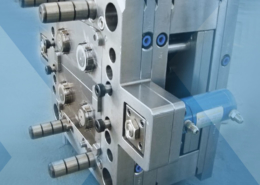
A Comprehensive Guide For PP Injection Molding - pp mold
Author:gly Date: 2024-10-15
The applications of PEEK range from medical to aerospace to machinery. Below is a list of some of its applications. Most of which are injection molded (tubings and Profiles use extrusion in most cases).
Today, with the internationalization of the market and the diversification of customer needs, our company has always adhered to the attitude of taking the forming site as the starting point, relying on the professional technical strength accumulated since the establishment of the company, and adopting the one-to-one implementation strategy to solve various problems with customers. .
Many polymers have certain properties that make them stand out from other polymers. Indeed it is possible that polymers are the most diverse class of materials. There are those polymers that have exceptional properties that demand further consideration. Both in their processing as well as their applications. One of such is PEEK. Let’s begin here with some of its properties that make it great in applications.
In addition, in many cases, they will be classified by the function or application of the injection molding machine, such as our common PET preform injection molding machine, PVC Pipe injection molding machine, etc. Plastic Injection molding machine manufacturers usually prepare or customize corresponding injection molding solutions for you. You can ask your intended manufacturer in detail.
Since there are many types of injection molding machines, it is necessary to correctly judge which type of injection molding machine or series should be used to produce the product, such as general thermoplastic or bakelite or PET material, single color, double color, multi-color-color, sandwich or mixed color . In addition, some products require conditions such as high stability (closed circuit), high precision, ultra-high injection speed, high injection pressure or rapid production (multi-circuit), and the appropriate series must also be selected for production.
After getting the above information, you can follow the steps below to choose a suitable plastic injection molding machine
Servo injection molding machines claim to take advantage of the best features of both hydraulic and electric systems, but in actuality use almost the same amount of electricity to operate as an electric injection molding machine depending on the manufacturer.
Headquarters and main manufacturing facilities are located in Canada, with additional manufacturing facilities in the United States, Luxembourg, Switzerland, China and the Czech Republic. In addition, three technical centers in Japan, Luxembourg and Shanghai, as well as a worldwide network of locations.
Shibaura Machinery is a well-known manufacturer and solutions provider of plastic injection molding machines, Shibaura designs and manufactures industrial machines and solutions to provide customers with optimum productivity and profitability, and to provide excellent service and support to maximize their return on investment . To pursue this goal, conduct business in a responsible and respectful manner, contribute to the industrial base, and help create a high-quality society through the continuous development of innovative technologies with a focus on mechanics, electronics and systems.
Some engineering plastics require higher injection pressure and suitable screw compression ratio design to have better molding effect, so in order to make the finished product injection better, the selection of the screw also needs to consider the required ratio of injection pressure and compression ratio. .
Production under sterile manufacturing conditions adds a lot of cost to the production. The ability to sterilize a product after manufacturing makes a less demanding process. It also makes it safe to reuse the product while retaining the sterile state. Thermal sterilization is one of the simplest and effective forms of sterilization. The ability of PEEK to withstand the high temperature contributes to its usefulness.
Injection-molded parts are an indispensable part of modern production and life, occupying a very large share in the plastics processing industry. A high-end injection molding machine is very important due to its complexity, accuracy, manufacturing speed, etc.
Since its establishment in 1947, NISSEI is a leading manufacturer of injection molding machines, and has continuously improved its professional and technical characteristics. With the concept of "professional, profound and extensive", it has gradually expanded the industry scope of related technology applications. While paying attention to improving the performance of injection molding machines, it also researches Developed molds, forming support systems, forming processing and other related technologies.
The melt gets into the mold through the gates. The gate is often overlooked. But it plays an important role in product formation. The gate determines the flow of melt into the mold hence the cooling pattern. This is particularly important for a polymer like PEEK that has high shrinkage. A bigger gate will allow more of the melt to enter the mold at a given time. This aids a more uniform temperature drop. Hence more uniform shrinkage, leading to better part formation. Although said to suit many applications, submarine gates are not very good for PEEK. Tab, fan, or edge gates work better for injection molding of PEEK. But also bear in mind the other factors which affect the gate specifications. For example, the number of mold cavities and the type of runner systems.
Hydraulic presses have historically been the only option available to molders until Nissei Plastic Industrial Co., LTD introduced the first all-electric injection molding machine in 1983.
Usually, the important factors that affect the selection of injection molding machines include molds, products, plastics, molding requirements, etc. Therefore, before making a selection, it is necessary to collect or master such information: such as mold size (width, height, thickness), weight, special design, etc.; type and quantity of plastic used (single raw material or multiple plastics); appearance size ( length, width, height, thickness), weight of injection molded products, etc.; molding requirements, such as quality requirements, production speed, etc.
Finished weight and number of cavities are used to determine the required "shot volume" and to select the appropriate "screw diameter".
Radiation is often used for the sterilization of medical tools. The material used for the production of these products must tolerate such radiation. Radiations used for sterilization include gamma radiation and UV radiation. Peek can tolerate these radiations without alterations to its chemical or physical integrity.
When the raw material is injected into the mold cavity under high pressure, the clamping force is generated, so the clamping unit of the plastic injection molding machine must provide enough "clamping force" to prevent the mold from opening. The clamping force requirement is calculated as follows.
Sumitomo (SHI) Demag Plastics Machinery North America, Inc. is part of a global group of companies dedicated to helping plastics processors compete more effectively in the global marketplace. Sumitomo (SHI) Demag and its Japanese parent company, Sumitomo Heavy Industries (SHI), are one of the specialized manufacturers of high-precision, high-performance plastic injection molding machines with annual sales of more than 5,000 units. The world's largest manufacturer of IM machines. Its global injection molding machine development and production network consists of four factories in Japan, Germany and China, with more than 3,000 employees.
Haitian is a leading plastic injection molding machine manufacturer in China. Haitian International Holdings Limited has accumulated more than five years of basic technical experience in the production of "Haitian" brand injection molding machines, and reached a new milestone in the company's history when it was listed on the stock exchange. The advanced corporate structure thus brings a crucial step towards the decisive globalization of the brand. The main focus of the Haitian brand is the development and production of standard injection molding machines for the mass production market. In this area, we create a vital competitive advantage for our customers through commercial efficiency, reliable machine design, extreme reliability and comprehensive support.
Most plastics shrink to an extent when cooled. This volume change from molten to hard solid-state is often accounted for in mold design. Shrinkage becomes more complex when it is anisotropic. In other words, the material shrinks in a different way in different directions. The pressure gets applied during cooling by holding the mold under pressure. This ensures even surfaces and geometry. For anisotropic shrinkage, apply pressure with consideration for shrinkage direction. So when designing the molds for PEEK consider this anisotropic shrinkage.
The mold and finished product should determine whether the "opening stroke" and "clamping stroke" are sufficient to remove the finished product.
Clamping force = the projected area of ââthe finished product in the opening and closing direction (cm2) × the number of cavities × the pressure in the mold (kg/cm2).
The company's main business verticals are automotive, packaging, medical, electrical, sports and leisure, toys, construction, etc.
With world-class "high cycle performance" as the core, through years of experience training, stronger and more evolved "long-life design" and "precise and stable molding" have been realized. In addition, it combines "advanced intelligence" with a new controller that is extremely easy to use. We respond to the diverse needs of various molding sites and contribute to improving productivity.
The first challenge a processor faces in injection molding of PEEK is its high melting point. While this is great in its application, it makes it more difficult in injection molding. Still, injection molding is the most cost-effective means to manufacture plastics. Even more so with PEEK. Working with PEEK means the machine operates at the very limit of the temperature range. So it is important to protect the equipment parts from heat damage or stress. This means using high-grade metals and insulations where necessary. PEEK gets molded in the same type of injection molding machines for more common plastics. But these have to be well adapted to meet the special requirements for PEEK. So any old machine won’t do. For an injection molding machine to be fit for processing it must reach around 400oC + 50oC. If it doesn’t, then modifications are necessary. Modifications carried out aim at increasing the thermocouple heating capacity. The heating bands are also changed to ceramic ones. To contain heat and reach higher temperatures faster, insulating blankets help. This insulates the barrel so that heat generated stays, the temperature rises faster. This reduces energy consumption, hence cost.
The opening and closing stroke should be at least twice the height of the finished product in the opening and closing direction, and should include the length of the vertical runner; the holding stroke should be sufficient to eject the finished product.
There are many different types of injection molding machines, and choosing the right type can bring greater benefits to your business.
There is no doubt that investment in injection molding machines is expensive and needs to be carefully considered. If you are looking for a suitable plastic injection molding machine manufacturer, you can look to us at Log Machine or a Chinese injection molding machine manufacturer, because Chinese plastic injection molding machines provide competitive prices while ensuring high quality. Investing in the right injection molding machine will pay off.
The width and height of the mold must conform to the minimum mold size recommended by the injection molding machine. Too small is not acceptable.
PEEK classifies as a high-performance material. These are plastics that keep their integrity in diverse and extreme applications. The mechanical properties give PEEK its high-performance characteristics. Looking at the chemical structure of PEEK, the superior properties are evident. Its repeating unit comprises three benzene rings. These connect by a ketone and an ether group. The structure is a repeating sequence of ketone and ether bound benzene rings. This gives it a strong, stable semi-crystalline structure. The superior mechanical properties also make the machining of PEEK possible. This is good when there is a need to cut off runners or flashes from injection-molded PEEK products. PEEk’s superior mechanical property complements its lightweight and low density. To put this in perspective, PEEK has a density of 1.32g/cm3. The density of PTFE is 2.2 g/cm3 while that of PET is 1.38g/cm3. This means you have a strong material that can withstand the heat of boiling water. Yet it is lighter than the plastic used in drinking water bottles. The industry goes nuts for such material.
PEEK is a rigid plastic at its service temperature. It is one of the top choices in overmolding. It makes for a good substrate material. It forms a strong core that can then have a softer or lower melting material overmolded on it. The high softening temperature gives a wider option of plastics for overmolding. With a wider gap in the melting point temperature options. This means more materials will be suitable as overmolds
Hydraulic machines, although not nearly as precise, are the predominant type in most of the world, with the exception of Japan.
When operating at such a high temperature the parts in contact with the melt must be high-quality. Copper or alloys are not used in the injection molding of PEEK. while these may work in processing lower melting polymers like polyethylene. They are vulnerable to corrosion at higher temperatures. High-quality stainless steel works for injection molding of PEEK. This is even more important for the screw and barrel. These are in longer contact with hot melt than any other part of the machine. Maintaining smooth well-polished surfaces is also important. This ensures an easy flow of melt and a good flow pattern. For such a tough polymer with a high melting point, viscosity tends to be lower. This is unlike a lower melting polymer which does not need as much heat to achieve lower viscosity. With more viscous material, smooth walls offer the least resistance to flow.
The temperature of the melt needs to stay at around 170 to 200oC further down the barrel. In the mold, it is a different case. This is where cooling happens. You don’t want the part cooling in an uneven way. Where some parts cool at a fast rate and others cool at slower rates. Rate of cooling affects crystallinity. This causes a mixture of amorphous and crystalline regions in the same product. This is often visible as uneven coloration on the product. The image below gives an example of such discoloration.
The projected area of ââthe finished product in the mold opening and closing direction is derived from the overall dimensions of the finished product.
Arburg is a German mechanical engineering company and a world-renowned manufacturer of injection molding machines. Owned by the Hehl and Keinath families, it ranks among the global industry leaders with its electric, hybrid and hydraulic plastic injection molding machines, turnkey systems and its industrial additive manufacturing systems.
Fanuc is a well-known CNC solution provider and plastic injection molding machine manufacturer. Teams of automation professionals work in customer service, engineering, finance, human resources, IT, logistics, operations, manufacturing, product development, sales and marketing, and training.
This includes resistance to water. In medical applications tools or implants get exposed to moisture for long periods. This could also be in a range of environments. Even more so in materials that come in contact with human tissue, serum, blood, or internal organs. These have a range of conditions. For example acidic, alkali, salty, and others. Like the acidic condition in the stomach to the closer to neutral blood. What’s even better about PEEK is that it retains its resistance to chemicals and solvents. It does this even at elevated temperatures. This is great in for example machines where fluids get hot from heating or friction.
When calculating the weight of the finished product, the number of cavities (how many cavities are in the mold) should be considered; for stability, the injection volume should be greater than 1.35 times the weight of the finished product, that is, the weight of the finished product should be within 75% of the injection volume.
JSW is a leading plastic injection molding machine manufacturer with many years of R&D manufacturing experience and extensive experience in manufacturing large electric injection molding machines ranging from 550 to 3000 metric tons.
Milacron is a leading manufacturer of plastic injection molding machines and is a global leader in the manufacture, distribution and service of highly engineered and custom systems in the plastics and processing industries, with a full portfolio of injection molding and extrusion equipment . Milacron maintains a strong market position and maintains leadership in process control systems, maintenance, repair and operational supplies for plastics processing equipment. Milacron provides customers with highly customized equipment, components and services throughout the life cycle of their plastics processing technology systems.
Headquartered in Austria and with 9 locations worldwide, ENGEL is the world's leading manufacturer of plastic injection molding machines. Besides machine building, it also offers a wide range of services. The company's main products include system solutions, electric, hydraulic and vertical injection molding machines, used machinery, control units, robots, process stabilization mechanisms, etc. Engel promises clamping forces of between 280 kN and 55,000 kN for its machines.
From the mold size, determine whether the machine's "large column spacing", "mold thickness", "mold minimum size" and "mold tray size" are appropriate to confirm whether the mold can be placed.
The clamping force of the machine should be greater than the clamping force. For the sake of safety, the clamping force of the machine usually needs to be greater than 1.17 times of the clamping force.
Metals have had a successful rein in many medical tools and equipment. This is partly due to the ease with which they clean and sterilize. Plastics like polyethylene cannot withstand high temperatures. Even the temperature close to the boiling point of water. Try pouring boiling water into a PET bottle and watch it soften. Sterilization occurs at temperatures over 180oC. Sterilization is a crucial part of medical practice. So the materials used need to be sterile as this could lead to the fatal loss. The products reused get sterilized before and after use. Those that are single-use get produced in sterile manufacturing conditions.
The width and height of the mold should be smaller than or at least one side should be smaller than the large column spacing; the width and height of the mold should preferably be within the range of the mold tray size; the thickness of the mold should be between the mold thickness of the plastic injection molding machine.
PEEK has very good resistance to water and another solvent. But moisture from the environment can settle on the surface. Any moisture gathered in storage will become gaseous during processing. At such high temperatures having air pockets in the melt is not a good idea. The recommendation is to dry PEEK to a moisture content of below 0.02%. This occurs by drying at a temperature of around 160oC in a circulating oven for 2 to 3 hours.
The temperature distribution along the barrel is also very important. In the same way the temperature of the melt as it passes through the runners and into the mold. The temperature distribution along the barrel starts from the feed. The feed should remain cool enough to avoid bridge formation. This is flow restriction as a result of the premature melting of the polymer at the feed zone. If this happens the pellets will stick at the feed throat rather than feed-forward.
In this case, it may be necessary to check whether the injection volume and injection speed of the machine are sufficient, whether it needs to be equipped with an accumulator, closed-loop control, etc. Screws that can provide higher injection pressures generally have lower injection speeds, and conversely, screws that can provide lower injection pressures generally have higher injection speeds. Therefore, when selecting the screw diameter, the injection volume, injection pressure and injection speed (injection speed) should be comprehensively considered and weighed.
PEEK processing occurs in conventional injection molding machines. But these have to go through modifications to adapt them for PEEK. Some extra precautions ensure a successful run. Good temperature control, big gates, and clean dry raw materials are some examples. Note that the processing demands also depend on the grade of PEEK used.
Husky is a well-known manufacturer of plastic injection molding machines and the largest brand supplier of injection molding equipment and services to the plastics industry. The Husky team of more than 4,300 dedicated engineers, designers, innovators, materials and software experts around the world is focused on creating success and profitability for our customers in more than 140 countries.
Ningbo Chuangji Machinery Co., Ltd. is located in Yuyao. Is a professional enterprise engaged in plastic injection molding machinery. Since the official launch of LOG Lange presses in 2007, the company's sales network has spread all over the world. It has established more than 50 dealers in mainland China, in North and South America, the CIS, Southeast Asia, Africa, the Middle East, and even Europe. There are dealers and service outlets in more than 20 overseas countries around the world. The company currently has four injection molding machine bases, covering a total area of more than 70,000 square meters, with an annual production capacity of more than 4,000 units. The company always adheres to the management concept of "focus, professionalism and concentration", and pays great attention to talent construction and technology development. Strong independent research and development capabilities and strict quality supervision system make Lange brand injection molding machines have the characteristics of energy saving, high pressure and high speed, precision and stability.
Today, I would like to introduce you to the world's top 10 Plastic injection molding machine manufacturers, hoping to help you.
So far, the specifications of the clamping unit have been preliminarily determined, and the tonnage of the machine has been roughly determined. Next, the following steps must be performed again to confirm which injection unit has a better screw diameter.
At the high temperature, non-PEEK materials get degraded. If the machine processes other plastics this could be residues of those. Lower melting plastics will degrade and cause dark specks on the plastics. This ruins the appearance and quality and may result in part rejection. To avoid this every part of the equipment should get cleaned before beginning the run with PEEK. This includes dismantling the screw and cleaning both the screw and barrel. These are the hottest parts and should get even more attention. Other parts like the nozzle. Runners and molds also need cleaning. If possible dedicate the injection machine to PEEK only. Other ancillary processing machines like the regrind included. Dedicating the entire line to PEEK means less chance of contamination.
While PEEK might be great for some high-end applications, it’s processing isn’t a walk in the park. If you are working with PEEK for the first time there are some special considerations to bear in mind. Regardless of whether you are already experienced at injection molding other plastics. PEEK presents some challenges which may not exist with other plastics. These are as follows.
The electric press, also known as Electric Machine Technology (EMT), reduces operation costs by cutting energy consumption and also addresses some of the environmental concerns surrounding the hydraulic press. Electric presses have been shown to be quieter, faster, and have a higher accuracy, however the machines are more expensive.
Polymers have replaced metals in many applications in the medical and other industries. This has led to improved treatment and management of several medical conditions. While the field is expanding, there are some polymers with well-established applications. Polyether ether ketone, or PEEK, is one such. It is biocompatible, sterilizable, and durable. It finds use in applications ranging from tissue replacement to medical tools. PEEK is a high-performance polymer. Beyond the medical industry, PEEK also finds use in more complex applications. An example is the fabrication of aerospace and machinery parts. Injection molding of PEEK extends its applications to more complex mass reproducible products. Injection molding of PEEK is different from the injection molding of other plastics. This article discusses some of the peculiarities associated with this. In doing so we also get to explore its properties, applications, and some of its special features. Here you’ll have a good insight into how injection molding of PEEK stands out from that of other plastics.
GETTING A QUOTE WITH LK-MOULD IS FREE AND SIMPLE.
FIND MORE OF OUR SERVICES:
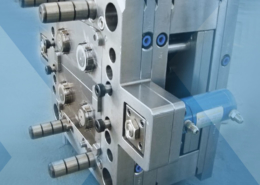
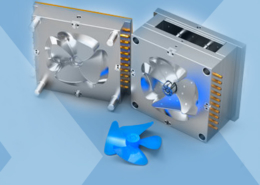
Plastic Molding

Rapid Prototyping
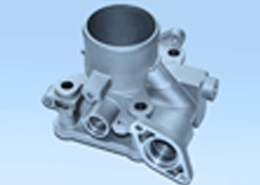
Pressure Die Casting
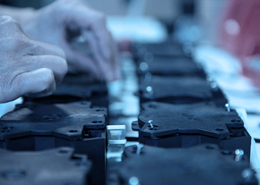
Parts Assembly
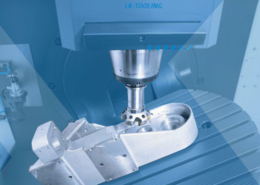