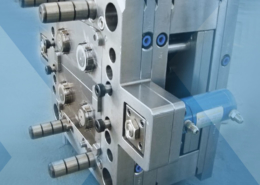
3D Printed Soft Plastics Molds - 3d printed soft plastic mold
Author:gly Date: 2024-10-15
In ISO 9001 quality management systems, the Management Representative (MR) plays a crucial role. While the 2015 version of ISO 9001 no longer mandates this position, having a trusted management member serve as an MR remains vital for streamlining operations and maintaining quality standards.
Compression molding is most often used with thermoset plastics whose chemical structure changes when melted and cooled to create a hard, rigid final product. Plastic resin is heated to a soft, almost "putty" state where it's not quite liquid, then it's placed into a heated mold. The putty is then pressed into shape by the mold and allowed to cool.
Over the years, NyproMold has faced the challenge of overseas competition head-on. “Like other companies, we continually fight with it,” Muldoon comments. “But, we find that automation, quality grade and tooling technologies give us an advantage in value and customer satisfaction.”
According to Muldoon, NyproMold is always looking for above-average individuals in the industry to join the NyproMold team. Currently, the company is in pursuit of experienced mold designers, and is working with a number of employment agencies to fulfill its needs.
Discover how CAD/CAM functionality tailored for the mold industry can significantly enhance the mold design process. In part three of the webinar series, Cimatron will focus on designing waterlines and cooling components. It will demonstrate how CAD/CAM tools can verify drill line depths for water lines and baffles, ensure that minimum steel requirements are met while placing water lines, and provide a complete list of all baffle cutoff lengths. Additionally, it will explore how to confidently design runners and gates using CAD functionality specifically developed for these aspects of mold design. Agenda: Waterlines and verification Conformal cooling Baffles and charts Runners and gates
Intralox's integration of the Alpha Laser ALFlak has significantly improved their tool room efficiency when it comes to difficult welds and urgent repairs.
Explore the standout articles of September, featuring innovations, expert insights, and strategies to boost efficiency and quality for your moldmaking needs.
After attending IMTS, it's clear that the integration of advanced technologies is ready to enhance precision, efficiency and automation in mold manufacturing processes. It’s a massive event, so here’s a glimpse of what the MMT team experienced firsthand.
A focus on electrode design and automation helps toolroom improve efficiency, reduce tooling costs and deliver higher quality products.
Join this webinar where Hexagon will explore how state-of-the-art CAD/CAM technology can drive your business forward. Learn how to optimize tool paths, enhance design accuracy and reduce lead times with advanced simulation. Discover the power of automation and real-time data for continuous improvement. Tailored for mold and die manufacturers, this session offers actionable insights to boost productivity and quality. Don’t miss this opportunity to gain a competitive edge in progressive die manufacturing. Agenda: Key challenges in progressive die manufacturing Optimizing tool paths Enhancing mold and die design accuracy Reducing lead times with simulation Automating processes for greater efficiency Leveraging real-time data for continuous improvement
This moldmaker’s humble beginnings as a prototype tool builder have expanded to include mold concept to completion in a number of markets.
Engineers use properly preloaded bolts, blocks, springs and side-action cores to enhance functionality and reliability in various mechanical systems.
Since 1988, Advanced Plastiform, Inc., has been providing superior custom plastic molding and fabrication services to companies in North Carolina, South Carolina, Maryland, Georgia and Pennsylvania. Contact us to make an appointment Mon-Fri 8-5.
Gerardo (Jerry) Miranda III, former global tooling manager for Oakley sunglasses, reshares his complete mold design checklist, an essential part of the product time and cost-to-market process.
After attending IMTS, it's clear that the integration of advanced technologies is ready to enhance precision, efficiency and automation in mold manufacturing processes. It’s a massive event, so here’s a glimpse of what the MMT team experienced firsthand.
Thermoforming involves heating a large sheet of plastic until it is soft and flexible, then stretching it over a single-sided, custom mold. Vacuum pressure or compressed air presses the thermoplastic tightly against the mold, creating the desired shape.
NyproMold (Clinton, MA)—a Nypro, Inc. company—was originally started 14 years ago as a joint ven-ture with its parent company as a builder of prototype tools. Today, the company’s capabilities range from concept to high-cavitation, ultra high production and multi-tool programs and the ability to provide complete turnkey system capability: part design assistance, FEA, mold flow, mold design and build, qualification, product inspection, automation and machine integration. Industries served include consumer/industrial, electronics/telecommunications, packaging, automotive and healthcare.
In ISO 9001 quality management systems, the Management Representative (MR) plays a crucial role. While the 2015 version of ISO 9001 no longer mandates this position, having a trusted management member serve as an MR remains vital for streamlining operations and maintaining quality standards.
MoldMaking Technology Editorial Director Christina Fuges sits down with Murphy Forsyth, GM – Injection Molding and Director Of Marketing for Zero Tolerance LLC in Clinton Township, MI.
When designing plastic products and components, one of the most challenging decisions is determining the right method of manufacturing them. Your goal is to have a durable, high-quality finished product while minimizing costs and speeding up efficiency and the right manufacturing method is key to meeting these goals. There are six main types of plastic manufacturing, and our thermoforming company in North Carolina is looking at each type and the associated benefits they offer.
Discover how to enhance your mold design process with CAD/CAM software specifically tailored for the moldmaking industry. In part two of this webinar series, Cimatron will demonstrate how to intelligently design mold components, such as slides and lifters, using powerful CAD/CAM tools to accelerate the design process. Additionally, it will cover how to avoid errors and ensure design accuracy for ejector pins by checking clearance distances, calculating cutoff heights correctly, and thoroughly documenting all ejector components. Agenda: Slides Lifters Inserts Ejection pins and charts
This work is performed in a 104,000-square foot facility with a small crew, that Muldoon notes can produce the same as a crew double its size—due to automation and the most modern equipment, including robotic toolmaking machines that can operate in a lights-out mode with no operator present.
Enter lean manufacturing principles to complement the company’s diverse offerings. According to NyproMold presi-dent Bill Muldoon, who was formerly a Nypro plant manager, the company is committed to its parent company’s lean program, HVS (High Velocity System)—a proprietary system practiced at all Nypro operations to save its customers money by driving waste and error out of all activities.
NyproMold relies on its apprenticeship program to bring new employees up-to-speed with the company’s methods of mold design and build. “For example, with our engineering apprenticeship, each potential apprentice must spend a minimum of six months on the manufacturing floor in each department—so as to fully understand how every process works—prior to moving on to the design room where he or she will learn the manufacturing standards,” Muldoon points out. “Then, when beginning to design, he or she will fully understand what it truly takes to manufacture a particular component and then to turn that into a much simpler design—saving money and time with each tool build.”
When used for conformal cooling in plastic injection, 3D printing opens a wide range of design freedom. This design freedom enables designers to develop highly-efficient thermal regulation networks. However, this blessing also comes at the expense of not only higher manufacturing cost but also higher design cost as the designer could spend weeks to develop optimal cooling channels. This webinar will explore strategies and tools — including SimForm, a front-end thermal simulation app — to help tool designers and tooling managers maximize the benefits of 3D printing while minimizing manufacturing and design costs. Agenda: 3D printing applied to the plastic injection industry 3D printing pros and cons Tools and methods to facilitate the integration of 3D printing
The need for data to track information and the history of the mold-building process is ever-increasing, and mold component solutions can help.
Injection molding is a plastic manufacturing method in which a thermoplastic is melted to a liquid, then injected into a double-sided mold using a highly pressurized injector. The plastic coats and fills the mold to create the needed shape, and is then cooled and ejected for finishing.
“The lesson learned in Moscow is one learned in most other areas that are trying to pull themselves up by their bootstraps—hang in, and eventually hundreds of millions of citizens will find ways to improve their standard of living—which includes quality modern plastics,” Lankton adds. Today, Nypro molds and makes molds in Moscow—with a number of consumer products customers.
MoldMaking Technology addresses the complete lifecycle of the manufacture and maintenance of a mold—from design to first shot—by providing solutions and strategies to moldmaking professionals charged with designing, building and repairing molds. About Us
It’s easy to imagine the advantages automation offers the moldmaking process, but it's challenging to change one’s mindset, develop a plan and invest.
Steps to improve data-driven decision-making and key features of a cloud-based system for mold monitoring and asset management.
The Editorial Advisory Board of MoldMaking Technology is made up of authorities with expertise within their respective business, industry, technology and profession. Their role is to advise on timely issues, trends, advances in the field, offer editorial thought and direction, review and comment on specific articles and generally act as a sounding board and a conscience for the publication.
After attending IMTS, it's clear that the integration of advanced technologies is ready to enhance precision, efficiency and automation in mold manufacturing processes. It’s a massive event, so here’s a glimpse of what the MMT team experienced firsthand.
All NyproMold employees may take any courses that will help them progress on the job—backed by a tuition reimbursement program. Additionally, the company sponsors frequent in-house demonstrations from its suppliers and encourages employees to attend trade shows. A profit-sharing program also is in place to increase employee satisfaction, Muldoon adds.
Rotational molding, or "roto-molding," involves pouring melted plastic into a mold, which is then rotated at a high speed. This coats the plastic evenly along the walls of the heated metal mold, leaving the interior hollow. This method is primarily used for large, hollow-walled containers, storage bins, and even kayaks.
Presentations will cover 3D printing for mold tooling, material innovation, product development, bridge production and full-scale, high-volume additive manufacturing.
Diamond compounds, with their varied grades, colors and base options, provide a comprehensive solution for mold builders in need of precise and superior polishing across diverse materials and applications.
Formnext Chicago is an industrial additive manufacturing expo taking place April 8-10, 2025 at McCormick Place in Chicago, Illinois. Formnext Chicago is the second in a series of Formnext events in the U.S. being produced by Mesago Messe Frankfurt, AMT – The Association For Manufacturing Technology, and Gardner Business Media (our publisher).
Understanding and facing the moldmaking industry’s obstacles to growth requires a strategy focused on increased profitability.
Released earlier, this video remains a valuable recruitment tool and is being re-promoted in celebration of Manufacturing Day 2024.
Extrusion molding is primarily used to manufacture long, straight pieces, such as tubing, hoses, or pipes. This method involves forcing liquid plastic into a die to form a shape. While round pieces are common, t-shapes, l-shapes, and squares are also achieved, depending on the shape of the die. Many thermoplastics can be used during extrusion molding.
The sixth largest U.S. employee-owned company, Nypro has taken advantage of numerous opportunities over the years to expand operations and ensure its position as a worldwide service provider. As an example, the company began looking at Moscow in 1990 as a potential locale for increasing its global presence. They entered Moscow as a minority owner in a molding company owned also by a Moscow manufacturing company and a Swiss importer. Nypro’s involvement in Moscow followed a trip down the Volga River by Chairman and former CEO Gordon Lankton.
NyproMold’s parent company Nypro, Inc. (Clinton, MA) was founded in 1955 as a precision injection molding company. At the present time, it is an integrated, innovative provider of plastics solutions, with 15,000 employees, a billion dollars in annual revenues, and 67 operations in 18 countries. Its array of services includes product design and development, mold design and fabrication, injection molding, precision metals, surface decoration technologies, diversity supply, assembly, and verification and contract manufacturing.
In 1988, Muldoon decided to start NyproMold with fellow Nypro employee Brian Walker. After building prototype molds for six years, they started NyproMold Chicago in 1994 at Nypro’s Chicago factory and two years later, they purchased mold facility Mark Tech (Leominster, MA), which was folded into NyproMold’s Clinton operations. In 2004, NyproMold Clinton moved into its brand new, 104,000 square foot facility—enabling the company to expand operations and offer art-to-part capabilities.
Identify pain points, tackle each one strategically and maintain flexibility to keep your moldmaking business on a path to growth.
Within a year, Nypro opened its own plant. “The big difference with Moscow was that we usually have global customers when we open new plants around the world, but with this one we had only local customers at the start in the late ‘80s and that remained the case until a couple of years ago,” Lankton notes. “Also, the idea of custom plastics was unknown in Russia—under the old Communist system, their industries traditionally handled all functions for their products, including plastics molding. The facility that we used in the beginning had been used before us for plastics, and we slowly brought it up to Nypro standards as resources grew. Even under those circumstances, it started as the most modern custom plastics factory in Russia and it remains that today.
Join MoldMaking Technology Editorial Director Christina Fuges as she gets the latest news on this mold builder's use of VR for mold design education.
NyproMold plans to continue climbing the ladder of success by opening facilities abroad—separate from Nypro Inc.’s other tool companies overseas. Muldoon feels this will help the company to realize its goal of reaching $45 million in sales within the next two years.
At Advanced Plastiform, Inc., we specialize in heavy-gauge thermoforming and injection molding. Our experienced team includes engineers and designers as well as manufacturers, all of whom are dedicated to helping you meet your goals. Our company works with industries across the Mid-Atlantic and Southeast, including North Carolina, South Carolina, Pennsylvania, Maryland, Tennessee, Georgia, and Virginia. To learn more, call us at 919-404-2080 or fill out the contact form to get started.
This webinar will provide an overview of new developments in hot runners, controllers, mold components, predesigned molds, process monitoring and mold maintenance equipment. These advancements are designed with the goals of lowering scrap rates, optimizing process temperatures and managing energy consumption. The solutions also aim to support productivity and may contribute to extending the operational lifespan of tooling equipment. Agenda: Innovative undercut and thread-forming components Predesign mold bases and plate control Melt delivery and control solutions Process monitoring and maintenance
A connected software solution streamlines the moldmaking process by providing a unified source of design data, enhancing efficiency and reducing errors, with five key steps benefiting from this integration.
Steel supplier discusses high thermal conductivity metal powders that also address the skills gaps via user-friendly materials and promote sustainability via durability and higher cycle counts.
Blow molding is similar to injection molding as the plastic is heated to a liquid state and injected into a mold. However, once the plastic is placed in the mold, air is injected into the plastic, inflating it so that it presses against the walls of the mold and achieves the desired shape.
Muldoon counts on his employees’ continued dedication to realize his dream. “We continually ensure that our employees are content in every venture we pursue, because without them we would be nowhere,” he states, “and with that, our constant focus is on making sure that every mold is fully operational and delivered on time.”
For 40+ years, Dynamic Tool Corp. has offered precision tooling, emphasizing education, mentoring and innovation. The company is committed to excellence, integrity, safety and customer service, as well as inspiring growth and quality in manufacturing.
Smart sensors and sophisticated process and measurement data management are driving intelligent moldmaking to new heights.
Join MoldMaking Technology Editorial Director Christina Fuges as she gets the latest news on this mold builder's use of VR for mold design education.
Steel supplier discusses high thermal conductivity metal powders that also address the skills gaps via user-friendly materials and promote sustainability via durability and higher cycle counts.
After attending IMTS, it's clear that the integration of advanced technologies is ready to enhance precision, efficiency and automation in mold manufacturing processes. It’s a massive event, so here’s a glimpse of what the MMT team experienced firsthand.
Discover how to enhance your mold design process with the right CAD/CAM tool for parting and cavity design. This webinar will explore CAD/CAM capabilities including how hybrid solid/surface modeling can streamline workflow and improve accuracy. Learn how to confidently tackle parting, runoff, and shutoff, ensuring precision and efficiency in your designs. Agenda: Part analysis QuickSplit techniques Parting and runoff strategies Shutoff solutions
A water-based, eco-friendly plastic mold cleaning system helps Rankine-Hinman Manufacturing restore flow rates and avoid big-ticket failures on complex and costly molds.
Survey findings reveal a shortage of skilled mold designers and engineers in the moldmaking community, calling for intervention through educational programs and exploration of training alternatives while seeking input from those who have addressed the issue successfully.
GETTING A QUOTE WITH LK-MOULD IS FREE AND SIMPLE.
FIND MORE OF OUR SERVICES:
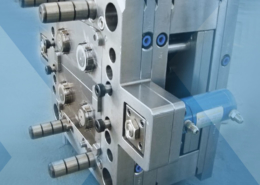
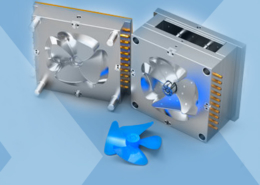
Plastic Molding

Rapid Prototyping
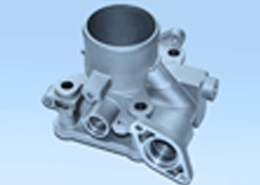
Pressure Die Casting
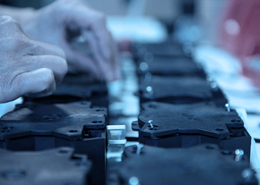
Parts Assembly
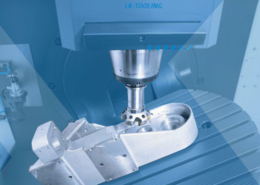