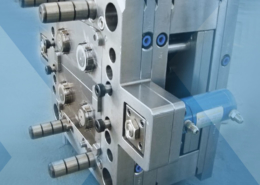
5 Advantages of Injection Molding for High-Volume ... - high volume injection mo
Author:gly Date: 2024-10-15
Advanced precision ceramic & plastic molding enable us to deliver high quality, cost-effective parts every single time and for a wide range of clients operating in specialized industries.
The process of manufacturing plastic injection molding is ideal for producing large quantities of identical objects due to the following key advantages:
Special varieties of plastic are typically used in the injection mold manufacture, including: polycarbonate, acrylonitrile butadiene styrene (ABS), nylon, etc.
We use high-quality resins in the process of manufacturing plastic injection molding, ensuring the durability and dependability of the final product. We also offer in-depth materials, expertise, and experience, enabling you to optimize quality and price.
The life of an injection mold is directly related to the type of mold, the type of material injected into it, and the number of parts produced.
American inventors and the first plastic injection molding manufacturers, brothers Isaiah and John Wesley Hyatt patented the very first injection molding machine in 1872. Despite its seemingly simple original design, this machine made the manufacturing process infinitely easier. It also served as the prototype for the sophisticated machines that we use nowadays, since the principle is much the same to this day.
Our team will adhere to your requirements and work closely with you to create the parts that meet your desired specifications. With years of expertise, we’ve created a streamlined process that guarantees optimal results, from mold building to shipment:
Our customers in California and worldwide benefit from our quality of material and workmanship, as well as excellent technical and production assistance. Using state-of-the-art technology and our experience and expertise, we provide comprehensive injection molding services ranging from assistance in design, development, prototyping, and manufacturing to match your specifications. Have the leader among injection mold manufacturing companies on your side.
Based on the above, manufacturing of plastic injection molding can take anywhere from 2 weeks for simple parts to up to 18 weeks (or more) for intricate designs.
Carefully selected resin pellets undergo the melting process, injecting them into the mold cavity, and left to cool and solidify.
As one of the top plastic injection molding companies in the industry, we employ state-of-the-art production technology and a wide range of effective techniques for precise custom plastic injection molding. This allows us to maximize yield and reduce waste, while maintaining consistent quality and on-time delivery at a competitive price.
To ensure high quality of fabricated parts, the best plastic injection molding companies employ a 4-stage process that consists of:
Since injection molding represents the most common method of plastic parts manufacturing, the list of products can range from bottle caps to car parts. More complex parts are made out of a combination of two or more materials through a special process called overmolding.
As a reputable plastic injection molding company, we offer an array of materials that can be used in the production process. Learn more about various materials that we use at our materials page.
Customized design and a full range of plastic material material offerings including a wide variety of colorant and over-molding options.
At Wunder Mold, we also do everything in our power to stay ahead of the curve by implementing all the current advancements in custom injection molding in California and across the nation and globe. What’s more, we’re always looking ahead, exploring new developments, making sure we’re constantly at the cutting edge of our industry. Give us a call today and let us how we can help you.
Custom injection molders design and manufacture custom molds and/or custom parts from a mold for the customer at small, medium, and large volumes. As the leading industry’s company, Wunder-Mold specializes in this process and is able to deliver a product design to your exact specifications and industry requirements.
During and after the injection molding, and before shipping the components to the client, the parts go through a thorough quality inspection.
A mold is essentially a hollow metal block. Cavities within it are filled through gates and runners, and once filled with plastic, will produce the desired part. To learn more about our process and what it entails, feel free to contact us at your convenience.
In a word: extremely. This method is widely recognized as one of the most accurate and precise, up to a fraction of an inch. As an example, the best plastic injection molding companies can produce parts with very tight tolerances, ranging from ±0.005” all the way to ±0.001”.
Customized design and a full range of plastic material material offerings including a wide variety of colorant and over-molding options.
Category NotesPlastic Some of the values displayed above may have been converted from their original units and/or rounded in order to display the information in a consistent format. Users requiring more precise data for scientific or engineering calculations can click on the property value to see the original value as well as raw conversions to equivalent units. We advise that you only use the original value or one of its raw conversions in your calculations to minimize rounding error. We also ask that you refer to MatWeb's terms of use regarding this information. Click here to view all the property values for this datasheet as they were originally entered into MatWeb.
Wunder-Mold’s quality and attention to detail are at the heart of our mission. As a plastic injection molding company that has been in the business for over 24 years, we constantly seek ways to further advance the scope, quality, and cost-efficiency of our injection mold manufacturing.
Capable project management from design to final part. One-stop service for all of our clients’ plastic injection molding.
Yes, plastic injection molding typically produces parts that are much stronger than their 3D-printed counterparts. These are the reasons why:
As a plastic injection molding company with years of experience in the field, we strive to provide the optimal solution for each client based on individual requirements. We can help with the design and development of new components or help reduce the cost of manufacturing parts based on an existing part design. We offer:
Polycarbonate (PC) is generally considered to be the top plastic for injection molding when it comes to sheer durability. This material boasts excellent impact resistance and high tensile strength, making it suitable for a wide range of applications, such as car parts, medical devices, and even electronics.
This page displays only the textof a material data sheet.To see MatWeb's complete datasheet for this material (includingmaterial property data, metalcompositions, material suppliers,etc), please click the button below.
A plastic injection company is a business that handles plastic molding manufacturing. Typically, these companies operate on a medium to large scale, producing large quantities of plastic molds and related products for a diverse range of applications.If you’re looking for one of the best plastic injection molding companies, we’re here to help you with our expertise and precision.
During the process of plastic molding manufacturing, a molten plastic mixture is forced under high pressure into a custom-made mold so that the material takes the shape of the mold cavity. Once the part has been removed from the mold it is typically finished, but may require secondary operations.
Custom plastic injection molders employ computer-aided design (CAD) software or similar to produce custom molds machined with different disciplines out of solid metal and generally have two halves that will come together during the mold assembly process.
Plastic injection molding is used for the production of plastic parts in medium to high volume production levels. These parts come in an array of different colors, shapes, and sizes.
A mold life expectancy can last between hundreds and millions of parts if properly constructed and maintained. The application (i.e. prototyping, production) usually dictates the mold’s endurance.
GETTING A QUOTE WITH LK-MOULD IS FREE AND SIMPLE.
FIND MORE OF OUR SERVICES:
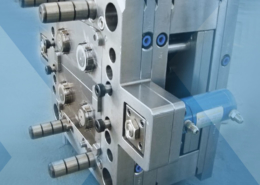
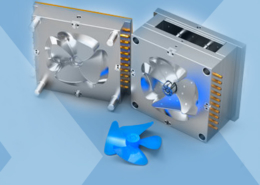
Plastic Molding

Rapid Prototyping
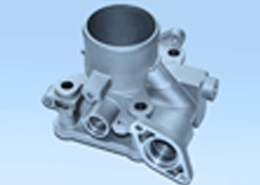
Pressure Die Casting
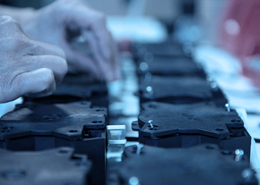
Parts Assembly
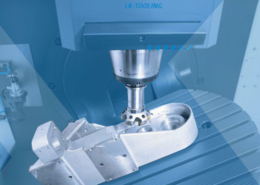