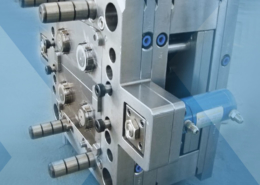
8 Types of Injection Molds - Prototool - injection molding mold
Author:gly Date: 2024-10-15
(1) Mold temperature is too high or insufficient cooling. The mold temperature should be reduced or the cooling time should be prolonged.
The injection molding process of plastic raw materials is mainly plasticizing, filling, cooling and shaping to become finished products. It is a process of heating and then cooling, and also the process of plastic changing from particles to different shapes. In this article, we will explain the PP injection molding process from the perspective of different stages and we present 11 common defects in Polypropylene injection molding.
(4) Poor mold exhaust, residual air in the mold cavity caused under injection. The exhaust system of the mold should be improved.
(2) Mold temperature is too low, barrel temperature is too high. The mold temperature should be increased properly to reduce the barrel temperature.
(4) The wall thickness of plastic parts changes too much. The shape and structure of plastic parts should be designed reasonably to avoid rapid change of wall thickness.
Plastic retyping depends on the mold or mold head. The injection molding product is three-dimensional, and the mold is more complex, and the shrinkage rate should be considered. Other products are flat, strip and needle like continuous product heads.
(6) If the barrel temperature is too low, the injection pressure is insufficient or the injection time is too short, the under injection will also be caused. The control quantity of relevant process parameters should be increased accordingly.
(4) When different kinds of resins are mixed, there will be silver streaks. Mixed use of different resins should be prevented.
RobotDigg Equip Makers Empower Engineers Global Sourcing Supply Chain from Shanghai RobotDigg Shanghai RobotDigg has been professionally manufacturing... >>more
Any raw material has the problem of shrinkage rate, which is caused by the internal stress caused by thermal expansion, cold contraction and crystallization. Generally speaking, thermal expansion and cold shrinkage are easy to overcome, which can be achieved by prolonging cooling time and maintaining pressure continuously. Crystalline raw materials tend to have larger shrinkage difference than non crystalline materials. PP is about 16% of 1000, but ABS is only about 4%. This part needs to be overcome in the mold or by adding additives to reduce shrinkage rate.
(2) The injection capacity of injection molding machine is less than the weight of plastic parts. The injection molding machine with larger specifications should be used.
(3) If the molding temperature is too high or the injection pressure is too low, the surface of the plastic parts will produce pores. The molding temperature should be reduced and the injection pressure should be increased.
The heater of the unit makes the raw material particles melt into liquid flow gradually. It is mainly suitable to adjust the temperature of different raw materials. Increasing the temperature will accelerate the flow of raw materials, which can increase the efficiency, but it does not necessarily guarantee the yield. Therefore, a proper balance must be achieved.
Good results and PP pyrolysis characteristics are that it is best to make the raw materials flow smoothly to the die head during production, so as to avoid the phenomenon of insufficient filling or reflux. Reflux represents that the flow rate of raw materials is faster than the output rate, and the average flow efficiency is increased, which is one of the available methods for processing, but it also causes abnormal MFR distribution, which may lead to instability The defect rate may increase.
Technical parameters Net weight: 380Kgs Wooden case packaging weight: 430Kgs PLC (touch screen, HMI) human-machine interface Taiwan Delta Electronics Solid State Relay Japan's Omron Planetary deceleration system Taiwan Matsuoka Seiko Feed torque 25.4N.M (servo motor + planetary reducer) Pressure ⥠0.8Mpa Displacement resolution of 0.1mm Displacement travel 0-80mm Feed speed 1-130rpm Open mold trip (about) 82mm (without mold) Injection force (about) 1800kg Injection volume (about) 30g/25 cubic centimeter (limpid car needs custom times the force system) Highest temperature One / two zones 360 ° C Three zones 180 ° C Temperature control accuracy ± 0.5 ° C (constant temperature) Power / full load power single AC 220V ± 10%; 50HZ; 2200W Screw diameter 25mm Corinth column spacing 210 * 196mm Dimensions 580 à 580 (floor 850) à 1700mm Packaging Size:1700*800*800mm Heating ring power 400W à 3 pcs Plastic, thermoplastic, or resin materials engineering plastics like PP, PE, PVC, ABS, etc.
In addition to pouring raw materials into runner gate, injection mold also has cooling channel cooling material design. Extrusion molding depends on the cooling channel in the roller to achieve the cooling effect, except for the air knife, cooling water directly poured on the blowing bag, and hollow air blowing and other cooling methods.
Most of PP plastic injection molding processing depends on screw to drive the fluidity, so the design of screw has a great influence. The diameter of screw affects the output, the compression ratio affects the pressure value, and also affects the output and finished product effect, including the mixing effect of various materials. The flow of raw materials mainly depends on the heater, but the friction of raw materials will also produce friction heat energy to accelerate the fluidity, so the screw compression ratio is small, the flow is small, and the rotational speed must be increased, resulting in more friction heat than the screw with large compression ratio.
Two years ago a demo video of Delrin Injection Molding The max mold platen size for the Digg Injection Molding Machine is 300x120x30mm, 30 grams, and 25cm3 (cubic centimeters) (Thanks to Spyker Workshop's check back).
Tensile specimen, three-point bending specimen, Izod impact energy specimen GB standard, or ASTM standards are available. The injection molding machine comes with Digg-Plate which is China's standard tensile test specimen plate. Digg-D638, Digg-D790, Digg-D256 are specimens of ASTM standard specimens for tensile test, flexural test, and Izod impact test, etc. For details, you could refer to https://www.researchgate.net/figure/ASTM-D638-Type-IV-Tensile-Test-Specimen-Details_fig5_314253059 Digg-AIM is a module for an automatic injection out instead of the standard manual plate which is the Tensile Test Specimen mold plate only.
(1) When the size of runner and gate of thick wall plastic parts is small, it is easy to produce surface pores. The size of runner and gate should be enlarged properly.
The elongation of finished products can be enhanced by processing, and the molecular weight distribution will also affect the elongation effect in high-speed production. All extruded products, including fibers, have different elongation. Vacuum and air compression molding can also be regarded as another form of extension.
Most of the plastic machines are designed like syringes. The extrusion force driven by the screw will cause huge pressure at the small outlet and improve the production efficiency. When the mold head is designed as a plane, how to make the raw materials evenly distributed on the whole surface, the design of the hanger mold head is very important. Pay attention to the extrusion opportunity increases the fishgill pump to stabilize the raw material supply.
(3) When the silver streaks always appear in a certain position, it is necessary to check whether there are surface scars on the surface of the corresponding mold cavity. If there is a reflection of the surface scars, the surface scars of the die cavity should be removed by machining.
(2) The structure design of the gating system is unreasonable. The structure of runner and gate should be improved to avoid turbulence during filling.
Product pricing: USD 300 customized fee needs to be added for 110 voltage. Besides this machine, you will need to match an air compressor. Normally customers buy air compressors themselves.
(3) The volatile content in the raw material is too high or the mold exhaust is poor. The volatile substances in the raw materials should be removed and the exhaust system of the mould should be improved.
Description: The machine is micro and improved one compared with traditional injection molding machines, itâs small and easy to be moved, itâs suitable for the production of small samples for academic usage or DIY. The product includes a mold clamping part, sol injection part, body, heating systems, control systems, and charging device. Itâs simple to use with little noise and no pollution; 110V or 220V AC single phase can be used in any electric field.Plastic companies or institutes of plastics can use the injection molding machine for dumb-bell test pieces, it was designed for. But as per experience from Spyker Workshop, it's a great production injection molding machine for small piece mid-volume production.
Other parts will be free in the packing list:One set of dumbbell tensile bars, one set of impact spline, One plate chromatography, sample sizes can be customized.Lead Time: within 10 working days after payment.
(6) The design of gating system is unreasonable. The filling performance of the gating system should be improved to make the melt flow smoothly in the mold cavity.
GETTING A QUOTE WITH LK-MOULD IS FREE AND SIMPLE.
FIND MORE OF OUR SERVICES:
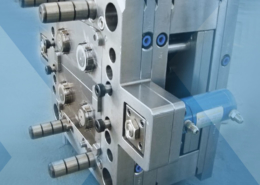
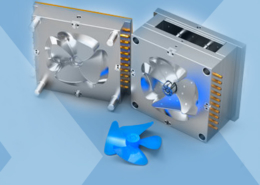
Plastic Molding

Rapid Prototyping
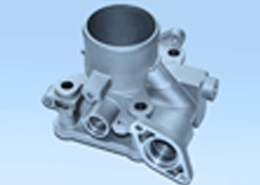
Pressure Die Casting
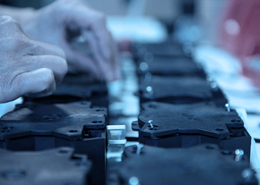
Parts Assembly
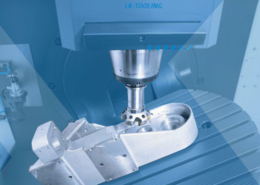