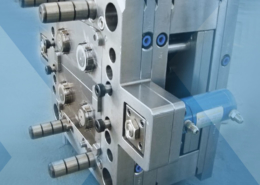
7 Injection Molding Plastic Types - plastic that can be molded
Author:gly Date: 2024-10-15
As for materials, while it’s true that you can use many of the same plastics for both processes, the end-use properties won’t be the same. Take the strength of a PEEK prototype, for example. Injection-molded PEEK is stronger because it’s made of a single layer of material. 3D-printed PEEK is weaker because it’s produced layer-by-layer. If you need to perform testing, that just won’t do. Plus, 3D printing won’t provide you with data about your part’s moldability.
Although acetal has high strength and rigidity, it can become quite brittle at low temperatures or when subjected to impact, which may cause the products to crack.
The injection pressure mainly depends on the melt flow characteristics of acetal (POM), the thickness and width of the runner and gate, and the thickness of the plastic product. Typically, it ranges from 40 to 130 MPa.
Injection-molded Acetal (polyoxymethylene) is typically a semi-crystalline thermoplastic that can be used for mechanical components such as bushings, bearings, gears, and sprockets.
Due to acetal’s minimal water absorption and outstanding dimensional stability, it is often used as a metal replacement material.
If you want to learn about the feasibility of projects involving Acetal (POM), Delrin, or other plastics, contact us immediately for a free quote.
3D printing is great for early-stage projects with less than 100 parts and lead times of 1 to 15 days. But what if you need more than 100 parts? If your design is complete and you can wait a few weeks, it’s worth considering prototype injection molding. There are some sound reasons to do so, especially if your early-stage prototypes used 3D printing.
Products made from injection-molded acetal exhibit high strength and rigidity, capable of withstanding high loads and stresses, making them suitable for manufacturing high-strength mechanical components.
Although acetal material has low moisture absorption, it is recommended to pre-dry the acetal resin at 80°C to 100°C (176°F to 212°F) for 2 to 4 hours to ensure adequate drying.
The common practice is to use a moderately fast injection speed. A slower speed can cause flow marks, while a faster speed can cause jetting and shear overheating.
Acetal plastics exhibit high mechanical strength and rigidity, good sliding properties (low friction coefficient), and excellent wear resistance.
When working with acetal in the injection molding process, several key factors need to be considered to ensure high-quality and reliable products.
There are plenty of prototyping applications for 3D printing, but don’t overlook prototype injection molding just because it requires tooling. Yes, you’ll have to pay for a mold and wait for it, but you’ll also get a tool that costs less than you might expect and with the tolerances you’ll need during a production run. Plus, while traditional injection molds can take months to machine, you can get a prototype injection mold in just a few weeks – and parts in less than 14 days.
3D printing and injection molding also have different part tolerances. With most 3D printing technologies, tolerances of at least 0.1 mm (0.004 in) are typical. Most injection molds are machined to similar tolerances, but parts with tighter tolerances are readily achievable. With injection molding, engineers can even specify two types of tolerances: commercial or fine. The surface finish of injection molded parts is typically superior to that of 3D printed parts, too.
To fully leverage the superior properties of acetal material, injection molding companies often utilize the acetal injection molding process for material processing.
Based on the chemical structure of the molecular chain, they are classified into two types: homopolymer acetal and copolymer acetal.
Acetal features a low friction coefficient and excellent wear resistance, making it ideal for producing sliding and friction components, such as gears, bearings, and sliders.
Acetal copolymer can withstand organic, inorganic solvents, and acids, maintaining stable performance over a wide temperature range, making it suitable for various industrial applications.
Also, 3D printing uses STL files, which define parts in terms of a triangle mesh, whereas the CAD files for injection molded parts are parameter-driven. To use your STL files with injection molding, you’ll first need to convert them from a mesh to a shape to a solid. That can introduce some problems, though it’s obviously better to address any issues during prototyping than during production.
Therefore, mastering the injection molding process of Acetal can not only optimize production efficiency but also significantly enhance product quality.
Compared to metals and other plastics, Acetal’s low friction coefficient, stiffness, and excellent wear performance contribute to the durability and longevity of the products.
We have assembled a professional manufacturing design team with extensive experience and established a physical manufacturing plant equipped with the latest injection molding equipment, offering cost-effective Acetal injection molding products.
Due to its low moisture absorption, acetal injection-molded products can maintain dimensional stability under different environmental conditions and are less prone to deformation.
As a leading injection molding company in China, FOWMOULD is dedicated to providing customers with one-stop services from product design, mold manufacturing, to plastic molding.
Visit the Fictiv Resource Center for more about prototype injection molding, including information about commodity vs. engineering plastics and mold finishes.
Generally, the mold temperature should be controlled between 75°C and 120°C, and the melt temperature should be between 190°C and 230°C (374°F to 446°F).
Even if they’re perfect, 3D-printed prototypes won’t seamlessly become injection-molded parts. That’s because 3D printing has different design rules for specifications, such as minimum wall thickness. If the specifications aren’t adjusted and the wall for an injection molded part is too thick or too thin, the production part could be defective even if the 3D-printed prototype was not. By using the same manufacturing process for prototyping and production, you can pinpoint problems with wall thickness before high-volume production begins.
If you’re considering prototype injection molding, what type of tooling do you need? Aluminum molds are the least expensive and can be machined to 3D-printing equivalent tolerances. If you need tighter tolerances, choose steel. That might seem expensive, but capable manufacturers can provide you with cost-effective prototype injection molds made of soft and semi-hardened steels.
Steel costs more than aluminum, but soft and semi-hardened steels cost less than the hardened steels used in traditional higher-volume injection molds. Your mold manufacturer can also help you control tooling costs by using aluminum for the base and steel for the mold cavity. Master unit dies (MUD) with a standard frame and customizable inserts are also available and can cut tooling costs by as much as 66 percent.
In plastic manufacturing, people often equate Acetal with POM, as they are essentially different names for the same material. Acetal, with its low friction coefficient and high wear resistance, makes it an ideal choice for producing high-precision and durable components.
When it’s time for late-stage prototyping, don’t dismiss plastic injection molding for runs of more than 100 parts. If your design is complete and ready for testing, there are considerable advantages to injection molding. You’ll have to wait a few weeks to get the parts you need, but prototype injection molding takes less time than you might think and uses tooling that can be cost-effective.
ACIS®, Autodesk Inventor®, CATIA® V5,Creo™ Parametric, IGES, Parasolid®, Pro/ENGINEER®,Siemens PLM Software’s NX™, SolidEdge®, SolidWorks®, STEP
Additive manufacturing is a smart choice if your design is evolving or still in the concept stage. Unlike injection molding, you’ll never have to modify or scrap a mold as your part design changes. 3D printing also lets you choose from a wide range of plastics, including many of the same materials you can use with injection molding.
As one of the most versatile plastic materials, HDPE is widely used in packaging, piping, consumer goods, agriculture, construction, and electrical insulation due to its excellent chemical resistance and flexibility.
GETTING A QUOTE WITH LK-MOULD IS FREE AND SIMPLE.
FIND MORE OF OUR SERVICES:
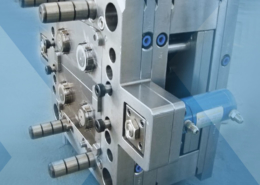
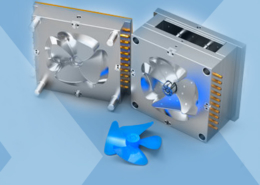
Plastic Molding

Rapid Prototyping
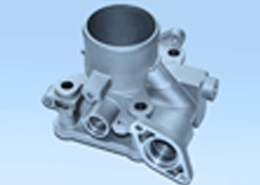
Pressure Die Casting
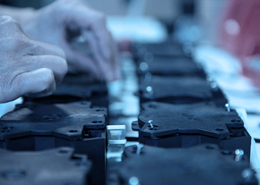
Parts Assembly
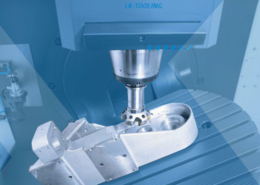