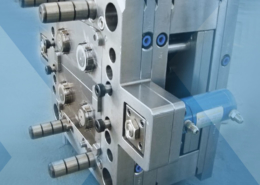
Unraveling the Potential of Co-Injection Molding in Modern Manufacturing
Author:gly Date: 2024-06-08
Co-injection molding, a sophisticated variant of traditional injection molding, has emerged as a game-changer in the realm of plastic manufacturing. This article aims to explore the intricacies of co-injection molding, shedding light on its significance, techniques, applications, and future prospects.
Introducing Co-Injection Molding
Breaking Ground
Co-injection molding, also known as multi-material or sandwich molding, involves the simultaneous injection of two or more different materials into a single mold cavity to produce a composite part. This innovative technique allows for the creation of components with distinct layers, combining the properties of different materials to achieve desired functionalities and aesthetics.
Background Overview
Traditional injection molding has limitations in achieving certain material properties and functionalities. Co-injection molding addresses these limitations by offering enhanced design flexibility, improved strength, reduced material usage, and cost savings. Its versatility makes it ideal for a wide range of industries, including automotive, aerospace, electronics, and consumer goods.
Techniques in Co-Injection Molding
Dual-Nozzle Injection
Dual-nozzle injection is a common approach in co-injection molding, where two materials are injected through separate nozzles into the mold cavity. This technique allows for precise control over material distribution, thickness, and layering, resulting in uniform and consistent parts.
Sequential Injection
Sequential injection involves the sequential injection of different materials into the mold cavity, either through the same or multiple nozzles. This technique enables the creation of complex structures with multiple layers, gradients, or patterns, expanding the design possibilities for engineers and designers.
Advantages and Challenges
Advantages of Co-Injection Molding
Co-injection molding offers numerous advantages over traditional molding techniques, including improved part strength, enhanced surface finish, reduced cycle times, and minimized material waste. It also allows for the incorporation of functional features such as inserts, overmolding, and encapsulation, streamlining the production process and enhancing product performance.
Challenges and Considerations
Despite its benefits, co-injection molding presents certain challenges, including material compatibility, process optimization, tooling complexity, and cost considerations. Achieving proper adhesion between different materials, optimizing processing parameters, and designing molds for multi-material injection require careful planning and expertise.
Applications and Future Directions
Applications Across Industries
Co-injection molding finds applications in diverse industries, including automotive components, packaging, consumer electronics, medical devices, and construction materials. Its ability to combine different materials, colors, textures, and functionalities opens doors to innovation and customization in product design and manufacturing.
Future Prospects and Innovations
Looking ahead, advancements in material science, process optimization, and digital manufacturing technologies are expected to drive further innovation in co-injection molding. From biodegradable plastics to smart materials with embedded sensors, the future holds promise for novel applications and sustainable solutions in co-injection molding.
Conclusion and Future Directions
In conclusion, co-injection molding represents a paradigm shift in modern manufacturing, offering unparalleled versatility, efficiency, and customization capabilities. By harnessing the potential of this innovative technique, manufacturers can unlock new opportunities for product differentiation, cost reduction, and environmental sustainability.
Moving forward, continued research and development efforts are essential to address the remaining challenges and push the boundaries of co-injection molding technology. Collaborative initiatives between industry stakeholders, academia, and regulatory bodies can pave the way for standardization, best practices, and the emergence of new materials and processes.
In summary, co-injection molding is not just a manufacturing technique; it is a catalyst for innovation and progress in the ever-evolving landscape of plastic manufacturing. By embracing its capabilities and overcoming its challenges, we can pave the way for a more efficient, sustainable, and resilient future in manufacturing.
GETTING A QUOTE WITH LK-MOULD IS FREE AND SIMPLE.
FIND MORE OF OUR SERVICES:
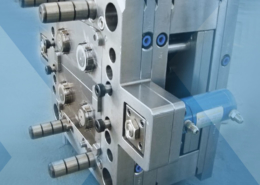
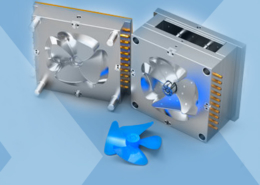
Plastic Molding

Rapid Prototyping
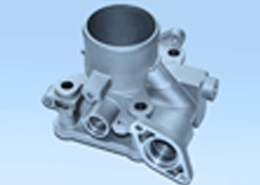
Pressure Die Casting
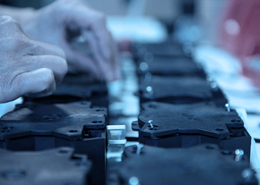
Parts Assembly
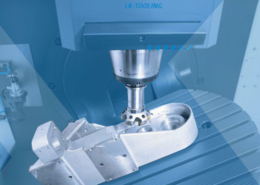