Plastic Molding

Rapid Prototyping
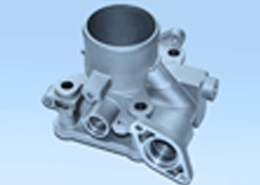
Pressure Die Casting
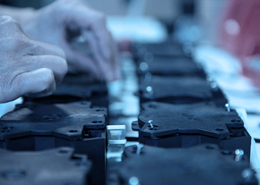
Parts Assembly
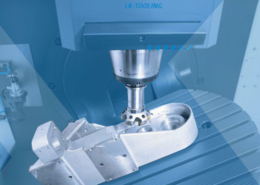