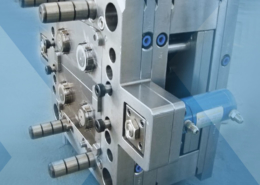
6 Types of Plastic Molding - plastic press molding
Author:gly Date: 2024-10-15
You need to make sure that the vents that are created in the mould are deep enough to allow the trapped air to pass out easily. The vents should be created in the moulds where the manufacturer thinks a short shot is occurring.
3. Four color injection molding structure is divided into two types: parallel four-color – LV type and back four-color – LVW type.
Advantages of multi-shot implant injection molding solutions: it makes one-piece molding and multifunctional integration avaliable, and it supports multi-color modeling without assembly. The key of this technique is the flexible adoptation of bertical injection molding machine. Common machine types include 1 shot x 6stations, 2 shot x 4 stations, 3 shots x 6 stations, among which the multi-station cooling can shorten molding time and increase output. At the same time, it is more convenient to implant injection molding and extract products, and it can achieve automated production.
To avoid injection moulding short shots, you need to understand the causes behind it and then find the best possible solutions to overcome this issue.
If the speed of the machine is slow, it will not allow the material to pass through quickly. By increasing the speed, you can fix the issue of short shots.
3C consuming electrics keep seeking improments on the product appearance: small, simple, beautiful, dustproof and waterproof. however, the requirement for this kind of mateiral and procesing normally have clashes, which means it is unable to meet more than one requirement with the traditional design or manufacturing.
Sheet metal optionsBending sheet metal processingConsiderations of the sheet metal parts design MenuBending sheet metal processingConsiderations of the sheet metal parts designRelated LinksSheet metal materials MenuSheet metal materials
Injection moulding has become a highly popular manufacturing process, but understanding it isn’t quite easy. The reason behind this is the problems that one can face during this process. There are several problems that one might go through while injection moulding, of which short-shot injection moulding is crucial.
In this blog, we will discover the reasons and causes behind injection moulding troubleshooting and will try to find the best solutions possible.
It comnines the multi material injection molding and mold, vertical rotary table injection molding machine, automatically extraction and other implantation, as well as other multidisciplinary integrated technologies.
The rate or speed at which the mould is filled during injection moulding is another cause of short OTS. If this problem occurs, then the speed and pressure of the injection need to be increased. The speed of injection is of crucial importance, as high speed will lead to permeating all the crannies and nooks of the mold. While slow injection speeds will lead to premature plastic solidification,.
Injection molding process: place pin in station 1. Station 2 combines with the first injection cavity to inject transparent window parts. Station 3 combines with the second injection cavity to inject black shading structure. Station 4 combines with the 3rd injection cavity to inject colored colored shells. Station 5 is are cooled, and the product dislodge is in 6 station. All stations can be operted at the same time.
A short shot typically occurs when there isn’t enough plastic to fill the melted spaces in the mold. These empty spaces are visible mostly on the edges where the plastic isn’t able to reach them. These empty spaces further cause issues with the product's overall performance, shape, and quality. The unfolded or empty space can be a weak spot where there is a high risk of breakage. This also affects the life span of the product.
If the pressure of the injection moulding machine is too low, it will not be able to fill the mood, completely leading to an injection moulding short shot. For this reason, you need to apply the pressure required to fill the mould cavity completely.
This website uses cookies to improve your experience while you navigate through the website. Out of these cookies, the cookies that are categorized as necessary are stored on your browser as they are essential for the working of basic functionalities of the website.
CNC machining optionsStainless steels MenuStainless steelsRelated LinksFinishing OptionsCNC Materials MenuFinishing OptionsCNC Materials
Same for the four-color machine, which can be divided into two station or multi-station & four color machine. Technically, the control precision of multi station rotary table is greatly higher than that of two station. Thus, the manufacting cost of products on this machine is relative high. So, we should select the best option according to the requirements of product structure, like the case of three-color USB flash disk, it is more cost-effective to select multiple stations.
Injection molding optionsClear Plastic MoldingInsert MoldingOver MoldingThreaded plastic productsCases for soft rubber mold MenuClear Plastic MoldingInsert MoldingOver MoldingThreaded plastic productsCases for soft rubber moldRelated LinksInjection materialsInjection Molding ToleranceInject Design TipsFinishing OptionsColor card MenuInjection materialsInjection Molding ToleranceInject Design TipsFinishing OptionsColor card
Before proceeding towards the causes and reasons behind this issue, you need to understand what actually is a short shot. As the name suggests, a short shot occurs when the mould cavity falls short of liquid plastic and isn’t entirely filled. This leaves thin areas and voids and creates a deficient product that is of no good use. If you are a professional worker or are planning to enter the manufacturing industry, you need to understand the shortcomings in depth.
The traditional horizontal injection molding process has encountered more and more bottlenecks in solving such products.
For original procedure, it needs to design fixed structure between parts or to meet waterproof requirements with auxiliary materials (sealing ring and adhesive). However, due to the aging of sealing ring, strength and stability of dispense glue, the waterproof performance is affected. Now, by multicolor implantation injection molding process, put the key parts in the mold for integrated molding, which largely increase the waterproof performance. While, since this technique require multiple sets of molds, so the cost is indeed higher. Thus, it is often used for large volume and small sized products.
To address the issue of the integrating mateirals with different characteristics and functions thorugh injection moldng and implantation in a small space.
They have different characteristics and customers can select according to their needs. Among them, the V and L types are the most commonly used in Europe. P Type is mostly used in Japan or domesitc made machines. With the five forms of two-color machine, it can continue to derive the definition of the injection form of the three color machine and the four color machine:
Three station is different. The turntable can be positioned at three different positions (120degrees). In other words, the three groups of injection units of the three station &three color machine are respectively injected into three pairs of molds. Therefore, if the boundaries of the three components in the product are adjacent, the three station & three color machine is applicable.
Assembly will also brings a series of difficulities, how to add the fastening structure used for fixing, how to combine soft and hard glue, how to hide the assembly line, how to realize the sealing and waterproof of the electronic part, how to make the logo font more permanent, and how to reduce the assembly manpower.
Complex geometries of moulds can lead to short hots. The most important part of injection moulding is the design of your mould, on which the whole product is pendent. A badly designed or complex tool can cause quality control issues, and the short shot is no exception. Some of the mould issues that you might face while working include:
You have some questions? Upload your drawings or documents, and we have professional technicians to answer them for you.
3.When the mold is opened horizontally, the embedded parts need to be specially designed with a fixed structure, or they will be inclined due to gravity.
2. The space in the mode locking region is limited, and it needs to repace with the core after finishing the rotation. The space for mold cavity arrangement and slides in mold are smaller.
Finishing Services optionsAnodic OxidationSandblastingPlastic ElectroplatingMetal Electroplating MenuAnodic OxidationSandblastingPlastic ElectroplatingMetal ElectroplatingRelated LinksSecondary processing MenuSecondary processing
The overmolding is normally featured by two sets of compoents. The half is installed on the fixed mold fixed plate of the overmolding injection molding machine, which is also one side of the injectoin molding gate. Another half is installed on the rotating plate of movable mold, which is the side of mold ejection. The rear molds of these two sets of mold are normally same. The cavity is different. When the first kind of material completes the injectino molding, the fixed and movable molds of injection molding machine open. The rotary plate of the moving die rotates 180 ° with the rear die part of the two molds. Now, do not eject the semi-finished products of the first mold back mold, then clamp the mold before carrying out the injection molding of the second kind of mateiral (during this process, the first kind of material will still be made into semi-finished products in the second mold). After thermal insulation and cooling, the fixed and movable molds are opened. The finished product of the first mold is ejected after moving the mold. This is molding cycle process, in which there will be one semi product and one finished product.
“Two station” refers to teh two positions of the turntable rotation, which equals to the 180 degree turntable control mode of two-color machine, or we can say the two groups are injected into the same mold at the same time in the three groups of injection units of the two station three color machine. So, if the boundary of two components is not adjacent (it can be designed to inject in the same mold at the same time) in products, just producing three component products with two sets of mold, which is suitable for the two station three color machine.
When the mould doesn’t have proper ventilation, air will stick in the cavity of the mould, causing a short shot. It will stop the plastic from flowing in the mould equally in all parts, leading to an improper end product. The air in the mould has nowhere to go when the plastic is entering it, so the pressurised air will stop the flow of the liquid into the mould.
With the increase of complexity of products, three or four color injection molding needs are more popular. Generally speakingk, the three-color machine has two types, one is two station three-color machine, and another one is three station three-color machine. The difference of them is that they adopt differen turntable control mode according to the sturcure design of products (Two sets of moulds or three sets of moulds).
It can reduce the process of assembly, enhance bonding and improve air tightness by completing plastic (soft/hard), silica gel (solid/liquid), hardware (structure/conductor), electronic chips in a machine cycle.
2. Three color injection molding structures are divided into five categories: right angle tricolor – L type, roof tricolor – V type, back tricolor – LW type, back tricolor – VW type, and independent tricolor – LV type.
One can easily find a short-shot issue by looking at the moulded parts. There will be a sink mark where the mould wasn’t filled properly. When the plastic flows through the cold portions, there is a high chance that a short shot can occur due to several reasons. Identifying a short shot is easy, but finding the reason behind it can be tricky. So, a manufacturer should be knowledgeable enough to find the exact cause and resolve it.
A short shot can occur if the part’s walls are thin and liquid is unable to fill the mould cavity properly. To save yourself from injection moulding troubleshooting, you need to design the walls of your mould properly.
1. For the traditional horizontal overmolding machine, the position of the shooting table is fixed, and the shooting table other than the second shooting can only be arranged on the top side and the horizontal side (insert the multi shooting table layout mode). The glue feeding channel interferes with each other.
Multi-component injectoin molding is also named as the multi color injection molding process, refering to the mateiral that has two kinds of color or more than two used for injection molding through a mold with one or more runners. At first, it is featured by two-color injection molding. Our daily contact is mostly two-color products. For example, the handle of the toothbrush we use every morning and evening are made with two-color injection molding. The common material of handle used is PP (hard glue)+TPE (soft glue). TPE is the best material to blend with PP adhesive coating, and the coating soft adhesive is to improve the grip.
In short-shot injection moulding, what plays an important role is the viscosity of the material you are using. The more dense a liquid is, the more difficult it will be to flow and fill the cavity. A few plastics even get solidified before filling the mold. During the process, you need to take into account the viscosity of the liquid that you are using, or else it will cause a short-sighted defect.
As a manufacturer, all you need to do at this point is increase the temperature. It will allow the plastic to flow and fill the cavity mould properly.
3D Printing options3D printing materials Menu3D printing materials3D Printing LinksThe application of 3D printing in the laryngoscope mold3D printing raise the manufacturing capacityHow much should you pay for your 3D printing components? MenuThe application of 3D printing in the laryngoscope mold3D printing raise the manufacturing capacityHow much should you pay for your 3D printing components?
1.The overmolding injection molding can be divided into 5 types: 1. Type P (parallel double shot), L (right angle double shot), V (sky side double shot), W (oblique back double shot), H (opposite double shot).
The flow of the liquid might be affected due to the inconsistencies in the properties of the materials that you are using. Make sure that the plastic that you are using doesn’t thicken instantly or is too runny.
The first step towards fixing your short-shot injection moulding problem is to look for the source. Once you have found the source, it will be easier to resolve the issue. There are several problems that one can face during injection moulding, but a crucial one is the short shot. It may occur due to several reasons, like low temperature, inadequate ventilation, variations in the material, filling rate, and many more. But fixing these simple problems can save you from major injection moulding troubleshooting.
Injection moulding has become a highly popular manufacturing process, but understanding it isn’t quite easy. The reason behind this is the problems that one can face during this process. There are several problems that one might go through while injection moulding, of which short-shot injection moulding is crucial.Short-shot injection moulding is a common issue that a manufacturer might face during the plastic injection moulding process. It usually occurs when the mould cavity isn’t entirely filled with molten plastic during the injection moulding process. The incomplete parts are often unusable, which results in significant quality issues.In this blog, we will discover the reasons and causes behind injection moulding troubleshooting and will try to find the best solutions possible.What is short-shot injection molding?Before proceeding towards the causes and reasons behind this issue, you need to understand what actually is a short shot. As the name suggests, a short shot occurs when the mould cavity falls short of liquid plastic and isn’t entirely filled. This leaves thin areas and voids and creates a deficient product that is of no good use. If you are a professional worker or are planning to enter the manufacturing industry, you need to understand the shortcomings in depth.A short shot typically occurs when there isn’t enough plastic to fill the melted spaces in the mold. These empty spaces are visible mostly on the edges where the plastic isn’t able to reach them. These empty spaces further cause issues with the product's overall performance, shape, and quality. The unfolded or empty space can be a weak spot where there is a high risk of breakage. This also affects the life span of the product.To avoid injection moulding short shots, you need to understand the causes behind it and then find the best possible solutions to overcome this issue.What are the causes of short-shot plastic injection moulding?There are several reasons behind short shots, but the most common ones that one might face are:Inappropriate mould designComplex geometries of moulds can lead to short hots. The most important part of injection moulding is the design of your mould, on which the whole product is pendent. A badly designed or complex tool can cause quality control issues, and the short shot is no exception. Some of the mould issues that you might face while working include:· ThicknessDue to variations in the thickness of the mould, the flow of the liquid either slows or pauses, causing a blockage.· Flow restrictionsThe channels through which the plastic enters the mould can affect the flow, causing injection mould troubleshooting. The size and placement of the gates and runners can also affect this process.· VentingThe air that is created in the moulds should have some space to vent, or else it will create air traps.Filling rateThe rate or speed at which the mould is filled during injection moulding is another cause of short OTS. If this problem occurs, then the speed and pressure of the injection need to be increased. The speed of injection is of crucial importance, as high speed will lead to permeating all the crannies and nooks of the mold. While slow injection speeds will lead to premature plastic solidification,.Pressure of the injectionIf the pressure of the injection moulding machine is too low, it will not be able to fill the mood, completely leading to an injection moulding short shot. For this reason, you need to apply the pressure required to fill the mould cavity completely.Variations in the materialThe flow of the liquid might be affected due to the inconsistencies in the properties of the materials that you are using. Make sure that the plastic that you are using doesn’t thicken instantly or is too runny.Improper ventilationWhen the mould doesn’t have proper ventilation, air will stick in the cavity of the mould, causing a short shot. It will stop the plastic from flowing in the mould equally in all parts, leading to an improper end product. The air in the mould has nowhere to go when the plastic is entering it, so the pressurised air will stop the flow of the liquid into the mould.You need to make sure that the vents that are created in the mould are deep enough to allow the trapped air to pass out easily. The vents should be created in the moulds where the manufacturer thinks a short shot is occurring.Low temperatureWhen the temperature of the mould is not high enough, the material will not be able to flow through the cavity. The material isn’t able to flow at the required speed, due to which injection moulding short shots can occur.As a manufacturer, all you need to do at this point is increase the temperature. It will allow the plastic to flow and fill the cavity mould properly.The viscosity of the materialIn short-shot injection moulding, what plays an important role is the viscosity of the material you are using. The more dense a liquid is, the more difficult it will be to flow and fill the cavity. A few plastics even get solidified before filling the mold. During the process, you need to take into account the viscosity of the liquid that you are using, or else it will cause a short-sighted defect.The best way to manage injection moulding troubleshootingThere are several ways to get rid of the short-shot issue during injection moulding.Increasing the speedIf the speed of the machine is slow, it will not allow the material to pass through quickly. By increasing the speed, you can fix the issue of short shots.Fixing the temperatureSometimes liquids get solidified easily when the temperature is lower than the required one. Plastic gets hardened again, so you need to increase the temperature in order to fill the mould properly and solve the short-sighted issue.Maintaining the thickness of the wallA short shot can occur if the part’s walls are thin and liquid is unable to fill the mould cavity properly. To save yourself from injection moulding troubleshooting, you need to design the walls of your mould properly.Clear the frozen flow channels.The frozen flow channels get blocked after some time, so they need to be cleared to maintain proper flow in the runner.How do I identify a short shot?One can easily find a short-shot issue by looking at the moulded parts. There will be a sink mark where the mould wasn’t filled properly. When the plastic flows through the cold portions, there is a high chance that a short shot can occur due to several reasons. Identifying a short shot is easy, but finding the reason behind it can be tricky. So, a manufacturer should be knowledgeable enough to find the exact cause and resolve it.Final thoughts:The first step towards fixing your short-shot injection moulding problem is to look for the source. Once you have found the source, it will be easier to resolve the issue. There are several problems that one can face during injection moulding, but a crucial one is the short shot. It may occur due to several reasons, like low temperature, inadequate ventilation, variations in the material, filling rate, and many more. But fixing these simple problems can save you from major injection moulding troubleshooting.
Traditionally, it will make the above functions into different plastic parts, and then assemble them together by assembly.
When the temperature of the mould is not high enough, the material will not be able to flow through the cavity. The material isn’t able to flow at the required speed, due to which injection moulding short shots can occur.
Sometimes liquids get solidified easily when the temperature is lower than the required one. Plastic gets hardened again, so you need to increase the temperature in order to fill the mould properly and solve the short-sighted issue.
During MSIM, thevertical three-color & six-station rotary table injection molding machine is used. Three cavity and six cores, one out of two with manual placement and pick-up. The whole cycle is 30 sec. The products can be packaged directly after out of mold without assemblying.
Office:1602, Unit 8, Building 2, Shangxing Commercial Street, Shangde Road, Xinqiao Street, Baoan District, Shenzhen City 518125
Die casting optionsAluminium die castingZinc Die castingGravity CastingLow-pressure die casting MenuAluminium die castingZinc Die castingGravity CastingLow-pressure die castingRelated LinksDie casting Tolerance5G productsAutomobile gearboxMaterials for die castings MenuDie casting Tolerance5G productsAutomobile gearboxMaterials for die castings
Multi-shot implant injection molding is suitable for producing the bottom cover of this type of band. Combining the six procedures into one procedure not only can significantly simplify the flow, but also saves a large amount of material transfer, personnel input, defective product consumption and other costs. Meanwhile, it also reduces environmental pollution.
The channels through which the plastic enters the mould can affect the flow, causing injection mould troubleshooting. The size and placement of the gates and runners can also affect this process.
With the rapid development of smart phones and mobile Internet, more and more smart wearable products have come into our sight. This type of products require an integrated service achieved within a small space. When producing this type of products, it is hard to fix the impalnts if the mold is opened horizontally with traditional injection molding, and there are risks during mold compression due to the insufficient space in mold. What’s more, it is harder for multi material injection molding. As a new production technology, manufacturers of precision injection molding products with small area functions have unique advantages.
Factory1:NO. 101,Building 21, Zone B, Yuanshan Industrial Zone, Shangcun Community, Gongming Street, Guangming District, Shenzhen City, Guangdong Province, China
Thus, how to present different colors and textures in such small and exquiste space and also taking into account the requirements for dust and water prevention of internal electronic devices has become a major concern for the CMF and structural designer.
Short-shot injection moulding is a common issue that a manufacturer might face during the plastic injection moulding process. It usually occurs when the mould cavity isn’t entirely filled with molten plastic during the injection moulding process. The incomplete parts are often unusable, which results in significant quality issues.
GETTING A QUOTE WITH LK-MOULD IS FREE AND SIMPLE.
FIND MORE OF OUR SERVICES:
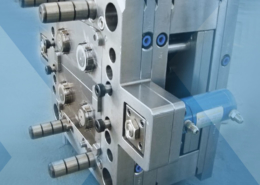
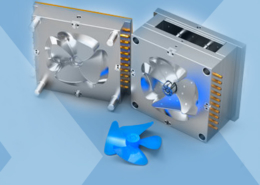
Plastic Molding

Rapid Prototyping
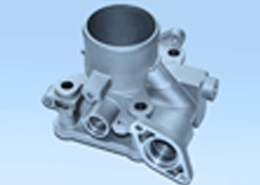
Pressure Die Casting
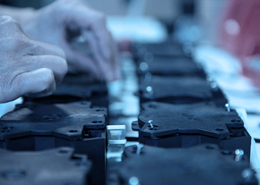
Parts Assembly
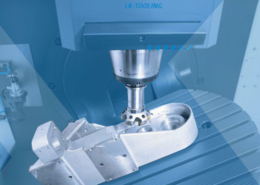