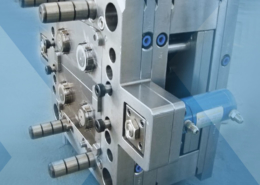
4 Ways to Mold Plastic - plastic casting molds
Author:gly Date: 2024-10-15
A special application of casting commonly used for the manufacture of hollow articles is plastisol casting. There are several variations; dip casting, slush casting and rotational casting. All are based on the fact that a plastisol liquid form is solidified as it comes in contact with a heated surface.
A predetermined amount of liquid plastisol is placed in a heated, closed, two-piece mold. The mold is then rotated, usually in two planes: this distributes the plastic against the walls of the mold in a thin even layer. As it comes in contact with the mold it solidifies. After the plastic is cured the mold is opened and the part removed.
Near Net Shapes – What are their benefits?Near net shapes are great for geometries that result in a poor machining yield from a stock shape or those requiring complex tools that are not cost justified by the volume of parts.
Let us apply our process know-how to arrive at the most cost effective process to manufacture your PEEK parts. We will work with your existing tooling or develop new tooling.
A liquid plastisol is poured into a heated hollow mold which is the shape of the outside of the object to be made. The plastisol in immediate contact with the walls of the mold solidifies. The longer the plastic remains in the mold, the thicker will be the layer of plastic that solidifies. The excess plastic, still in the liquid form, is poured from the mold. After the plastic is cured the mold is opened and the part is removed.
Both thermosets and thermoplastics may be cast. Commonly used materials for casting include acrylics, phenolics, polyesters and epoxies.
Our in-house molding operation uses all electric machines with appropriately sized barrels minimizing time at temperature during molding to maximize the properties and consistency of every part we mold. Our range of machine sizes between 35 and 300 tons means we can mold parts ranging in size from .03 oz. to 20 oz.
Many products are made by casting rather than molding. In casting, the liquid is simply poured into the mold, rather than being forced in.
We design our process to meet your needs. Our Toyo injection-compression molding machines combined with our experience processing PEEK enables us to do what others cannot: precision tolerances, zero draft, fiber orientation, insert molding and heavy cross sections. All machines are RJG equipped allowing us to monitor in-cavity conditions and develop the most reliable molding process for a given part. We apply scientific molding principles when molding PEEK parts.
A heated plug the size and shape of the inside of the article to be cast is dipped into a container of liquid plastisol. The mold is withdrawn at a given rate. The plastic immediately surrounding the mold adheres to it and solidifies. The slower the rate of withdrawal, the thicker will be the layer of plastic. After cure, the plastic is stripped from the mold.
The plastic is prepared in liquid form. In some cases the resin is naturally a liquid and in others a granular solid is liquefied by heat. The liquid plastic is poured into a closed mold and air bubbles are removed. The plastic is cured at room temperature or in an oven at low heat. The cured plastic is then removed from the mold.
GETTING A QUOTE WITH LK-MOULD IS FREE AND SIMPLE.
FIND MORE OF OUR SERVICES:
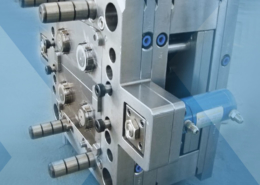
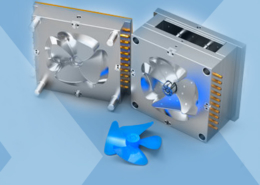
Plastic Molding

Rapid Prototyping
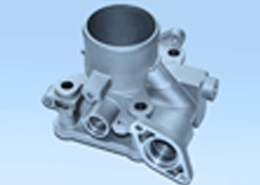
Pressure Die Casting
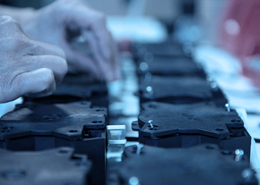
Parts Assembly
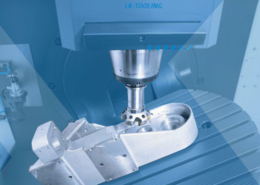