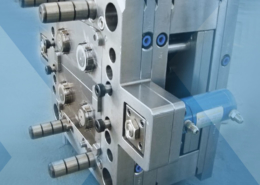
2K injection molding process - 2k injection molding
Author:gly Date: 2024-10-15
Crafted Plastics has built its reputation on producing extruded plastic profiles and plastic tubing that meet the specifications and quality standards of our customers. We offer single extrusion, co-extrusion, and tri-extrusion production along with many value-added processes either in-line or off-line.
Creating plastic parts for commercial and medical applications requires different processes, dependent on shape and usage requirements.
Extreme Molding is a unique silicone molding company formed in 2002 outside Albany, N.Y. We pride ourselves on being one of the longest-tenured women-owned molders operating in the United States
Our range of in-house capabilities means that attention to detail will follow your product from start to finish, which means that each item has complete manufacturing traceability.
Crafted Plastics offers in-house engineering to help with material selection and tool design. Most of our extrusion dies and tooling are made onsite by our team.
One of the most unique aspects about Extreme Molding is our full-service production model. Our model saves our clients time, money, and warehouse space. We mold your silicone products and take care of any post-production operations, such as assembly, packaging, and fulfillment.
Extreme Molding is the top choice for high-end consumer and life science products made from high-performance silicones. From our home just outside of Albany, NY, we partner with both small and large businesses throughout the United States, Canada and Europe.
Crafted Plastics has served the plastics extrusion needs of manufacturers and distributors worldwide since 1982. Whether it’s a basic extruded profile or a more complex profile, our commitment is to produce custom extrusions that meet your specifications.
Material is heated and forced through an opening cut into series of metal plates with a shape similar to the final product, creating a continuous form that can be stretched and then cooled to shape before cutting to length. Examples: tubing and window profiles.
Extrusion is ideal when a variety of lengths of a constant cross-section is required. By producing stock with a continuous production process, setup and die costs are lower when compared to injection molding where a unique mold would be required for each length.
“We looked for a US manufacturing partner for a full year before we finally found Extreme Molding. They found creative ways to help us bring costs down so that we could afford to manufacture in the US, and the fact that they also do fulfillment helps us realize additional savings as well. The Extreme Molding Team has integrity, tons of expertise, and maintains a high standard of quality in everything they do. All in all, they are excellent partners, and amazing people.”
As one of the few American molders owned and operated by women, Extreme Molding is particularly passionate about partnering with the manufacturers of quality health care products for women and babies. We have been producing LilyPadz, self-adhesive silicone breast shields for nursing mothers, for more than a decade. Hospital-issued neonatal pacifiers also have been a core product for many years. When it became necessary to find an alternative to polycarbonate, we were first in the nation to mold BPA-free Eastman Tritan co-polyester with silicone to make a safer pacifier.
Extreme Molding has the technical capabilities to handle any complex silicone molding application. Over the years we have developed expertise in the markets of non-regulated healthcare products (specifically for women and infants), specialty consumer/light industrial products, pet supplies, and medical components.
Extrusion creates continuous linear part with a constant cross-section; injection molding produces three-dimensional shapes. The final shape required for a part dictates the process used, but both extrusion and injection molding have their benefits.
Secondary operations complement our extrusion operation. Secondary operations include forming, notching, punching, piercing, drilling, tight tolerance sawing and other assembly capabilities.
At Extreme Molding, you will find between 75-100 professionals ready to be your partners in making your products successful. We are one of the few U.S. molders that are women owned and operated.
If you have a great idea, we can help bring it to life. We’ve done this before and enjoy becoming partners throughout product creation. From advising you through the mold sourcing process, to delivering your new product to customers, we want to work with you every step of the way.
Molten material—typically thermoplastic polymer—is injected into a mold to create a solid shape. Examples: plastic combs and three-dimensional objects with openings, such as crates. Injection molding typically has a higher initial cost given the complexity of the mold structure, but the process creates a finished piece that doesn’t require assembly or secondary processing.
GETTING A QUOTE WITH LK-MOULD IS FREE AND SIMPLE.
FIND MORE OF OUR SERVICES:
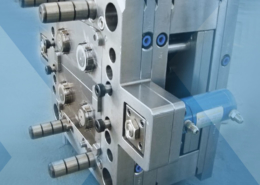
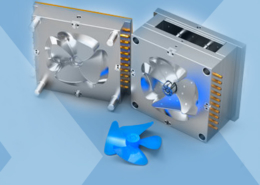
Plastic Molding

Rapid Prototyping
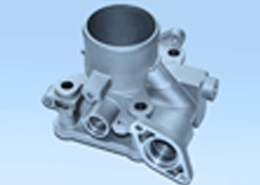
Pressure Die Casting
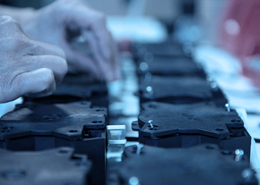
Parts Assembly
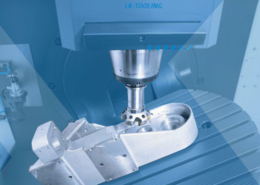