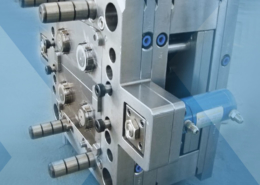
5 Major Advantages to Using Plastic Injection Molding for ... - plastic molding
Author:gly Date: 2024-10-15
The second process creates Part 2, which contains Part 1. This process is similar to insert molding, with the difference that, instead of a metal insert, both parts are created with plastic injection molding.
The process results in a final assembly with greater strength than mechanically fixing the plastic and metal parts together.
Low volume production can be considered anything between a hundred to a couple of thousand parts. For these low-volume applications, manufacturers usually produce the molds in-house and do the molding themselves.
What is the cost of injection molding? This is a commonly asked question by people wondering about adopting this technology.
This cost can vary based on the process used to create the molds. Usually, three processes are employed for this purpose:
Not at all. Injection molding is one of the cheapest manufacturing processes. Even so, you can still lower the injection molding costs per molding cycle by following the tips suggested in this guide.
Make full use of the molds by reusing them for various applications. You can not only use the same mold for the same part but also for similar parts as well. This can be done by making adjustments or mold mods wherever possible.
Injection molding is one of the most widely applied manufacturing processes nowadays. Every day, you see and touch multiple parts created by this process, like bottle caps and plastic handles.
While the molding equipment is a one-time investment, creating the mold and mold base for the part costs money. It is an expense for every different part produced. Therefore, tooling costs are one of the most important driving factors for injection molding.
Family injection molds also have multiple cavities inside them. However, the part cavities are for different parts, so a family mold can simultaneously create different shapes of injection molded parts.
This process creates plastic parts with metal inserts fused directly into them. An example of this is the metal fasteners that you see inserted in plastic components.
For example, you can manufacture the top and bottom ends for a plastic container in a single-family cavity injection mold. This type of mold cavitation is a more expensive option in terms of mold cost. But they make the overall production process faster and cheaper.
CNC machining has a little drawback in terms of the machine cycle for making molds. These machines require setup time for the tooling and changing the tools for different cut shapes.
Highly complex designs with more cavities and high mold polish result in extra costs. Such designs require research, development, and technical expertise. For this purpose, you can hire a professional or outsource the design process. Both options incur expenses.
The size and design of the part will considerably affect the cost. Large injection molded parts require greater material costs and larger molds. Similarly, complex designs may require a multi-step molding process.
The features of the final product also impact the injection mold cost. If the product has complex features, these might require small components made by a separate injection molding process. One way to lower costs is to eliminate unnecessary features during the design stage.
Volumetric metric capacity is the right way to specify the injection unit and compare suppliers. Tackle this analysis carefully to account for the type of material used by your application. Most molding machine manufacturers present injection unit specifications based on PS. But the performance data will be different for other materials.
If the manufacturer needs additional services such as polishing or secondary finishing for the product, these represent an extra expense. While it is not a part of the injection molding cost, the service provider might consider it an added cost.
Large volume production deals with hundreds of thousands of parts. For this comparison, let us assume we are producing 100,000 parts of the same type.
Just like CNC machining, EDM also has high accuracy. However, while CNC machining can be used for materials other than metals, EDM is only suitable for metal molds.
This is, no doubt, a big expense for any business. Therefore, most manufacturers outsource the injection molding process to experts like 3ERP with high-end injection molding machinery. Outsourcing makes injection molding a cost-effective option, in which the client can source the lowest cost for the part required and minimize the variable costs of production.
Tonnage is presented by manufacturers in three ways: kilonewtons, metric tons and U.S. tons. Asian suppliers typically refer to kilonewtons, whereas European suppliers will discuss metric tons and U.S. suppliers and customers talk about U.S. tons. A metric ton is basically a 10th of a kilonewton. A U.S. ton is going to be 10 percent more than a metric ton.
Injection molding is a popular manufacturing process for creating many parts and components. As such, learning about the costs of producing an injection molded part is vital before considering this process for your manufacturing operation.
An example of this is the soft rubber grip that you see embedded into plastic and rubber products, such as toothbrushes.
The cost of material for plastic resin pellets used in the injection molding process is from $1 per kg to $5 per kg. The final cost of injected material will depend on the amount used, which, in turn depends on the design required.
This is the simplest type of injection molding process. The plastic is injected directly into the mold cavities to create the final piece. Of the three different molding processes, this one has the lowest cost.
Electrical Discharge Machining is also known as EDM. This technology is utilized for creating molds with intricate shapes. It is accomplished by using electrical discharges to melt and bend the metal workpiece and give it the desired shape.
We are often asked, “My total shot weight is 100 ounces. Does this mean I need a 100-ounce shot?” No! Here are some of the common rules of thumb that you should use in specifying the injection unit.
After reading this guide, you can evaluate the exact manufacturing costs that injection molding will require for your particular requirements.
Repair Costs: Injection molding is a mechanical process requiring multiple types of equipment. Therefore, there are bound to be repair and maintenance processes that result in expenses.
The clamp has tons to consider. Yes, that pun was intended. Beyond just clamp tonnage, other important factors are tie-bar spacing, minimum mold height, maximum mold height, stroke and daylight.
This is a little more complex process than basic injection molding. It involves positioning metal inserts in the mold. Once the metal inserts are in position, the plastic injection molding takes place.
Target 20 to 80 percent shot capacity for applications using general-purpose resins but a 30 to 50 percent shot capacity for engineered resins.
You might have seen that manufacturing costs per part become less when the production takes place in large quantities. The same idea holds true for injection molding as well.
The benefit of self-mating parts is that you can use a single half mold to create the entire part. It keeps the cost of the mold low, and the plastic injection mold size is half. This method increases the volume of production.
3D printing is one of the cheapest and fastest ways of making molds for injection molding. This process requires nothing but a 3D printer, so the expense is considerably less. Additionally, there is no need for skilled operators, saving labor costs.
After reading this article, you now have a better idea about the plastic injection molding cost and how it varies from project to project. You even know about the cost variations that occur due to the injection mold cost and injection mold tooling cost.
3ERP provides every injection molding service you might require, from low-cost injection molding to mass production parts. There are even material options, such as thermoplastic, thermoset silicone, and metal injection molding.
To get a better understanding of the plastic injection molding costs for a part for different production volumes, let’s examine a typical case.
While the process is cheap compared to its alternatives, you can further reduce the costs. For that purpose, here are some pointers that you need to take into account:
Analyze the clamp specifications and the injection unit specifications of the molding machine under consideration separately.
Professional industrial injection molding equipment costs between $50,000 and $200,000. There may also be shipping costs involved. These machines are not for hobbyists and amateurs as they require skilled operators.
Single cavity molds have one cavity inside. So they make one part per cycle time. While the cost of the mold is less, the production rate of parts is slower. This leads to higher part costs.
Setup Costs: There are specific setup requirements for every step of injection molding. For instance, when making the molds, some setup of tooling is required. And setting up the mold and configuring the equipment during injection molding all involve an operator’s time.
Multi-cavity molds and family molds allow you to multiply the production rate and reduce the cycle time. This can reduce the cost of the entire operation by a significant margin, especially in medium to large production runs.
As stated in the plastic injection molds cost overview, higher volume means lower costs per part. This, combined with savings in mold size and number of molds, lead to significant savings in the final plastic injection mold costs.
Medium volume production can range between five thousand to tens of thousands of parts. For this production scale, manufacturers usually outsource the mold production and molding processes.
How about when you purchase an injection unit that is too large for the minimum shot size required? You underutilize the injection unit. This may result in shot inconsistencies since the ratio of material from the seating of the check ring to shot size will result in inconsistent shot weights. A certain amount of material is required to set the check ring. As shot utilization goes down, the effect of the check valve on the material flow goes up. Additionally, you might end up with residence time that is too long, causing the material to degrade.
Bigger parts are not always better parts. When the size of the parts increases, so does the expense of injection molds required for the parts. If the same process can be accomplished by reducing the part size, it is a good idea to opt for it.
Many established brands such as BMW, Lamborghini, and Electrolux already use the injection molding services offered by 3ERP.
Get in touch with 3ERP today to get an injection molding quote for your project. Whether it is a simple injection molding project or something that deals with inserts or overmolding, we handle it all!
Specialize in CNC machining, 3D printing, urethane casting, rapid tooling, injection molding, metal casting, sheet metal and extrusion
There is small-scale injection molding equipment that businesses keep in-house. Then there are large injection molding machines typically used by service providers and those in the large-scale manufacturing industry with large production volumes.
Generally speaking, to get an injection mold cost quote, you need to choose the manufacturer who can provide you with the best results at the cheapest rates. 3ERP is your answer in this regard.
One of the mistakes many molders make is to misunderstand stroke vs. daylight. Stroke is the dimension from either the minimum mold height or the maximum mold height, to the most open position of the moving platen. Daylight is the dimension of the face of your fixed platen to the face of the moving platen in its most open position. Stroke and how it is referred to changes depending on whether you are talking about a toggle machine or a hydraulic cylinder machine.
This is a very wide price bracket. The exact value fluctuates based on several components involved in the injection molding process. These factors that influence the cost are:
The base cost of an injection mold is not a fixed number that will be the same for every application. It is a varying value that can fall between a couple of hundred to hundreds of thousands of dollars.
The injection unit is often an afterthought when it comes to quoting machines. Factors to consider include material type, fillers in the material, the molded shot size, the cycle time, the residence time, the injection plastic pressure, screw recovery time and screw geometry.
Injection molding machinery suppliers often receive requests for quotes asking for pricing based on the tonnage of the machine only. When asked for more details, the buyer might respond, “I just need a 1,000-ton quote.” Better to consider the molding machine as two separate pieces — the clamp unit and the injection unit — and dig into the details to help ensure you purchase the best configuration for your needs.
What happens if you purchase a machine and the screw and barrel are too small for the application? You overutilize the injection unit. When processing, the residence time may be too short, restricting the homogenized melt; recovery time may exceed the cooling time and you’re wasting precious cycle time.
Complex features can call for complex molds and extra steps in the injection molding process. Therefore, eliminating unnecessary features results in a lower cost for injection molds.
Most steps involved in injection molding are automated and run by software systems. For instance, CNC machines are run by Computer Numerical Controlled software, 3D printers run on their own software, and injection molding also has automated processing.
Plastic injection molding offers a certain degree of versatility concerning the plastics you can use as the injection material. Some examples include ABS, PU, PE, PP, and PC.
In this regard, you can eliminate any features that are just for the sake of cosmetic finishes. This will end up saving money.
DFM stands for Design For Manufacturing. DFM in injection molding refers to producing a part that serves the purpose of the customer and is within their stipulated budget.
An important factor to consider is tie-bar spacing. Today’s molders are trying to put big molds into clamps. Don’t forget about minimum mold height, maximum mold height, stroke and daylight to ensure the largest mold you plan to run will fit comfortably in the machine.
This article examines the costs of injection molding. Understanding the factors that influence these costs will help you estimate your injection molding project costs.
Let's look at the types of clamp design. The toggle clamp is a time-tested design that has been around for decades, as has the clamp design based on a hydraulic ram. Over the last 20 years, the industry developed the two-platen machine, which for practical purposes has replaced the hydraulic ram. Last is the C-frame clamp design typically employed by vertical machines; it has more recently been seen in horizontal machines but only those offered by one supplier. The most common clamp designs are toggle and the two-platen.
Say you are molding PP, though, with that same screw. PP has a melt factor of 0.73 gram per cubic centimeter. To reflect the true performance specifications using PP, take the volumetric capacity of 9,698 cubic centimeters, multiply it by a melt factor of 0.73 gram per cubic centimeter of PP, and you have 7,079 grams of processable weight, not 8,825 grams. There is a loss of almost 20 percent in injection capacity between the PS-based specification sheet data versus the performance you will experience using PP. This is significant, especially when you consider materials that apply to the 20/80 rule. You might need to move up an entire injection unit size to maintain the proper injection pressures, proper screw recovery time and proper residence time.
Considering the maximum shot size of any given injection unit, general-purpose resins like PP, PE and PS will run best if the shot size is 20 to 80 percent of the injection unit’s shot capacity — the 20/80 rule. Engineered resins like ABS, PC, EOM and nylons will run best if the shot size is somewhere between 30 and 50 percent of shot capacity.
When you are fulfilling a large production volume, you will require a corresponding large number of molds. However, the cost of the molds does not increase linearly. For example, if the cost of a mold is $1 per part for 100 parts, the cost for 5000 parts can be about $0.5 per part, and for 100,000 molds it can be $0.25 per part.
For example, a screw with 9,698 cubic centimeters of volumetric capacity will process 8,825 grams of PS at 26,397 PSI. This is based on the material’s melt factor of 0.91 gram per cubic centimeter.
Now that you know the various costs associated with injection molding, one vital question remains unanswered. What will be the cost of injection molding for my project?
The best thing is that you get your parts made by a world-class team of engineers using the most advanced equipment, without bearing any of the costs for the same.
Beyond just clamp tonnage, review other important factors such as tie-bar spacing, minimum mold height, maximum mold height, stroke and daylight.
Are you considering using injection molding service for your next project? Then send a query to 3ERP at our contact email, and our team will reach out to you with the best price available for your requirements.
Overmolding is also a little more complex than basic injection molding. In overmolding, an initial part is created using injection molding, let us say Part 1. Then, Part 1 is placed inside another mold, and another plastic injection molding process takes place.
Operator Costs: Regardless of the self-regulated machinery used, an operator must oversee the process. The cost of the operator is something to factor into the labor costs.
For low production quantities, manufacturers create molds of 3D printed polymer resin since it is cheap and doesn’t have to go through a long production cycle.
A single part can be approached through different CAD designs. However, not every design idea is ideal. Some designs for the same part may lead to time and resource wastage. Therefore, simplifying part complexity through efficient CAD design ensures the best utilization of resources.
CNC machining is usually employed for metal molds. A stainless steel mold or an aluminum mold would be typical. For example, machining an aluminum mold uses cutting tools to remove material from an aluminum block. This method of machining creates aluminum molds with unmatchable preciseness.
For DFM, analysts consider several factors based on art, science, and technology to find the most efficient design, resulting in reduced injection mold costs.
Multi cavity molds have multiple cavities inside, so they can make more than one part simultaneously. Although this type of mold has a higher initial cost, it leads to significantly lower part costs. It is a cost-effective solution for large quantities.
The entire production run for this volume takes about 3 days to manufacture the finished parts. For a 100-part run, let us assume the following parameters:
This is one of the most creative ways to save money on injection molds and simplify the design. Self-mating parts are the parts that attach to themselves when rotated 180 degrees.
Similarly, the labor costs per part also decrease for larger production volumes. While the final cost of production increases for higher production volumes, you will incur significantly lower per part expenses.
As you can see, the injection molding costs per part decrease significantly for high-volume production. Therefore, high-volume projects have the best cost-effectiveness for injection molding costs.
Using technologies like insert injection molding and overmolding helps save costs in the long run. For instance, insert molding eliminates the need to create threads on the plastic for attaching it to metal parts.
Every injection molding material has its specific benefits. The perfect material for your injection mold will depend on your requirements and budget constraints.
Unless otherwise specified, most machine manufacturers quote their molding machines with a general purpose (GP) screw. But many applications should be using a mixing screw, and sometimes, a barrier mixing screw.
The injection mold cost of 3ERP will come as an exact quote that matches your precise requirements. Therefore, you will not be paying extra for something you do not require.
Always remember to adjust your calculations for the right output factor of the material that you'll be running and then adjust your specifications properly for the calculated shot size.
GETTING A QUOTE WITH LK-MOULD IS FREE AND SIMPLE.
FIND MORE OF OUR SERVICES:
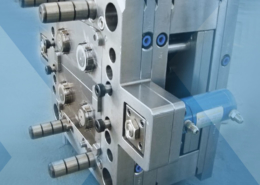
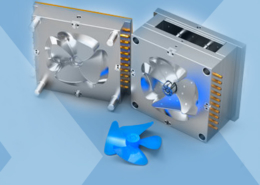
Plastic Molding

Rapid Prototyping
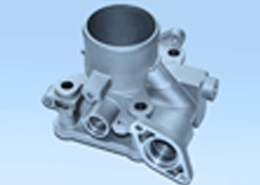
Pressure Die Casting
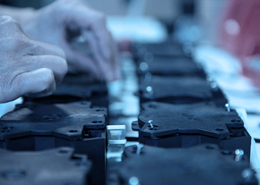
Parts Assembly
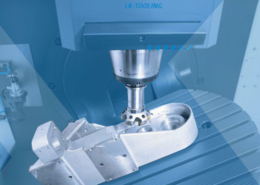