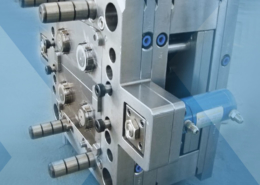
Unveiling the Potential of Double Shot Injection Molding
Author:gly Date: 2024-06-08
In the dynamic landscape of manufacturing, double shot injection molding stands as a beacon of innovation, blending precision engineering with artistic flair. This article embarks on a journey to explore the intricacies of double shot injection molding, from its inception to its burgeoning role in shaping industries worldwide.
Introduction
Double shot injection molding, a cutting-edge technique in the realm of plastic manufacturing, revolutionizes the creation of intricate and multi-material components. Unlike conventional injection molding processes, it enables the seamless integration of two materials or colors within a single part, unlocking new design possibilities and enhancing product aesthetics and functionality.
Historical Evolution
The origins of double shot injection molding can be traced back to the mid-20th century, with the advent of multi-material molding technologies. Initially employed for niche applications, such as automotive interiors and consumer electronics, its adoption gradually proliferated across diverse industries, fueled by advancements in material science and manufacturing capabilities.
The refinement of mold design, injection techniques, and material compatibility further propelled the evolution of double shot injection molding, making it a cornerstone of modern manufacturing processes.
Technical Insights
At its core, double shot injection molding involves the sequential injection of two materials or colors into a single mold, culminating in the formation of a composite part. This process necessitates precise control of injection parameters, mold temperature, and cooling rates to ensure optimal material bonding and part integrity.
Advanced mold technologies, such as rotating or sliding cores, facilitate the intricate geometries and complex features inherent in double shot molding. Moreover, the compatibility of various thermoplastic resins and elastomers expands the design palette, enabling engineers to tailor material properties to specific application requirements.
Enhanced Design Flexibility
Double shot injection molding empowers designers to transcend traditional constraints, offering unparalleled freedom in material selection, color combinations, and part geometries. By seamlessly integrating soft-touch grips, decorative inserts, or functional overlays within a single component, manufacturers can elevate product aesthetics and user experience.
Furthermore, the ability to mold dissimilar materials or durometers in tandem enhances product performance and versatility, catering to diverse market needs. From automotive dashboards to medical device housings, double shot injection molding enables the realization of intricate designs with precision and consistency.
Cost Efficiency and Production Optimization
Despite its advanced capabilities, double shot injection molding offers compelling cost efficiencies and production advantages. By consolidating multiple manufacturing steps into a single operation, it reduces cycle times, labor costs, and material waste, enhancing overall productivity and profitability.
Moreover, the seamless integration of automation and robotics further streamlines production processes, ensuring consistent quality and scalability. As a result, manufacturers can accelerate time-to-market, respond agilely to market demands, and maintain a competitive edge in a fast-paced global economy.
Market Applications and Future Prospects
The versatility and adaptability of double shot injection molding find applications across a myriad of industries, including automotive, electronics, healthcare, and consumer goods. From decorative trim components to functional assemblies, its footprint continues to expand, driven by evolving consumer preferences and technological advancements.
Looking ahead, the future of double shot injection molding holds promise for further innovation and refinement. Advancements in materials science, mold technologies, and digital manufacturing are poised to unlock new frontiers in design complexity, production efficiency, and sustainability.
Conclusion
In conclusion, double shot injection molding emerges as a transformative force in modern manufacturing, transcending conventional boundaries to redefine possibilities. Its fusion of precision engineering, design flexibility, and production efficiency underscores its significance in shaping industries and driving innovation.
As industries navigate the complexities of a rapidly evolving marketplace, the adoption of double shot injection molding offers a pathway towards differentiation, efficiency, and sustainability. By embracing this technology and harnessing its potential, manufacturers can embark on a journey towards a future characterized by ingenuity, excellence, and enduring value.
GETTING A QUOTE WITH LK-MOULD IS FREE AND SIMPLE.
FIND MORE OF OUR SERVICES:
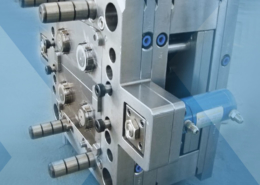
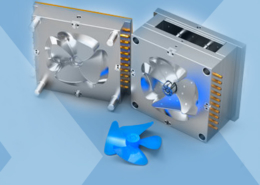
Plastic Molding

Rapid Prototyping
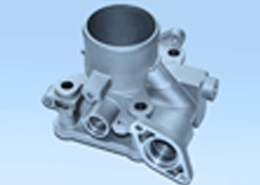
Pressure Die Casting
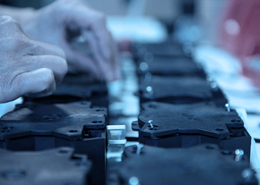
Parts Assembly
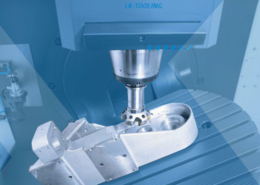