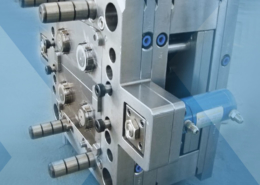
Unveiling the World of Custom Injection Molding
Author:gly Date: 2024-06-08
Custom injection molding stands as a cornerstone of modern manufacturing, offering a versatile and efficient method for producing a wide array of plastic components tailored to specific needs and requirements. In this article, we embark on a journey to explore the intricacies of custom injection molding, from its origins to its contemporary applications and future prospects.
Introduction: Piquing Curiosity
Imagine a world where every product, from the tiniest component to the most intricate assembly, is perfectly customized to fit its intended purpose. This is the realm of custom injection molding, where precision meets versatility, and innovation knows no bounds. Join us as we unravel the mysteries behind this fascinating manufacturing process.
Origins and Evolution
Early Beginnings
The roots of injection molding can be traced back to the late 19th century, with the invention of the first injection molding machine by John Wesley Hyatt. Since then, the process has undergone significant advancements in materials, technology, and techniques, paving the way for custom injection molding as we know it today.
Technological Advancements
The advent of computer-aided design (CAD) and computer-aided manufacturing (CAM) has revolutionized the custom injection molding industry. These digital tools enable precise modeling and simulation of complex geometries, facilitating the production of intricate and highly customized components with unprecedented accuracy and efficiency.
Industry Applications
Custom injection molding finds applications across a diverse range of industries, from automotive and aerospace to healthcare and consumer goods. Its versatility and scalability make it an ideal choice for producing everything from interior trim components and medical devices to consumer electronics and packaging solutions.
The Custom Injection Process
Design and Prototyping
The custom injection molding process begins with the design phase, where engineers work closely with clients to conceptualize and refine product specifications. Prototyping techniques such as rapid prototyping and 3D printing allow for iterative testing and validation of designs before full-scale production begins.
Tooling and Mold Making
Once the design is finalized, the next step is to create the molds that will shape the plastic components. Tooling engineers employ advanced machining and fabrication techniques to produce high-quality molds with precision and durability, ensuring consistent and reliable performance throughout the production process.
Injection Molding
With molds in hand, the injection molding process can commence. Plastic resin pellets are melted and injected into the mold cavity under high pressure, where they cool and solidify to form the desired shape. State-of-the-art machinery and automated systems ensure fast cycle times and tight tolerances, maximizing productivity and quality.
Quality Control and Assurance
Inspection and Testing
Quality control is paramount in custom injection molding to ensure that every component meets or exceeds customer expectations. Automated inspection systems, including coordinate measuring machines (CMMs) and optical scanners, are used to verify dimensional accuracy and detect any defects or imperfections.
Traceability and Documentation
Traceability is essential for tracking and managing the production process from start to finish. Advanced data management systems record key metrics such as material properties, process parameters, and inspection results, providing valuable insights for continuous improvement and compliance with industry standards.
Continuous Improvement
The pursuit of excellence is an ongoing endeavor in custom injection molding. Through continuous monitoring, analysis, and optimization of processes and performance metrics, manufacturers strive to minimize waste, reduce cycle times, and enhance product quality, ultimately delivering greater value to customers.
Conclusion: Embracing Innovation and Possibility
In conclusion, custom injection molding represents the pinnacle of modern manufacturing, combining cutting-edge technology with time-honored craftsmanship to bring bespoke plastic components to life. As we look to the future, the potential for innovation and discovery in this field is limitless. By embracing new materials, techniques, and applications, we can unlock new possibilities and drive progress in industries ranging from automotive and electronics to healthcare and beyond. Together, let us embark on this journey of exploration and imagination, where every idea has the power to shape the world around us.
GETTING A QUOTE WITH LK-MOULD IS FREE AND SIMPLE.
FIND MORE OF OUR SERVICES:
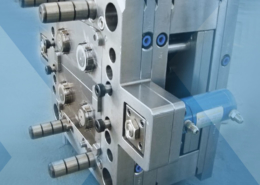
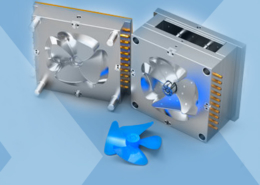
Plastic Molding

Rapid Prototyping
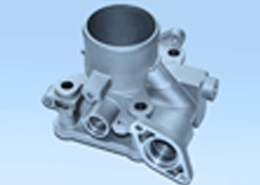
Pressure Die Casting
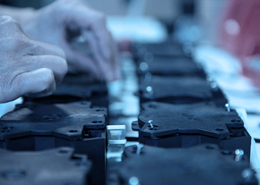
Parts Assembly
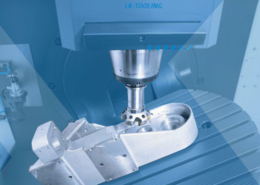