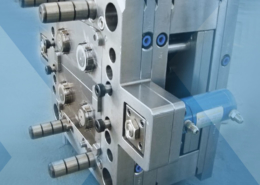
5 Safety Precautions for Projects Involving Plastic Injection ... - ppe for inje
Author:gly Date: 2024-10-15
Embracing a culture that prioritizes top-notch service, innovation, and technology, Rosti stands as one of the largest injection molding companies, operating multiple facilities with a combined production space exceeding 78,000 square feet. From humble beginnings, Rosti has evolved into one of the world’s most innovative producers of small- and medium-sized, medium- and high-volume plastic injection molded parts among European injection molding companies.
Operating from their main plant in Schwanenstadt, Upper Austria, Camo employs around 190 professionals who work within a converted area of approximately 10,000 square meters. Their commitment to excellence and comprehensive solutions has solidified their position as a trusted partner in the plastic injection moulding industry.
Omnia Plastica has been a presence in Italy and internationally since 1950, operating with a group of companies that covers the entire supply chain of technical and industrial plastic stock shapes. Utilizing various technologies, from extrusion to anionic polymerization, the company ensures a comprehensive range of services in the realm of technopolymers. The injection molding and surface treatment departments further enhance their offerings in the world of technopolymers.
Choose STAMM AG as your trusted partner for injection molding solutions that push the boundaries of precision and innovation.
Cast urethanes are also a good choice for applications that require smooth surfaces with little post-processing and inserts or threads that must be strong. For instance, producing 50 to 100 percent stronger bonding than standard heat-staked inlays using our unique cast urethane micro-welding technologies.
Type of Business: Precision Injection Moulding. Location: UK. History: Since 1962. Key Products & Service: Injection Molding, Mold Design, Mold Manufacture, Micro Injection Molding. Materials:ABS, PP, PE, PMMA, PA, PS, PC, PEEK, PVC, PET and more.
Type of Business: Precision Plastic Moulding. Location: Switzerland. History: Since 1962. Key Products & Service: Micro Injection Moulding, Precision Injection Moulding, Mould Design & Engineering, Mould Making, Hybrid Components Moulding, Multi Component Moulding, Thin-Wall Injection Moulding. Materials:ABS, PP, PE, PMMA, PA, PS, PC, PEEK, PVC, PET and more.
For this reason, it is essential to collaborate with a manufacturer knowledgeable about each method’s ins and outs. Molding partners can be had at the lowest possible cost and of the highest possible quality by going to SeaSkyMedical. The company is a medical plastic injection molding producer. SeaSkyMedical offers complete services and assistance to its consumers.
Injection-molded objects that do not have excessive complexity or require extra components can typically be used immediately off the machine for their intended usage in small manufacturing runs. Furthermore, hard tools can withstand higher temperatures than soft tools, making them ideal for certain high-temperature materials.
For three decades, Rosti (formerly Plastic Components, Inc.) has served as a leading manufacturer of plastic molded parts, leveraging engineering expertise, automation, and technology to redefine industry norms and provide clients with a strategic partner for their injection molding needs.
It is essential to determine which tasks necessitate the utilization of heavy equipment to prevent putting operational efficiency and product quality at risk. Hard tooling can be the only option if the application working on calls for instruments with extraordinarily exact designs.
As a member of the EWF Invest Group and one of the biggest injection molding companies, Robust Plastics manufactures sophisticated, premium custom mold and plastic injection molding products for automotive, technical parts, and industrial packaging applications.
Because of the material qualities of cast urethanes and even 3D-printed parts, smaller manufacturing runs have permitted the creation of custom-tailored parts at a low cost.
When it is understood that hard tooling will eventually be employed, but parts are required immediately, cast urethanes serve as a stepping stone. Cast urethanes meet market deadlines while the tool is being developed and the first shot is fired.
Having thrived in the plastic injection molding industry for over five decades, Chess Plastics, based in the Midlands, has evolved from a small family operation into a round-the-clock success story. With 18 large molding machines ranging from 400 tonnes to 1300 tonnes lock size, they cater to a diverse range of industries. Among many European injection molding companies, their capabilities extend to the cost-effective production of large injection molding products, crafting components that range from 300 mm square up to 1400 mm square.
Sungplastic, a Chinese plastic injection molding factory with over two decades of expertise, is dedicated to rapid prototyping, plastic injection molding production, and plastic mold fabrication, low volume injection molding and medium to high volume production. Our focus lies in customized plastic part molding across diverse sectors, including electronics, automotive, consumer products, and the medical industry, including low volume injection molding. With a remarkable proficiency in producing low volume injection molded plastic products with precise tolerances and exceptionally high surface finishes, Sungplastic stands out in the plastic injection molding industry and has became one of Chinese biggest injection molding companies.
This saves time and money by eliminating the need for soft tooling for market tests. Making prototypes and presenting them to industry experts, employees, and other relevant parties allows for getting input on the parts before mass production begins.
Camo serves as one of comprehensive and the biggest plastic injection molding companies, offering expertise in development, mold making, custom injection moulding, and assembly of plastic molded parts, whether they are intended for the automotive, electronics, household/construction, or medical technology sectors.
Another crucial consideration is the type of sheet metal used. If the metal is soft enough, harsh tools may not be necessary. However, hard tooling may be required to get the desired results if the sheet metal is exceedingly thin or has intricate characteristics.
When the item’s geometry necessitates lengthy injection molding tool design development durations, it’s recommend shifting to cast urethanes. Cast urethane components use 3D-printed master patterns and CNC-machined master patterns to generate a first shot with the precise geometry in half the time required by injection molding.
Components made of silicone, also known as soft tooling, are created using urethane molding. Whereas components made of steel or aluminum are produced using injection molding know as hard tooling.
Type of Business: Plastic Injection Molding Supplier. Location: Austria. History: Started in 1988. Key Products & Service: Tailored Plastic Injection Moulding, IK Injection Molding, Insert Technique, Tool making. Materials:ABS, PP, PE, PMMA, PA, PC, PVC and more.
Type of Business: Precision Plastic Injection Molding Supplier. Location: Italy. History: Started in 1950. Key Products & Service: Plastic Injection Moulding, Machining, Extrusion. Materials:ABS, PP, PE, PMMA, PA, PC, PVC and more.
Drawing on a wealth of professional plastic injection molding knowledge and low volume injection molding production experience, Sungplastic has proudly served numerous countries and established brands worldwide as a trusted plastic molding fabricator.
Type of Business: Plastic Injection Molded Part Maker. Location: UK. History: Started in 1967. Key Products & Service: Tooling, Large Injection Moulding, Engineered Plastic Injection Moulding. Materials:ABS, PP, PE, PMMA, PA, PS, PC, PEEK, PVC, PET and more.
Working with soft tools is ideal for producing fewer than a few thousand pieces because they are not required for an extended time. Soft tooling allows for cost reductions and faster completion of on-demand, low-volume projects.
At the core of Sovrin’s corporate philosophy lies the rigorous application of lean 6 sigma principles, showcasing their unwavering commitment to operational efficiency and unmatched quality standards. With a team of 140 dedicated specialists and a fleet of 52 state-of-the-art molding machines, Sovrin is at the forefront of fabricating intricate components. This expertise is particularly evident in their pivotal role within the healthcare industry, where they have been instrumental for over three decades.
Located in Bury, Lancashire, on a spacious 44,000 sq foot site, they stand as a well-established, family-owned plastic part manufacturing company with a dedicated team of 35 staff. Their team combines experience, technical knowledge, drive, and enthusiasm to deliver outstanding results. Among many European injection molding companies, their commitment is unwavering, aiming to surpass customer expectations by producing quality products promptly and with a friendly attitude.
With an impressive legacy spanning over 50 years, Sovrin Plastics has established itself as a leader in the field of injection molding. Among many European injection molding companies, their unwavering dedication to precision micro molded parts permeates their specialized work in the medical, electronics, and engineering sectors.
Checklist for Casting with Urethane: The initial step in developing a soft tool for urethane casting is creating a master pattern. Because the surface of the master pattern is immediately transferred from the master pattern to the silicone throughout the process of making a soft tool, the surface must be in good condition.
Regarding durability, soft tools cannot compete with hard tools; silicone tools are good for 25 to 50 shots of a part before they must be retired. It is conceivable to build tools that endure thousands or hundreds of thousands of shots.
Chess Plastics is a plastic injection molding company deeply attuned to the needs of our customers. Their commitment is evident in a consistent and sustained investment plan that focuses on acquiring new machines, implementing automation, and providing ongoing training to enhance the skills of their workforce. Despite their growth and success, Chess Plastics remains a family-run business, with Glyn and Gareth Olden serving as the controlling Directors. Their dedicated team operates efficiently from a spacious 52,000-square-foot facility in Droitwich, Worcestershire, running a 3-shift system 24 hours a day.
Omnia Plastica, the parent company, is headquartered in Italy and maintains offices in Busto Arsizio (Varese), Cinisello Balsamo (Milan), and Parma. The Group’s initial processing and distribution subsidiary, Industrial Plastics Europe, was established in Holland in 1972. To comprehensively cover northern European markets, the Group established Plastim in the UK in 1997. More recently, in 2013, Plastem was inaugurated as a new branch to oversee distribution on the African continent.
Furthermore, material, volume, turnaround time, and shape will all play a factor in any soft versus hard tooling selection. Still, the project now has access to many options that were not accessible a decade ago.
European injection molding companies have embraced these trends, adapting their processes and investing in state-of-the-art machinery to meet evolving customer needs. Furthermore, the industry has been actively exploring new materials, such as bioplastics and recycled polymers, to align with the growing emphasis on environmental sustainability. With their expertise, technological prowess, and dedication to excellence, European Injection Molding Companies continue to lead the way in delivering cutting-edge solutions to diverse industries across the continent.
Cast urethanes are used as the product’s initial release to avoid downtime and gather consumer reaction. A hard tool can take weeks to complete, whereas a cast urethane end-use product can be produced in five to seven days.
Type of Business: Bespoke Injection Molding. Location: UK. History: Since 1967. Key Products & Service: Micro Injection Moulding, Cleanroom Injection Moulding, Plastic Injection Moulding of Precision Components, Medical Device Assembly & Packing, Mould Tool Manufacture, Prototyping. Materials:ABS, PP, PE, PMMA, PA, PS, PC, PEEK, PVC, PET and more.
However, when working such as corporate stakeholders, this must consider the request behind the scenes. It would be more cost-effective to show them the soft tool version rather than constructing hard tools for them to view. When it comes time to build the production tools, switch to a hard tooling strategy.
Steel/aluminum tools are used for injection molding prototypes or bridges. When a high number of parts, typically 100 to 100,000s, are required, hard tooling is used.
Hard tooling is a tooling technique that is commonly utilized in plastic injection molding. Additionally, hard tooling is a manufacturing process that involves making tools and dies out of tougher metal alloys that are typically utilized in the prototype stage of the manufacturing process. The generation of a product capable of being mass-produced accurately and consistently should be the end goal of any hard tooling.
Sovrin’s production operations are meticulously carried out within controlled Class 7 & 8 Cleanrooms, ensuring the highest level of cleanliness necessary for manufacturing medical-grade products. Embracing technological advancements, Sovrin stays at the forefront by utilizing pioneering materials, including bio-absorbable and conductive polymers, to drive innovations in medical and electronic product development.
Steels of the finest quality, such as H13 or 420, are used in producing hard tools used in mass manufacturing. The production of a difficult instrument involves additional steps and additional time.
Type of Business: Plastic Molded Part Manufacturer. Location: UK. History: Started in 1896. Key Products & Service: Custom Plastic Molding, Roto Molding, Tooling, Overmolding, mold building, prototype production, assembly, packaging, and secondary services Materials:ABS, PP, PE, PMMA, PA, PS, PC, PEEK, PVC, PET and more.
Seasky Medical serves you with medical injection molding solutions from design to tooling to material selection and manufacturing. Contact our specialized team and solve your problem now.
Equipped with flexible manufacturing facilities, their setup is designed to cater to your specific needs. Whether you require a high-volume continuous supply, a few thousand parts throughout the product life cycle, or merely fifty to one hundred parts for design verification in the correct materials before committing to the expense of production tooling, among numerous European injection molding Companies, they are committed to delivering the custom injection molded parts you need, precisely when you need them.
Choosing the appropriate solution for the sheet metal tooling process, this will allow to produce higher-quality work while still adhering to the schedule and budget constraints. The differences between the various tooling techniques are outlined in this article section.
Among European injection molding companies, Micro Systems is your go-to expert for ultra-precision mold making and plastic injection molding in the UK, providing comprehensive turnkey manufacturing solutions. Boasting over two decades of experience in mold making and injection molding, they offer a diverse range of custom services. Their offerings include mold design, mold manufacture, factory acceptance testing (FAT), and prototype validation, extending to the production of multi-cavity mold systems and mass-production supply of molded components. They cater to various industries, including Medical & Pharmaceutical, Ophthalmic, Biotech, Diagnostic, and other Industrial markets.
The process of hard tooling begins with constructing a tooling design at the beginning of the procedure. After that, the design is utilized to build a mold, which represents the thing being sought after in an unfavorable light. The positive image of the product is known as a die.
As a responsive injection molding company based in the UK, they bring over 45 years of experience to the table in crafting high-quality injection-molded parts and assembled products. Their diverse range of injection molding machines, spanning from 20 tonnes to 250 tonnes, enables to manufacture large plastic parts weighing up to 1 kg, as well as precision miniature parts weighing just a few milligrams.
Type of Business: Custom Plastic Injection Molding Company. Location: Sweden. History: Over 30 years. Key Products & Service: Plastic Part Design and Engineering, Custom Molding, Prototype Production, Tooling Building and Tool Transfer, Metal to Plastic, and more services. Materials:ABS, PP, PE, PMMA, PA, PS, PC, PEEK, PVC, PET and more.
As a leading manufacturer specializing in precision-engineered injection molds and micro molds, Micro Systems leads the way in innovative solutions. Their capabilities include the design and production of multi-cavity, high-volume molds, complemented by turnkey solutions to meet the manufacturing needs of medical devices. With Class-7 cleanroom production capabilities, they ensure the highest standards of quality.
Type of Business: Plastic Components Molding. Location: UK. History: Started in 1975. Key Products & Service: Tooling, Large Injection Moulding, Engineered Plastic Injection Moulding. Materials:ABS, PP, PE, PMMA, PA, PS, PC, PEEK, PVC, PET and more.
Type of Business: Plastic Injection Molding Manufacturer.Location: Dongguan, Guangdong province, China.History: Over 20 years.Key Products & Service: Plastic Mold Manufacturing, Plastic Injection Molding, Overmolding, Insert Molding, Rapid Prototyping.Materials:ABS, PP, PE, PMMA, PA, PS, PC, PEEK, PVC, PET and more.
An injection molding machine injects material into steel/aluminum tools. The equipment takes fewer people to inject mold into the mold than silicone molds. The material will cure in seconds to minutes, allowing for substantially more pieces to be produced than with silicone tools.
Curing time can range from 1 to 24 hours, depending on the material. After the components in the molds have cured, the molds are opened by hand, and any necessary finishing is done by hand.
Production volume is essential when deciding whether to use soft or hard tooling for sheet metal. Soft tooling may be the most cost-effective option if the low volume is the norm because it is frequently less expensive than hard tooling. Soft tooling can also be used for prototyping before switching to hard tooling for bigger production runs.
Cast urethane pieces require a mold that can be broken apart to release the part; however, by utilizing 3D printing, these molds may be made and deployed more quickly, resulting in the delivery of sophisticated soft tools in days.
At Excelsior, entrust your plastic product vision to our extensive expertise in plastic part manufacturing. Boasting a century-long legacy, their proficiency in rotomoulding empowers us to create plastic products across diverse sectors, including agriculture, education, sports, and leisure.
After the curing process is complete, the master design is removed. The silicone is then cast using one of many different types of industrial cast urethane materials to make the finished cast product.
Hard tooling is commonly used in products that demand high precision, such as electronic components. It is also appropriate for items that will be made in large quantities. Hard tooling can be costly initially, but long-term savings can be significant.
Rosti Group, a multinational contract manufacturer and plastic injection molding company with eight production facilities across Europe and Asia, has successfully acquired Plastic Components, Inc., expanding its global geographic reach.
The speed, versatility, and low cost of soft tooling are three of its most well-known benefits. Traditional hard tooling operations are more expensive than soft tooling techniques, which are less labor-intensive.
This is derived from the mold and utilized to construct the die. After the mold has been created, the product can be manufactured in huge quantities during mass production.
In 2021, the Group expanded its portfolio by acquiring PLASTICI INDUSTRIALI, a renowned player in the field of Italian engineering stock shapes.
When building hard tools too quickly, it may face severe problems in the future, resulting in higher-than-expected production costs and missed product deadlines. To put it another way, take advantage of soft tooling wherever it is feasible to do so since, in the long run, it will save a significant amount of money, time, and money.
STAMM AG is a renowned leader in the field of injection molding technologies, known for its unwavering commitment to innovation and excellence. With a blend of rich heritage and a forward-thinking approach, they are the ideal partner for tailor-made solutions that exemplify precision and exceptional performance.
Choose Sovrin Plastics as your trusted partner for injection molding solutions that combine decades of expertise, operational excellence, and a commitment to advancing technology in the medical and electronics sectors.
Recognizing the difference will make it easier for the project to complete on time and within budget while ensuring that all components are functional.
Priming and painting, and even glossy paint on surfaces where clarity is essential, is the typical next step after dry blasting or hand sanding on the interior and outside of a building. After completion of the master pattern, a one-of-a-kind procedure of pouring and curing silicone is utilized to secure the pattern.
Medical Carrying Case in PolyJet Blue Starting with a smoother surface makes the process go more quickly. Which is why hand finishing is required for all SLA and PolyJet master designs before tools can be created.
Contact SeaSkyMedical now to take advantage of thier product development, from prototypes through full-scale production.
Beyond mold making and component supply, Micro Systems offers additional services such as factory acceptance testing (FAT), mold validations, and technical molding support, forming a comprehensive service package. They hold ISO 9001 and ISO 13485 certifications, underscoring our commitment to quality. Their operational facilities are strategically located in Warrington, UK, and Singapore, facilitating global accessibility for their services.
Furthermore, STAMM AG’s capabilities extend beyond the realm of miniature components. They excel in the fabrication of hybrid components, ingeniously combining different materials to create multifaceted solutions that satisfy both aesthetic and functional requirements. Their expertise in multi-component molding is unparalleled, incorporating sophisticated technologies such as rotary tables, index plate systems, and core-back processes. Each of these techniques is meticulously customized to meet the intricate tooling needs of their esteemed clientele.
Molding procedures involving urethane and injection molding are the two most widely used. The type of tooling used to create the pieces is one of the most noticeable variations between the two methods.
Plastic Mold Manufacturing Plastic Injection MoldingRapid PrototypingCNC MachiningSheet Metal StampingPressure Die CastingSilicone & Rubber PartsSurface Finishing
Two different types of additive manufacturing produce the best results in terms of surface smoothness, feature detail, and production speed when it comes to the creation of soft tools:
Among many European injection molding companies, their expertise in precision injection molding is unmatched, developed over three decades of dedicated practice in creating components with extraordinary precision, fine tolerances, and controlled shot weights. As one of strong micro molding companies, they consistently produce parts with accuracies as tight as ±0.01mm and a weight range spanning from 0.01g to 150g. In the realm of micro-injection molding, they stand out by manufacturing components in large quantities that defy traditional weight limitations, delving into the microgram range.
Making a urethane mold is part of the soft tooling process, which is also commonly referred to as urethane molding. In most cases, prototypes or low-volume manufacturing runs demand for the utilization of molds of this particular sort.
Despite being a cost-effective solution for mass manufacturing of similar products, injection molding needs higher precise machines for creating low-volume or highly customized products especially for medical molding companies. Moreover, the various molding procedures necessitate the use of specific tools. It is critical to take the proper strategy to provide customers with parts that work properly.
Camo’s unwavering philosophy is centered around providing integrated support to their customers throughout the entire value chain. With a focus on collaboration, they offer consulting services in planning, construction and optimization, tool/mold making, injection moulding, automation, assembly, and packaging since their establishment in 1988.
A dedicated high-tech division, Bell Safety Defence&Security, specializes in the design, manufacturing, and sale of civil and military safety devices, including helmets and shields. The Bell Safety Group, a family-owned industrial company with a modern management model and an international distribution network, operates on the principles of reliability, competence, and innovation. Comprising four companies covering the entire plastics processing chain, the group is widely recognized as a primary technological mediator through its injection moulding products and plastic injection moulding processes among European injection molding companies.
Type of Business: Plastic Injection Moulding Manufacturer. Location: Austria. History: Started in 1874. Key Products & Service: Tool Design & Construction, Injection Molding, Assembling & Finishing. Materials:ABS, PP, PE, PMMA, PA, PC, PVC and more.
Molds made of silicone can be utilized for prototyping, bridge manufacturing, and the low-volume production of anything from one to hundreds of individual pieces. The majority of silicone molds allow for 25 shots to be poured into each cavity.
The level of detail relay that platinum-reinforced silicone possesses is sometimes compared by our engineers to that of human hair. 3D printing results in the most efficient use of resources and the quickest turnaround times for master patterns.
There were relatively few cost-effective options for creating small to medium batches for limited market releases and bridging applications before the invention of cast urethane molding. One of these alternatives was cast urethane molding.
A pre-hardened steel tool is what’s known as a soft tool. It’s a low-cost manufacturing solution that’s ideal for low-volume production. Because pre-harden steel is a lesser grade of steel with reduced hardness and wear resistance, the soft tool can only endure molding cycles of no more than 500k shots, and it is difficult to maintain tight tolerances.
Rotomoulded products, like many other plastic manufacturing methods, utilize thermoplastics that can be melted and reshaped without compromising strength and integrity. Leveraging their experience as plastic manufacturers, this flexibility allows to fashion an almost limitless array of shapes from thermoplastics, offering endless possibilities for your product. Essentially, if you can envision it, we can bring it to fruition.
As a premier plastic injection molded parts manufacturer, we specialize in working with engineering-grade plastics, thermoplastics, modified plastics, and composites to create tailor-made molded plastic components. Our commitment extends to meeting specific requirements such as chemical resistance, flexural strength, durometer, and yield strength.
Seasky Medical serves you with medical injection molding solutions from design to tooling to material selection and manufacturing. Contact our specialized team and solve your problem now.
There are several factors when considering soft and hard tooling for injection molding. Before settling on a method, it is necessary to consider the type of material, the costs, the amount, prototypes, and many other factors.
It is a standard option for producers who produce a tiny number of goods, often between one and one hundred units at a time. In most cases, silicone molds are injected with material that is gravity-fed through a tube.
The company’s plastic injection molding production expertise is complemented by a wide range of services, including just-in-time delivery, tool design, and new plastic injection molding product development. The utmost quality, customer satisfaction, and service orientation are prioritized. They hold certifications in accordance with IATF 16949 and ISO 9001 quality standards.
GETTING A QUOTE WITH LK-MOULD IS FREE AND SIMPLE.
FIND MORE OF OUR SERVICES:
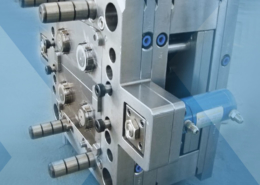
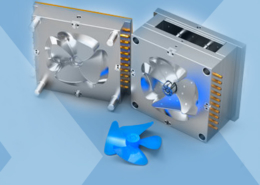
Plastic Molding

Rapid Prototyping
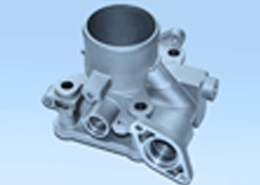
Pressure Die Casting
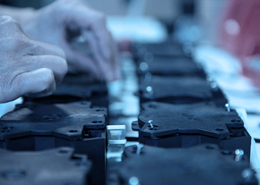
Parts Assembly
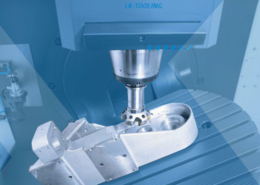