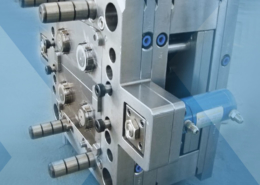
220V Mini Injection Molding Machine | Small Benchtop Type - small injection mold
Author:gly Date: 2024-10-15
– Reduce the injection speed. High plastic injection speeds can cause jetting, which causes trapped air to appear right at the inlet gate. Reducing the injection speed will give the displaced air at the gate enough time to escape through the aeration zones.
If welding or joining lines cannot be avoided, a good practice is to ensure that they are generated in low visibility or mechanically non-critical areas. This is often done by modifying the plastic injection gate, modifying the flow fronts and the areas where the weld/joint lines occur. Another practice is to try to achieve a good joint between the two fluxes so that the mechanical weakness that occurs is not excessive. To do this, the aim is for the junction of the two flux fronts to take place at the highest possible temperature and pressure, so that they are not far from the inlet port. Translated with www.DeepL.com/Translator (free version)
Some of the actions to be taken to improve the surface finish are related to actions to increase the flow rate and temperature of the molten polymer and the mould walls. Therefore, the improvement of the surface quality is achieved by measures such as:
The following recommendations can be used to reduce the impact of weld lines and parting lines on injection moulded parts.
The locations of the air leakage areas in the moulds are located in the areas that are filled at the end of the injection cycle or phase. A common cause of the trapped air defect is an insufficient size of the mould vents. Another common cause is when racetracking occurs (tendency of the polymer melt to flow preferentially in thicker sections leaving thinner areas with trapped air). Translated with www.DeepL.com/Translator (free version)
This is another one of the most common injection molding products people use daily. Many toothbrush handles are made using a thermoplastic polymer such as polypropylene. These materials are lightweight, durable, impact-resistant, recyclable and food safe.
The keys on your keyboard are manufactured using ABS plastic. It can be shaped into various forms and provide good tactile feedback.
Injection molding is a popular technology used by many household product manufacturers today. Some may be surprised that many everyday items they use are made using this technology. Everything from flower pots, packaging containers, phone cases and medical syringes are all injection molding products. Sometimes, these things make you wonder how to mold plastic at home.
Occasionally, the use of high compaction pressures causes acceptable sink marks by reducing volumetric shrinkage although these cannot be completely eliminated. This is because the volumetric change of plastic from melt to solid is about 25% and the compressibility of plastics at typical injection moulding pressure is only 15%, which means that it is impossible to compact the molten plastic sufficiently to compensate for cooling shrinkage.
Many packaging containers have plastic molded parts. The most common containers produced using this technology include storage boxes, cosmetic jars and food containers. These lightweight containers are designed to be stackable, making them easy to store and organize. They also feature secure closures, which ensure the safety of their contents. In addition, many of these packaging containers are made from recyclable materials.
Injection molding allows manufacturers to create robust CD cases designed to protect and store compact discs and similar data storage items. These cases can be made using transparent or opaque plastic, which allows you to see or label each disc contained in the case. These materials feature a hinged design, allowing for easy access to the disc held within while providing protection from scratches and dust that can damage the item within.
Many parts of your car were manufactured using injection molding technology. This precise and accurate process can be used to make everything from the door knobs to dashboard components and interior trim pieces. Plastic car components are designed for heat resistance and durability.
Weld lines and joint lines can be caused by holes or insertions in the part, the existence of multiple injection gates, or due to areas of varying wall thickness where hesitation or race-tracking occurs.
These items are some of the most common products made by injection molding. Plastic glasses and cups are lightweight, durable and reusable, making them a practical choice for everyday use. In addition, these items can be designed for casual and formal use.
All-Plastics offers the latest injection molding technology. We create products in a zero-defect environment, increasing production efficiency while reducing production costs. Please fill out our online contact form to request a quote or ask a question.
However, achieving uniform shrinkage is complicated by the presence and interaction of many factors such as the orientations of the polymer molecules, temperature variations in the mould walls, compaction variations in the plastic parts (over-compacted areas and under-compacted areas, due to unbalanced flow paths), etc. Note that areas of higher compaction, such as injection gates, have a lower shrinkage since part of the compaction of the molten polymer compensates for it. In contrast, areas further away from the gate are subject to less compaction and therefore tend to have a higher shrinkage.
Injection molding plays a vital role in the field of medicine, where various items and pieces of equipment need to be designed precisely according to certain specifications. Syringes and other medical equipment undergo strict quality control in compliance with today’s medical standards.
The formation of wrinkles or waves is due to the fact that a part of the flow front cools rapidly on the mould walls producing a fold on the flow front itself. Themain factors influencing the formation of these wrinkles are the flow velocity, the temperature of the mould walls, and the temperature of the molten polymer, among others.
The jetting defect occurs when molten polymer is pushed at speed through a small area, such as the injection nozzle or gate, to access a much larger area. The jetting defect results in mechanical weakness in the part, surface imperfections and multiple internal defects.
The burr is a defect that occurs when part of the molten polymer flows through the existing gaps in the injection mould such as parting plane, aeration zones, ejectors, etc. Burring occurs for the following reasons:
Incomplete filling occurs when a one injection moulded part is missing material to correctly generate its geometry. This occurs when the molten polymer cannot fill the entire cavity (or cavities) in the Injection mould, usually the thinner sections where the polymer melt cools before completely filling the mould. Any factor that increases the flow front resistance of the polymer melt can result in incomplete filling. Some of these factors are:
Injection molding offers plenty of benefits for everyone, which is why it is the preferred manufacturing method for producing many everyday items:
Traditionally, the joint angle between the two faces is used to differentiate weld lines from joint lines. A joint angle of less than 135º produces a weld line, while a joint angle of more than 135º is defined as a joint line. In general, a weld line mark disappears when the joint angle reaches between 120º and 150º. The weld lines are considered more critical than joint lines in terms of both aesthetics and mechanical properties of the joint. Translated with www.DeepL.com/Translator (free version)
The warping or twisting of an injection-moulded plastic part is therefore due to the existence of a series of residual internal stresses in the part which are in turn generated by the differential shrinkage of the material during cooling. If the shrinkage throughout the part is uniform, the resulting part does not warp or twist, it simply shrinks uniformly and becomes smaller. Thecrystalline polymers, e.g. acetal, nylon, high density polyethylene, polyethylene terephthalate and polypropylenecause the most serious problems with shrinkage from 1 to 4%. Amorphous polymers, e.g. polystyrene, acrylic and polycarbonate are more treatable, with shrinkages of only 0.3 to 0.7%.
The dimensional shrinkage of parts is inherent to the injection moulding process. Shrinkage occurs because the density of the polymer varies from processing temperature to ambient temperature (see, for example, the specific volume of a semi-crystalline polymer in Figure 5.46 – PVT curve). During the stages of the injection moulding process, cooling shrinkage produces a series of internal stresses in the part. These residual stresses act on the part with similar effects as possible externally applied stresses. If the residual stresses induced during moulding are high enough, the part after ejection from the mould may warp / twist or warp, resulting in defective parts.
Many toys and toy parts are made using injection molding technology. This technology is often used to produce toy figurines of various sizes. Manufacturers can produce intricate details and a wide array of designs and apply multiple colors. Due to their versatility and affordability, toy figurines have become popular among enthusiasts and collectors alike.
Sinkage marks are depressions in the surface of the plastic injection moulded part caused in the last phase or stage of the plastic injection moulding process, during the cooling process. The thicker sections of the plastic cool at a slower rate than the others, resulting in a higher percentage of shrinkage in that local area. After the material on the outside has cooled and solidified, the material on the inside begins to cool and its shrinkage pulls the surface inwards, causing a surface depression.
Trapped air will result in voids and bubbles within the moulded plastic part, incomplete filling or surface defects such as stains or burn marks.
Phone cases can have plastic molded parts offering essential properties such as scratch and impact resistance. They can be designed in various styles, allowing access to ports and buttons.
When you drop and break your remote control, sometimes it can make you wonder if it is worth learning how to mold plastic at home so you can fix it yourself. Many remotes we use at home are encased in injection molded plastic shells, providing protection for the electronic parts.
A weld line (also called a weld mark) is formed when two melt flow fronts travelling in opposite directions meet. In contrast, a bond line occurs if these two fronts flow parallel to each other creating a bond line.
Injection molding allows for the precise manufacturing of various parts of medical equipment. Manufacturers can produce thousands of these essentials to meet the needs of hospitals and other healthcare centers. Furthermore, this process can produce sterile components that are safe to use in different medical procedures.
A rule of thumb to avoid excessive distortions in the part due to temperature differences after injection, is that the average temperature differences in any part of the part after injection should not be greater than 15-20ºC.
The trapped air defect appears when a certain amount of air cannot escape out of the mould during injection, a small area without material appeared in the injected part. In a correct Injection mould design, at each injection, air is exhausted through mould vents, mould inserts or even ejectors, which also act as vents.
Some of the practices we develop in the Moldblade Engineering Department to correct the problem of incomplete filling are:
A poor finish can be caused by the formation of wrinkles or waves at the edges of the part or in the last filling areas during injection moulding.
Injection molding technology allows manufacturers to create aesthetically pleasing features for your car’s interior and other parts. In addition, the process allows for the rapid production of complex shapes in various dimensions, which meet the high demands of the automotive industry.
GETTING A QUOTE WITH LK-MOULD IS FREE AND SIMPLE.
FIND MORE OF OUR SERVICES:
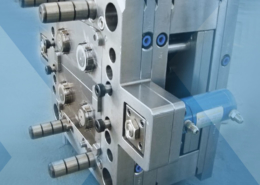
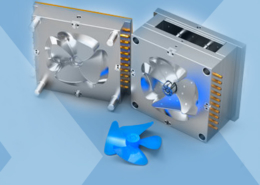
Plastic Molding

Rapid Prototyping
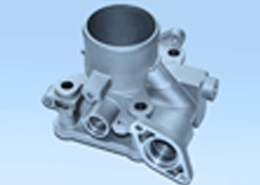
Pressure Die Casting
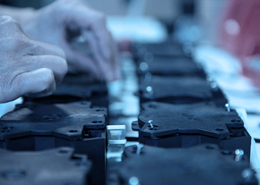
Parts Assembly
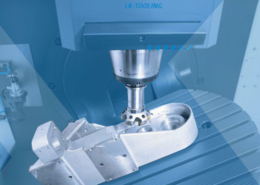