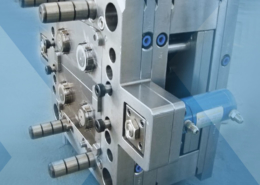
5 Ways Prototype Tooling Speeds up the Production Process - prototype tooling pl
Author:gly Date: 2024-10-15
These are depressions or indents on the surface of the molded part. They occur when the material experiences uneven shrinkage during cooling, resulting in localized depressions.
These two commonly used polyethylene materials share some similarities but also notable differences. Some are discussed below:
With blow molding, a hollow HDPE product is created. The process starts by extruding a tube-like parison of molten HDPE. It is then placed in a mold, and the air is blown into it, causing the material to expand and take the shape of the mold.
Yes, HDPE can be injection-molded. It is a commonly used technique for shaping HDPE into various products. HDPE pellets are melted and injected under intense pressure into a mold cavity during the injection molding.
Invest in material testing and characterization equipment to analyze the properties of the HDPE material. This technology helps ensure the material meets the required specifications, allowing for better process control and optimized part quality.
The HDPE molding process encompasses various techniques, each serving specific purposes. To end your curiosity, let’s look at three commonly used HDPE molding processes: injection molding, blow molding, and rotational molding.
Since the glass filled material is nonconductive, it is ideal for applications within the automotive and electrical industries. It is also a practical choice for manufacturing parts that handle electrical currents.
Regular maintenance is essential to keep the mold in optimal condition and prolong its lifespan. This includes routine cleaning, inspection, lubrication of moving parts, and addressing signs of wear, damage, or parting line mismatch.
Techniques such as ultrasonic testing, dye penetrant inspection, and magnetic particle inspection can be employed to identify cracks, surface defects, or hidden flaws within the mold structure.
Ready to elevate your HDPE injection molding projects to new heights? Contact Kemal Manufacturing today, and let us bring your ideas to life with precision, reliability, and unmatched quality.
Low Impact Strength at Low Temperatures: It exhibits reduced impact strength at low temperatures, becoming more susceptible to cracking or failure under impact or cold weather conditions.
HDPE is a thermoplastic acknowledged for its versatile usage, exceptional durability, strength, and chemical and moisture resistance.
These are air pockets or gaps within the molded part. You’ll witness them resulting from inadequate venting, poor material flow, or entrapped air during the injection.
For HDPE molding applications, injection molding is the best option because it guarantees exact control over dimensions, good surface polish, and repeatability.
Density – The primary difference between LDPE and HDPE is their density. LDPE has a lower density, typically ranging from 0.910 to 0.940 g/cm³, while HDPE has a higher density, typically ranging from 0.940 to 0.970 g/cm³.
Applying suitable coatings or surface treatments, such as chrome plating or nitriding, can enhance the mold’s lifespan and facilitate easy part release.
Evaluate the desired time-to-market for your product. HDPE injection molding generally has faster cycle times, allowing for quicker production and turnaround.
Transparency – LDPE is more transparent than HDPE. HDPE has a translucent appearance, while LDPE allows more light transmission, giving it a higher degree of transparency.
Strength and Stiffness – HDPE has higher tensile strength and stiffness than LDPE, making it more suitable for applications requiring greater structural integrity and dimensional stability.
Processability – HDPE is generally easier to process than LDPE. HDPE exhibits better flow properties, making it more suitable for injection molding or blow molding.
While HDPE (High-Density Polyethylene) has numerous advantages for molding applications, there are a few disadvantages to consider:
You can assess the mold’s performance during molding. This can include injecting a test material into the mold and evaluating factors such as material flow, filling behavior, cooling efficiency, and ejection of the molded parts.
Glass filled nylon injection molding is a practical choice for creating durable molded parts that will encounter friction and wear. The main characteristics and benefits of molding with this material compared to general purpose nylon include:
Scientific plastic molding design, material processing, and process control are advancing. Glass filled nylon injection molding can create molded parts that replace metal parts. This is beneficial for applications that require a reduction in weight or noise.
The benefits of HDPE are not limited to strength, chemical resistance, toughness, and moisture resistance, but you’ll find it economical, sustainable, and eco-friendly.
By following these restrictions and precautions, you can minimize the risk of defects and achieve high-quality finished products.
Consider your product’s desired quality and surface finish. Injection molding typically provides precise dimensions and smooth surface finishes.
In this process, HDPE pellets are melted and injected into a mold cavity using high pressure. Once inside the mold, the molten HDPE solidifies and takes the shape of the mold.
HDPE (High-Density Polyethylene) is a versatile material widely used in various industries to produce different products.
Consider using energy-efficient machinery and equipment for molding. Upgrading to more efficient motors, heaters, and cooling systems can reduce energy consumption, lower operational costs, and contribute to environmental sustainability.
Draft angles allow for the smooth release of the part from the mold cavity without causing damage or deformation. Adequate draft angles also facilitate proper material filling during the molding process.
Rotational molding involves rotating a hollow mold while heated HDPE resin is gradually melted and coated on the inner surfaces of the mold. The mold rotates as the melted HDPE cools and solidifies, forming the desired shape.
We provide a comprehensive range of plastic molding services including mold design assistance, modeling, prototyping, manufacturing, and testing.
Evaluate the design requirements of your product. Injection molding suits intricate and detailed designs, while blow molding is ideal for hollow objects. Rotational molding is well-suited for large, seamless products.
Moreover, HDPE is flexible, allowing easy bending and shaping during molding. It demonstrates high impact resistance, ensuring resistance to fractures or cracks.
You should consider factors such as part geometry, wall thickness, draft angles, gating and ejection systems, and venting. The mold construction should also be robust and precise to withstand molding pressures and temperature cycles.
When it comes to optimizing your molding process, several technologies can help you achieve better results. Consider implementing the following:
The desired shape is subsequently achieved when the molten HDPE hardens in the mold. The finished item is then evacuated after the mold has been opened.
Polyamides are commonly known as nylon. They are one of the most used engineering thermoplastics. Nylon is extensively used for wire coatings and other electrical components. Glass filled nylon is the preferred choice when you need a tougher material, as it makes the nylon considerably stronger.
Integrate robotics and automation into your HDPE molding process. Automated systems can streamline operations, reduce human error, and increase efficiency.
This is performed using various tools such as calipers, micrometers, height gauges, and coordinate measuring machines (CMM).
When the final portion has cooled, the mold is opened, releasing it. With HDPE injection molding, you can produce intricate and detailed products with high precision and consistency.
You can identify any potential issues or defects in molds by employing these inspection and testing methods, allowing for timely corrective actions and ensuring the production of high-quality molded products.
Heat Resistance – HDPE exhibits better heat resistance than LDPE. HDPE has a higher melting point and can withstand higher temperatures before softening or deforming.
Explore innovative mold cooling technologies like conformal cooling systems. These systems use advanced cooling channels that conform to the shape of the mold, providing more efficient and uniform cooling.
Careful consideration should be given to the mold design, including using slides, lifters, or collapsible cores to accommodate undercuts and complex geometries.
Plastic Molded Concepts has expertise in molding with many different engineering-grade resins, including glass filled nylon.
The selection and positioning of gating and ejection systems impact the flow of HDPE material and the ejection of the finished part. Proper gate design ensures uniform material flow into the mold cavity, minimizing the risk of flow lines, air traps, or part defects.
It involves a thorough visual examination of the mold surface, components, and critical areas to identify any signs of wear, damage, or defects.
While using HDPE for molding, you must be aware of certain constraints and take the needed precautions to achieve a successful molding activity.
This article will lead you to knowledge about High-Density Polyethylene (HDPE) and a few of its numerous applications. You may be working as a product designer or an engineer or have an interest in plastics, increasing your views and scope of options.
HDPE exhibits notable chemical and physical properties. It can tolerate chemical solvents, withstand corrosion, and survive dampness. It resists the effects of acids, bases, and other substances, preserving its life and robustness.
Blow molding and rotational molding may have longer cycles due to cooling and curing processes. Select a process that aligns with your time requirements.
Robots can handle material handling, part ejection, and quality inspection, allowing for faster production and consistent output.
After cooling, the mold is opened, and the final blow-molded HDPE product is released. This process is frequently used to create hollow things like bottles and containers.
Blow molding and rotational molding may have slight variations and surface texture. Assess which process can meet your quality expectations.
This technology allows you to identify deviations or variations during molding and make necessary adjustments to maintain consistency and quality.
Several important mold considerations can greatly impact the final product’s overall process and quality. Here are key factors to keep in mind:
Selecting the appropriate mold materials is crucial for HDPE molding. High-quality steels, such as hardened tool steels, are commonly used due to their durability and resistance to wear and corrosion.
Utilize advanced monitoring and control systems that provide real-time data on key process parameters such as pressure, temperature, and cycle times.
These methods help ensure that the mold surface is free from imperfections, scratches, or roughness that may impact the quality of the molded parts.
This makes it a popular choice for plastic product manufacturers. So, to unlock a world of creativity and use, embrace choices offered by HDPE molding.
It refers to excess material that protrudes from the mold’s parting line. Flashing occurs when the mold does not close properly, leading to material escaping between the mold halves.
Physically, HDPE is lightweight yet sturdy, providing an excellent strength-to-weight ratio. It retains its shape and dimensional stability even under extreme temperatures, making it suitable for diverse environments.
Susceptibility to UV Degradation: HDPE is vulnerable to UV degradation when exposed to prolonged sunlight or ultraviolet radiation. This may result in the material’s brittleness, color fading, or surface cracking over time.
Understand the specific material properties of HDPE that your product requires. Consider factors like strength, durability, chemical resistance, and flexibility.
These qualities make glass-reinforced polyamides superior to general purpose polyamides. The engineered resin has advantageous mechanical properties. It is suitable for injection molded parts that need to endure high static loads over long periods in high temperature environments.
It is advisable to avoid abrupt changes in wall thickness, as this can lead to uneven flow and potential defects in the final molded product.
Consider the required production volume. Injection molding is efficient for high-volume production, while blow molding and rotational molding are often used for medium to large production quantities.
Use simulation software to model and simulate the HDPE molding process. This technology lets you virtually test different mold designs, process parameters, and material properties before production, helping you optimize the process, reduce trial and error, and minimize waste.
It refers to the distortion or deformation of the molded part from its intended shape. It can occur due to non-uniform cooling, inadequate cooling time, improper mold design, or excessive internal stresses in the material.
The addition of glass powder or fibers to nylon resin creates this engineering grade resin. Glass is added to polyamides to increase their mechanical strength, rigidity, and hardness. It also makes them more resistant to creep, wear, chemical exposure, and high temperatures.
Chemical Resistance – LDPE and HDPE exhibit good resistance against many chemicals, making them suitable for applications that involve contact with various substances.
All three molding processes can accommodate HDPE, but certain properties may be more relevant to one process than the others.
Additionally, HDPE is known for its low friction coefficient, making it ideal for applications requiring smooth surfaces.
Surface analysis methods, such as profilometry and microscopy, can be used to examine the surface finish and texture of the mold.
Plastic Molded Concepts is a U.S based company that uniquely specializes in molding with engineered resins. We have been thriving in the plastic molding business for 45 years. We have the experience and certified in-house Master Molders, allowing us to take on projects of any complexity.
The mold is opened once the cooling process is complete, and the final rotational-molded HDPE product is extracted. This method is suitable for creating large, seamless, durable products like tanks, bins, and playground equipment.
Assess the cost implications of each molding process. Injection molding typically requires upfront tooling costs but offers high production efficiency, making it cost-effective for large volumes.
HDPE molding involves melting and injecting material into a mold cavity to create a specific shape. This process has revolutionized making products such as containers, PET bottles, and automobile parts. You can use it for the manufacturing of a bottle or container.
Maintaining uniform wall thickness throughout the part promotes even cooling and minimizes the risk of warping, sink marks, or uneven shrinkage.
You’ll find it suitable in processes including blow molding, injection molding, and extrusion to manufacture a wide range of products such as pipes, containers, bottles, automobile parts, and toys.
These include scratches, blemishes, or uneven texture on the molded part’s surface. It can arise due to contamination in the material, mold surface imperfections, inadequate mold cooling, or improper mold release agent application.
Blow and rotational molding may have lower tooling costs but are suitable for specific product types and production volumes.
GETTING A QUOTE WITH LK-MOULD IS FREE AND SIMPLE.
FIND MORE OF OUR SERVICES:
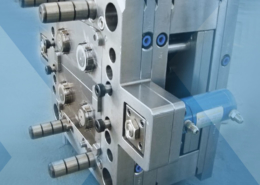
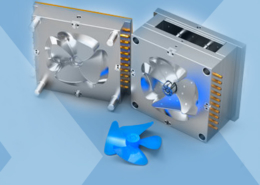
Plastic Molding

Rapid Prototyping
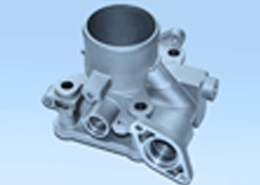
Pressure Die Casting
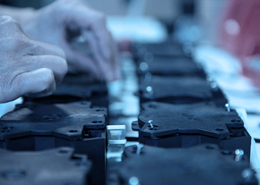
Parts Assembly
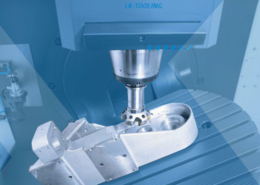