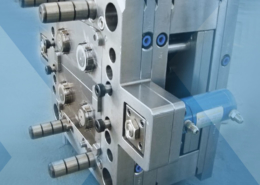
2K injection molding process - 2k molding
Author:gly Date: 2024-10-15
Create an account today, and when you upload your CAD data and provide RFQ details, we’ll find the solutions that meet your needs.
P20 is a commonly used, general purpose tool material. It strikes a strong balance between cost, available tooling lead time, part quality and dimensional part stability. Fictiv often uses another grade of steel, 718H, which is a bit harder than P20, but has the same general advantages and disadvantages.
We exist to eliminate bottlenecks in new product development by integrating the people, processes, and platform you need to source custom parts.
The rule to remember when initially designing you part is: "Maximize metal and minimize plastic." Figure 1, for example includes a post (properly drafted, of course) rising from a base. Figure 2 shows the same part after the designer has decided that the post needs to be thicker. (Added plastic is shown in red.) This change was easy to execute. If the change had gone in the other direction, however, it would have required the milling of a new mold.
There are multiple commonly used grades of metals for tooling, and they’re typically used for the different stages of product development and validation. These different types of materials produce molds that provide assorted achievable tooling lead times and costs, different plastic part cycle times and associated unit costs, and varying levels of dimensional part precision and cosmetic quality of appearance.
Get machined parts anodized and chromate plated with our quick-turn finishing option. Eligible materials include aluminum 6061/6082 and 7075.
Each type of mold material has its advantages and disadvantages, so it helps to create a “game plan” early in the design process for tooling and bringing your product to market. Here, we’ll discuss the prevalent mold materials, their advantages and disadvantages, and common use cases for each.
By signing up, you agree to our Terms of Use and Privacy Policy. We may use the info you submit to contact you and use data from third parties to personalize your experience.
Hardened steels are most often used for high production quantity tooling. They’re typically multiple cavities with hot runner systems. The tool lives are longer but the manufacturing time and tooling costs are the highest of any material. High production quantity tooling is used to minimize part unit costs, which offsets the higher up front NRE (non-recurring engineering) costs.
If the product demand is high and the designs are finalized and locked, customers typically move to hardened steel, production multi-cavity tooling. The NRE tooling costs are higher, but the minimized unit pricing and cycle times combined with maximized production capacity make it a logical next step in tooling.
Aluminum is often used as an alternative to harder steel grades in situations that call for faster tool production time and prototype/low volume part production. Though aluminum is a common material in the industry, at present, it’s seldom used by Fictiv.
Not sure how thick a wall should be? Start thin and thicken it later. (ProtoQuote will warn you if your wall is too thin for effective mold filling.) Unsure whether you'll need a rib to strengthen your part or a brace to prevent warp? Leave it off and add it later if it's needed. Have two mating parts that might (or might not) need alignment pins? Put the holes in and leave the pins off. If you need them, you can add the pins in the next iteration. If you don't, you can eliminate the holes.
By signing up, you agree to our Terms of Use and Privacy Policy. We may use the info you submit to contact you and use data from third parties to personalize your experience.
Create high quality custom mechanicals with precision and accuracy.
By signing up, you agree to our Terms of Use and Privacy Policy. We may use the info you submit to contact you and use data from third parties to personalize your experience.
The whole purpose of prototyping is to allow yourself the option of tweaking your model—thickening a wall, adding a rib, placing text or a logo—before locking in a final design for production. For injection-molded plastic prototypes, tweaks can entail the creation of a whole new mold. A new mold may be quite affordable if your parts are being made by Protolabs, but if the change can be made by modifying the existing mold, your cost will be even lower.
Our digital factories create prototypes and low-volume parts fast, while our manufacturing network, offers advanced capabilities and volume pricing.
Oftentimes engineers and product designers place much focus on selecting the appropriate grade of plastic when developing injection molding part designs. Equally important, though frequently an afterthought, are the metal materials used to manufacture the injection molding tool itself.
We exist to eliminate bottlenecks in new product development by integrating the people, processes, and platform you need to source custom parts.
Though the sequence described above is typical for Fictiv customers, there are factors which may prompt engineers and product designers to do it differently. Fictiv has a wealth of knowledge and expertise for injection molding, both in the US and overseas, and we’re happy to review and provide DFM feedback on your next tooling project.
Our helpful design aid demonstrates part features that are too thin or too thick, bad bosses, right and wrong ribs, and other considerations to be mindful of while designing parts for injection molding.
By signing up, you agree to our Terms of Use and Privacy Policy. We may use the info you submit to contact you and use data from third parties to personalize your experience.
Proto Labs, Inc. 5540 Pioneer Creek Dr. Maple Plain, MN 55359 United States P: 877-479-3680 F: 763-479-2679 E: [email protected]
NAK80 is semi-hardened tool steel, which Fictiv most often uses for highly polished clear or glossy plastic parts. It’s also used when the tooling life needs to be longer than P20 steel or when a part has several side actions. It has similar advantages and disadvantages as P20, plus:
A word of advice: we find that if customers 3d print a prototype set prior to releasing tooling, the need for ECO’s is drastically reduced.
One final thing to keep in mind when you plan for changes: at Protolabs, we can make parts to tolerances of ±0.003 in. plus the shrink tolerance of the resin.
By signing up, you agree to our Terms of Use and Privacy Policy. We may use the info you submit to contact you and use data from third parties to personalize your experience.
By signing up, you agree to our Terms of Use and Privacy Policy. We may use the info you submit to contact you and use data from third parties to personalize your experience.
If you aren't entirely sure whether a feature is needed or whether a feature is the right size, you might want to review your part feature by feature, asking yourself which ones may need to be changed in later iterations before committing your design for prototyping; Then start with the "less plastic" option.
By signing up, you agree to our Terms of Use and Privacy Policy. We may use the info you submit to contact you and use data from third parties to personalize your experience.
During these validation phases, more than one third of Fictiv customers’ tools require design changes through an ECO, which usually takes 3-5 days to modify the tooling. Single cavity, P20 or NAK80 tooling for ECO’s provides more freedom to make non steel-safe changes than aluminum at a lower cost than a hardened steel, multi-cavity production tool.
By signing up, you agree to our Terms of Use and Privacy Policy. We may use the info you submit to contact you and use data from third parties to personalize your experience.
Designing with this in mind is called "steel safe" or "metal safe," and doing so can save you both money and time when you have to modify your design. For example:
Access a wide breadth of capabilities through our highly vetted network.
Tough Black (Loctite Henkel 3843) and Ceramic-Filled (BASF 3280) are two new advanced photopolymer materials now available for 3D printing.
This grade of steel is the most commonly used for high production quantity tooling, and is good for thermal fatigue, and longer tooling life. It can better resist wear from some plastic materials, such as those with glass-filled additives, than the metal materials previously listed.
By signing up, you agree to our Terms of Use and Privacy Policy. We may use the info you submit to contact you and use data from third parties to personalize your experience.
Our trained employees ensure your parts will be delivered on time and to spec.
There's one critical fact to remember if you want to be able to modify your part by modifying the original mold. It is relatively easy to remove metal from an existing metal mold. Adding metal, on the other hand, can be difficult or, for all practical purposes, impossible with rapid injection molding. To look at this from the part perspective, you can add plastic, but you can't take it away.
Such molds enable our customers to save on NRE costs at the beginning stages of a new product, and help bring an initial product to market faster. This can unlock investments and produce a bridge production quantity of parts to tide them over until production tooling comes online.
Accelerate development with instant quotes, expert DFM, and automated production updates.
Usually, Fictiv customers start with single cavity, P20 or NAK80 steel tools for their engineering validation testing (EVT) and design validation testing (DVT). These tools are finished and produce the first samples (T1) in 10-25 days.
GETTING A QUOTE WITH LK-MOULD IS FREE AND SIMPLE.
FIND MORE OF OUR SERVICES:
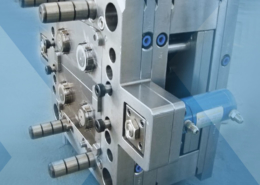
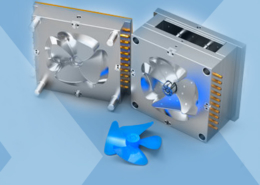
Plastic Molding

Rapid Prototyping
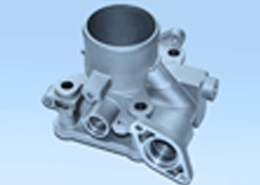
Pressure Die Casting
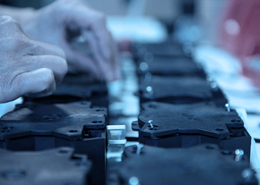
Parts Assembly
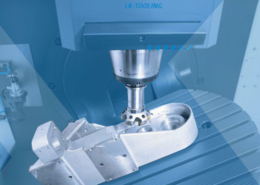