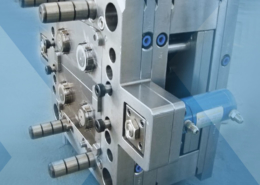
3 Plate Mold Design For Plastic Injection Molding - 3 part injection mold
Author:gly Date: 2024-10-15
Established in 2008,Guangzhou Jeepine Intelligent Compression Molding Machine Co., Ltd is one of the leading manufacturer of The High-compacity Cap Compression Molding Machine ,dedicated to High-efficiency and cost-saving compressing molding technology.especially for the bottled water cap compression molding,beverage cap moulding,dairy cap molding,liquor cap molding,condiment cap molding,cosmetics closure molding and pharmaceutical rotary closure molding machine. Jeepine are leading the advanced compression technology for plastic closures in China,with the aim of creating value for customers. We have a professional R&D team,CAE academicians , overseas returnees ,doctors and masters who dedicated to make a superb design for caps and research the newest technique to create the value for customers. Whatever platform strategy, mature technology and innovative solution would be brought to you, optimal combination possibilities for high efficiency,high capacity,high stability and offered you the right solution as you need, enhancing your benefits.
We're committed to quality and concrete actions. That means we always deliver solutions in a professional and practical way.
We have a professional R&D team, CAE academicians, overseas returnees, doctors and masters who dedicated to make a superb design for caps and research the newest technique to create the value for customers.
Multi-cavity point Plastic bottle cap molds have mature technology from 4 to 32 cavities, simplified hot runner work, and low cost.
The blade is specially designed The unscrewing ring knife edge of the plastic bottle cap mold adopts a split structure, which can make the blade not deformed, the positioning is accurate, the replacement is easy, and the mold is closed without pressure. defect.
We're well-known as one of the leading plastic cap mould manufacturers and suppliers in China for our quality products and customized service. Please feel free to buy bulk plastic cap mould made in China here from our factory.
Plastic Cap Mould is an abbreviation of molds includes compress molding, extrusion molding, injection molding, blow molding and low foam molding. It is a tool to make a fixed shape products with kinds of plastics. The tool is mostly have two parts called male mold and female mold. There is some empty space after the male mold and female mold closed. That is the plastic product`s shape. We put some melt plastic to fill the empty space and then we got a plastic part after it was cured.
RevPart is ready to answer any questions you have about the benefits of polypropylene, and any other material selection inquiries. Contact us today.
Ejection of the bottle caps from the mold Now, it's time to remove the injection-molded caps from the mold cavities. The mold will be able to handle thousands of production cycles, so you can repeat the process again as needed.
Reduce downtime During the use of plastic bottle cap molds, there is always the possibility of major failures that require shutdown and maintenance, and can no longer continue working during shutdown. Therefore, it is hoped that the shorter the shutdown time, the better, and the fewer the shutdown times, the better. The major failure of the mold is often not sudden. It has an accumulation process.
We have a professional R&D team,CAE academicians , overseas returnees ,doctors and masters who dedicated to make a superb design for caps and research the newest technique to create the value for customers.
Raw material: HDPE/PPMax production capacity: 100,000pcs/h Cavity: 24/48/54 Cap type: 3025/2925/38mm/1810/1881/2622/alaska/etc
Material : HDPECapacity: 100000pcs/h Forming by: Compression molding Cavity : 24/36/48/54 cavity Cap type : 3025/2925/38mm/28mm/2622/alaska /etc
Reduce operating costs In the process of using the mold, there are many operating costs, such as inspection costs, adjustment costs, lubricant costs, repair costs, etc. The sum of these costs is the operating cost. Of these costs, the largest amount is repair costs. If the maintenance of the mold is not good, many extra repair costs are often paid, which makes the mold unable to work normally and increases the operating cost.
You can contact us about pre-sale, in-sale and after-sale services, we will give you a very satisfactory answer, and we serve you online 24 hours a day.
High efficiency The plastic bottle cap mold adopts a simplified dispensing hot runner, no glue mouth waste, and the cycle reaches 5 seconds.
Feeding the plastic materials into the mold Next, it's time for you to feed the plastic materials into the mold. You will need to do this before starting the injection molding operation to ensure that the plastic materials will be ready when you start the production operation.
At the outset, only you understand the different weight that each of these factors has in the calculus of material choice for your specific project. Of course, it’s important to share this information with your manufacturing partner so that it can best assist you in choosing the right material.
Established in 2008, We have more than 10 years rich experiences in cap compression molding machine. Up to now,We're obtained nearly 100 national patents,in science&Technology"and has winned the certifications of UL,ISO9001 :2015 and TUV.
Polypropylene, as mentioned above, is a cost-effective material on a raw material basis. Although resin prices fluctuate based on supply and demand, polypropylene will almost always be a competitive option — provided that it meets your product requirements. Some secondary cost benefits of polypropylene include:
With so many versatile applications, polypropylene is thus well-suited to a broad range of product types, as well. One of the most common uses is the living hinge — a one-piece hinged construction commonly seen in products like caps for consumer products (think of the flip-top on a mustard bottle). The living hinge is one of the most important innovations in plastic injection molding, and polypropylene is probably the most ideal resin for the job. This is mainly on account of its high property of flexibility — ability to bend multiple times — hundreds or thousands — without breaking.
Timely maintenance For example, the lack of oil in the sliding part will lead to increased wear. If it can be maintained in time and oiled in time, it will reduce wear. Delaying the shutdown of the mold, as in the lateral core pulling mechanism of the inclined guide column, the screw fixing the inclined guide column is loosened, which causes the position of the inclined guide column to change. In severe cases, the inclined guide column can be deformed or even broken. These problems will be discovered in time during maintenance and tightened in time, and these similar problems will not occur.
Material : HDPECapacity: 20000-22000pcs/h Cap weight : 2622 CSD 1.8g; 2622 Water cap 1.1gCap type: 2622 water cap , 2622 CSD cap
In this article, we’ll take a detailed look at polypropylene injection molding: when it can be used, what products and applications it’s most suited for, and what the advantages of using it are. As you read through, remember that with the wide variety of plastic resins available from which to choose, there’s no textbook “best solution” — it always depends on your specific needs. Polypropylene is one of the more versatile and commonly used materials available, which is why we’re focusing on it today, but it’s important to always compare the advantages and disadvantages of any material against the requirements of your project.
As a quick refresher, before we begin our deep dive into polypropylene, just a few of the factors that might drive your material choice include:
The cooling process of the injection-molded plastics Now, the extrusion process will be complete, and the injection-molded bottle caps will need to cool down before you can eject them from the mold. Depending on various factors, you will need to wait for different cool-down times for the plastic bottle caps.
Using the extrusion mechanism For plastic bottle cap production, you will need to use the extrusion mechanism, as this is the mechanism that works best to produce tube-shaped products. With the extrusion mechanism, you can create plastic bottle caps that will have the best design, along with the threading system inside the cap.
High life expectancy The cavity of the plastic bottle cap mold is made of high-quality mold steel, and the guide post and guide sleeve of the mold are lubricated without oil, which has the strong advantages of no pollution and a service life of up to ten million times.
Guarantee product quality To ensure that the plastic mold can produce qualified plastic parts stably and reliably, the plastic bottle cap mold must be in good working condition. When the injection mold is working, it is always impossible to stay in working condition. There will always be one or another situation, such as the lack of oil in the guide post and guide sleeve, which will cause action blockage, and the loosening of the fasteners, which will cause deformation of the action. These small problems will adversely affect the quality of the product. Overcome these minor problems and make the mold in good working condition.
Continuous compression molding machine for the production of plastic caps by extruding the granulated compound (HDPE, PP), cutting it into single pellets, inserting it into the cavities, and finally molding the cap according to a defined design. The output of the machine depends upon resin, part design and part weight.
Clamp the mold based on the tonnage requirement After completing the mold for the plastic bottle cap design, you will need to clamp the mold according to the tonnage requirement of your machine, which will allow you to connect the feeding system with the mold. Be sure to follow the tonnage requirement to ensure that your mold will hold its place during the production period.
Polypropylene is one of the more commonly used injection molding resins for a reason: It’s extremely versatile and has a number of applications for which it’s suited. In addition, polypropylene injection molding parameters, such as melt temperature and viscosity, lend themselves to relatively easy, cost-effective production in a wide range of uses.
GETTING A QUOTE WITH LK-MOULD IS FREE AND SIMPLE.
FIND MORE OF OUR SERVICES:
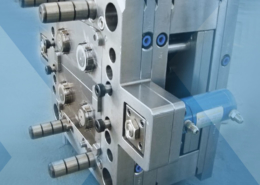
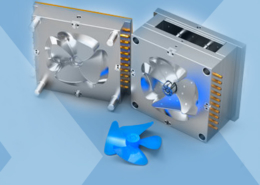
Plastic Molding

Rapid Prototyping
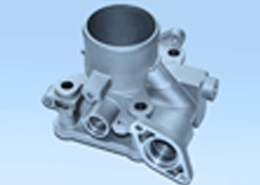
Pressure Die Casting
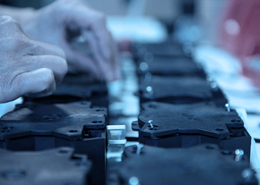
Parts Assembly
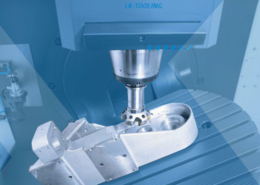